- お役立ち記事
- Points to ensure quality and precautions for mounting on boards of 0603 size or smaller
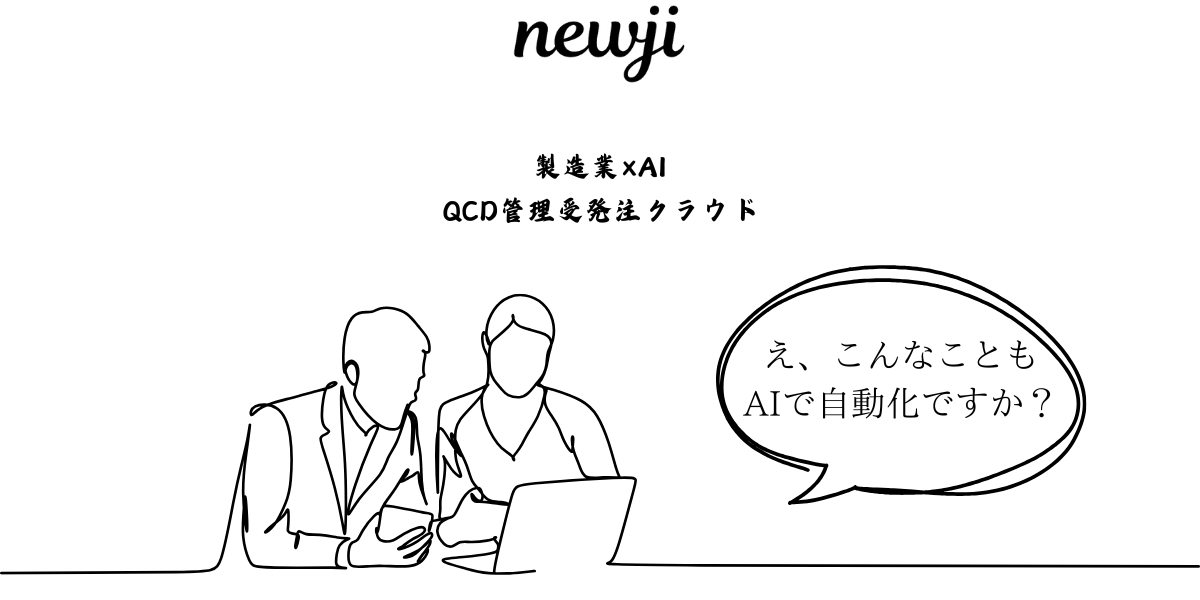
Points to ensure quality and precautions for mounting on boards of 0603 size or smaller
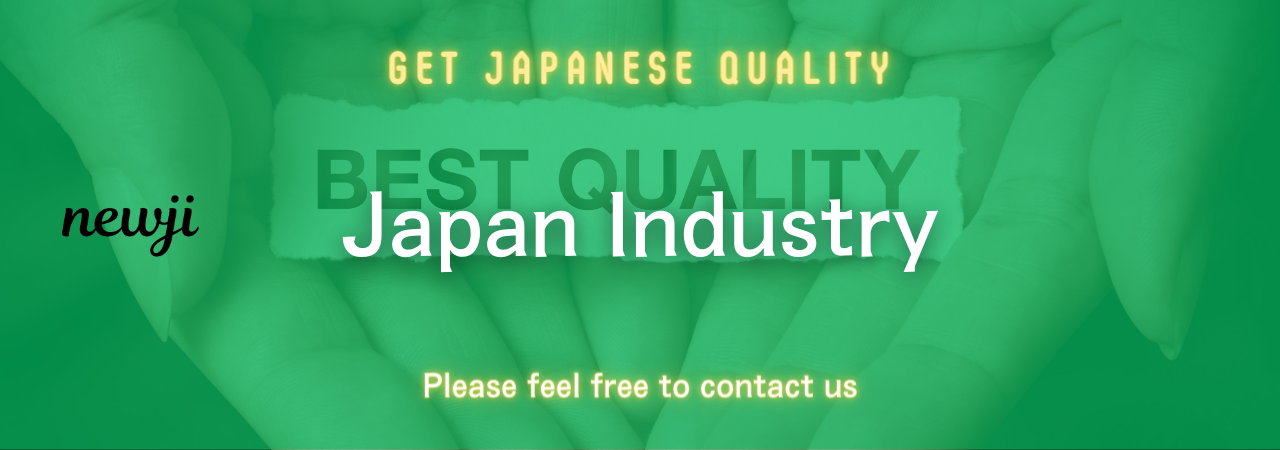
目次
Understanding 0603 Size or Smaller Components
As the world of electronics continues to evolve, the need for compact and efficient components has become more pressing.
One of the most common sizes for surface-mount components is the 0603 size, which translates to 0.06 inches by 0.03 inches.
These components have gained popularity due to their small footprint, which allows for more compact and lightweight designs.
However, working with such small components can present certain challenges.
The precision required to ensure quality and successful mounting is greater than with larger components.
Understanding the specific characteristics of 0603 components is essential.
They are typically passive components such as resistors and capacitors, but active components may also be available.
Their size makes handling more delicate, and even minor inaccuracies can lead to failures.
Key Considerations for Quality Assurance
When dealing with 0603 size or smaller components, quality assurance is paramount.
This begins with sourcing components from reputable suppliers to guarantee quality standards are met.
A critical factor is ensuring the consistency of component placement on the PCB.
Automated pick-and-place machines are often employed to achieve the necessary precision.
These machines must be calibrated correctly for small component sizes.
Another consideration is the solder paste application.
The stencil used must match the components’ small size to avoid bridging or insufficient paste application.
Lastly, the inspection process should include optical or X-ray inspection to catch any potential misplacements or defects.
Regular testing ensures that the components are performing as expected.
Precautions During Mounting
Mounting 0603 or smaller components requires strict adherence to specific precautions to avoid complications during assembly.
Firstly, the working environment should be controlled.
Humidity and static electricity can affect component placement and performance.
Utilize anti-static wristbands and mats during handling to prevent electrostatic discharge.
Temperature control during the soldering process is another critical factor.
Reflow ovens must be set to the correct temperature profile to ensure components are not damaged.
Rapid heating can cause thermal shock, leading to failures.
Additionally, it’s important to use the proper solder alloy.
A lead-free solder with an appropriate melting point is recommended for modern assemblies.
This minimizes thermal stress and improves joint reliability.
Common Challenges and How to Handle Them
Working with small components like 0603 sizes can bring about several challenges.
Firstly, these components are easy to misplace due to their tiny size.
Maintaining a clear workspace can help mitigate this issue.
Another challenge is the potential for tombstoning, where one end of the component lifts during reflow soldering.
This can be minimized by ensuring even heat distribution across the board.
To avoid solder bridges, careful control of solder paste volume and accurate placement is crucial.
Using a stencil with smaller apertures can assist in precise application.
Lastly, there might be connectivity issues if pads on the PCB are not aligned correctly with component terminals.
Using design software with precise layout tools can ensure proper alignment.
Best Practices for Successful Mounting
To ensure successful mounting of 0603 size or smaller components, following best practices is essential.
Firstly, ensure that the PCB design is optimized for the components being used.
This includes precise pad design and solder mask definition.
Invest in high-quality pick-and-place machines capable of handling small components with accuracy.
Regular maintenance and calibration of these machines ensure they continue to perform optimally.
During solder paste application, use a stencil designed specifically for small components.
The stencil’s thickness and aperture size determine the volume of paste applied, which is crucial for preventing solder defects.
Finally, conduct thorough testing after assembly.
Functional tests, along with thermal cycling tests, can identify weak joints or components that have been heat-damaged.
Implementing these tests as part of the quality control process will help ensure the reliability of the final product.
Conclusion
Mounting 0603 size or smaller components on boards comes with its own set of challenges but also offers many advantages in terms of device miniaturization.
Ensuring quality and taking appropriate precautions are key to successful implementation.
By understanding the unique requirements and employing the right tools and techniques, manufacturers can achieve reliable and efficient electronic assemblies.
Adopting best practices from design to testing will ensure that these small components serve their purpose effectively, contributing to the overall success of electronic products.
資料ダウンロード
QCD調達購買管理クラウド「newji」は、調達購買部門で必要なQCD管理全てを備えた、現場特化型兼クラウド型の今世紀最高の購買管理システムとなります。
ユーザー登録
調達購買業務の効率化だけでなく、システムを導入することで、コスト削減や製品・資材のステータス可視化のほか、属人化していた購買情報の共有化による内部不正防止や統制にも役立ちます。
NEWJI DX
製造業に特化したデジタルトランスフォーメーション(DX)の実現を目指す請負開発型のコンサルティングサービスです。AI、iPaaS、および先端の技術を駆使して、製造プロセスの効率化、業務効率化、チームワーク強化、コスト削減、品質向上を実現します。このサービスは、製造業の課題を深く理解し、それに対する最適なデジタルソリューションを提供することで、企業が持続的な成長とイノベーションを達成できるようサポートします。
オンライン講座
製造業、主に購買・調達部門にお勤めの方々に向けた情報を配信しております。
新任の方やベテランの方、管理職を対象とした幅広いコンテンツをご用意しております。
お問い合わせ
コストダウンが利益に直結する術だと理解していても、なかなか前に進めることができない状況。そんな時は、newjiのコストダウン自動化機能で大きく利益貢献しよう!
(Β版非公開)