- お役立ち記事
- Mastering Virus Inactivation: Discover How Japanese Manufacturing Leads the Way in Innovative Solutions
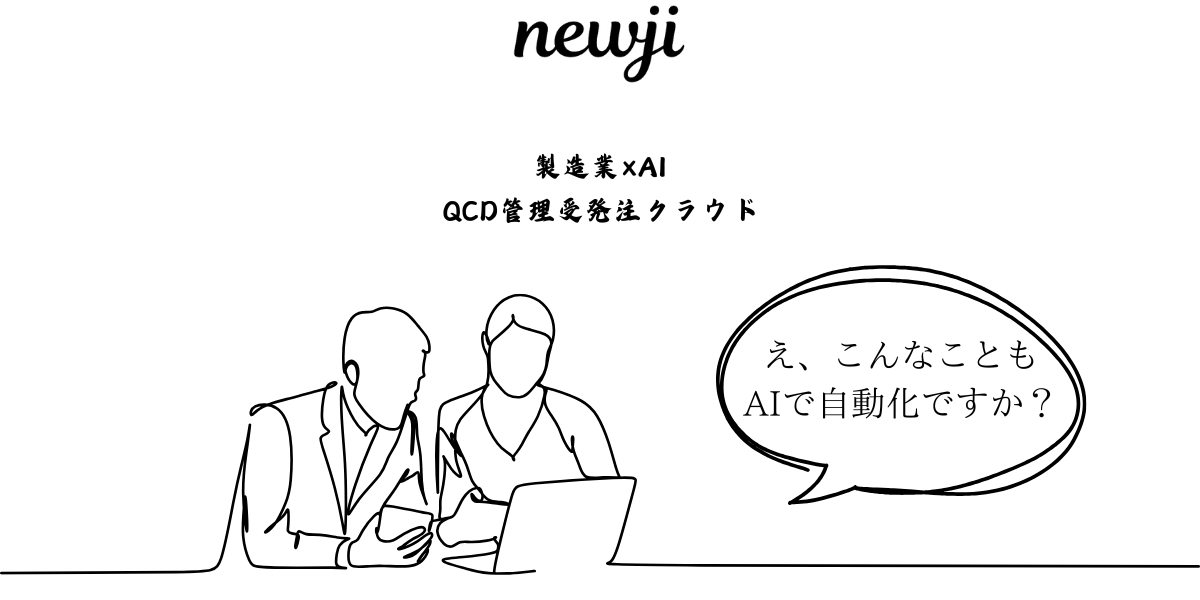
Mastering Virus Inactivation: Discover How Japanese Manufacturing Leads the Way in Innovative Solutions
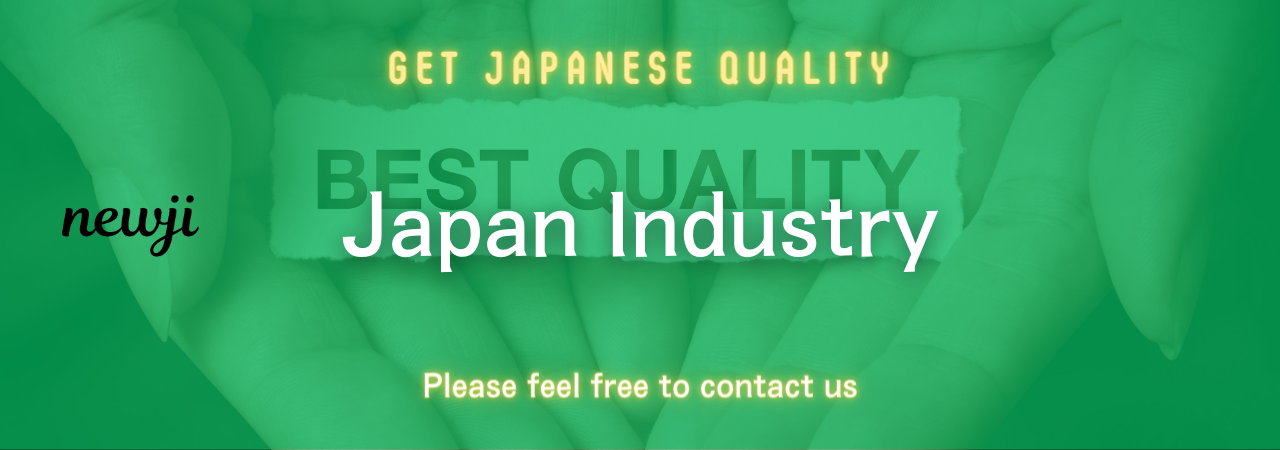
目次
Introduction to Virus Inactivation in Manufacturing
In today’s global landscape, virus inactivation has become a critical component in various manufacturing processes. Ensuring the integrity and safety of products, especially in sectors like pharmaceuticals, food, and electronics, is paramount. Japanese manufacturing has emerged as a leader in developing innovative virus inactivation solutions, setting benchmarks for quality and efficiency worldwide.
The Importance of Virus Inactivation in Manufacturing
Virus inactivation refers to the processes and technologies used to eliminate or deactivate viruses within manufacturing environments. This is crucial for several reasons.
Ensuring Product Safety
Manufacturers must guarantee that their products are free from viral contamination to protect consumers and maintain trust. This is particularly important in sectors like healthcare and food production.
Compliance with Regulations
Adhering to international and local regulations regarding virus control is mandatory. Failure to comply can result in severe penalties, product recalls, and reputational damage.
Maintaining Operational Efficiency
Effective virus inactivation minimizes disruptions caused by contamination incidents, ensuring smooth and continuous production processes.
Japanese Manufacturing: A Leader in Virus Inactivation
Japanese manufacturing companies have long been recognized for their commitment to quality and innovation. Their approach to virus inactivation exemplifies this dedication.
Advanced Technologies
Japanese manufacturers invest heavily in research and development, resulting in cutting-edge virus inactivation technologies. These include:
– **Ultraviolet (UV) Sterilization**: Utilizes UV light to deactivate viruses on surfaces and within products.
– **High-Pressure Processing (HPP)**: Applies intense pressure to disrupt viral structures without damaging the product.
– **Nanotechnology**: Employs nanoparticles to target and neutralize viruses effectively.
Quality Control Systems
Robust quality control systems are integral to Japanese manufacturing. These systems ensure that virus inactivation processes are consistently applied and monitored, maintaining high standards across all production stages.
Lean Manufacturing Practices
Japanese manufacturers often adopt lean manufacturing principles, which emphasize waste reduction and efficiency. This approach extends to virus inactivation, optimizing processes to achieve maximum effectiveness with minimal resource expenditure.
Procurement and Purchasing in Virus Inactivation Solutions
Effective procurement and purchasing strategies are essential for sourcing high-quality virus inactivation solutions. Japanese manufacturers excel in this area through several practices.
Supplier Selection and Evaluation
Japanese companies rigorously evaluate suppliers to ensure they meet stringent quality and reliability standards. This includes assessing their technological capabilities, compliance with regulations, and track record in virus inactivation solutions.
Building Strong Supplier Relationships
Long-term partnerships with suppliers are a cornerstone of Japanese procurement strategies. These relationships foster collaboration, innovation, and mutual trust, enhancing the quality of virus inactivation products and services.
Cost Management
Japanese manufacturers employ meticulous cost management practices to balance quality and affordability. Negotiating favorable terms without compromising on the effectiveness of virus inactivation solutions is a key focus.
Advantages of Japanese Virus Inactivation Solutions
Japanese manufacturing offers several advantages in the realm of virus inactivation.
High-Quality Standards
Japanese products are synonymous with quality. Rigorous testing and adherence to international standards ensure that virus inactivation solutions are reliable and effective.
Innovative Technologies
Continuous innovation drives the development of more efficient and effective virus inactivation methods. Japanese companies’ commitment to R&D ensures they remain at the forefront of technological advancements.
Cultural Commitment to Excellence
A cultural emphasis on meticulousness and continuous improvement, known as kaizen, underpins Japanese manufacturing excellence. This commitment translates into superior virus inactivation processes and products.
Challenges and Disadvantages
Despite their strengths, Japanese manufacturers face certain challenges in virus inactivation.
High Production Costs
Advanced technologies and stringent quality standards can result in higher production costs. Balancing cost with quality remains a persistent challenge.
Market Competition
As global demand for virus inactivation solutions grows, competition intensifies. Japanese manufacturers must continuously innovate to maintain their competitive edge.
Supply Chain Disruptions
Global supply chain disruptions, such as those caused by pandemics or geopolitical tensions, can impact the availability of essential components for virus inactivation technologies.
Supplier Negotiation Techniques
Effective negotiation with suppliers is crucial for securing high-quality virus inactivation solutions at competitive prices. Japanese manufacturers employ several techniques to achieve mutually beneficial agreements.
Win-Win Approach
Japanese negotiators focus on creating win-win scenarios, ensuring that both parties benefit from the agreement. This fosters long-term partnerships and sustained cooperation.
Detailed Contractual Agreements
Clear and detailed contracts minimize misunderstandings and set precise expectations for both parties. This includes specifications for virus inactivation technologies, delivery schedules, and quality standards.
Long-Term Commitment
Demonstrating a commitment to long-term collaboration encourages suppliers to invest in innovation and quality improvements, enhancing the overall effectiveness of virus inactivation solutions.
Market Conditions and Trends
Understanding market conditions is essential for navigating the virus inactivation landscape.
Increased Demand Post-Pandemic
The COVID-19 pandemic heightened awareness of virus transmission, leading to increased demand for effective virus inactivation solutions across various industries.
Technological Advancements
Ongoing advancements in biotechnology, materials science, and automation are driving the development of more sophisticated virus inactivation methods.
Globalization and Supply Chain Integration
Global supply chains facilitate the widespread distribution of virus inactivation technologies, but also introduce complexities related to logistics, regulatory compliance, and quality control.
Best Practices in Virus Inactivation
Implementing best practices ensures the effectiveness and reliability of virus inactivation processes.
Comprehensive Risk Assessment
Conducting thorough risk assessments identifies potential viral threats and informs the selection of appropriate inactivation methods.
Continuous Monitoring and Validation
Regular monitoring and validation of virus inactivation processes ensure they remain effective and comply with evolving standards and regulations.
Employee Training and Awareness
Educating employees about virus inactivation techniques and the importance of maintaining high standards promotes a culture of safety and quality.
Integration of Automation and AI
Leveraging automation and artificial intelligence enhances the precision and efficiency of virus inactivation processes, reducing the potential for human error.
Case Studies: Success Stories from Japanese Manufacturers
Examining real-world examples highlights the effectiveness of Japanese virus inactivation solutions.
Pharmaceutical Sector: Ensuring Sterility
A leading Japanese pharmaceutical company implemented advanced UV sterilization techniques in their production lines. This resulted in a significant reduction in viral contamination, ensuring the production of sterile medications and enhancing patient safety.
Food Industry: Extending Shelf Life
A Japanese food processing firm adopted high-pressure processing (HPP) to inactivate viruses in perishable products. This not only ensured food safety but also extended shelf life, reducing waste and increasing profitability.
Electronics Manufacturing: Protecting Sensitive Components
In the electronics sector, a Japanese manufacturer utilized nanotechnology-based virus inactivation methods to protect sensitive components during production. This approach minimized contamination risks, ensuring the reliability and longevity of electronic devices.
Future Outlook: Innovations on the Horizon
The future of virus inactivation in Japanese manufacturing looks promising, with several key trends and innovations on the horizon.
Integration of Biotechnology
Biotechnology advancements will lead to more targeted and effective virus inactivation methods, minimizing the impact on product quality.
Sustainable Practices
There is a growing emphasis on developing eco-friendly virus inactivation technologies that reduce environmental impact while maintaining high efficacy.
Smart Manufacturing
The adoption of smart manufacturing technologies, including the Internet of Things (IoT) and artificial intelligence (AI), will further enhance the precision and efficiency of virus inactivation processes.
Personalized Solutions
Customized virus inactivation solutions tailored to specific industries and products will become more prevalent, addressing unique challenges and requirements.
Conclusion
Japanese manufacturing continues to lead the way in innovative virus inactivation solutions, driven by a commitment to quality, advanced technologies, and effective procurement and purchasing strategies. By understanding and implementing best practices, navigating market conditions, and leveraging supplier relationships, manufacturers worldwide can enhance their virus inactivation capabilities. As the landscape evolves, ongoing innovation and adaptability will be key to maintaining safety, efficiency, and excellence in manufacturing processes.
資料ダウンロード
QCD調達購買管理クラウド「newji」は、調達購買部門で必要なQCD管理全てを備えた、現場特化型兼クラウド型の今世紀最高の購買管理システムとなります。
ユーザー登録
調達購買業務の効率化だけでなく、システムを導入することで、コスト削減や製品・資材のステータス可視化のほか、属人化していた購買情報の共有化による内部不正防止や統制にも役立ちます。
NEWJI DX
製造業に特化したデジタルトランスフォーメーション(DX)の実現を目指す請負開発型のコンサルティングサービスです。AI、iPaaS、および先端の技術を駆使して、製造プロセスの効率化、業務効率化、チームワーク強化、コスト削減、品質向上を実現します。このサービスは、製造業の課題を深く理解し、それに対する最適なデジタルソリューションを提供することで、企業が持続的な成長とイノベーションを達成できるようサポートします。
オンライン講座
製造業、主に購買・調達部門にお勤めの方々に向けた情報を配信しております。
新任の方やベテランの方、管理職を対象とした幅広いコンテンツをご用意しております。
お問い合わせ
コストダウンが利益に直結する術だと理解していても、なかなか前に進めることができない状況。そんな時は、newjiのコストダウン自動化機能で大きく利益貢献しよう!
(Β版非公開)