- お役立ち記事
- Fundamentals of die casting technology and key points for countermeasures against casting defects and defects
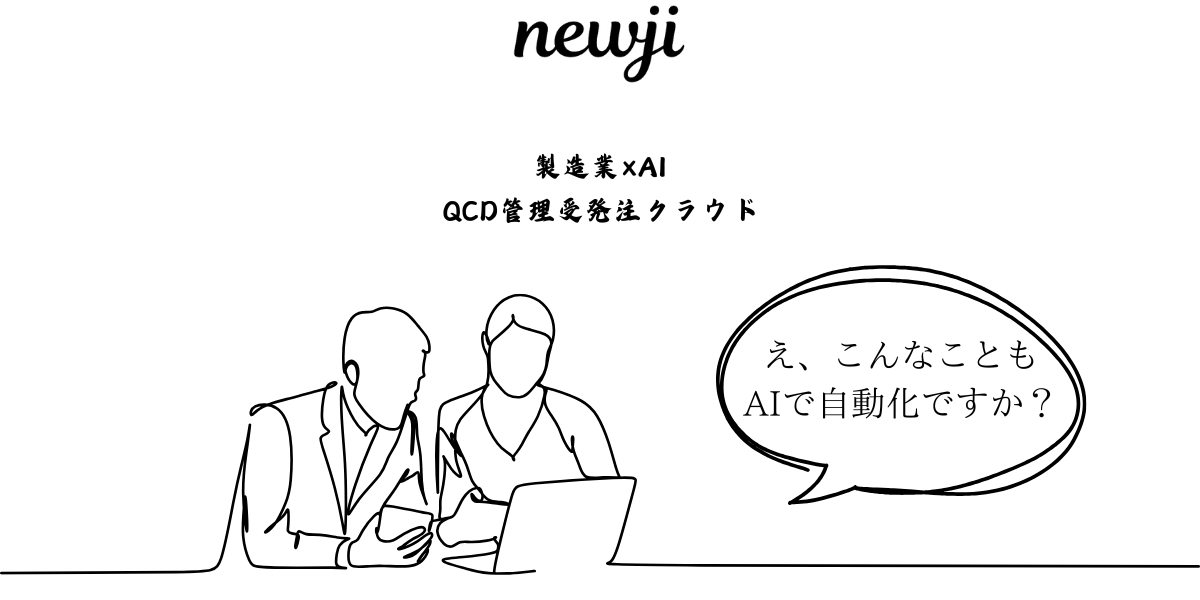
Fundamentals of die casting technology and key points for countermeasures against casting defects and defects
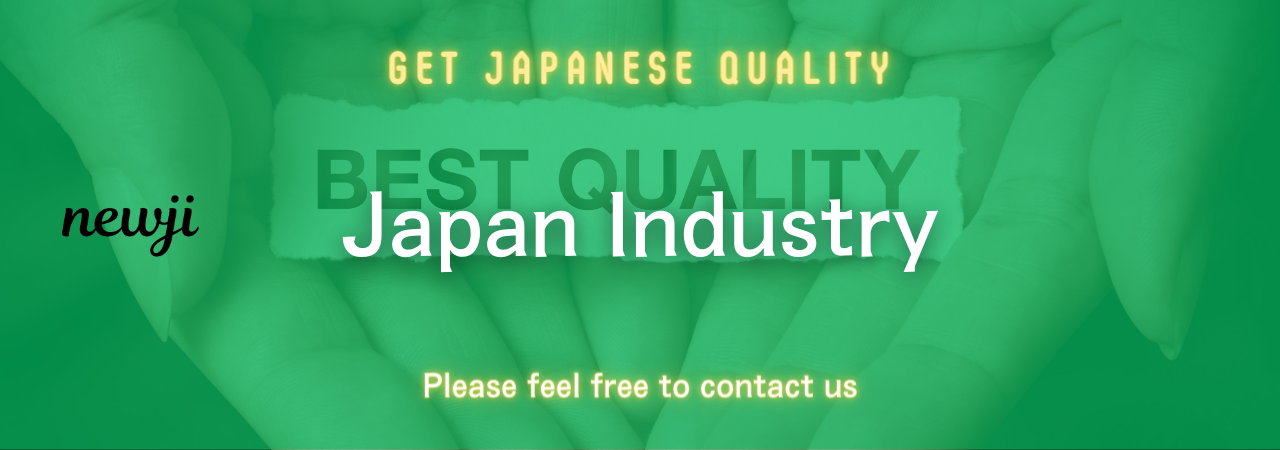
Die casting is a manufacturing process used to produce accurately dimensioned, sharply defined, and smooth or textured-surface metal parts. It is accomplished by forcing molten metal under high pressure into reusable metal dies. This process is highly popular due to its speed, cost-effectiveness, and the fine details of the finished product.
目次
Understanding Die Casting Technology
Die casting involves several steps that ensure high-quality production.
The Die Casting Process
The process starts with the preparation of the mold, which includes two parts: the stationary die half and the movable die half. The dies are created from steel and are designed to allow an exact shape of the final product.
Once the mold is in place, molten metal is poured into the mold under high pressure. This pressure is maintained until the metal solidifies. Precision temperature control is crucial in this stage to ensure the proper flow of metal.
Post-solidification involves the ejection of the cast part from the die, and any excess metal is trimmed or machined to produce the final product.
Types of Die Casting
Die casting is primarily divided into two types: hot chamber die casting and cold chamber die casting.
– **Hot Chamber Die Casting**: Used primarily for alloys with low melting points such as zinc. The metal is held in a furnace and a portion of the furnace is merged into the machine to make the casting process seamless.
– **Cold Chamber Die Casting**: More suitable for alloys with higher melting points, such as aluminum, brass, and certain magnesium alloys. The molten metal is ladled into a cold chamber where it is cast.
Advantages of Die Casting
Die casting offers several benefits, making it an attractive choice for mass production.
– **Accuracy and Efficiency**: The technique produces parts that are dimensionally accurate and require little or no machining.
– **Complex Shapes**: Capable of producing complex shapes with great detail and varied wall thickness, which is not always possible with other manufacturing processes.
– **Versatility**: Die casting can be used to create a wide range of components used in different industries including automotive, aerospace, and consumer electronics.
– **Strength and Weight**: The parts produced have high tensile strength and can be made lighter by creating thin walls.
Common Die Casting Defects
Despite its benefits, die casting is prone to certain defects that can affect the integrity and quality of the final product.
Porosity
Porosity is the presence of tiny holes or voids within the cast part. It can result from trapped gases, insufficient metal supply, or improper mold design. Porosity weakens the structural integrity of the component and may affect its performance.
Incomplete Filling
Also known as “short shot,” this defect occurs when the metal fails to fill the mold cavity entirely. It typically results from inadequate pressure, improper temperatures, or incorrect flow rates.
Flash
Flash appears as excess material on the edges of the cast part, usually due to excessively high metal pressure or poorly aligned die halves. It requires additional machining to remove unwanted material.
Surface Defects
Surface defects like pitting, grooves, or cold shuts can form due to inconsistent cooling rates, dirt in the mold, or incorrect die temperature.
Countermeasures Against Casting Defects
Understanding these common defects allows for implementation of strategic countermeasures to enhance product quality.
Optimizing Mold Design
Ensuring the mold is designed perfectly is critical. Simulations can predict potential issues in the design phase, allowing for modifications before actual production. Proper venting and adequate gate design help reduce porosity.
Maintaining Ideal Process Conditions
Careful regulation of temperature and pressure during die casting is necessary. This helps in achieving optimal metal flow and prevents defects like short shots or cold shuts.
Regular Equipment Maintenance
Scheduled maintenance of machinery ensures consistent production quality. Checking for wear and tear, especially in dies and casting guns, prevents unwanted surface defects.
Quality Control Procedures
Implementing a robust quality control system, including data monitoring and rigorous inspection, helps in early detection of defects, enabling swift corrective measures.
Conclusion
Die casting is a sophisticated yet efficient manufacturing process utilized widely across industries. Understanding its fundamentals, from types to typical defects, is crucial for leveraging its full potential.
By addressing potential drawbacks with appropriate countermeasures and constantly refining techniques, manufacturers can ensure the high standards expected in today’s competitive market. With rehearsed precision and strategic insights, die casting remains a cornerstone of modern manufacturing, balancing efficiency with exceptional quality.
資料ダウンロード
QCD調達購買管理クラウド「newji」は、調達購買部門で必要なQCD管理全てを備えた、現場特化型兼クラウド型の今世紀最高の購買管理システムとなります。
ユーザー登録
調達購買業務の効率化だけでなく、システムを導入することで、コスト削減や製品・資材のステータス可視化のほか、属人化していた購買情報の共有化による内部不正防止や統制にも役立ちます。
NEWJI DX
製造業に特化したデジタルトランスフォーメーション(DX)の実現を目指す請負開発型のコンサルティングサービスです。AI、iPaaS、および先端の技術を駆使して、製造プロセスの効率化、業務効率化、チームワーク強化、コスト削減、品質向上を実現します。このサービスは、製造業の課題を深く理解し、それに対する最適なデジタルソリューションを提供することで、企業が持続的な成長とイノベーションを達成できるようサポートします。
オンライン講座
製造業、主に購買・調達部門にお勤めの方々に向けた情報を配信しております。
新任の方やベテランの方、管理職を対象とした幅広いコンテンツをご用意しております。
お問い合わせ
コストダウンが利益に直結する術だと理解していても、なかなか前に進めることができない状況。そんな時は、newjiのコストダウン自動化機能で大きく利益貢献しよう!
(Β版非公開)