- お役立ち記事
- Fundamentals of material strength studies, stress/strain analysis, and residual stress measurement methods for use in strength design
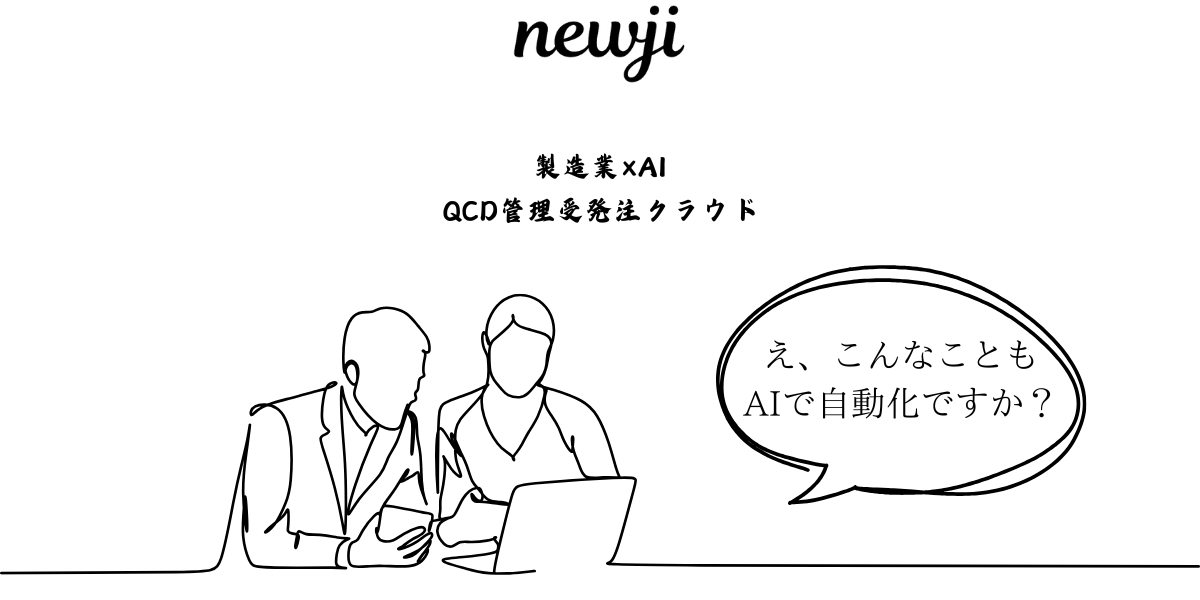
Fundamentals of material strength studies, stress/strain analysis, and residual stress measurement methods for use in strength design
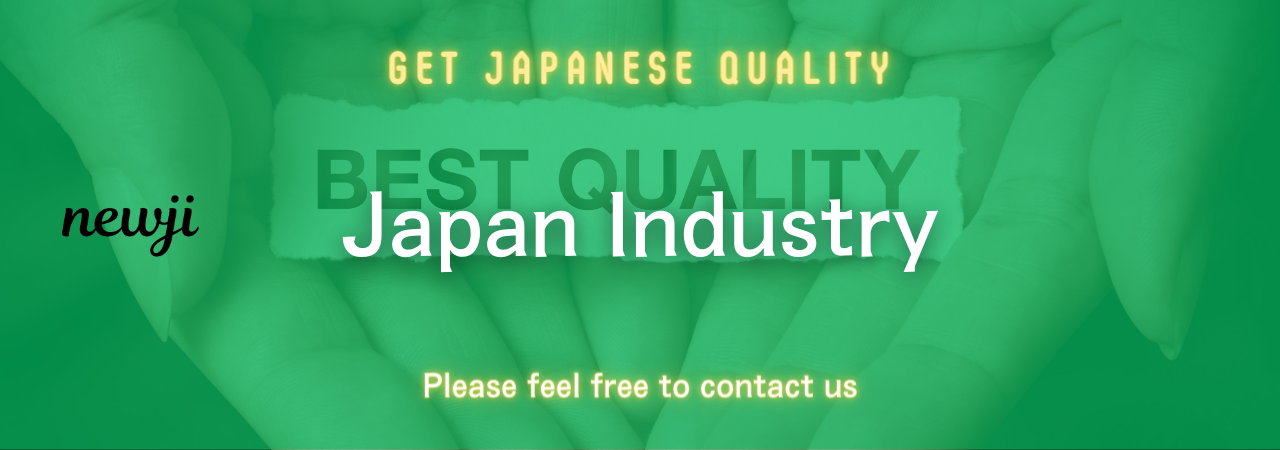
目次
Understanding Material Strength
Material strength is a fundamental concept in engineering and design.
It refers to the ability of a material to withstand an applied load without failing or undergoing excessive deformation.
Understanding material strength is crucial in strength design, where the aim is to ensure that structures or components can bear the loads they are subjected to during their lifetime.
The study of material strength involves assessing how different materials react to stress and strain.
Engineers utilize this information to predict the behavior of materials under various conditions, ensuring safety and durability.
Stress and Strain: Key Concepts
Stress and strain are critical concepts in understanding material strength.
Stress is defined as the internal force exerted by an external load per unit area within a material.
It is measured in units of force per area, such as pascals (Pa) or pounds per square inch (psi).
Strain, on the other hand, is the amount of deformation experienced by a material in response to an applied stress.
It is usually expressed as a dimensionless ratio or percentage of change in the material’s original length.
Types of Stress
In material strength studies, stress is categorized into several types:
1. **Tensile Stress**: This type refers to the stress applied to a material resulting in stretching.
It occurs when forces act to extend the material.
An example is the stress experienced by a rope in a tug-of-war game.
2. **Compressive Stress**: Opposite to tensile stress, compressive stress results in the material being squeezed.
This is seen in pillars or columns that support weight from a floor above.
3. **Shear Stress**: Shear stress occurs when forces are applied parallel to a material’s surface, causing internal sliding.
It is typically seen in scissors cutting through paper.
Strain Analysis
To effectively design materials for strength, engineers perform strain analysis to observe how materials deform under stress.
This analysis helps in predicting the material’s behavior, which is essential for strength design.
The two main methods used in strain analysis are:
1. **Elastic Strain**: This is the temporary deformation that disappears once the applied stress is removed.
Materials that exhibit elastic behavior return to their original shape and size.
The elastic limit is the maximum stress that a material can withstand without permanent deformation.
2. **Plastic Strain**: Plastic strain refers to permanent deformation.
When the stress exceeds the elastic limit, the material undergoes a permanent change in shape.
Understanding plastic strain is crucial in designing components that endure persistent loads.
Residual Stress Measurement
Residual stress is the internal stress present in a material even after the original cause of the stress has been removed.
It can affect a material’s strength and can lead to failure if not properly managed.
Several methods are used for residual stress measurement, including:
1. **X-Ray Diffraction (XRD)**: XRD is a non-destructive technique that uses X-rays to measure the spacing between crystal planes, allowing for residual stress determination.
2. **Hole-Drilling Method**: This semi-destructive method involves drilling a small hole into the material and measuring the resulting deformation.
The change in strain provides information about the residual stress.
3. **Deep Hole Drilling Technique**: This technique measures residual stress by examining strain relief when a hole is drilled deep into the material.
Importance of Stress and Strain Analysis in Strength Design
Stress and strain analysis is integral to strength design as it ensures the safety and efficiency of materials and structures.
Understanding how materials perform under stress and how they can deform helps engineers create designs that are both robust and cost-effective.
Incorporating residual stress measurement into the design process further aids in predicting potential failures and enhancing material performance.
By leveraging these analyses, engineers can develop products that not only meet but exceed safety and performance standards.
Conclusion
Understanding the fundamentals of material strength, including stress and strain analysis and residual stress measurement, is key to effective strength design.
By comprehensively analyzing these factors, engineers can harness material capabilities to create safe, durable, and efficient products that stand the test of time.
The marriage of these principles within engineering ensures that structures and components maintain their integrity, fulfilling their intended purposes without compromise.
資料ダウンロード
QCD調達購買管理クラウド「newji」は、調達購買部門で必要なQCD管理全てを備えた、現場特化型兼クラウド型の今世紀最高の購買管理システムとなります。
ユーザー登録
調達購買業務の効率化だけでなく、システムを導入することで、コスト削減や製品・資材のステータス可視化のほか、属人化していた購買情報の共有化による内部不正防止や統制にも役立ちます。
NEWJI DX
製造業に特化したデジタルトランスフォーメーション(DX)の実現を目指す請負開発型のコンサルティングサービスです。AI、iPaaS、および先端の技術を駆使して、製造プロセスの効率化、業務効率化、チームワーク強化、コスト削減、品質向上を実現します。このサービスは、製造業の課題を深く理解し、それに対する最適なデジタルソリューションを提供することで、企業が持続的な成長とイノベーションを達成できるようサポートします。
オンライン講座
製造業、主に購買・調達部門にお勤めの方々に向けた情報を配信しております。
新任の方やベテランの方、管理職を対象とした幅広いコンテンツをご用意しております。
お問い合わせ
コストダウンが利益に直結する術だと理解していても、なかなか前に進めることができない状況。そんな時は、newjiのコストダウン自動化機能で大きく利益貢献しよう!
(Β版非公開)