- お役立ち記事
- Fatigue fracture fractography
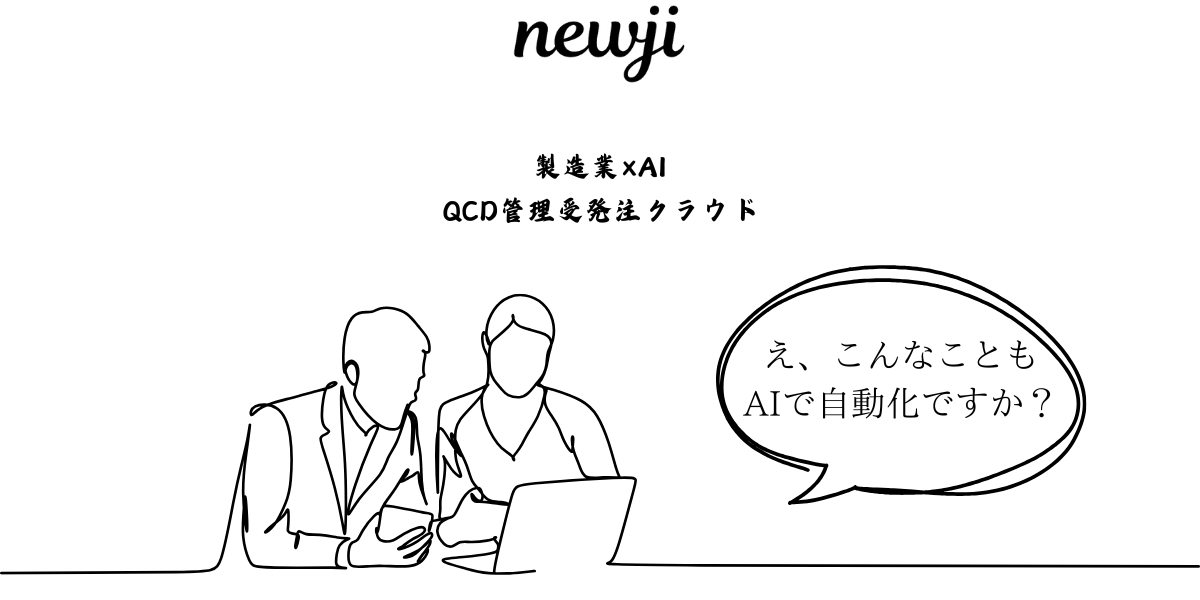
Fatigue fracture fractography
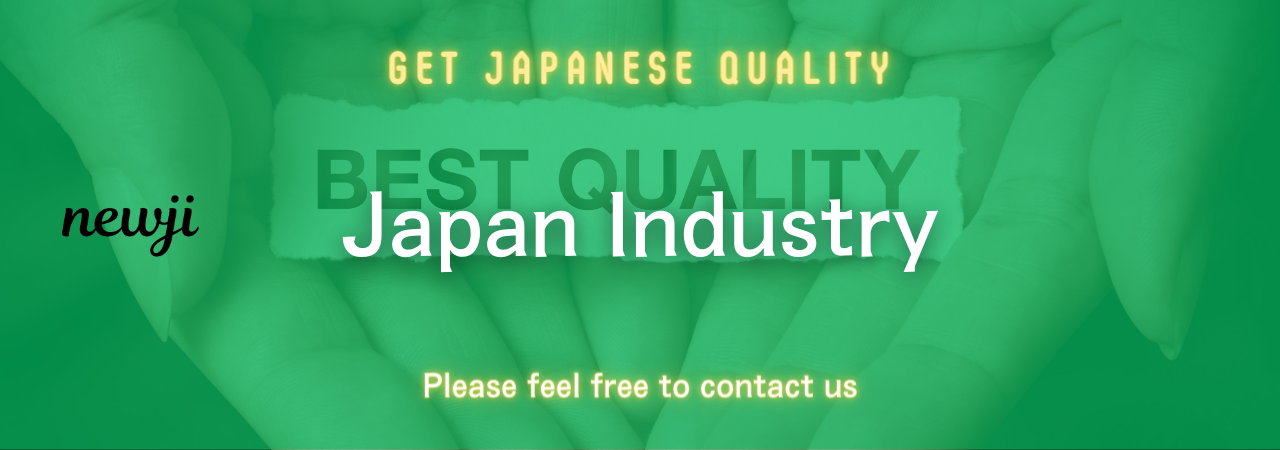
目次
Understanding Fatigue Fracture Fractography
Fatigue fracture fractography is a fascinating field that deals with the study of fracture surfaces on materials and components that have failed due to fatigue.
This analysis helps us understand the reasons behind the failure, allowing engineers and manufacturers to design more robust systems, prevent future failures, and ensure safety and reliability.
Let’s dive deeper into the subject to understand how it works, why it happens, and what we can learn from it.
What is Fatigue Fracture?
Fatigue fracture refers to the progressive and localized structural damage that occurs when a material is subjected to cyclic or repeated loading.
Even if the stresses are relatively low, over time, this repeated loading can lead to crack formation and eventually cause the material to fracture.
Fatigue fractures are common in many engineering structures, such as bridges, aircraft, and engines, where components are exposed to repeated stress cycles.
The Science Behind Fatigue Fracture
When a material is subjected to cyclic loading, microscopic cracks can initiate at stress concentration points such as surface scratches, corners, or inclusions within the material.
As the loading continues, these cracks grow progressively with each cycle, until the remaining cross-section of the material can no longer support the mechanical load, leading to a sudden fracture.
The process of crack initiation and growth is influenced by various factors, including the material properties, the magnitude and frequency of the applied stress, and the environmental conditions.
What is Fractography?
Fractography is the study of fracture surfaces of materials.
It involves examining the fractured surfaces visually or using microscopic techniques to identify characteristics and features that reveal how the fracture occurred.
Fractography can indicate the mode of fracture, such as ductile or brittle, and it can highlight features like beach marks and striations indicative of fatigue processes.
Importance of Fractography in Engineering
Fractography is vital in understanding the root cause of failure in engineering components.
It helps in failure analysis investigations to determine if fatigue was the cause of the fracture.
By examining the characteristics of the fracture surface, engineers can determine the origin of the crack and assess its progression.
This information is crucial in making decisions about material selection, manufacturing processes, and design improvements.
Key Features of Fatigue Fracture Surfaces
Fracture surfaces from fatigue failures exhibit specific features that help identify the fatigue process.
Here are some key features that fractographers look for:
1. Beach Marks
Beach marks are concentric rings or lines visible on the fracture surface, marking the progression of crack growth during different stress cycles.
They resemble the patterns left on the shore by the retreating sea and indicate interruptions in the loading process, such as machine shutdowns or operational pauses.
2. Striations
Striations are fine lines observed microscopically, representing incremental crack growth during each cycle of load application.
They appear like ladder patterns on the fracture surface and are critical indicators of the fatigue failure mechanism.
Striations provide insights into the growth rate of the crack and the load conditions experienced by the component.
3. Ratchet Marks
Ratchet marks are step-like features on the fracture surface that occur when separate areas of the crack front join together.
These marks are often seen in components with complex geometries or multiple crack initiation sites.
They provide information about the interaction of different crack fronts and can help identify the origin of the fracture.
Factors Influencing Fatigue Fracture
Several factors affect the initiation and propagation of fatigue cracks:
1. Material Properties
The type of material and its properties, such as strength, toughness, and ductility, significantly influence fatigue behavior.
Materials with high fracture toughness are generally more resistant to crack propagation, while those with lower toughness may fail more easily under cyclic loads.
2. Surface Finish
The surface condition of a component can impact crack initiation.
Rough surfaces or surface defects such as scratches and pits act as stress concentration points, promoting crack formation.
Smooth and polished surfaces are advantageous in reducing the risk of fatigue failure.
3. Stress Magnitude and Frequency
The level of applied stress and the frequency of the cycles directly impact the fatigue life of a material.
Higher stress levels and more frequent cycles accelerate the crack initiation and growth process, leading to premature failure.
Applications and Benefits of Fatigue Fractography
Understanding fatigue fracture fractography has numerous applications and benefits across industries:
1. Failure Analysis
Fractography aids in failure analysis by determining if fatigue was the cause of a component’s failure.
This analysis helps in identifying design and material flaws, assessing manufacturing processes, and making informed decisions to prevent future failures.
2. Quality Control
Fractography is used as a quality control tool to inspect and ensure that components meet the required standards and specifications.
It helps identify potential defects or stress concentration points that could lead to fatigue failures.
3. Design Optimization
By understanding the fatigue behavior of materials through fractography, engineers can optimize designs for improved performance and reliability.
This involves selecting appropriate materials, considering surface treatments, and enhancing component geometries to minimize stress concentrations.
In Conclusion
Fatigue fracture fractography is an essential aspect of engineering and material science, providing valuable insights into the failure mechanisms of components subjected to cyclic loading.
By carefully examining fracture surfaces, engineers can identify the root causes of failures, optimize designs, and ensure the safety and reliability of critical structures and machinery.
Whether in aerospace, automotive, or civil engineering, understanding fatigue behavior and the principles of fractography is crucial for preventing future failures and improving the performance of materials and components.
資料ダウンロード
QCD調達購買管理クラウド「newji」は、調達購買部門で必要なQCD管理全てを備えた、現場特化型兼クラウド型の今世紀最高の購買管理システムとなります。
ユーザー登録
調達購買業務の効率化だけでなく、システムを導入することで、コスト削減や製品・資材のステータス可視化のほか、属人化していた購買情報の共有化による内部不正防止や統制にも役立ちます。
NEWJI DX
製造業に特化したデジタルトランスフォーメーション(DX)の実現を目指す請負開発型のコンサルティングサービスです。AI、iPaaS、および先端の技術を駆使して、製造プロセスの効率化、業務効率化、チームワーク強化、コスト削減、品質向上を実現します。このサービスは、製造業の課題を深く理解し、それに対する最適なデジタルソリューションを提供することで、企業が持続的な成長とイノベーションを達成できるようサポートします。
オンライン講座
製造業、主に購買・調達部門にお勤めの方々に向けた情報を配信しております。
新任の方やベテランの方、管理職を対象とした幅広いコンテンツをご用意しております。
お問い合わせ
コストダウンが利益に直結する術だと理解していても、なかなか前に進めることができない状況。そんな時は、newjiのコストダウン自動化機能で大きく利益貢献しよう!
(Β版非公開)