- お役立ち記事
- Fundamentals of sensorless vector control and application to permanent magnet synchronous motor control
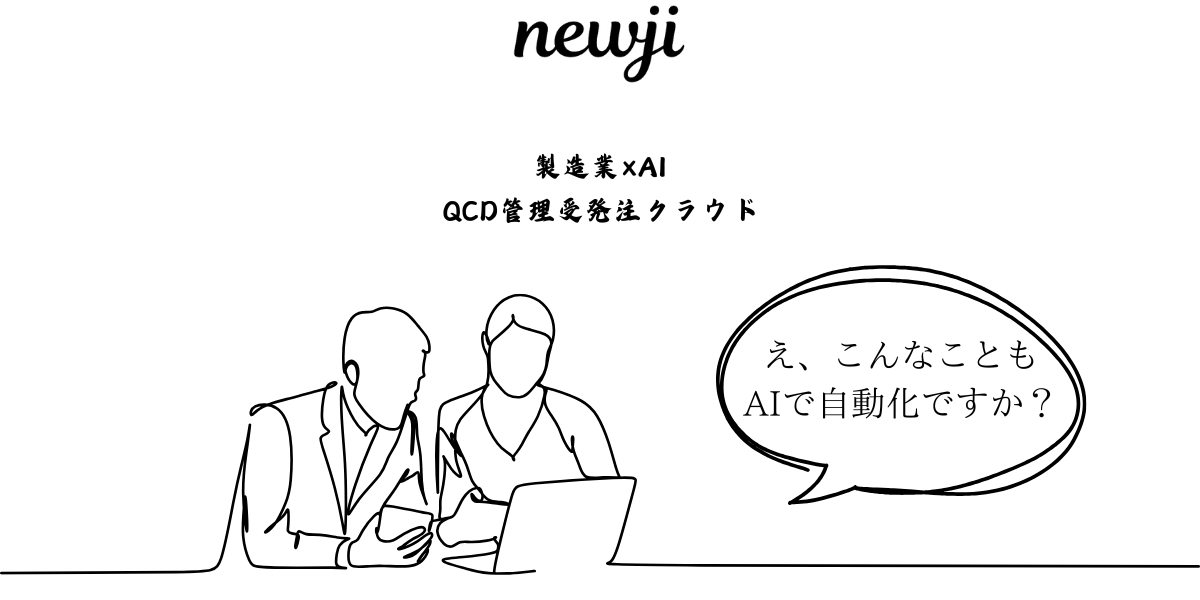
Fundamentals of sensorless vector control and application to permanent magnet synchronous motor control
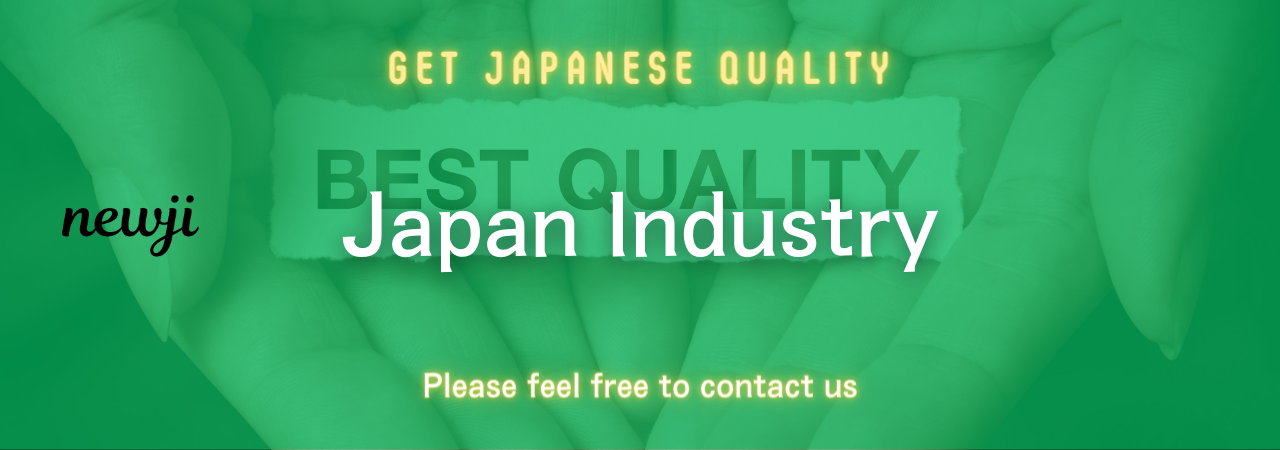
目次
Understanding Sensorless Vector Control
Sensorless vector control is a significant advancement in the field of motor control technology.
It eliminates the need for physical sensors in determining critical motor parameters using mathematical models and algorithms.
This technology finds its applications primarily in the control of Permanent Magnet Synchronous Motors (PMSMs), enhancing their efficiency and reliability.
What is Sensorless Vector Control?
Sensorless vector control is a technique used in electric motor drives to control the torque and speed of an electric motor without the need for physical sensors.
Traditional motor control methods rely heavily on physical sensors to determine key operational parameters like rotor position and speed.
However, sensorless vector control, leverages advanced algorithms and the motor’s inherent properties.
The use of such algorithms allows for estimation of these parameters with high accuracy without the physical presence of sensors.
By eliminating the need for sensors, sensorless vector control reduces the physical complexity of the motor control system.
There’s a decrease in wiring, fewer failure points, and a reduction in maintenance requirements.
Additionally, fewer sensors lead to reduced costs and increased system reliability.
The Importance of Permanent Magnet Synchronous Motors
Permanent Magnet Synchronous Motors (PMSMs) are renowned for their efficiency and remarkable performance characteristics.
Used in a variety of applications, PMSMs are preferred for their compact size and high torque density.
PMSMs have permanent magnets embedded within the rotor, which eliminates the need for external excitation and results in high efficiency and precise control.
Incorporating sensorless vector control for PMSMs magnifies these advantages.
It optimizes performance by providing smooth, precise control over the motor’s speed and torque without relying on sensors.
The Working Principle of Sensorless Vector Control
Sensorless vector control essentially revolves around real-time algorithms that estimate rotor position and speed.
This is based on the parameters derived from the motor’s back electromotive force (EMF) and its inductance.
These algorithms are integrated into the motor drive’s control system software and continuously process the current and voltage signals.
The core of sensorless vector control is the Field-Oriented Control (FOC) method.
FOC involves controlling the motor’s stator currents.
This is done by decomposing them into two orthogonal components: one that is responsible for generating torque and the other for field flux.
Facilitating the independent control of these two components allows for efficient, dynamic motor control.
The sensorless vector control systems deploy state observers and adaptive algorithms to estimate vital motor states.
The adaptability of these algorithms ensures that, even in varying operational conditions, the estimations maintain high accuracy.
Benefits of Sensorless Vector Control
There are numerous benefits of adopting sensorless vector control in PMSM systems:
1. **Cost-Effectiveness**: By eliminating position and speed sensors, the overall system cost is notably reduced. It also simplifies the motor’s design and assembly.
2. **Reliability**: Fewer components result in fewer potential points of failure, enhancing the durability and reliability of the motor control system.
3. **Maintenance**: A simpler structure leads to reduced maintenance needs. This is crucial in applications where accessibility is limited or where long operational life is essential.
4. **Performance**: Sensorless vector control offers improved control performance with smooth torque. This is beneficial for precision applications that require strict speed and position sensitiveness.
5. **Installation Flexibility**: The elimination of sensors allows for more flexible installation options since there are no space constraints imposed by sensor placement.
Applications of Sensorless Vector Control in PMSM
PMSMs with sensorless vector control are applied in a diverse range of industries due to their enhanced capabilities.
Industrial Automation
In industrial settings, PMSMs are increasingly replacing induction motors.
Their precision control is ideal for applications in robotics, CNC machines, and automated guided vehicles, where accuracy and efficiency are paramount.
Electric Vehicles
The automotive industry benefits immensely from sensorless vector control technology.
The efficient control of PMSMs improves the performance of electric vehicles, offering smooth acceleration and enhanced energy efficiency.
Home Appliances
High-performance home appliances, such as washing machines and air conditioners, leverage PMSMs for their high efficiency, quiet operation, and reliability, especially without sensor complications.
Renewable Energy
Wind turbines and other renewable energy systems utilize PMSMs for their high efficiency and reliability.
Sensorless vector control ensures that these systems operate optimally, contributing to sustainable energy production.
Challenges and Future Prospects
While sensorless vector control offers numerous advantages, it does present challenges, especially in varying operational conditions.
The accuracy of estimation algorithms can decline at very low speeds due to reduced back EMF.
Research and advancements in adaptive algorithms, along with machine learning techniques, show promise in overcoming these challenges.
**Future Developments**:
1. **Advanced Estimation Techniques**: Development of more sophisticated algorithms that can accurately estimate motor parameters regardless of load changes or other disturbances.
2. **Integration with IoT**: Integrating sensorless vector control with IoT-based systems for real-time monitoring and predictive maintenance.
3. **Wide Adoption**: As technology progresses, sensorless vector control is expected to become mainstream in various applications, owing to its advantages and cost-efficiency.
In conclusion, sensorless vector control is an essential development in the control of permanent magnet synchronous motors.
Its elimination of sensors while maintaining high precision control revolutionizes motor efficiency and reliability, paving the way for advanced applications across different industries.
資料ダウンロード
QCD調達購買管理クラウド「newji」は、調達購買部門で必要なQCD管理全てを備えた、現場特化型兼クラウド型の今世紀最高の購買管理システムとなります。
ユーザー登録
調達購買業務の効率化だけでなく、システムを導入することで、コスト削減や製品・資材のステータス可視化のほか、属人化していた購買情報の共有化による内部不正防止や統制にも役立ちます。
NEWJI DX
製造業に特化したデジタルトランスフォーメーション(DX)の実現を目指す請負開発型のコンサルティングサービスです。AI、iPaaS、および先端の技術を駆使して、製造プロセスの効率化、業務効率化、チームワーク強化、コスト削減、品質向上を実現します。このサービスは、製造業の課題を深く理解し、それに対する最適なデジタルソリューションを提供することで、企業が持続的な成長とイノベーションを達成できるようサポートします。
オンライン講座
製造業、主に購買・調達部門にお勤めの方々に向けた情報を配信しております。
新任の方やベテランの方、管理職を対象とした幅広いコンテンツをご用意しております。
お問い合わせ
コストダウンが利益に直結する術だと理解していても、なかなか前に進めることができない状況。そんな時は、newjiのコストダウン自動化機能で大きく利益貢献しよう!
(Β版非公開)