- お役立ち記事
- Unlocking Efficiency: The Role of Real-time Ethernet in Revolutionizing Japanese Manufacturing
月間77,185名の
製造業ご担当者様が閲覧しています*
*2025年2月28日現在のGoogle Analyticsのデータより
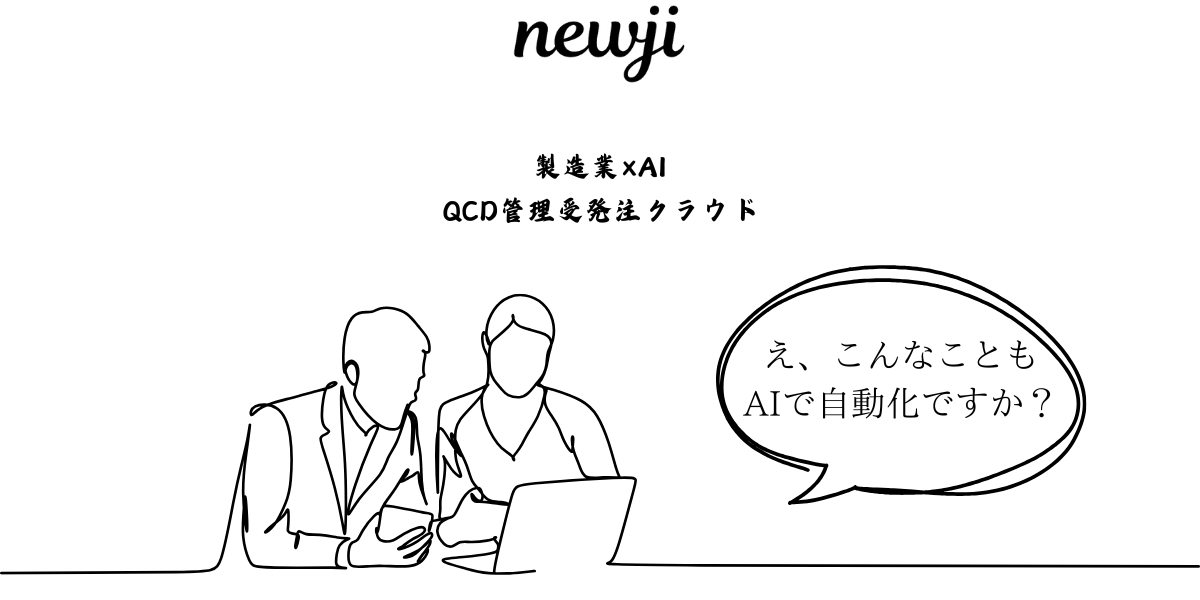
Unlocking Efficiency: The Role of Real-time Ethernet in Revolutionizing Japanese Manufacturing
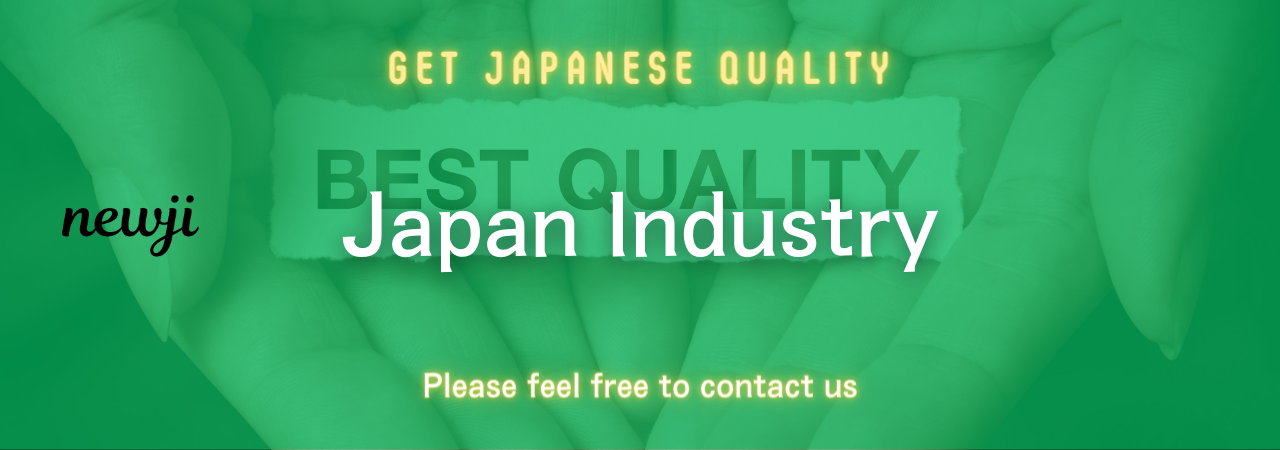
目次
Introduction
Real-time Ethernet is rapidly transforming the landscape of Japanese manufacturing.
As industries strive for higher efficiency and precision, the adoption of advanced networking technologies becomes paramount.
This article delves into the pivotal role of Real-time Ethernet in revolutionizing manufacturing processes in Japan.
We will explore practical insights from the procurement and purchasing perspective, examine the advantages and disadvantages, discuss supplier negotiation techniques, analyze market conditions, and highlight best practices for successful implementation.
Understanding Real-time Ethernet
What is Real-time Ethernet?
Real-time Ethernet is a specialized form of Ethernet designed to meet the stringent timing and reliability requirements of industrial environments.
Unlike standard Ethernet, which prioritizes data throughput, Real-time Ethernet ensures deterministic communication with minimal latency and jitter.
This capability is crucial for applications where precise timing is essential, such as automated machinery control and real-time data acquisition.
How It Differs from Standard Ethernet
Standard Ethernet operates on a best-effort basis, meaning that data packets are delivered as resources allow, without guarantees on delivery time.
In contrast, Real-time Ethernet incorporates mechanisms like time synchronization, priority-based scheduling, and redundant pathways to ensure timely and reliable data transmission.
These features make Real-time Ethernet suitable for mission-critical applications where delays or data loss can result in significant operational disruptions.
The Importance of Real-time Ethernet in Manufacturing
In the highly competitive manufacturing sector, especially within Japan, efficiency and precision are non-negotiable.
Real-time Ethernet addresses these needs by facilitating seamless communication between machines, sensors, and control systems.
This integration enables real-time monitoring, rapid response to changes in the production line, and enhanced automation capabilities.
Furthermore, Real-time Ethernet supports Industry 4.0 initiatives, driving the digital transformation of manufacturing processes.
Advantages of Real-time Ethernet in Japanese Manufacturing
Enhanced Communication
Real-time Ethernet provides robust and reliable communication channels between various components of the manufacturing ecosystem.
This enhanced connectivity ensures that data flows smoothly and promptly, enabling better coordination and synchronization across the production line.
As a result, manufacturers can achieve higher operational efficiency and reduce downtime caused by communication breakdowns.
Improved Efficiency
By enabling real-time data exchange, Real-time Ethernet allows for immediate adjustments to manufacturing processes based on current data insights.
This capability minimizes waste, optimizes resource utilization, and accelerates production cycles.
In Japanese manufacturing settings, where precision and lean manufacturing principles are highly valued, Real-time Ethernet plays a critical role in maintaining high efficiency levels.
Scalability
Real-time Ethernet systems are highly scalable, allowing manufacturers to expand their operations without significant overhauls to the existing network infrastructure.
This scalability is particularly beneficial for Japanese manufacturers looking to grow or diversify their production lines while maintaining seamless communication across all levels.
Disadvantages and Challenges
Implementation Costs
One of the primary challenges associated with Real-time Ethernet is the initial cost of implementation.
Upgrading existing networks or installing new Real-time Ethernet systems can require substantial investment in hardware, software, and training.
For some manufacturers, especially small to medium-sized enterprises, these costs may pose a significant barrier to adoption.
Technical Complexity
Real-time Ethernet systems are inherently more complex than standard Ethernet networks.
They demand a higher level of technical expertise for installation, configuration, and maintenance.
Japanese manufacturers may need to invest in specialized training for their personnel or partner with experienced suppliers to effectively manage these systems.
Real-world Applications in Japanese Factories
Numerous Japanese manufacturing giants have successfully integrated Real-time Ethernet into their production lines.
For instance, automotive manufacturers utilize Real-time Ethernet to synchronize robotic assembly units, ensuring consistent quality and reducing assembly time.
Electronics manufacturers employ it for precision machining and real-time monitoring of production parameters, leading to higher product reliability and faster time-to-market.
These applications demonstrate the tangible benefits of Real-time Ethernet in enhancing manufacturing performance.
Supplier Negotiation Techniques for Real-time Ethernet Solutions
Building Relationships
In Japanese business culture, establishing strong relationships with suppliers is crucial.
When negotiating for Real-time Ethernet solutions, manufacturers should focus on building trust and long-term partnerships.
Regular communication, transparency in requirements, and mutual respect are key elements that can lead to more favorable terms and better collaboration.
Leveraging Technical Expertise
Suppliers of Real-time Ethernet solutions often possess deep technical knowledge.
Manufacturers should leverage this expertise by engaging in collaborative discussions to tailor solutions that meet their specific needs.
By involving suppliers in the planning and implementation phases, manufacturers can ensure that the solutions are optimized for their unique operational requirements.
Market Conditions Impacting Real-time Ethernet Adoption
Current Trends
The global push towards Industry 4.0 and the increasing demand for automation and smart manufacturing are driving the adoption of Real-time Ethernet in Japan.
Technological advancements in networking hardware and software are making Real-time Ethernet more accessible and cost-effective.
Moreover, the COVID-19 pandemic has underscored the importance of resilient and adaptable manufacturing systems, further accelerating the adoption of advanced networking solutions.
Future Outlook
Looking ahead, the market for Real-time Ethernet is expected to grow significantly.
Factors such as the continuous evolution of manufacturing technologies, the rise of the Internet of Things (IoT), and the need for seamless data integration will propel further adoption.
Japanese manufacturers are poised to benefit from these trends, maintaining their competitive edge through the implementation of Real-time Ethernet solutions.
Best Practices for Implementing Real-time Ethernet
Planning and Assessment
Successful implementation of Real-time Ethernet begins with thorough planning and assessment.
Manufacturers should evaluate their current network infrastructure, identify specific needs, and set clear objectives for what they aim to achieve with Real-time Ethernet.
Conducting a detailed analysis helps in selecting the appropriate technology and avoiding potential pitfalls during deployment.
Training and Support
Equipping the workforce with the necessary skills to manage Real-time Ethernet systems is essential.
Investing in comprehensive training programs ensures that employees can effectively operate and maintain the new network infrastructure.
Additionally, establishing a support framework, either in-house or through partnerships with suppliers, can facilitate ongoing maintenance and troubleshooting.
Integration with Existing Systems
For a seamless transition, Real-time Ethernet should be integrated with existing manufacturing systems and processes.
This integration requires careful planning to ensure compatibility and minimize disruptions.
Employing standardized protocols and ensuring interoperability between new and legacy systems can enhance the overall efficiency of the manufacturing operation.
Continuous Monitoring and Optimization
Post-implementation, continuous monitoring of the Real-time Ethernet network is crucial to maintain optimal performance.
Regular assessments allow manufacturers to identify and address any emerging issues promptly.
Moreover, ongoing optimization efforts can further enhance network efficiency and support the evolving needs of the manufacturing process.
Conclusion
Real-time Ethernet is a transformative technology that is revolutionizing Japanese manufacturing by enhancing communication, improving efficiency, and enabling scalable operations.
While there are challenges related to implementation costs and technical complexity, the benefits far outweigh the drawbacks for manufacturers committed to maintaining a competitive edge.
By adopting best practices in planning, training, integration, and continuous monitoring, Japanese manufacturers can fully unlock the potential of Real-time Ethernet.
As the manufacturing landscape continues to evolve, Real-time Ethernet will undoubtedly remain a cornerstone of innovation and efficiency in Japan’s industrial sector.
資料ダウンロード
QCD管理受発注クラウド「newji」は、受発注部門で必要なQCD管理全てを備えた、現場特化型兼クラウド型の今世紀最高の受発注管理システムとなります。
ユーザー登録
受発注業務の効率化だけでなく、システムを導入することで、コスト削減や製品・資材のステータス可視化のほか、属人化していた受発注情報の共有化による内部不正防止や統制にも役立ちます。
NEWJI DX
製造業に特化したデジタルトランスフォーメーション(DX)の実現を目指す請負開発型のコンサルティングサービスです。AI、iPaaS、および先端の技術を駆使して、製造プロセスの効率化、業務効率化、チームワーク強化、コスト削減、品質向上を実現します。このサービスは、製造業の課題を深く理解し、それに対する最適なデジタルソリューションを提供することで、企業が持続的な成長とイノベーションを達成できるようサポートします。
製造業ニュース解説
製造業、主に購買・調達部門にお勤めの方々に向けた情報を配信しております。
新任の方やベテランの方、管理職を対象とした幅広いコンテンツをご用意しております。
お問い合わせ
コストダウンが利益に直結する術だと理解していても、なかなか前に進めることができない状況。そんな時は、newjiのコストダウン自動化機能で大きく利益貢献しよう!
(β版非公開)