- お役立ち記事
- Basics of permanent magnet synchronous motor control and application to sensorless control
月間77,185名の
製造業ご担当者様が閲覧しています*
*2025年2月28日現在のGoogle Analyticsのデータより
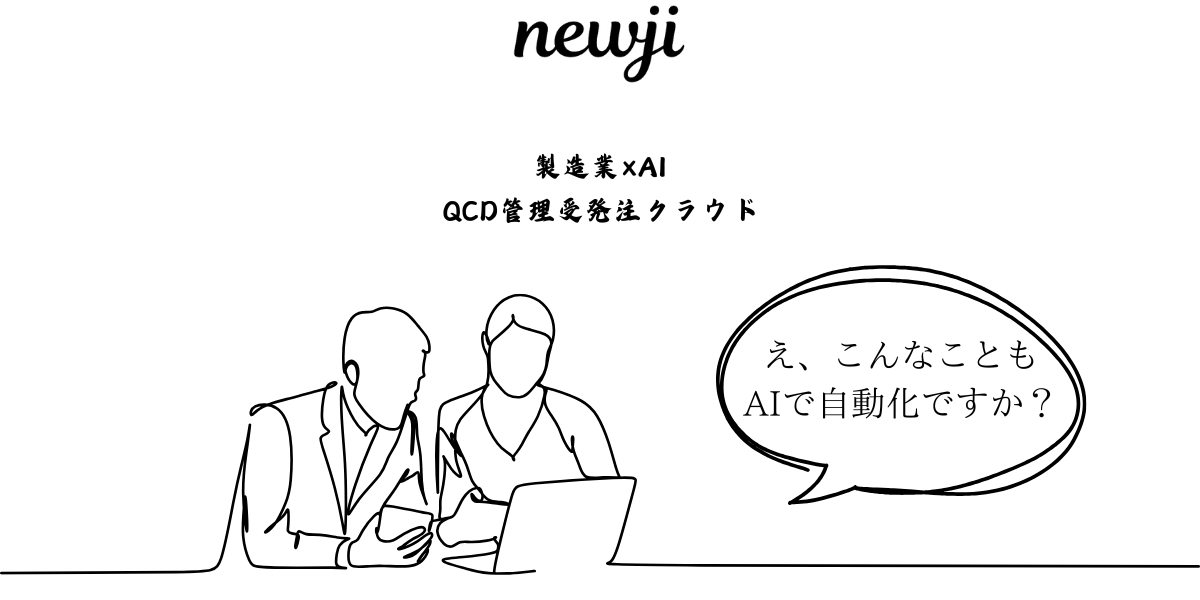
Basics of permanent magnet synchronous motor control and application to sensorless control
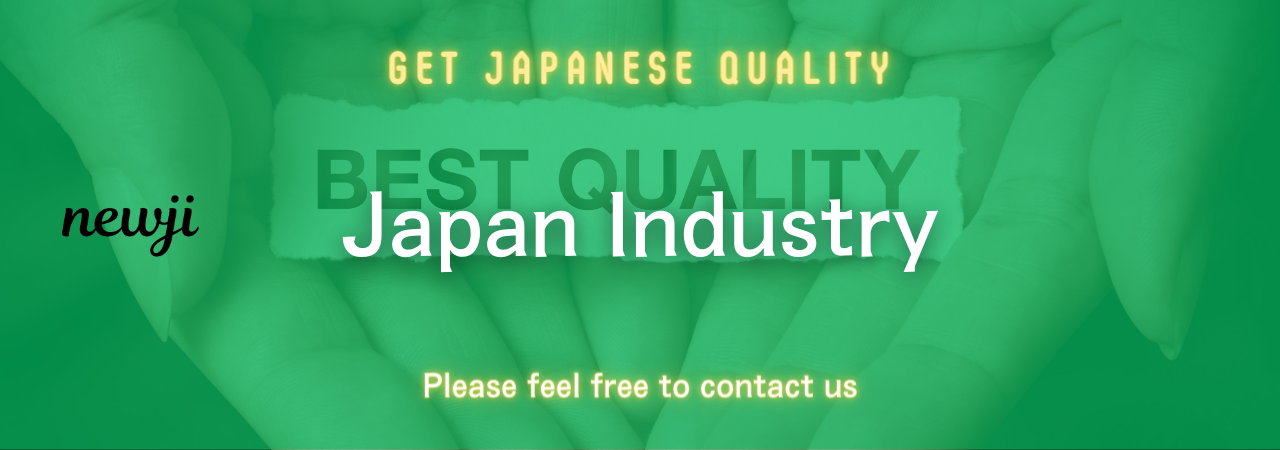
Permanent magnet synchronous motors (PMSMs) have become increasingly popular in various applications due to their high efficiency and compact size.
These motors are widely used in electric vehicles, industrial automation, and household appliances.
The demand for energy-efficient solutions has driven the adoption of PMSMs, which offer superior performance compared to traditional induction motors.
目次
Understanding Permanent Magnet Synchronous Motors
PMSMs are a type of synchronous motor that uses permanent magnets embedded in the rotor.
Unlike induction motors, where the rotor is magnetized by the stator field, PMSMs have a rotor with built-in permanent magnets that generate a magnetic field consistently.
This results in higher efficiency and reduced energy consumption, particularly at low speeds.
Advantages of PMSMs
One of the key advantages of PMSMs is their high power density.
This means they can generate more power for a given size compared to other motor types.
Additionally, their efficiency is significantly higher, especially under partial load conditions.
This makes them ideal for applications where energy savings are a priority.
PMSMs also offer better torque-to-current ratios, meaning they require less current to produce the same amount of torque as other motors.
This characteristic leads to smoother operation and reduces the stress on the power supply.
Furthermore, PMSMs have a longer lifespan due to fewer moving parts and less wear and tear.
Basic Principles of PMSM Control
Controlling a PMSM involves managing the current supplied to the motor to achieve desired torque and speed.
This requires a precise control strategy to ensure efficient and stable operation.
Vector control, also known as field-oriented control (FOC), is the most common method used in PMSM control.
Field-Oriented Control (FOC)
FOC is a technique that decouples the stator current into two orthogonal components: one controlling the rotor’s magnetic field and the other controlling the torque.
By doing so, it allows independent control of the motor’s torque and field flux.
FOC provides better dynamic performance and reduces torque ripple, resulting in smoother motor operation.
The FOC method relies on precise knowledge of the rotor position to achieve accurate control.
Traditionally, this has been accomplished using position sensors, such as encoders or resolvers, to provide real-time feedback on the rotor position.
Sensorless Control of PMSMs
While sensors offer precise feedback for motor control, they add complexity and cost to the system.
Moreover, sensors can be susceptible to environmental factors and mechanical failures, reducing the system’s overall reliability.
To overcome these challenges, sensorless control methods have been developed, allowing PMSMs to operate without position sensors.
Principles of Sensorless Control
Sensorless control techniques estimate the rotor’s position and speed by analyzing the motor’s electrical parameters.
These methods use mathematical models to predict the rotor position based on the motor’s voltage and current measurements.
By eliminating the need for physical sensors, sensorless control simplifies the motor system and reduces costs.
Common Sensorless Control Techniques
Several sensorless control methods exist, each with its own advantages and limitations.
Some of the most popular techniques include:
1. **Back EMF Estimation**: This method estimates rotor position by measuring the back electromotive force (EMF) generated by the motor.
Back EMF is proportional to the rotor speed and can be used to determine the rotor angle.
This technique is best suited for high-speed applications where the back EMF signal is strong.
2. **Model-Based Estimation**: This approach uses mathematical models of the PMSM to estimate rotor position.
By comparing the predicted and measured motor currents, it can derive information about the rotor’s position.
Model-based estimation performs well across a wide range of speeds but requires accurate motor parameters for optimal results.
3. **High-Frequency Signal Injection**: This technique injects high-frequency signals into the motor and analyzes the response to determine the rotor position.
It is particularly effective at low speeds and standstill, where back EMF is insufficient for estimation.
However, high-frequency signal injection may introduce additional noise into the system.
Applications of Sensorless PMSM Control
Sensorless control has opened up new opportunities for PMSM applications, particularly in cost-sensitive and high-reliability markets.
Some common applications include:
Electric Vehicles
In electric vehicles, reducing system costs while maintaining performance and reliability is crucial.
Sensorless PMSM control eliminates the need for costly position sensors, making it an attractive option for electric drive systems.
Additionally, sensorless control improves system robustness by removing failure-prone components.
Industrial Automation
Industrial applications, such as conveyors and robotic arms, benefit from sensorless PMSM control due to its flexibility and cost-effectiveness.
Removing sensors reduces maintenance costs and increases system uptime, making it ideal for continuous production environments.
Household Appliances
In household appliances like washing machines and refrigerators, efficiency and cost savings are paramount.
Sensorless PMSM control offers a streamlined approach to motor control without compromising performance, leading to lower production costs and enhanced energy efficiency.
The Future of PMSM Control
As technology advances, the demand for energy-efficient, cost-effective, and reliable motor solutions continues to grow.
With ongoing developments in sensorless control techniques and the increasing capabilities of digital processors, PMSMs are expected to become even more prominent in various industries.
The adoption of PMSMs and sensorless control is likely to expand as manufacturers seek to optimize performance and reduce costs.
Understanding the basics of PMSM control and sensorless techniques will be essential for engineers and designers looking to leverage these motors in their next-generation applications.
資料ダウンロード
QCD管理受発注クラウド「newji」は、受発注部門で必要なQCD管理全てを備えた、現場特化型兼クラウド型の今世紀最高の受発注管理システムとなります。
ユーザー登録
受発注業務の効率化だけでなく、システムを導入することで、コスト削減や製品・資材のステータス可視化のほか、属人化していた受発注情報の共有化による内部不正防止や統制にも役立ちます。
NEWJI DX
製造業に特化したデジタルトランスフォーメーション(DX)の実現を目指す請負開発型のコンサルティングサービスです。AI、iPaaS、および先端の技術を駆使して、製造プロセスの効率化、業務効率化、チームワーク強化、コスト削減、品質向上を実現します。このサービスは、製造業の課題を深く理解し、それに対する最適なデジタルソリューションを提供することで、企業が持続的な成長とイノベーションを達成できるようサポートします。
製造業ニュース解説
製造業、主に購買・調達部門にお勤めの方々に向けた情報を配信しております。
新任の方やベテランの方、管理職を対象とした幅広いコンテンツをご用意しております。
お問い合わせ
コストダウンが利益に直結する術だと理解していても、なかなか前に進めることができない状況。そんな時は、newjiのコストダウン自動化機能で大きく利益貢献しよう!
(β版非公開)