- お役立ち記事
- “Toyota-style why-why analysis” and implementation points for defect prevention measures
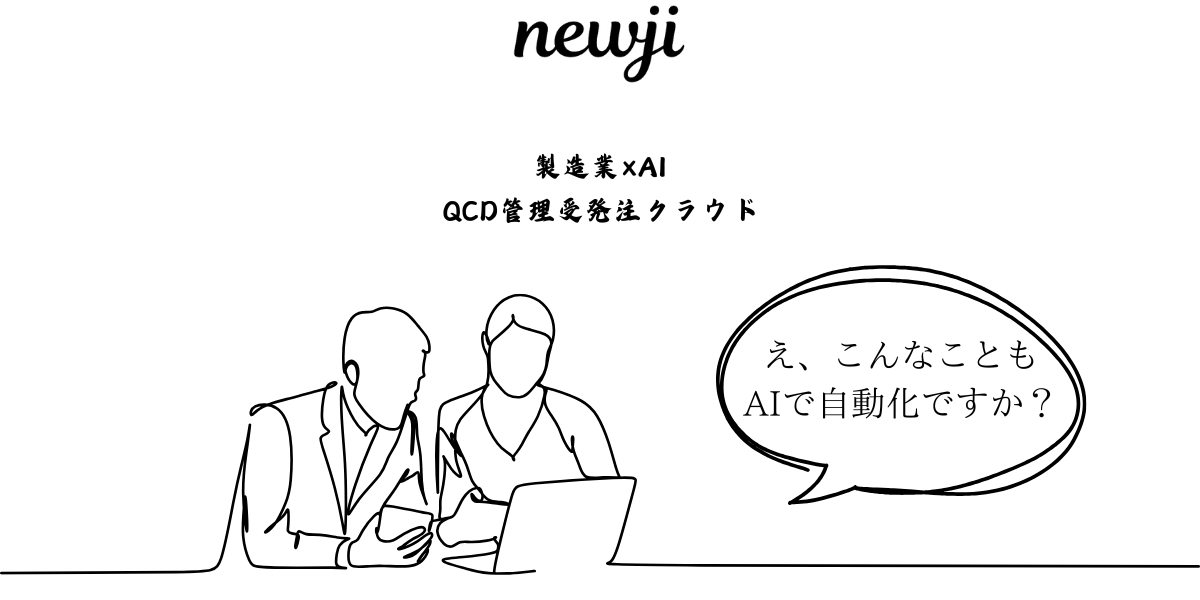
“Toyota-style why-why analysis” and implementation points for defect prevention measures
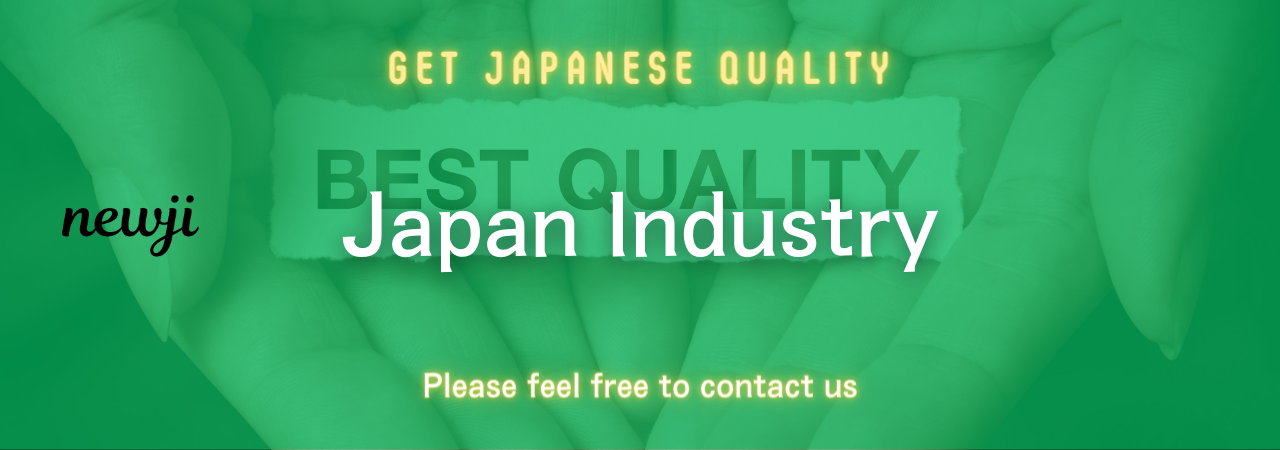
目次
Understanding Toyota-Style Why-Why Analysis
The Toyota-style why-why analysis is a problem-solving method that helps identify the root cause of a defect or issue.
It involves asking “why” multiple times until the fundamental cause is discovered.
This straightforward yet effective approach was popularized by Taiichi Ohno, the father of the Toyota Production System, and is integral to lean manufacturing practices.
By systematically drilling down into the problem, organizations can develop long-term solutions rather than just treating symptoms.
The Steps in Why-Why Analysis
Conducting a why-why analysis is generally a simple, five-step process.
1. Identify the Problem
It is crucial to clearly articulate the problem at hand.
Write a precise problem statement to set a clear focus.
Make sure that everyone involved understands what needs to be addressed.
2. Ask Why the Problem Occurred
Once the problem is identified, the first “why” should address why the problem exists or occurred.
Consider what immediate, visible factors contributed to the issue.
3. Ask Subsequent Whys
Continue asking “why” for each answer provided, diving deeper into secondary causes.
Typically, five iterations of questioning are recommended, but the number can vary depending on the complexity of the problem.
4. Identify the Root Cause
When you can no longer answer “why,” you have likely identified the root cause of the problem.
This root cause should be an actionable item that can be addressed directly.
5. Develop and Implement Solutions
Once the root cause is identified, brainstorm solutions to eliminate it.
Plan implementation steps, assign responsibilities, and establish a timeline to ensure the solution is applied effectively.
Benefits of Why-Why Analysis
Using a why-why analysis has several benefits, particularly in preventing defects and streamlining processes.
Improves Problem-Solving Skills
By repeatedly questioning and probing deeper into issues, team members enhance their problem-solving abilities.
It encourages critical thinking and analytical skills, fostering a culture of continuous improvement.
Prevents Recurrence of Defects
Addressing root causes rather than surface symptoms minimizes the likelihood of issues recurring.
This preventive measure is more cost-effective than constant repairs and reworks.
Enhances Team Collaboration
The process of conducting a why-why analysis is typically collaborative.
It builds consensus and encourages input from all team members, ensuring diverse perspectives are considered to develop robust solutions.
Aids in Documentation
Documenting each step in the why-why analysis helps in creating a knowledge base for future reference.
It provides a structured approach to understanding past problems and establishing a guideline for addressing similar issues.
Implementing Why-Why Analysis for Defect Prevention
To make the most out of Toyota-style why-why analysis, organizations must adopt a diligent and methodical approach to implementation.
Ensure Proper Training
Educate team members on the importance and methodology of why-why analysis.
Provide training sessions and resources to build competence and confidence in conducting thorough analyses.
Encourage a Blame-Free Environment
For effective problem-solving, create an environment where team members feel safe to express their thoughts without fear of repercussion.
This encourages honest and open communication, leading to more accurate root cause identification.
Maintain Consistent Documentation
Ensure that every step in the process is documented accurately and comprehensively.
This helps track progress, refine strategies, and prevent similar issues in the future.
Involve Cross-Functional Teams
Involve diverse team members from different departments to contribute their expertise and insights.
Cross-functional collaboration can uncover root causes that might have been overlooked by a single team.
Evaluate and Adapt Solutions
After implementing a solution, monitor its effectiveness and make adjustments as necessary.
Regularly review outcomes to ensure that the root cause has been addressed and prevented from recurring.
Challenges in Why-Why Analysis
While why-why analysis is a powerful tool, several challenges can arise in its implementation.
Inadequate Problem Definition
An improperly defined problem can detract from the efficacy of the analysis.
It may lead to addressing symptoms rather than the root cause.
Insufficient Depth of Analysis
Stopping the questioning process prematurely or failing to dig deep enough can result in superficial solutions.
It is important to persevere until the true root cause is discovered.
Lack of Consistent Follow-Through
Without proper follow-through, solutions may not be implemented effectively, and problems may persist.
Accountability and responsibility must be clearly assigned to ensure successful resolution.
Resistance to Change
Employees may resist implementing new solutions due to entrenched habits or skepticism.
Creating a culture of acceptance and buy-in is crucial for smooth adoption of changes.
Conclusion
The Toyota-style why-why analysis is a valuable tool for any organization seeking to improve its problem-solving capabilities and prevent defects.
By thoroughly investigating and addressing root causes, teams can devise effective, long-term solutions.
With clear problem definition, collaborative efforts, and comprehensive documentation, why-why analysis can drive continuous improvement and create a more efficient and productive work environment.
資料ダウンロード
QCD調達購買管理クラウド「newji」は、調達購買部門で必要なQCD管理全てを備えた、現場特化型兼クラウド型の今世紀最高の購買管理システムとなります。
ユーザー登録
調達購買業務の効率化だけでなく、システムを導入することで、コスト削減や製品・資材のステータス可視化のほか、属人化していた購買情報の共有化による内部不正防止や統制にも役立ちます。
NEWJI DX
製造業に特化したデジタルトランスフォーメーション(DX)の実現を目指す請負開発型のコンサルティングサービスです。AI、iPaaS、および先端の技術を駆使して、製造プロセスの効率化、業務効率化、チームワーク強化、コスト削減、品質向上を実現します。このサービスは、製造業の課題を深く理解し、それに対する最適なデジタルソリューションを提供することで、企業が持続的な成長とイノベーションを達成できるようサポートします。
オンライン講座
製造業、主に購買・調達部門にお勤めの方々に向けた情報を配信しております。
新任の方やベテランの方、管理職を対象とした幅広いコンテンツをご用意しております。
お問い合わせ
コストダウンが利益に直結する術だと理解していても、なかなか前に進めることができない状況。そんな時は、newjiのコストダウン自動化機能で大きく利益貢献しよう!
(Β版非公開)