- お役立ち記事
- Basics of fracture mechanics and how to apply them to crack growth analysis and life estimation technology
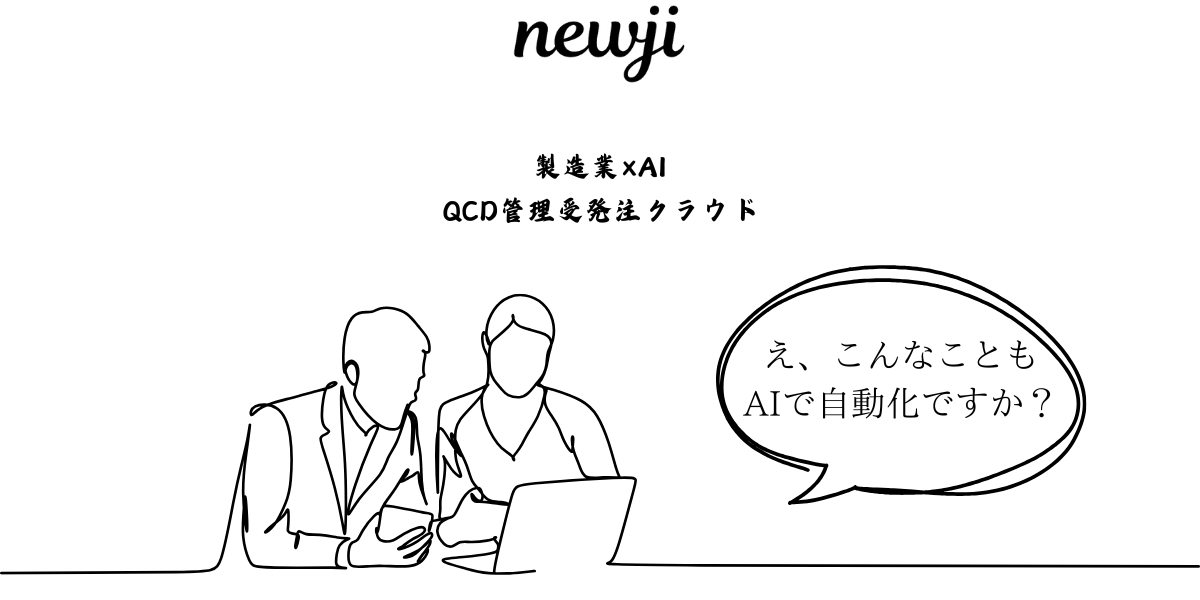
Basics of fracture mechanics and how to apply them to crack growth analysis and life estimation technology
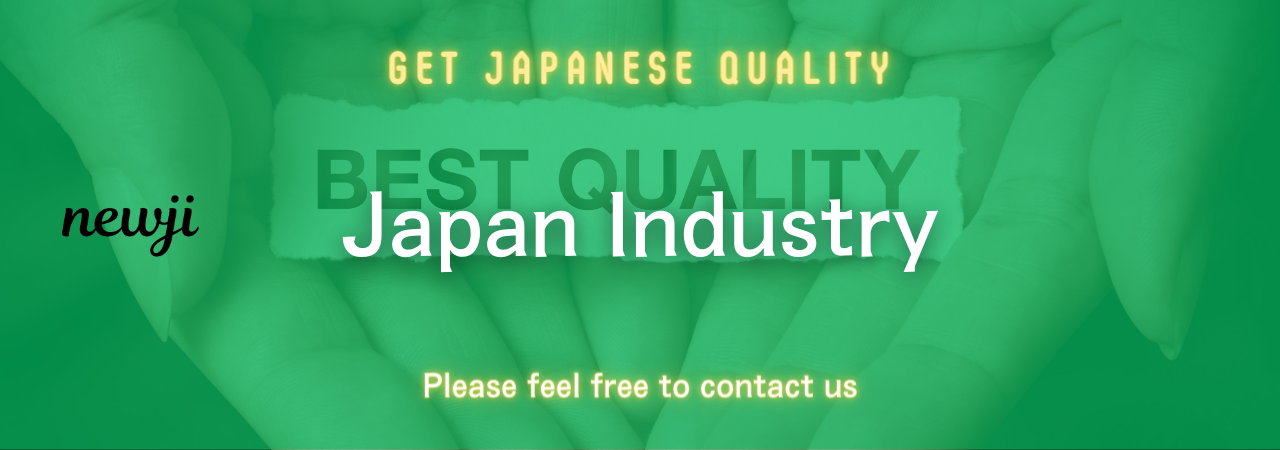
Fracture mechanics is a vital field of study in engineering and materials science, concerned with understanding how and why materials fail due to crack growth and fracture.
This domain provides critical insights for designing safer and more durable products by predicting how cracks advance in various materials and estimating the life expectancy of components under stress.
目次
Understanding Fracture Mechanics
Fracture mechanics is primarily focused on analyzing stress and strain at the tip of a crack, which is a critical region for understanding material failure.
The discipline integrates concepts from material science, physics, and engineering to predict and mitigate the failure of structures and components.
At its core, fracture mechanics is about understanding three fundamental parameters: stress intensity factor (K), crack tip opening displacement (CTOD), and the J-integral.
These parameters help in quantifying the crack driving forces and the resistance offered by the material.
Stress Intensity Factor
The stress intensity factor (K) is a measure of the stress state near a crack tip and is fundamental in the linear-elastic fracture mechanics (LEFM) framework.
It relates to the size and shape of the crack, the type of loading, and the material properties.
K helps predict crack growth under varied loading conditions, acting as a threshold parameter beyond which a crack will propagate.
Crack Tip Opening Displacement
Crack Tip Opening Displacement (CTOD) is a measure of deformation at the crack tip, indicating how much the faces of the crack have opened under stress.
CTOD is crucial in elastic-plastic fracture mechanics, relevant when materials do not behave in a perfectly elastic manner.
It is beneficial for metals and alloys that exhibit significant plasticity before failure.
J-Integral
The J-integral is another critical parameter in fracture mechanics, providing a way to quantify the energy release rate associated with crack propagation under both linear and non-linear conditions.
It is particularly useful in elastic-plastic materials to evaluate the stability of crack growth and predict failure under complex loading scenarios.
Applications of Fracture Mechanics to Crack Growth Analysis
Fracture mechanics plays a significant role in crack growth analysis by helping engineers understand how cracks initiate and propagate in different materials and structures.
This analysis is vital for industries such as aerospace, automotive, civil engineering, and energy, where component failure can lead to catastrophic consequences.
Fatigue Crack Growth
In many applications, materials are subject to cyclic loading, leading to fatigue crack growth.
Fracture mechanics allows for the assessment of fatigue life by predicting crack growth rates using Paris’ Law, which relates the stress intensity factor range to the crack growth rate.
This analysis helps in designing components that can withstand repeated loading without failure.
Fracture Toughness Testing
Fracture toughness testing is essential for determining a material’s resistance to crack propagation.
By testing specimens under controlled conditions, engineers can identify critical stress intensity factors, helping design safer materials and structures.
This knowledge is useful in ensuring that components can withstand operational stresses without catastrophic fracture.
Failure Analysis
Fracture mechanics is a crucial tool in failure analysis, helping determine the cause of material failure in damaged components.
By examining fracture surfaces and analyzing crack paths, engineers can identify failure origins and conditions.
This information is instrumental in preventing future failures by improving design and material selection.
Life Estimation Technology in Fracture Mechanics
Life estimation technology utilizes fracture mechanics principles to estimate the remaining service life of materials and components.
By understanding crack growth behavior and material properties, engineers can perform predictive maintenance, extending the lifespan of structures and minimizing unexpected failures.
Predictive Maintenance
Using fracture mechanics insight, industries can implement predictive maintenance strategies that rely on regular inspections and monitoring to detect small cracks before they become critical.
This proactive approach prolongs the life of components, enhances safety, and reduces costs associated with unplanned downtime.
Finite Element Analysis
Finite Element Analysis (FEA) is a powerful computational tool used in conjunction with fracture mechanics to model crack propagation and predict the behavior of cracks under various loading conditions.
FEA allows engineers to simulate real-world scenarios, leading to more accurate predictions of crack growth and component life.
Design for Durability
Incorporating fracture mechanics principles into the design phase ensures that products are built to withstand the stresses they will encounter throughout their life cycle.
By selecting appropriate materials and incorporating design features that mitigate crack initiation and propagation, engineers can significantly enhance durability and reliability.
Conclusion
Fracture mechanics is a foundational aspect of engineering that provides essential insights into the behavior of materials under stress and crack growth.
By understanding and applying these principles, engineers can design safer and more durable products, accurately predict component lifespan, and implement maintenance strategies that prevent catastrophic failures.
In a world where the integrity of materials often dictates safety and success, the application of fracture mechanics continues to be a critical factor in engineering excellence.
資料ダウンロード
QCD調達購買管理クラウド「newji」は、調達購買部門で必要なQCD管理全てを備えた、現場特化型兼クラウド型の今世紀最高の購買管理システムとなります。
ユーザー登録
調達購買業務の効率化だけでなく、システムを導入することで、コスト削減や製品・資材のステータス可視化のほか、属人化していた購買情報の共有化による内部不正防止や統制にも役立ちます。
NEWJI DX
製造業に特化したデジタルトランスフォーメーション(DX)の実現を目指す請負開発型のコンサルティングサービスです。AI、iPaaS、および先端の技術を駆使して、製造プロセスの効率化、業務効率化、チームワーク強化、コスト削減、品質向上を実現します。このサービスは、製造業の課題を深く理解し、それに対する最適なデジタルソリューションを提供することで、企業が持続的な成長とイノベーションを達成できるようサポートします。
オンライン講座
製造業、主に購買・調達部門にお勤めの方々に向けた情報を配信しております。
新任の方やベテランの方、管理職を対象とした幅広いコンテンツをご用意しております。
お問い合わせ
コストダウンが利益に直結する術だと理解していても、なかなか前に進めることができない状況。そんな時は、newjiのコストダウン自動化機能で大きく利益貢献しよう!
(Β版非公開)