- お役立ち記事
- Mechanism of fretting fatigue and practical fretting fatigue design and countermeasure techniques
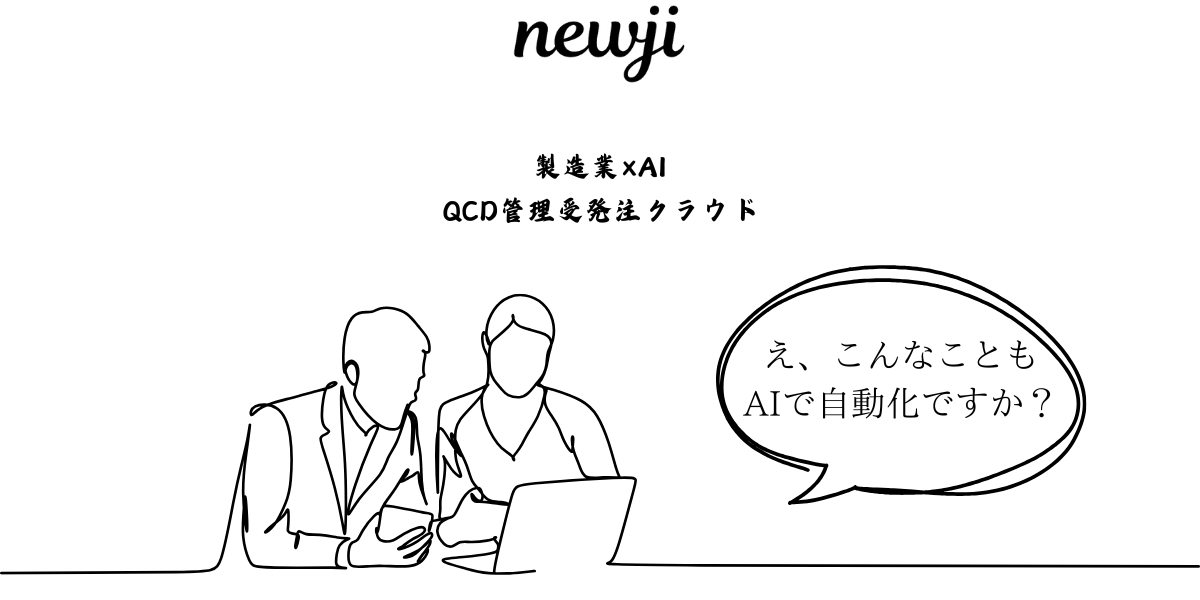
Mechanism of fretting fatigue and practical fretting fatigue design and countermeasure techniques
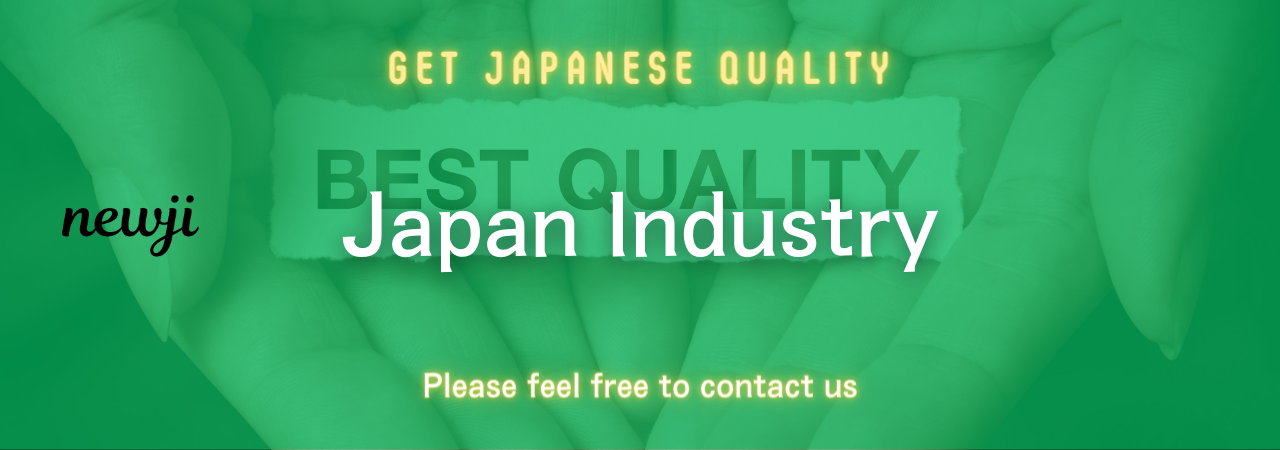
目次
Understanding Fretting Fatigue
Fretting fatigue is a unique and often challenging phenomenon encountered in various mechanical and structural applications.
To grasp its mechanism, it’s essential to first understand the basic concept.
Fretting fatigue occurs when two surfaces in contact experience small, oscillatory relative motion, typically induced by vibrations or cyclic loading.
The repeated movement leads to the initiation and propagation of small cracks that can ultimately result in fatigue failure.
This issue is particularly prevalent in components subjected to fluctuating stresses, such as aircraft engines, turbine blades, bolted joints, and railway axles.
The combination of mechanical loading and surface interaction makes fretting fatigue an important consideration in the design and durability of these parts.
The Mechanism Behind Fretting Fatigue
The mechanism of fretting fatigue involves several intricate processes.
When two surfaces are in contact under load, micro-movements at the interface cause localized friction and wear.
This can lead to the development of tiny debris particles at the contact points.
These debris particles exacerbate surface damage by acting as abrasives, further intensifying the wear process.
As micro-movements continue, the surfaces undergo plastic deformation.
This leads to the formation of micro-cracks, which propagate under continued cyclic loading.
The material’s resistance to fretting fatigue largely depends on its ability to withstand these micro-movements and resist crack growth.
The complex interplay of surface roughness, contact pressure, and the materials’ mechanical properties further influences the initiation and propagation of fretting fatigue cracks.
Factors Influencing Fretting Fatigue
Several factors can affect the onset and progression of fretting fatigue.
Material Properties
The material composition and properties play a crucial role in determining fretting fatigue resistance.
Materials with high toughness and ductility tend to perform better, as they can absorb more deformation without cracking.
Additionally, surface treatments or coatings that enhance hardness and reduce friction can offer significant resistance against fretting.
Contact Pressure and Surface Roughness
The level of contact pressure and surface roughness directly impacts the severity of fretting fatigue.
Higher contact pressures can accelerate the wear process and increase the likelihood of crack initiation.
Similarly, surfaces with higher roughness values can increase friction and exacerbate surface damage.
Environmental Conditions
Environmental factors such as temperature, humidity, and corrosive elements can also influence fretting fatigue.
Elevated temperatures may soften materials, making them more susceptible to wear.
Corrosive environments can accelerate crack growth by weakening the material at the interface.
Load Conditions
The magnitude and direction of the applied load influence fretting fatigue behavior.
Higher amplitude cyclic loads tend to increase the rate of crack initiation and growth.
The duration over which these loads are applied can also affect the material’s ability to withstand fretting fatigue.
Countermeasure Techniques for Fretting Fatigue
Addressing fretting fatigue involves applying a combination of design strategies, material selection, and surface treatments.
Material Selection
Choosing the right material can significantly reduce the risk of fretting fatigue.
Opt for materials with high strength and fatigue resistance.
Metals such as titanium alloys and certain steels have shown promise in mitigating fretting due to their superior toughness and fatigue properties.
Surface Treatments
Surface treatments and coatings are effective ways to enhance a material’s resistance to fretting fatigue.
Techniques such as nitriding, carburizing, and anodizing can improve the surface’s hardness, thereby reducing wear.
Application of coatings like PTFE, nickel, or chromium can minimize friction and prevent damage at the contact interface.
Design Optimization
Careful design optimization can help alleviate fretting fatigue issues.
Design components to minimize stress concentrations, distribute loads evenly, and ensure proper alignment of parts.
Incorporate features like chamfers or fillets to avoid sharp edges where stress could concentrate and initiate cracking.
Maintain Proper Lubrication
Adequate lubrication can reduce friction and wear at the contact surfaces, delaying the onset of fretting fatigue.
Regular maintenance to ensure consistent lubrication is crucial, especially in high-demand applications like aerospace or automotive industries.
Regular Inspection and Monitoring
Implement regular inspection protocols to monitor components susceptible to fretting fatigue.
Non-destructive testing methods such as ultrasonics or infrared thermography can detect early signs of wear or crack initiation.
Proactive maintenance based on these inspections can prevent catastrophic failures.
Practical Applications and Considerations
Fretting fatigue is a critical consideration in industries where safety and reliability are paramount.
Aerospace Industry
In aerospace applications, the lightweight yet high-stress components like turbine blades and engine parts are vulnerable to fretting fatigue.
Designers need to carefully balance material selection and structural integrity to ensure long-term performance without compromising safety.
Automotive Engineering
In the automotive sector, components like gears, bearings, and axle assemblies are frequently subjected to cyclic loads, making them prone to fretting fatigue.
Adopting advanced materials and coatings can significantly enhance their lifespan and functionality.
Infrastructure and Railway Systems
Railway axles and infrastructure elements experience continuous stress and movement, leading to fretting fatigue concerns.
Regular inspections, durable material choices, and optimal design adjustments are essential to maintain safety and minimize disruptions.
Conclusion
Understanding the mechanism of fretting fatigue and implementing practical design and countermeasure techniques is key to mitigating its effects.
Material selection, surface treatments, and innovative design practices play significant roles in enhancing the longevity and reliability of components subjected to fretting.
By adopting a proactive approach and integrating these strategies, industries can effectively manage fretting fatigue challenges and ensure the safety and efficiency of their systems and structures.
資料ダウンロード
QCD調達購買管理クラウド「newji」は、調達購買部門で必要なQCD管理全てを備えた、現場特化型兼クラウド型の今世紀最高の購買管理システムとなります。
ユーザー登録
調達購買業務の効率化だけでなく、システムを導入することで、コスト削減や製品・資材のステータス可視化のほか、属人化していた購買情報の共有化による内部不正防止や統制にも役立ちます。
NEWJI DX
製造業に特化したデジタルトランスフォーメーション(DX)の実現を目指す請負開発型のコンサルティングサービスです。AI、iPaaS、および先端の技術を駆使して、製造プロセスの効率化、業務効率化、チームワーク強化、コスト削減、品質向上を実現します。このサービスは、製造業の課題を深く理解し、それに対する最適なデジタルソリューションを提供することで、企業が持続的な成長とイノベーションを達成できるようサポートします。
オンライン講座
製造業、主に購買・調達部門にお勤めの方々に向けた情報を配信しております。
新任の方やベテランの方、管理職を対象とした幅広いコンテンツをご用意しております。
お問い合わせ
コストダウンが利益に直結する術だと理解していても、なかなか前に進めることができない状況。そんな時は、newjiのコストダウン自動化機能で大きく利益貢献しよう!
(Β版非公開)