- お役立ち記事
- Causes of human error and effective preventive measures through pokayoke
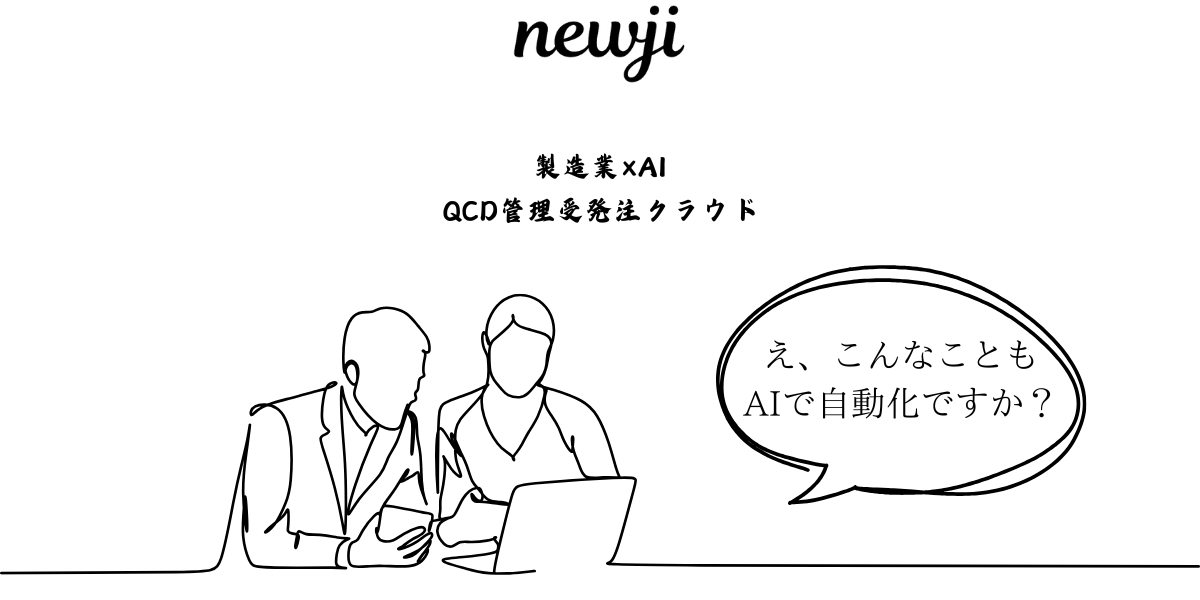
Causes of human error and effective preventive measures through pokayoke
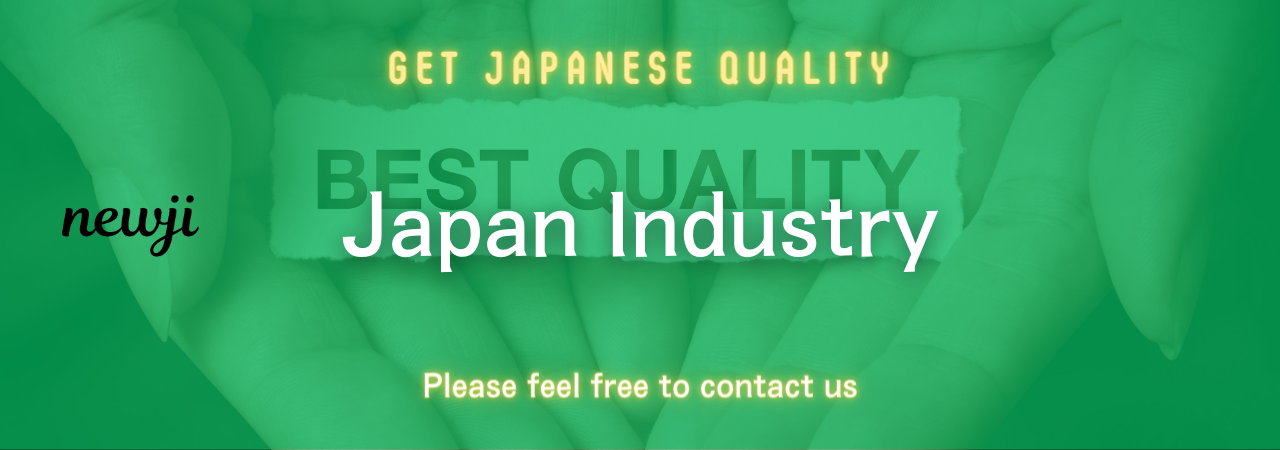
目次
Understanding Human Error
Human error is an unavoidable aspect of life, impacting various fields from manufacturing to healthcare.
It refers to unintentional mistakes or actions that lead to unintended outcomes, potentially causing harm or inefficiency.
Comprehending the causes of human error is crucial in implementing measures to reduce its occurrence.
Common Causes of Human Error
Several factors contribute to human error, with the most common being fatigue.
When individuals are tired, their cognitive functions and decision-making abilities are compromised.
This can lead to mistakes in judgment or oversight in critical tasks.
Distractions also play a significant role in human error.
In environments where constant attention is required, such as operating machinery or driving, distractions can divert focus away from the task at hand.
This results in mistakes that could otherwise be avoided.
Stress is another major contributor.
High levels of stress can impair cognitive functions and create a conducive environment for error.
In high-stakes or high-pressure situations, the likelihood of making mistakes increases.
Lack of training or inadequate knowledge also contributes significantly to human error.
When individuals are not properly equipped with the necessary skills or information, they are more prone to making errors.
This is particularly true in complex systems where a thorough understanding is essential.
The Role of System and Environment
The environment and the systems in place can either mitigate or exacerbate human error.
Complex systems often increase the chance of error due to their multifaceted nature and potential for misunderstanding.
A poorly designed system can confuse or mislead, leading individuals to make mistakes they might not have made in a simpler, more intuitive setup.
Furthermore, the quality of communication within an organization significantly impacts error rates.
Miscommunication or lack of clear directives can lead to incorrect execution of tasks, resulting in undesirable outcomes.
Introducing Pokayoke
Pokayoke, a Japanese term meaning “mistake-proofing,” is an effective technique aimed at reducing human error.
Originally developed by Shigeo Shingo in the context of manufacturing, pokayoke seeks to prevent mistakes by designing systems that either make errors impossible or immediately detect and rectify them.
Its core purpose is to create processes that consider human limitations and compensate for them.
How Pokayoke Works
Pokayoke employs various methods to achieve its goal of reducing error.
One approach is to design features that prevent incorrect action.
For example, incorporating fixtures or guides that ensure components can only be assembled in the correct orientation eliminates the possibility of assembly errors.
Another method is to implement controls that automatically stop processes when an error is detected.
This could involve sensors that immediately halt operations when a deviation from the norm is identified, preventing further errors from occurring.
Visual aids and reminders are also crucial in the pokayoke strategy.
Labels, signs, or colored indicators can help draw attention to important information or caution against potential errors.
These visual cues serve as a constant reminder to remain vigilant and detail-oriented.
The Benefits of Pokayoke
The adoption of pokayoke offers several benefits.
It greatly reduces the frequency of errors, improving overall efficiency and productivity.
By minimizing mistakes, organizations can save time and resources that would otherwise be spent correcting errors.
Increased safety is another significant benefit.
By integrating pokayoke, potential hazards associated with human error are reduced, creating a safer environment for workers and end-users alike.
Furthermore, implementing pokayoke can enhance quality assurance.
Consistent error-free production or service delivery ensures higher quality output, leading to increased customer satisfaction and trust in the brand.
Effective Implementation of Pokayoke
To effectively implement pokayoke, an organization must first analyze its processes to identify potential error points.
Conducting a thorough examination allows for the identification of areas where human error is most likely to occur, providing a clear target for system improvements.
Once these error-prone areas are identified, organizations can design or modify processes to incorporate pokayoke principles.
This involves considering each step of a process and determining how errors might occur and what countermeasures can prevent them.
Training and engaging employees is also crucial for successful implementation.
Workers need to understand the new processes and the role of pokayoke within their job functions.
Their involvement in designing and refining pokayoke solutions can lead to more practical and effective outcomes.
Lastly, continuous monitoring and feedback are essential.
Systems should be regularly reviewed to ensure they remain effective and relevant, adjusting as necessary to accommodate changes in processes or technology.
Conclusion
Human error is a pervasive issue across industries, yet it can be effectively managed through understanding its causes and implementing preventive measures like pokayoke.
By designing systems that acknowledge and compensate for human limitations, organizations can reduce errors, increase safety, and ensure high-quality outcomes.
Embracing a culture of mistake-proofing not only enhances productivity but also fosters a safer and more efficient working environment.
資料ダウンロード
QCD調達購買管理クラウド「newji」は、調達購買部門で必要なQCD管理全てを備えた、現場特化型兼クラウド型の今世紀最高の購買管理システムとなります。
ユーザー登録
調達購買業務の効率化だけでなく、システムを導入することで、コスト削減や製品・資材のステータス可視化のほか、属人化していた購買情報の共有化による内部不正防止や統制にも役立ちます。
NEWJI DX
製造業に特化したデジタルトランスフォーメーション(DX)の実現を目指す請負開発型のコンサルティングサービスです。AI、iPaaS、および先端の技術を駆使して、製造プロセスの効率化、業務効率化、チームワーク強化、コスト削減、品質向上を実現します。このサービスは、製造業の課題を深く理解し、それに対する最適なデジタルソリューションを提供することで、企業が持続的な成長とイノベーションを達成できるようサポートします。
オンライン講座
製造業、主に購買・調達部門にお勤めの方々に向けた情報を配信しております。
新任の方やベテランの方、管理職を対象とした幅広いコンテンツをご用意しております。
お問い合わせ
コストダウンが利益に直結する術だと理解していても、なかなか前に進めることができない状況。そんな時は、newjiのコストダウン自動化機能で大きく利益貢献しよう!
(Β版非公開)