- お役立ち記事
- Basics of forging processing, mechanisms of defects, and countermeasure technology points
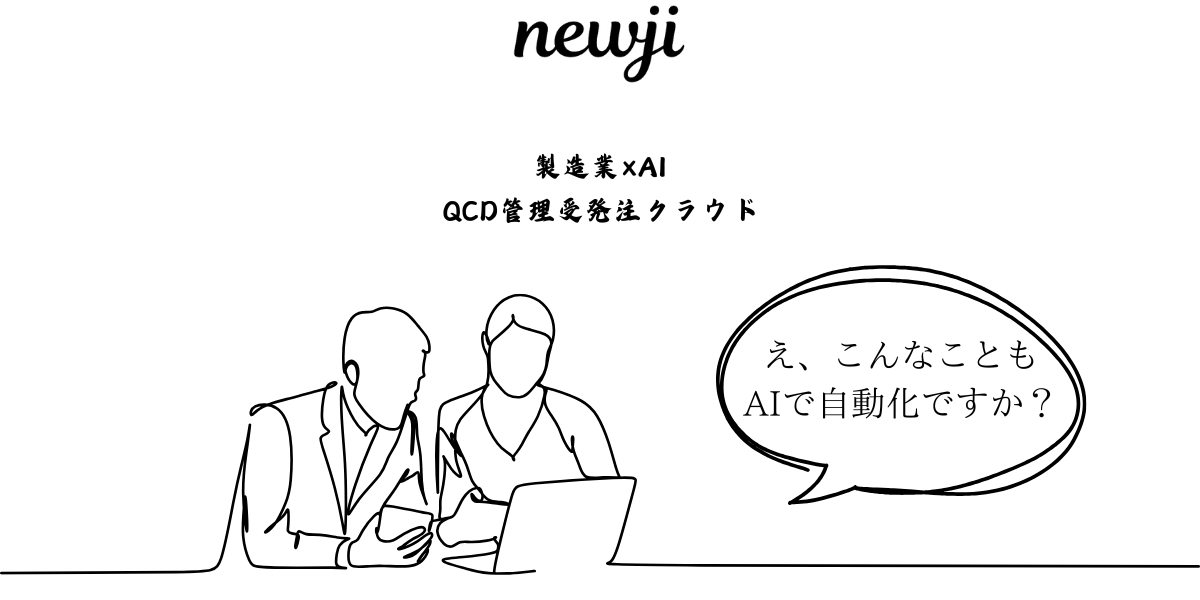
Basics of forging processing, mechanisms of defects, and countermeasure technology points
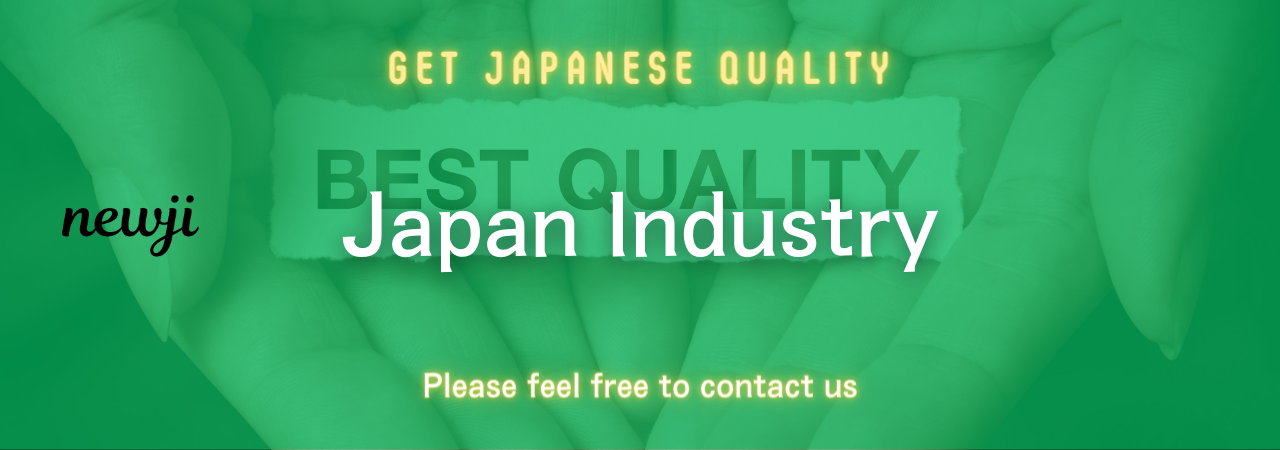
目次
Understanding Forging Processing
Forging is a fascinating technique of shaping metals into desired forms by applying compressive forces.
This process has been used for centuries to create tools, hardware, and even intricate art pieces.
At its core, forging involves heating metals to a pliable state and then using various techniques to shape them.
It’s a process that ensures the material retains its strength and integrity, which is why forged parts are commonly used in critical applications, such as in automotive and aerospace industries.
Types of Forging
There are several types of forging methods, each suited for different applications and materials.
1. Open Die Forging
In open die forging, the metal is deformed between multiple punches or dies that do not completely enclose the material.
This method allows for the shaping of large components and is commonly used for custom metalwork.
Due to the free-form nature of this process, it requires skilled operators to ensure precision and consistency.
2. Closed Die Forging
Closed die forging, also known as impression die forging, involves compressing the material in a die that fully surrounds it.
This technique is effective for mass-producing parts with complex shapes and requires less finishing work compared to open die forging.
The precision of closed die forging makes it ideal for manufacturing gears, crankshafts, and other detailed components.
3. Cold Forging
Cold forging is performed at or near room temperature, which can enhance the strength of the material through strain hardening.
This method is suitable for smaller parts where precision and finish quality are critical.
Cold forging is often used in the production of fasteners, hinges, and other small parts.
Defects in Forging
Despite its advantages, forging can sometimes result in defects that affect the quality of the end product.
Understanding these defects and their causes is vital for improving forging processes.
Common Forging Defects
1. Surface Cracks
Surface cracks are small fractures that appear on the surface of the forged parts.
They can be caused by excessive forces or improper temperature control during forging.
Surface cracks weaken the structural integrity of the component and can lead to failure over time.
2. Laps and Folds
Laps and folds occur when the metal folds over itself during the forging process.
This defect usually happens when the metal is not heated uniformly or when it is improperly manipulated.
Laps and folds can create weak points in the workpiece, making it unsuitable for critical applications.
3. Scale Pits
Scale pits are small depressions formed on the surface due to the oxidation of the metal during heating.
Scale can be difficult to remove entirely, leaving pits that compromise the surface finish.
These defects are often addressed by improving temperature control and post-forging treatments.
4. Internal Voids
Internal voids are cavities within the metal caused by trapped air or gas during the forging process.
They can significantly reduce the durability and strength of the metal.
This defect is commonly addressed by careful selection of raw materials and ensuring proper venting of dies.
Countermeasures and Technological Points
Effective countermeasures can greatly minimize forging defects and improve product quality.
Implementing good practices in material handling, temperature control, and equipment maintenance is crucial.
Optimizing Material Selection
Choosing the right metal alloy is a key factor in preventing defects.
Understanding the properties of different alloys helps in selecting the appropriate material for specific applications.
Materials with high workability and resistance to cracking are ideal for reducing the risk of surface and internal defects.
Maintaining Temperature Control
Accurate temperature control is fundamental in preventing defects such as surface cracks and scale pits.
Using advanced temperature monitoring systems ensures the metal reaches optimal temperatures for forging.
Consistent heating and cooling cycles also prevent unwanted changes in the metal’s structure.
Regular Equipment Maintenance
Regular maintenance of forging equipment is essential for ensuring consistent performance.
Checking for wear and tear, aligning dies, and calibrating machinery help prevent dimensional inaccuracies.
Properly maintained equipment reduces the likelihood of defects related to machine malfunction.
Skilled Workforce
Training and employing a skilled workforce significantly impacts the quality of forging.
Skilled operators can adjust processes in real-time to address unexpected issues, minimizing potential defects.
Continuous training in the latest forging techniques and technology introduces operators to innovative methods that improve productivity and quality.
Conclusion
Forging is a complex, yet rewarding process that remains indispensable in various industries.
By understanding the fundamentals of forging, common defects, and the technologies available to counteract them, manufacturers can produce high-quality products consistently.
Implementing the strategies discussed can lead to improved efficiency, fewer defects, and ultimately, reduced costs in metal forging operations.
Staying updated with technological advancements in forging will ensure manufacturers meet the ever-evolving needs of the industry.
資料ダウンロード
QCD調達購買管理クラウド「newji」は、調達購買部門で必要なQCD管理全てを備えた、現場特化型兼クラウド型の今世紀最高の購買管理システムとなります。
ユーザー登録
調達購買業務の効率化だけでなく、システムを導入することで、コスト削減や製品・資材のステータス可視化のほか、属人化していた購買情報の共有化による内部不正防止や統制にも役立ちます。
NEWJI DX
製造業に特化したデジタルトランスフォーメーション(DX)の実現を目指す請負開発型のコンサルティングサービスです。AI、iPaaS、および先端の技術を駆使して、製造プロセスの効率化、業務効率化、チームワーク強化、コスト削減、品質向上を実現します。このサービスは、製造業の課題を深く理解し、それに対する最適なデジタルソリューションを提供することで、企業が持続的な成長とイノベーションを達成できるようサポートします。
オンライン講座
製造業、主に購買・調達部門にお勤めの方々に向けた情報を配信しております。
新任の方やベテランの方、管理職を対象とした幅広いコンテンツをご用意しております。
お問い合わせ
コストダウンが利益に直結する術だと理解していても、なかなか前に進めることができない状況。そんな時は、newjiのコストダウン自動化機能で大きく利益貢献しよう!
(Β版非公開)