- お役立ち記事
- DR and FMEA
月間77,185名の
製造業ご担当者様が閲覧しています*
*2025年2月28日現在のGoogle Analyticsのデータより
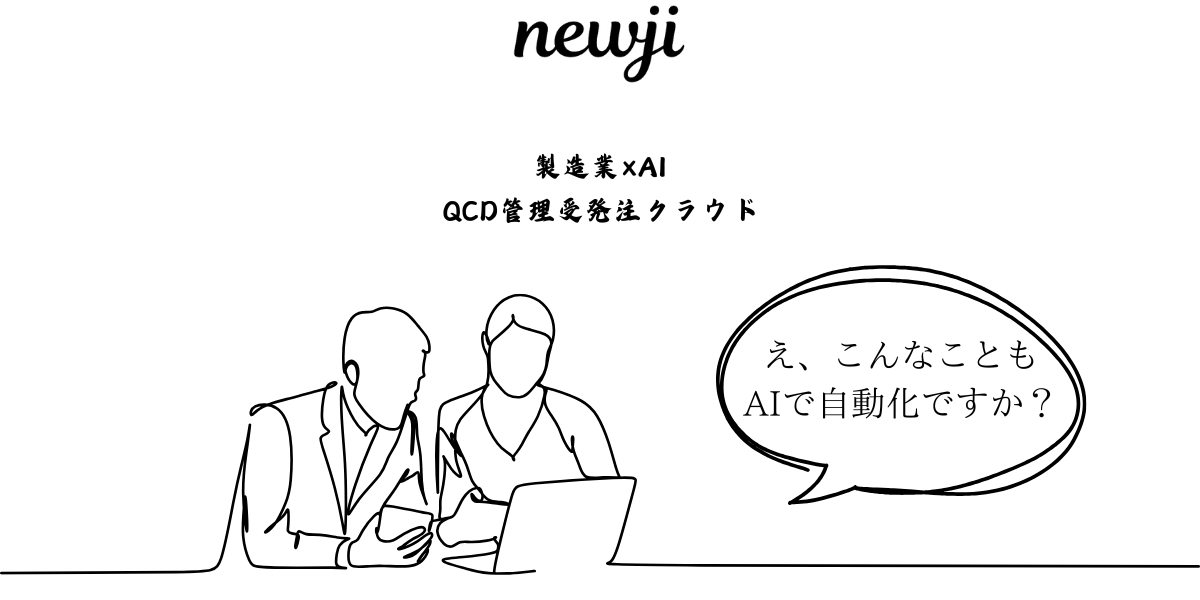
DR and FMEA
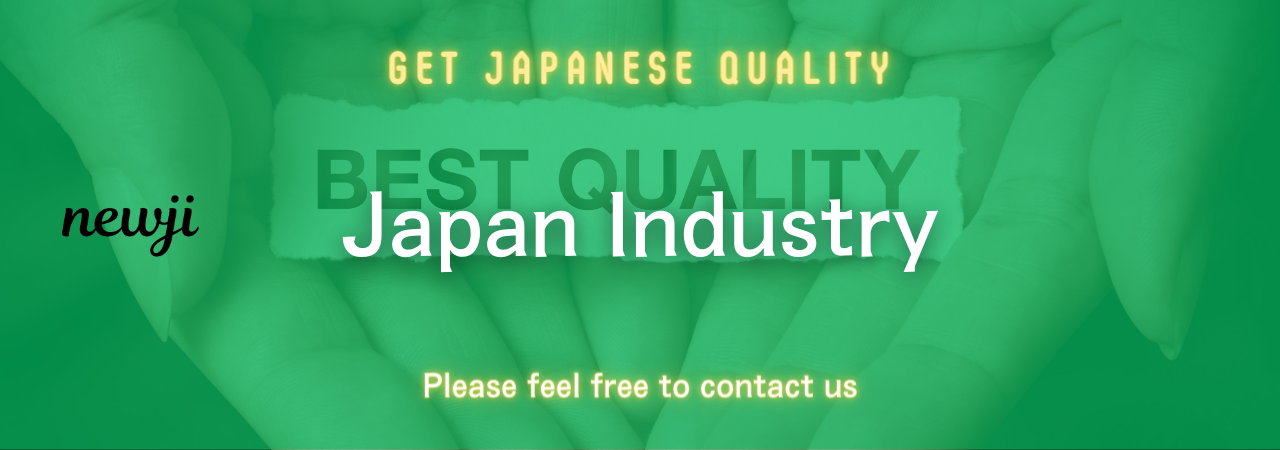
目次
Understanding DR and FMEA
To start with, let’s demystify two important processes in risk management and quality control: DR and FMEA.
Each plays a pivotal role in identifying potential problems and enhancing product or service reliability.
Both are valuable tools in industries like automotive, manufacturing, healthcare, and any other sector concerned with minimizing risk.
What is DR?
DR stands for Design Review.
It is a systematic process intended to evaluate the design of a product or system.
The main goal of a DR is to ensure that the design meets customer requirements and that there are no hidden flaws that could cause a problem once the product is in use.
Design reviews are typically conducted at several stages during a project, ensuring that all aspects of a design are scrutinized and validated before moving forward.
This might include preliminary design reviews, critical design reviews, and even post-release reviews.
By conducting DR, teams can identify potential problems, inconsistencies, or omissions early in the design process.
It can also boost communication and collaboration among team members, and improve overall project quality.
Benefits of DR
Design Reviews bring numerous benefits to any development process.
One of the primary advantages is risk mitigation.
By catching potential issues early, teams can avoid costly redesigns or recalls.
Another advantage is improved design accuracy and quality.
By consulting with cross-functional teams, you improve the prospects of addressing a diverse set of design variables and constraints.
Additionally, DRs promote better documentation and knowledge sharing within a team.
Reviews can serve as valuable checkpoints for project progress, ensuring that everyone is aligned and aware of their roles and responsibilities.
How is DR Conducted?
Conducting a DR involves assembling a team of stakeholders who are relevant to the particular phase of the project in question.
This group typically includes designers, engineers, project managers, and quality assurance specialists.
The review team evaluates the design documents which may include schematics, drawings, or prototypes.
Advance planning is essential for a successful DR to ensure the team has adequate information and time to fully understand the design.
The team discusses the design’s ability to meet requirements, its adherence to standards, and any potential risks.
Once feedback is given, any required changes are implemented before the next phase of development can proceed.
What is FMEA?
FMEA, or Failure Modes and Effects Analysis, is a structured approach to identifying and addressing potential failures in a product or process.
It is often used as a preventive measure to improve quality and reliability.
FMEA helps teams foresee potential problems, evaluate the severity of these problems, and prioritize issues to focus on eliminating or reducing failures.
It is a versatile tool, used both for the design phase (Design FMEA) and operational processes (Process FMEA).
Benefits of FMEA
One of the major benefits of FMEA is its preemptive approach to problem-solving.
By anticipating potential failure modes, teams can design processes or systems that are more robust and less likely to encounter these issues.
This results in higher quality products and services.
FMEA also encourages a collaborative environment, as it often involves multiple team members from different disciplines.
This not only enhances teamwork but also ensures that various perspectives are considered in the risk analysis.
Additionally, FMEA can lead to improved customer satisfaction.
By delivering reliable products that perform as expected, businesses can build stronger, trust-based relationships with their customers.
How is FMEA Conducted?
Conducting an FMEA follows several steps.
First, a cross-functional team is assembled.
The team then conducts a thorough analysis, starting with listing all potential failure modes in the product or process.
Next, the team assesses the potential impact of each failure using a scoring system based on severity, occurrence, and detection capability.
The scores provide a Risk Priority Number (RPN) that helps prioritize which failure modes require immediate attention.
After identification and prioritization, the team brainstorms ways to mitigate these risks.
This could involve redesigning parts of the product, implementing additional testing, or incorporating more robust materials.
Finally, actions are taken to address the identified risks.
The impact of these actions is monitored and may be incorporated into future iterations of the FMEA process.
The Relationship Between DR and FMEA
While DR and FMEA serve different purposes, they complement each other within the risk management framework.
Both prioritize detecting and addressing potential issues early in the product lifecycle, which saves time, money, and resources later on.
DR is focused more on the validation and verification of design against specifications and requirements.
It ensures that designs are sound before advancing to the next phases.
On the other hand, FMEA takes an in-depth look at potential failure points and prioritizes them based on risk.
While DR covers broad aspects of design, FMEA goes into detail about functional and process-related issues.
When used in conjunction, DR and FMEA drive superior quality and performance of the final product by leveraging their respective strengths.
Conducting both helps provide comprehensive coverage of risk areas, creating a robust framework for achieving product or service excellence.
By understanding and effectively implementing DR and FMEA, teams can not only meet but exceed quality and reliability expectations.
This synergy ultimately results in better products, satisfied customers, and successful projects.
資料ダウンロード
QCD管理受発注クラウド「newji」は、受発注部門で必要なQCD管理全てを備えた、現場特化型兼クラウド型の今世紀最高の受発注管理システムとなります。
ユーザー登録
受発注業務の効率化だけでなく、システムを導入することで、コスト削減や製品・資材のステータス可視化のほか、属人化していた受発注情報の共有化による内部不正防止や統制にも役立ちます。
NEWJI DX
製造業に特化したデジタルトランスフォーメーション(DX)の実現を目指す請負開発型のコンサルティングサービスです。AI、iPaaS、および先端の技術を駆使して、製造プロセスの効率化、業務効率化、チームワーク強化、コスト削減、品質向上を実現します。このサービスは、製造業の課題を深く理解し、それに対する最適なデジタルソリューションを提供することで、企業が持続的な成長とイノベーションを達成できるようサポートします。
製造業ニュース解説
製造業、主に購買・調達部門にお勤めの方々に向けた情報を配信しております。
新任の方やベテランの方、管理職を対象とした幅広いコンテンツをご用意しております。
お問い合わせ
コストダウンが利益に直結する術だと理解していても、なかなか前に進めることができない状況。そんな時は、newjiのコストダウン自動化機能で大きく利益貢献しよう!
(β版非公開)