- お役立ち記事
- Mastering Workplace Efficiency: The 5S Methodology from Japanese Manufacturing
月間77,185名の
製造業ご担当者様が閲覧しています*
*2025年2月28日現在のGoogle Analyticsのデータより
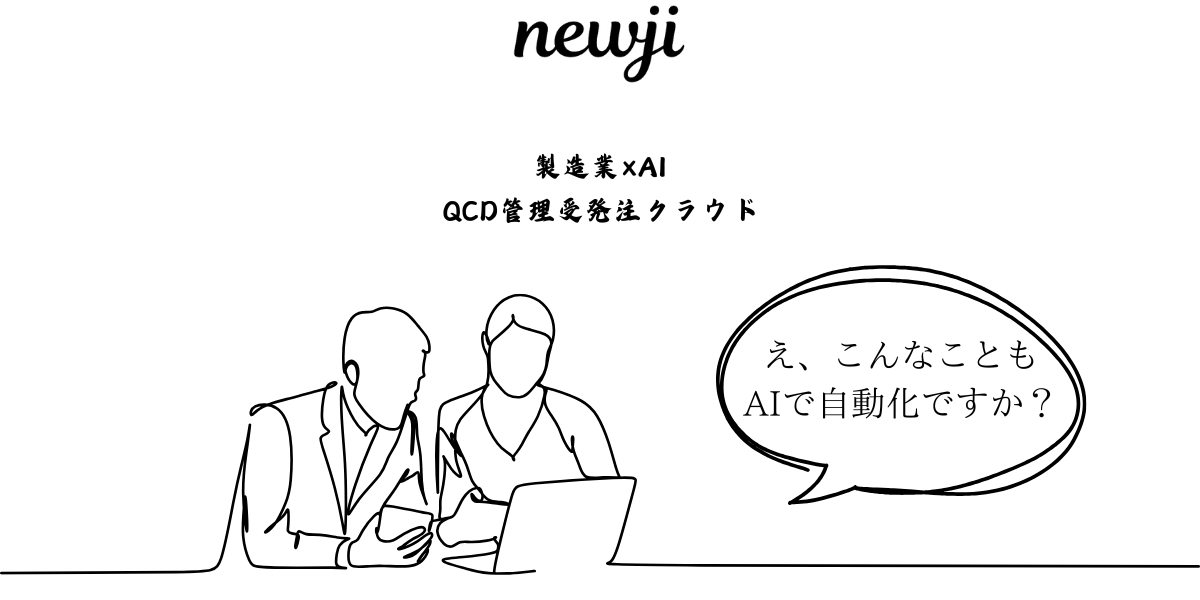
Mastering Workplace Efficiency: The 5S Methodology from Japanese Manufacturing
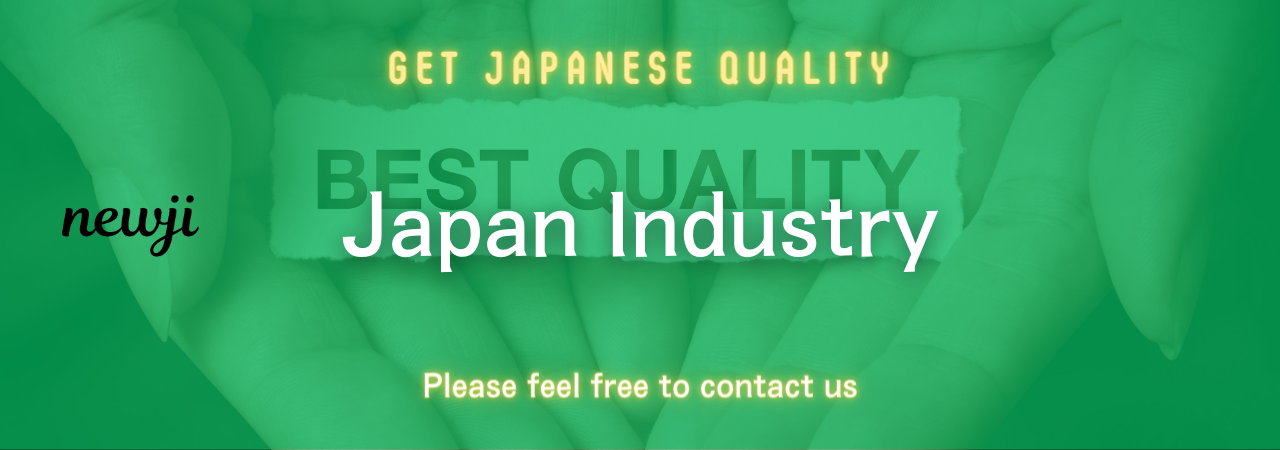
目次
Introduction to the 5S Methodology
The 5S methodology is a cornerstone of Japanese manufacturing efficiency practices. It originates from five Japanese words: Seiri, Seiton, Seiso, Seiketsu, and Shitsuke.
These terms translate to Sort, Set in Order, Shine, Standardize, and Sustain in English.
The 5S methodology aims to create and maintain an organized, clean, and efficient workplace.
By implementing these principles, companies can enhance productivity, reduce waste, and improve overall quality.
The methodology is not only applicable to manufacturing but also extends to various business operations, including procurement and purchasing.
Seiri (Sort)
Seiri involves identifying and eliminating unnecessary items from the workplace.
In procurement and purchasing, this means reviewing suppliers, materials, and processes to determine what is essential.
By sorting through suppliers, companies can focus on those that provide the best value and quality.
Removing redundant or low-performing suppliers streamlines the procurement process.
This step reduces clutter, minimizes confusion, and ensures that only critical resources are utilized.
Seiton (Set in Order)
Seiton emphasizes organizing and arranging items for optimal efficiency.
In the context of procurement, this involves organizing supplier information, contracts, and purchase orders systematically.
Implementing digital tools and software can aid in categorizing and accessing procurement data swiftly.
Proper organization facilitates quicker decision-making and enhances communication with suppliers.
A well-ordered procurement system reduces the time spent searching for information and increases overall efficiency.
Seiso (Shine)
Seiso focuses on maintaining cleanliness and orderliness in the workplace.
For procurement departments, this translates to maintaining accurate and up-to-date records.
Regular audits and reviews ensure that procurement data is clean and free from errors.
A clean procurement process minimizes the risk of mistakes, such as duplicate orders or incorrect deliveries.
Shine also involves fostering a culture of accountability, where team members take responsibility for maintaining organized records.
Seiketsu (Standardize)
Seiketsu aims to standardize best practices across processes.
In procurement and purchasing, this means developing standardized procedures for supplier selection, evaluation, and management.
Standardization ensures consistency, reduces variability, and enhances the reliability of procurement activities.
Implementing standard operating procedures (SOPs) allows for easier training and onboarding of new team members.
Consistent processes lead to more predictable outcomes and facilitate continuous improvement.
Shitsuke (Sustain)
Shitsuke is about sustaining and embedding the 5S principles into the organizational culture.
For procurement departments, sustaining 5S requires ongoing training, monitoring, and reinforcement of best practices.
Regular reviews and feedback sessions help maintain adherence to standardized procedures.
Encouraging a culture of continuous improvement motivates team members to uphold 5S principles.
Sustaining 5S ensures that efficiency gains are maintained over the long term and adapt to changing business needs.
Implementing 5S in Procurement and Purchasing
Implementing the 5S methodology in procurement involves adapting each step to fit the unique requirements of purchasing operations.
Starting with Sort, procurement teams must evaluate their current suppliers and processes to identify areas of improvement.
Set in Order involves organizing procurement data and establishing clear workflows.
Shine requires maintaining accurate records and ensuring transparency in procurement activities.
Standardize entails creating consistent procedures for supplier interactions and contract management.
Sustain focuses on embedding these practices into the daily routines of the procurement team.
Assessing Current Procurement Processes
Before implementing 5S, it’s crucial to assess the current state of procurement processes.
Identify bottlenecks, inefficiencies, and areas where waste occurs.
Gather feedback from team members to understand challenges and opportunities for improvement.
This assessment provides a baseline for measuring the impact of 5S implementation.
Developing a 5S Implementation Plan
Create a detailed plan outlining the steps for implementing each of the 5S principles.
Assign responsibilities to team members and set achievable timelines.
Provide training to ensure that everyone understands the 5S concepts and their role in the process.
Establish metrics to monitor progress and evaluate the effectiveness of the implementation.
Advantages and Disadvantages of 5S
The 5S methodology offers numerous advantages for procurement and purchasing departments, but it also has some challenges.
Advantages
5S enhances workplace organization, leading to increased efficiency and productivity.
It reduces waste by eliminating unnecessary processes and resources.
Standardization ensures consistency and reliability in procurement activities.
A clean and organized procurement environment fosters better decision-making and collaboration.
Continuous improvement drives long-term sustainability and adaptability to market changes.
Disadvantages
Implementing 5S can require significant time and resources upfront.
There may be resistance to change from team members accustomed to existing processes.
Maintaining 5S principles requires ongoing commitment and discipline.
If not properly implemented, 5S can lead to superficial changes without addressing underlying issues.
Balancing standardization with flexibility can be challenging in dynamic market conditions.
Supplier Negotiation Techniques and 5S
Effective supplier negotiation is essential for successful procurement, and the 5S methodology can enhance these negotiations.
Preparation and Information Management
Sorting and setting in order involve collecting and organizing all relevant supplier information.
Having accurate and comprehensive data enables better negotiation strategies.
Understand the supplier’s strengths, weaknesses, and market position to leverage during negotiations.
Standardized Negotiation Processes
Standardizing negotiation procedures ensures consistency and fairness.
Develop templates and frameworks for common negotiation scenarios.
Standardization reduces the likelihood of errors and enhances the professionalism of negotiations.
Building Long-term Relationships
Sustain involves fostering strong relationships with key suppliers.
Building trust and mutual respect leads to more favorable terms and collaboration.
Long-term relationships can result in better pricing, priority service, and improved quality.
Market Conditions and 5S
Understanding market conditions is crucial for effective procurement and purchasing.
Adapting to Market Fluctuations
5S enables procurement teams to respond swiftly to changes in market conditions.
An organized and efficient process allows for quicker adjustments to sourcing strategies.
This adaptability helps maintain supply chain stability and mitigate risks associated with market volatility.
Supplier Market Analysis
Regularly analyze the supplier market to identify trends and opportunities.
Use standardized processes to evaluate new suppliers and assess their fit with organizational needs.
Staying informed about market conditions ensures that procurement strategies remain relevant and competitive.
Best Practices for 5S in Procurement and Purchasing
Adopting best practices ensures the successful implementation and sustainability of the 5S methodology.
Continuous Training and Education
Provide ongoing training to keep the procurement team updated on 5S principles and industry best practices.
Continuous education fosters a culture of learning and improvement within the department.
Regular Audits and Assessments
Conduct regular audits to assess adherence to 5S principles.
Use these assessments to identify areas for improvement and recognize achievements.
Audits help maintain accountability and ensure that 5S practices are consistently applied.
Leveraging Technology
Implement digital tools and software to support 5S initiatives.
Technology can aid in organizing procurement data, automating routine tasks, and enhancing communication.
Leveraging technology increases efficiency and reduces the risk of human error.
Encouraging Team Involvement
Engage the entire procurement team in the 5S implementation process.
Encourage team members to contribute ideas and participate in continuous improvement efforts.
A collaborative approach ensures buy-in and sustained commitment to 5S principles.
Conclusion
The 5S methodology offers a structured approach to enhancing workplace efficiency in procurement and purchasing.
By sorting, setting in order, shining, standardizing, and sustaining best practices, organizations can achieve significant improvements in productivity and quality.
Despite some challenges, the benefits of implementing 5S—such as reduced waste, improved organization, and stronger supplier relationships—make it a valuable strategy for modern manufacturing companies.
Embracing the 5S principles fosters a culture of continuous improvement, positioning companies to thrive in competitive and dynamic markets.
Integrating 5S into procurement processes not only streamlines operations but also contributes to the overall success and sustainability of the organization.
資料ダウンロード
QCD管理受発注クラウド「newji」は、受発注部門で必要なQCD管理全てを備えた、現場特化型兼クラウド型の今世紀最高の受発注管理システムとなります。
ユーザー登録
受発注業務の効率化だけでなく、システムを導入することで、コスト削減や製品・資材のステータス可視化のほか、属人化していた受発注情報の共有化による内部不正防止や統制にも役立ちます。
NEWJI DX
製造業に特化したデジタルトランスフォーメーション(DX)の実現を目指す請負開発型のコンサルティングサービスです。AI、iPaaS、および先端の技術を駆使して、製造プロセスの効率化、業務効率化、チームワーク強化、コスト削減、品質向上を実現します。このサービスは、製造業の課題を深く理解し、それに対する最適なデジタルソリューションを提供することで、企業が持続的な成長とイノベーションを達成できるようサポートします。
製造業ニュース解説
製造業、主に購買・調達部門にお勤めの方々に向けた情報を配信しております。
新任の方やベテランの方、管理職を対象とした幅広いコンテンツをご用意しております。
お問い合わせ
コストダウンが利益に直結する術だと理解していても、なかなか前に進めることができない状況。そんな時は、newjiのコストダウン自動化機能で大きく利益貢献しよう!
(β版非公開)