- お役立ち記事
- Revolutionizing Japanese Manufacturing: The Impact of CAD Design on Modern Production Techniques
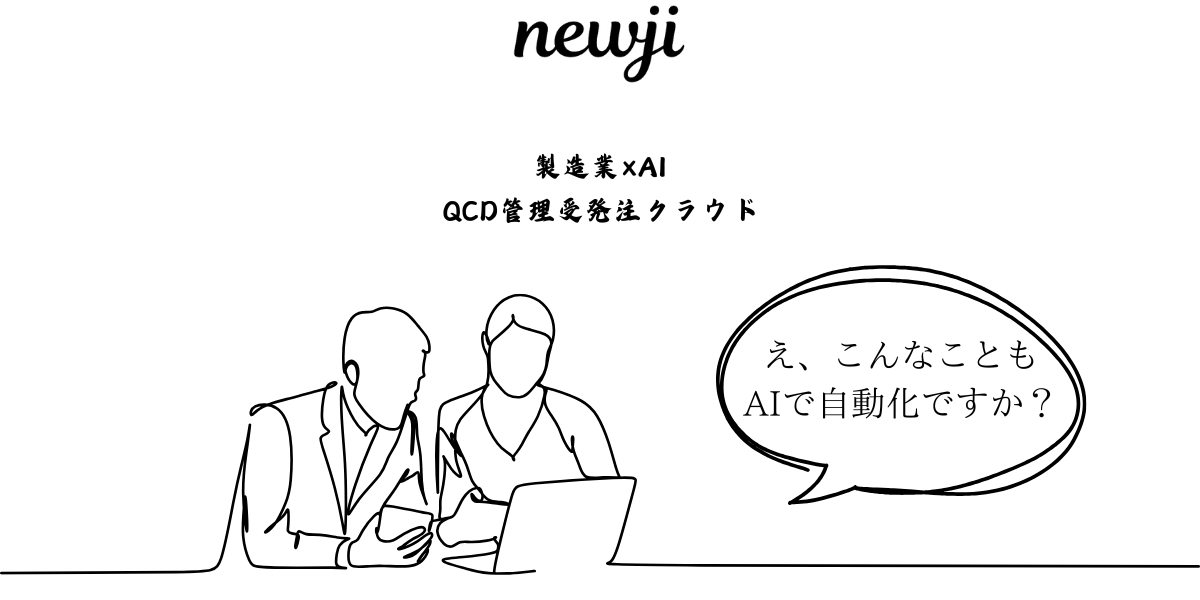
Revolutionizing Japanese Manufacturing: The Impact of CAD Design on Modern Production Techniques
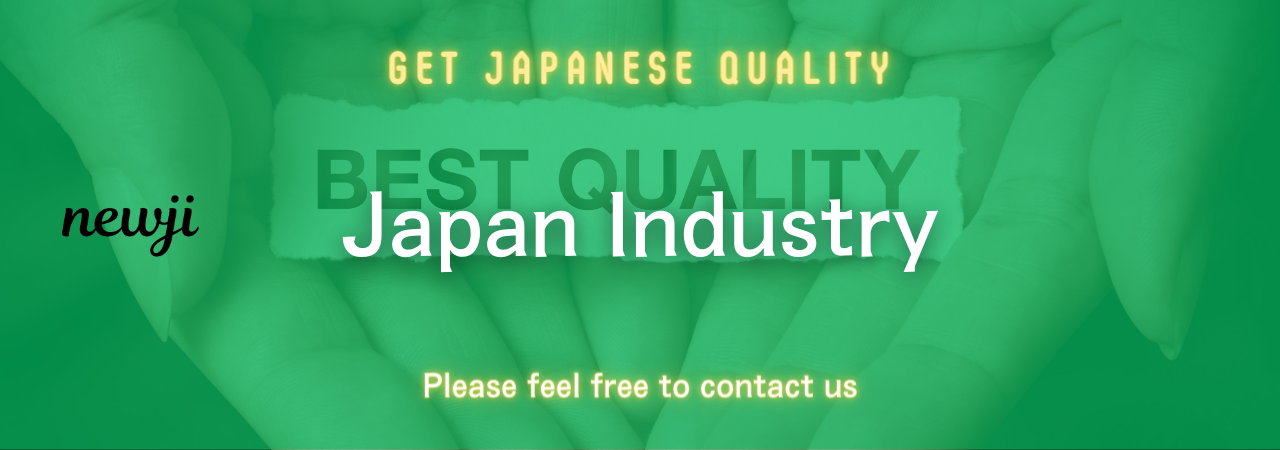
目次
Introduction to CAD Design in Japanese Manufacturing
Computer-Aided Design (CAD) has fundamentally transformed the landscape of manufacturing worldwide. In Japan, a country renowned for its precision, efficiency, and innovative manufacturing practices, CAD design plays a pivotal role in maintaining competitiveness and driving advancements in production techniques. This article explores the profound impact of CAD on modern Japanese manufacturing, particularly focusing on procurement and purchasing processes, supplier negotiations, market conditions, and best practices that have emerged from this technological integration.
The Evolution of CAD in Japanese Manufacturing
Historical Context
Japan’s manufacturing prowess has long been associated with concepts like Kaizen and Just-In-Time (JIT) production. The integration of CAD into these frameworks marked a significant leap forward. Early adoption of CAD in the Japanese manufacturing sector was driven by the need for greater precision, reduced lead times, and enhanced collaboration across different stages of production.
Technological Advancements
Over the past few decades, CAD technology has evolved from simple 2D drafting tools to sophisticated 3D modeling and simulation software. Japanese manufacturers have leveraged these advancements to design complex components, optimize assembly processes, and foresee potential manufacturing challenges before they arise. This proactive approach has minimized errors, reduced waste, and improved overall product quality.
Advantages of CAD Design in Modern Production Techniques
Enhanced Precision and Accuracy
CAD allows for meticulous design specifications, ensuring that each component meets exact dimensions and tolerances. This level of precision is crucial in industries such as automotive and electronics, where even minor deviations can lead to significant issues in the final product.
Accelerated Product Development
With CAD, Japanese manufacturers can rapidly prototype and iterate designs. This accelerates the product development cycle, enabling companies to bring new products to market more quickly and respond swiftly to changing consumer demands.
Improved Collaboration and Communication
CAD facilitates better communication between different departments, suppliers, and stakeholders. Detailed digital models can be easily shared and reviewed, ensuring that everyone involved has a clear understanding of design specifications and project requirements.
Cost Efficiency
By identifying potential design flaws early in the development process, CAD reduces the need for expensive rework and minimizes material waste. Additionally, optimized designs often lead to more efficient manufacturing processes, lowering overall production costs.
Challenges and Disadvantages of CAD Integration
High Initial Investment
Implementing CAD systems requires significant upfront costs, including software licenses, hardware upgrades, and training for staff. For smaller manufacturers, these expenses can be a barrier to adoption.
Complexity and Learning Curve
CAD software can be complex and requires a skilled workforce to operate effectively. Ensuring that employees are adequately trained and proficient in CAD tools is essential but can be time-consuming and costly.
Dependence on Technology
Reliance on CAD technology means that any system failures or software issues can disrupt the entire design and production process. Maintaining robust IT infrastructure and having contingency plans in place are critical to mitigating these risks.
Impact of CAD on Procurement and Purchasing
Streamlined Supplier Selection
CAD data provides detailed specifications that aid in the precise selection of suppliers. Procurement teams can assess potential suppliers based on their ability to meet specific design requirements, ensuring higher quality and better compatibility with production processes.
Enhanced Supplier Communication
With CAD, procurement and purchasing departments can communicate design changes and updates seamlessly with suppliers. This reduces misunderstandings and ensures that suppliers have accurate and up-to-date information, leading to more efficient order fulfillment.
Improved Inventory Management
CAD facilitates better forecasting and inventory planning by providing accurate data on material requirements. This helps procurement teams maintain optimal inventory levels, reducing the costs associated with overstocking or stockouts.
Supplier Negotiation Techniques
Effective negotiations with suppliers are crucial for securing favorable terms and ensuring quality. CAD-equipped procurement professionals can leverage detailed design information to negotiate better prices, lead times, and quality standards. By demonstrating a clear understanding of the design requirements, they can build stronger relationships with suppliers and drive mutual benefits.
Market Conditions Influenced by CAD in Japanese Manufacturing
Increased Competitiveness
The adoption of CAD has heightened the competitiveness of Japanese manufacturers in the global market. The ability to produce high-quality, innovative products quickly and efficiently has positioned Japanese companies as leaders in various industries, including automotive, electronics, and machinery.
Global Supply Chain Integration
CAD has facilitated the integration of global supply chains by enabling seamless collaboration across different geographic locations. Japanese manufacturers can work with suppliers from around the world more effectively, ensuring consistency and quality in their products.
Demand for Skilled Professionals
As CAD becomes more integral to manufacturing, there is a growing demand for professionals skilled in CAD software and related technologies. This has led to an emphasis on specialized training programs and education to equip the workforce with the necessary skills.
Best Practices for Implementing CAD in Japanese Manufacturing
Comprehensive Training Programs
Investing in thorough training for employees is essential to maximize the benefits of CAD. Companies should provide ongoing education and certifications to ensure that their workforce remains proficient in the latest CAD tools and techniques.
Integration with Existing Systems
Seamlessly integrating CAD with other enterprise systems, such as Enterprise Resource Planning (ERP) and Manufacturing Execution Systems (MES), enhances data flow and operational efficiency. This holistic approach ensures that design data is effectively utilized across the entire manufacturing process.
Continuous Improvement and Feedback
Adopting a Kaizen mindset, companies should continuously seek feedback on CAD processes and identify areas for improvement. Regular reviews and updates to CAD practices can lead to sustained enhancements in productivity and quality.
Collaboration with Suppliers
Engaging suppliers early in the design process fosters better collaboration and alignment. Sharing CAD models and design specifications with suppliers enables them to understand requirements fully and contribute valuable insights to the design and manufacturing processes.
Practical Insights from the Field
Case Study: Automotive Industry
In the Japanese automotive sector, CAD has been instrumental in designing complex vehicle components with high precision. For instance, Toyota utilizes advanced CAD systems to design engine parts that meet stringent performance and durability standards. This has not only improved product quality but also streamlined the procurement process by clearly defining material and manufacturing requirements for suppliers.
Electronics Manufacturing
Japanese electronics manufacturers use CAD to design intricate circuit boards and compact device housings. The ability to simulate thermal and mechanical stresses in CAD ensures that products are both functional and reliable. This meticulous design process aids procurement teams in selecting suppliers who can meet the exacting standards necessary for high-performance electronics.
Machinery and Equipment
In the machinery industry, CAD enables the design of highly specialized equipment tailored to specific manufacturing needs. By using CAD to create detailed models and simulations, companies can optimize machinery performance and ensure compatibility with existing production lines. This level of detail assists procurement departments in sourcing components that fit seamlessly into the overall system.
Advantages in Supplier Relationships
Enhanced Transparency
CAD fosters greater transparency between manufacturers and suppliers by providing clear and detailed design specifications. This transparency reduces the likelihood of errors and misunderstandings, fostering trust and stronger partnerships.
Joint Development Initiatives
Collaborative development projects become more feasible with CAD, as both parties can work on the same digital models. This joint approach accelerates innovation and ensures that both manufacturers and suppliers are aligned in their goals and processes.
Quality Assurance
CAD enables precise quality control measures by allowing manufacturers to specify exact tolerances and standards. Suppliers can use this information to implement rigorous quality assurance processes, ensuring that components meet the required specifications consistently.
Challenges in Supplier Negotiations with CAD
Standardization of Digital Data
One of the challenges in supplier negotiations is ensuring that all parties use standardized CAD formats. Variations in software and file types can hinder smooth collaboration and data sharing, necessitating agreements on common standards.
Intellectual Property Concerns
Sharing detailed CAD models with suppliers raises concerns about intellectual property (IP) protection. Manufacturers must establish clear agreements and safeguards to protect their designs while allowing suppliers to use the data effectively.
Managing Change Requests
During the production process, design changes may be necessary. Managing these change requests effectively requires robust communication channels and flexible negotiation strategies to accommodate adjustments without disrupting the supply chain.
Market Trends Shaping CAD Integration
Rise of Industry 4.0
Industry 4.0, characterized by the integration of digital technologies into manufacturing, has accelerated the adoption of CAD in Japanese manufacturing. Smart factories leverage CAD data for automation, real-time monitoring, and data-driven decision-making, enhancing overall production efficiency.
Sustainability and Eco-Friendly Design
There is a growing emphasis on sustainable manufacturing practices. CAD enables the design of eco-friendly products by optimizing material usage, reducing waste, and facilitating the creation of energy-efficient components. This aligns with the global trend towards sustainability and meets increasing consumer demand for environmentally responsible products.
Customization and Flexibility
Consumers increasingly demand personalized products, and CAD provides the flexibility needed to accommodate these preferences. Japanese manufacturers can use CAD to design customized components swiftly, catering to niche markets and enhancing customer satisfaction.
Best Practices for Procurement and Purchasing with CAD
Early Supplier Involvement
Involving suppliers early in the design process ensures that procurement considerations are integrated from the outset. This collaboration helps identify potential sourcing challenges and enables proactive solutions, leading to a more efficient procurement process.
Leveraging CAD for Cost Analysis
CAD models allow procurement teams to perform detailed cost analyses by breaking down components and materials. This enables more accurate budgeting and cost estimation, facilitating better financial planning and supplier negotiations.
Implementing Robust Data Management
Effective management of CAD data is critical for procurement and purchasing. Implementing robust data management systems ensures that all design information is accessible, secure, and up-to-date, supporting informed decision-making and efficient procurement operations.
Continuous Supplier Evaluation
Regularly evaluating supplier performance using CAD data ensures that suppliers consistently meet quality and delivery standards. This continuous assessment helps maintain high standards and fosters long-term, reliable supplier relationships.
Future Outlook: CAD and Japanese Manufacturing
Integration with Artificial Intelligence
The future of CAD in Japanese manufacturing involves deeper integration with artificial intelligence (AI). AI-driven CAD tools can automate complex design tasks, predict potential manufacturing issues, and optimize designs for performance and cost, further enhancing efficiency and innovation.
Virtual and Augmented Reality
Virtual and augmented reality technologies are set to complement CAD by providing immersive visualization of designs. This can enhance collaboration, improve design reviews, and facilitate better decision-making by allowing stakeholders to interact with virtual prototypes.
Sustainable and Smart Manufacturing
As sustainability becomes increasingly important, CAD will play a crucial role in designing eco-friendly products and smart manufacturing systems. This includes the development of energy-efficient components, recyclable materials, and intelligent systems that optimize resource usage.
Conclusion
CAD design has revolutionized Japanese manufacturing by enhancing precision, accelerating product development, and improving collaboration across various facets of production. While there are challenges in terms of initial investment and technological dependence, the advantages far outweigh the drawbacks. The integration of CAD into procurement and purchasing processes has streamlined supplier selection, improved communication, and enabled more effective cost management. As Japanese manufacturers continue to embrace technological advancements and industry trends, CAD will remain a cornerstone of their production techniques, driving innovation and maintaining their competitive edge in the global market. Implementing best practices, fostering strong supplier relationships, and staying abreast of emerging technologies will ensure that CAD continues to deliver substantial benefits to the manufacturing sector in Japan and beyond.
資料ダウンロード
QCD調達購買管理クラウド「newji」は、調達購買部門で必要なQCD管理全てを備えた、現場特化型兼クラウド型の今世紀最高の購買管理システムとなります。
ユーザー登録
調達購買業務の効率化だけでなく、システムを導入することで、コスト削減や製品・資材のステータス可視化のほか、属人化していた購買情報の共有化による内部不正防止や統制にも役立ちます。
NEWJI DX
製造業に特化したデジタルトランスフォーメーション(DX)の実現を目指す請負開発型のコンサルティングサービスです。AI、iPaaS、および先端の技術を駆使して、製造プロセスの効率化、業務効率化、チームワーク強化、コスト削減、品質向上を実現します。このサービスは、製造業の課題を深く理解し、それに対する最適なデジタルソリューションを提供することで、企業が持続的な成長とイノベーションを達成できるようサポートします。
オンライン講座
製造業、主に購買・調達部門にお勤めの方々に向けた情報を配信しております。
新任の方やベテランの方、管理職を対象とした幅広いコンテンツをご用意しております。
お問い合わせ
コストダウンが利益に直結する術だと理解していても、なかなか前に進めることができない状況。そんな時は、newjiのコストダウン自動化機能で大きく利益貢献しよう!
(Β版非公開)