- お役立ち記事
- Fundamentals of friction, wear, and lubrication, wear improvement technology, and its key points
月間77,185名の
製造業ご担当者様が閲覧しています*
*2025年2月28日現在のGoogle Analyticsのデータより
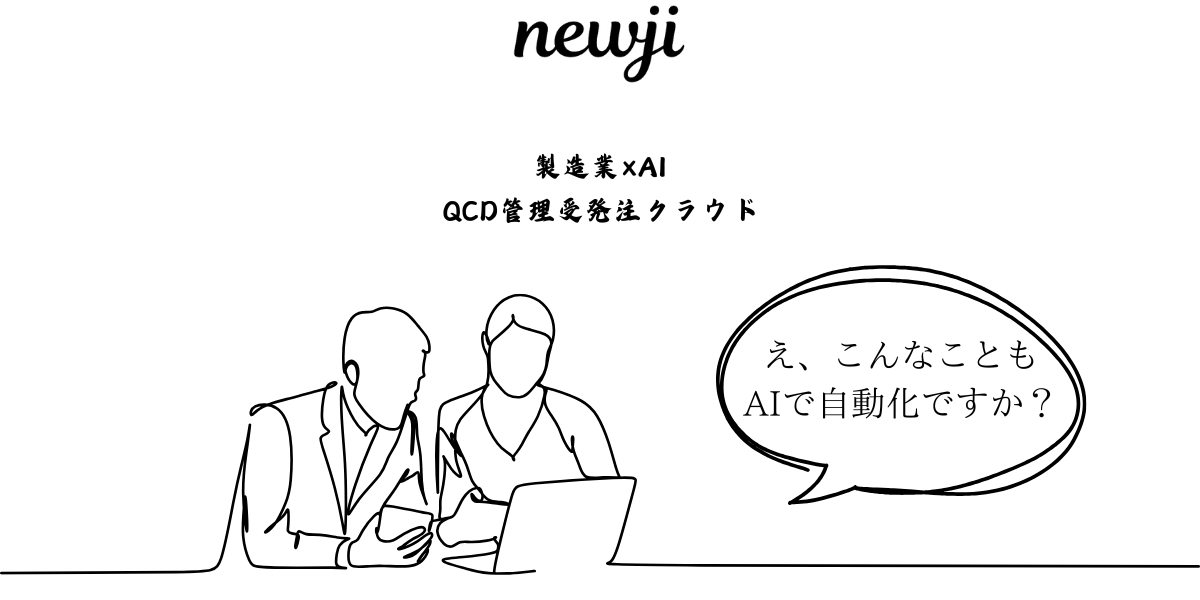
Fundamentals of friction, wear, and lubrication, wear improvement technology, and its key points
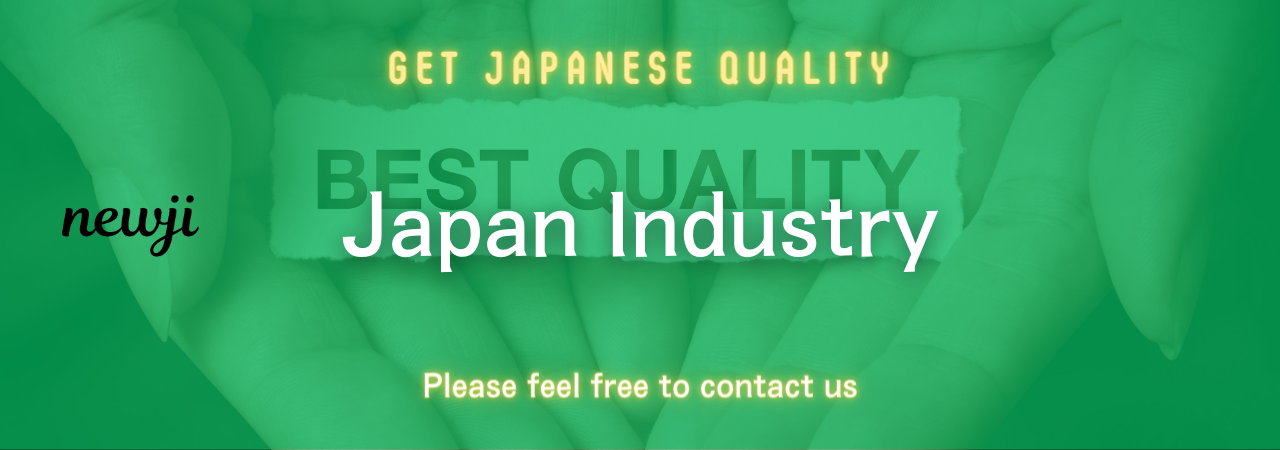
目次
Understanding Friction
Friction is a natural force that opposes motion between two surfaces that are in contact.
It plays a crucial role in our daily lives and various technological applications.
Friction can be helpful, such as when it provides traction for walking, or it can be a nuisance, like the resistance one feels when pushing a heavy object.
Understanding the basics of friction helps in finding ways to manage and utilize it effectively.
Types of Friction
There are mainly three types of friction: static, sliding, and rolling friction.
Static friction acts on objects that are not moving, helping to keep them in place.
Sliding friction occurs when two surfaces slide over each other and is generally less than static friction.
Rolling friction happens when an object rolls over a surface and is usually much less than sliding friction.
Recognizing these types aids in determining how different materials will interact.
Factors Affecting Friction
The amount of friction primarily depends on the nature of the surfaces in contact and the force pressing them together.
Smoother or lubricated surfaces tend to have less friction, while rough surfaces increase it.
The weight or normal force also plays a role; heavier objects will generally experience more friction than lighter ones.
Knowing these factors can assist in controlling friction to achieve desired outcomes.
Exploring Wear
Wear is the gradual removal or deformation of material due to mechanical action, often as a result of friction.
It is a natural consequence that occurs when surfaces interact over time.
Wear can lead to the deterioration of materials, affecting the performance and lifespan of tools, machinery, and components.
Types of Wear
There are several types of wear, including abrasive, adhesive, surface fatigue, and corrosive wear.
Abrasive wear happens when material is removed through scraping or grinding.
Adhesive wear occurs when materials transfer between surfaces due to adhesion.
Surface fatigue wear is the result of repeated loading, causing material degradation.
Corrosive wear occurs when chemical reactions affect the material during mechanical interaction.
Understanding these types helps in identifying and addressing wear issues effectively.
Factors Contributing to Wear
Several factors contribute to wear, such as load, speed, temperature, and environmental conditions.
Higher loads and speeds can increase the rate of wear due to greater force and heat generation.
Temperature can influence the strength and hardness of materials, affecting their wear resistance.
Environmental factors like moisture, dust, and chemicals can also accelerate wear by impacting surface conditions.
Recognizing these contributors aids in finding effective wear reduction strategies.
Lubrication and Its Importance
Lubrication involves applying a substance, known as a lubricant, between surfaces to reduce friction and wear.
It plays a vital role in enhancing efficiency and prolonging the life of machinery and components.
By reducing direct contact between surfaces, lubrication also aids in dissipating heat and distributing loads more evenly.
Types of Lubricants
Lubricants come in various forms, including oils, greases, and solid lubricants.
Oils are liquid lubricants that flow easily, making them suitable for high-speed applications.
Greases are thicker substances that offer excellent adherence to surfaces and are used in moderate-speed applications.
Solid lubricants, like graphite, provide lubrication under extreme conditions such as high temperatures or vacuum environments.
Choosing the right type of lubricant is essential for optimal performance and wear reduction.
Lubrication Techniques
Several lubrication techniques exist to ensure effective application, such as manual lubrication, automatic lubrication systems, and dry lubrication.
Manual lubrication involves applying a lubricant periodically by hand.
Automatic lubrication systems deliver lubricants to surfaces in measured amounts at regular intervals, which is ideal for hard-to-reach or continuously operating systems.
Dry lubrication uses solid lubricants and is beneficial for environments where liquid lubricants are unsuitable.
Selecting an appropriate lubrication method can significantly influence the efficiency of machinery and components.
Wear Improvement Technologies
To enhance wear resistance and prolong the life of materials, various wear improvement technologies have been developed.
These technologies focus on modifying surface properties and utilizing advanced materials.
Surface Treatments
Surface treatments, such as heat treatment, coatings, and surface hardening, can significantly improve wear resistance.
Heat treatment alters the microstructure of a material to enhance its hardness and durability.
Coatings, like ceramic or metallic layers, provide a protective barrier against wear and corrosion.
Surface hardening techniques increase surface strength while maintaining core toughness, offering a balanced approach to wear resistance.
These treatments help materials withstand harsh operating conditions.
Advanced Materials
The development of advanced materials, such as composites and ceramics, has expanded the possibilities for wear improvement.
Composites combine different materials to harness desirable properties like strength, toughness, and resistance to wear and corrosion.
Ceramic materials offer excellent hardness and heat resistance, making them suitable for demanding applications.
Incorporating these materials into machinery and components supports long-lasting performance and reliability.
Key Points for Wear Improvement
When implementing wear improvement strategies, several key points should be considered.
Firstly, understanding the specific operating conditions and environment is essential.
Tailoring solutions to meet unique challenges ensures effectiveness and efficiency.
Secondly, regular monitoring and maintenance are crucial for identifying wear issues before they escalate.
Implementing proactive measures helps to maintain performance and reduce downtime.
Lastly, investment in research and development can lead to innovative solutions and technological advancements.
By staying informed and adopting cutting-edge approaches, industries can enhance wear resistance and improve overall system longevity.
In conclusion, understanding the fundamentals of friction, wear, and lubrication is pivotal for optimizing machinery and components.
Employing wear improvement technologies and adhering to key points can significantly extend the lifespan and efficiency of systems.
By mastering these concepts, individuals and industries can ensure the reliability and performance of their equipment in various applications.
資料ダウンロード
QCD管理受発注クラウド「newji」は、受発注部門で必要なQCD管理全てを備えた、現場特化型兼クラウド型の今世紀最高の受発注管理システムとなります。
ユーザー登録
受発注業務の効率化だけでなく、システムを導入することで、コスト削減や製品・資材のステータス可視化のほか、属人化していた受発注情報の共有化による内部不正防止や統制にも役立ちます。
NEWJI DX
製造業に特化したデジタルトランスフォーメーション(DX)の実現を目指す請負開発型のコンサルティングサービスです。AI、iPaaS、および先端の技術を駆使して、製造プロセスの効率化、業務効率化、チームワーク強化、コスト削減、品質向上を実現します。このサービスは、製造業の課題を深く理解し、それに対する最適なデジタルソリューションを提供することで、企業が持続的な成長とイノベーションを達成できるようサポートします。
製造業ニュース解説
製造業、主に購買・調達部門にお勤めの方々に向けた情報を配信しております。
新任の方やベテランの方、管理職を対象とした幅広いコンテンツをご用意しております。
お問い合わせ
コストダウンが利益に直結する術だと理解していても、なかなか前に進めることができない状況。そんな時は、newjiのコストダウン自動化機能で大きく利益貢献しよう!
(β版非公開)