- お役立ち記事
- Mechanism of metal fatigue fracture and its application to fatigue design and fracture accident analysis
月間77,185名の
製造業ご担当者様が閲覧しています*
*2025年2月28日現在のGoogle Analyticsのデータより
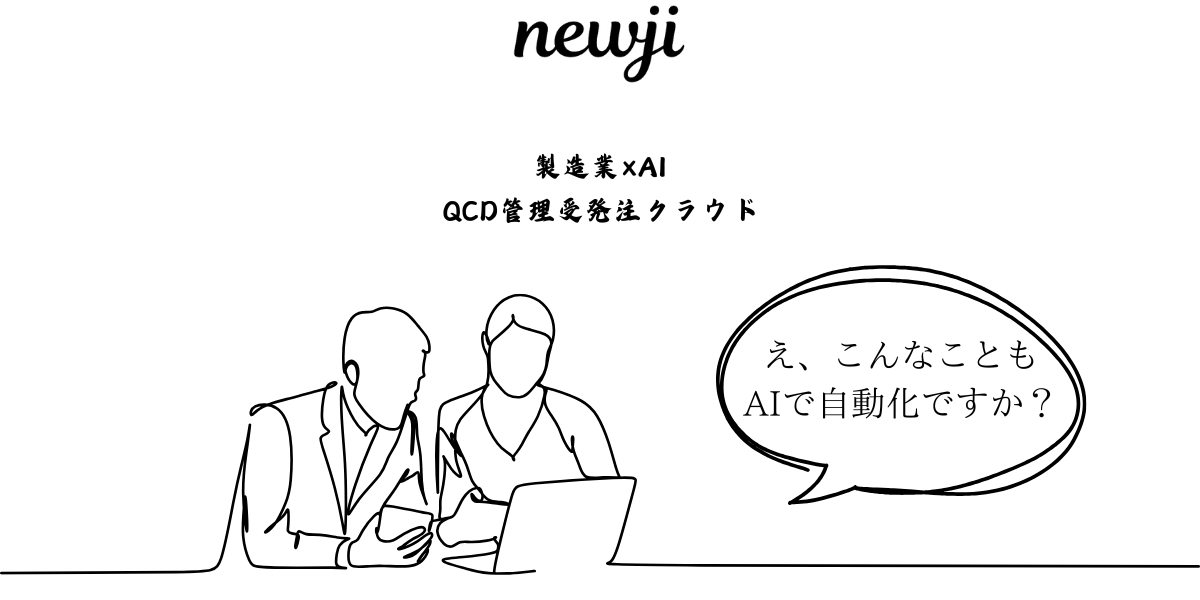
Mechanism of metal fatigue fracture and its application to fatigue design and fracture accident analysis
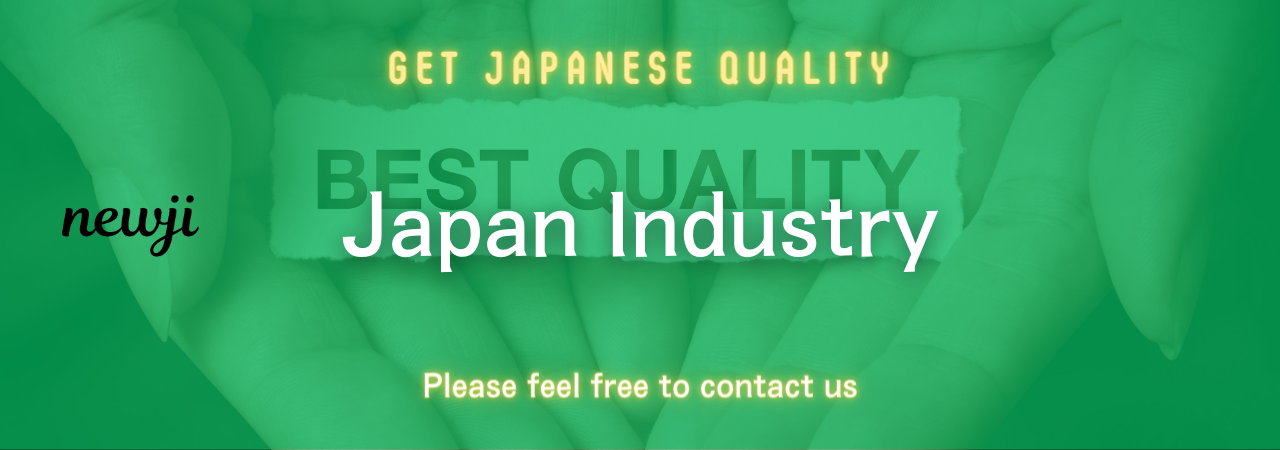
目次
Understanding Metal Fatigue
Metal fatigue is a phenomenon that leads to the progressive and localized structural damage of a material under cyclic loading.
This means that when metal parts are repeatedly subjected to stress and strain, they can ultimately break even if the load is less than the metal’s tensile strength.
The concept of metal fatigue is critical in a wide array of industries, especially those involving transportation, construction, and manufacturing.
This is because it directly impacts the lifespan and reliability of metal components.
What Causes Metal Fatigue?
Metal fatigue occurs due to the repeated application of stress over time.
This cyclic stress creates microscopic cracks in the metal that gradually expand and weaken the material.
Unlike a sudden fracture that happens due to an overwhelming force, metal fatigue is a silent process that often goes unnoticed until a failure occurs.
Factors contributing to metal fatigue include the magnitude of the stress, the number of cycles, and the environment in which the metal is used.
The Mechanism of Metal Fatigue Fracture
Understanding the mechanism of metal fatigue fracture is crucial for predicting and preventing potential failures.
The process generally involves three main stages: initiation, propagation, and final fracture.
Initially, small cracks begin at points of stress concentration, such as surface scratches or internal material defects.
These cracks then start to propagate with each cycle of stress, gradually increasing in size.
Over time, the remaining uncracked section becomes too weak to withstand the loads, leading to a sudden and complete fracture.
The Role of Microstructure
The microstructure of metal plays a significant role in its susceptibility to fatigue.
Factors such as grain size, phase distribution, and the presence of inclusions can influence how easily cracks initiate and propagate.
For example, metals with a finer grain structure tend to exhibit better resistance to fatigue because their small grains can inhibit the movement of dislocations.
Conversely, the presence of inclusions or impurities can act as stress concentrators and initiate cracks more easily.
Applications in Fatigue Design
One of the key applications of understanding metal fatigue is in fatigue design.
Fatigue design involves the development of products and structures that can withstand the anticipated cyclic stresses throughout their service life.
Engineers utilize several techniques to achieve this, including selecting appropriate materials, optimizing designs to reduce stress concentrations, and conducting fatigue testing.
Material Selection and Treatment
The choice of material is paramount in fatigue design.
Some materials naturally exhibit better fatigue resistance due to their inherent properties.
For instance, stainless steel and titanium alloys are known for their high resistance to fatigue.
In addition, surface treatments such as shot peening or surface hardening can enhance a metal’s fatigue strength.
These treatments work by introducing compressive surface stresses that counteract the tensile stresses that cause fatigue.
Design Optimization
Another critical approach in fatigue design is to optimize the geometry and design of components to minimize stress concentrations.
This can involve modifying the shape of a component, adding fillets or radii to sharp corners, and ensuring that load paths are as smooth as possible.
Computer-aided design (CAD) and finite element analysis (FEA) tools are instrumental in identifying and addressing potential stress concentrations in a design.
Fatigue Testing
Fatigue testing is a method to evaluate a material’s performance under simulated service conditions.
This testing helps engineers to understand how materials respond to cyclic loading and to estimate their fatigue life.
Typically, samples are subjected to repeated cycles of stress until failure occurs.
The results are then used to create S-N curves (stress-number of cycles) that provide valuable data for fatigue design.
Analysis of Fatigue Fracture Accidents
When a fatigue fracture accident occurs, performing a detailed fracture analysis is essential to understand the root cause and prevent future occurrences.
The analysis generally involves a combination of visual inspection, non-destructive testing, and metallurgical examination.
Visual Inspection and Non-destructive Testing
The initial step in fracture analysis often involves a visual inspection to identify any obvious signs of fatigue, such as beach marks or striations.
Non-destructive testing methods, including ultrasonic testing and dye penetrant inspection, can further reveal the extent and location of cracks without damaging the component.
Metallurgical Examination
A deeper understanding of the fracture mechanism requires metallurgical examination, which involves analyzing the microstructure of the fractured component.
Techniques such as scanning electron microscopy (SEM) and energy-dispersive X-ray spectroscopy (EDX) provide detailed images and elemental analysis of the fracture surface.
This information is crucial in identifying the initiation sites and understanding the conditions that led to crack growth.
Implementing Preventative Measures
Conclusions from fatigue fracture analysis can be used to implement preventative measures.
This may include redesigning components, changing materials, or modifying manufacturing processes.
The ultimate goal is to enhance the durability and reliability of metal components, thus preventing similar failures in the future.
Understanding the mechanism of metal fatigue fracture is crucial in ensuring the safety and longevity of structures and mechanical components.
Through effective fatigue design and thorough analysis of fracture accidents, engineers can mitigate the risks associated with metal fatigue and improve the overall quality of their products.
As industries continue to evolve, ongoing research and development in metal fatigue are essential to keep up with new challenges and technological advancements.
資料ダウンロード
QCD管理受発注クラウド「newji」は、受発注部門で必要なQCD管理全てを備えた、現場特化型兼クラウド型の今世紀最高の受発注管理システムとなります。
ユーザー登録
受発注業務の効率化だけでなく、システムを導入することで、コスト削減や製品・資材のステータス可視化のほか、属人化していた受発注情報の共有化による内部不正防止や統制にも役立ちます。
NEWJI DX
製造業に特化したデジタルトランスフォーメーション(DX)の実現を目指す請負開発型のコンサルティングサービスです。AI、iPaaS、および先端の技術を駆使して、製造プロセスの効率化、業務効率化、チームワーク強化、コスト削減、品質向上を実現します。このサービスは、製造業の課題を深く理解し、それに対する最適なデジタルソリューションを提供することで、企業が持続的な成長とイノベーションを達成できるようサポートします。
製造業ニュース解説
製造業、主に購買・調達部門にお勤めの方々に向けた情報を配信しております。
新任の方やベテランの方、管理職を対象とした幅広いコンテンツをご用意しております。
お問い合わせ
コストダウンが利益に直結する術だと理解していても、なかなか前に進めることができない状況。そんな時は、newjiのコストダウン自動化機能で大きく利益貢献しよう!
(β版非公開)