- お役立ち記事
- Basics of surface hardening technology by heat treatment and its application to improve functionality
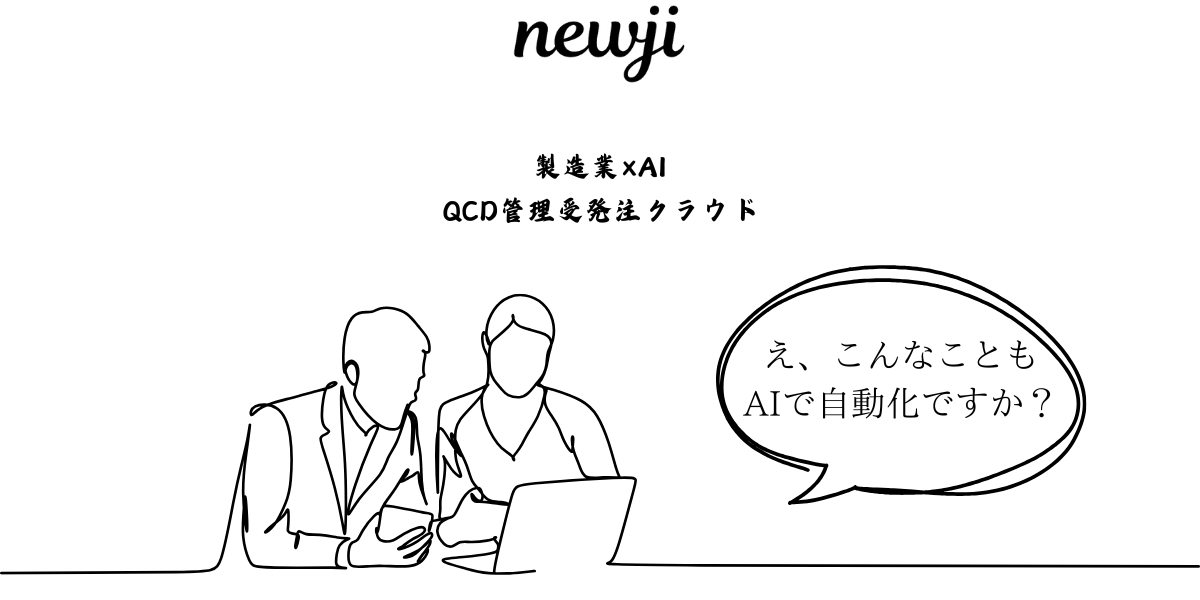
Basics of surface hardening technology by heat treatment and its application to improve functionality
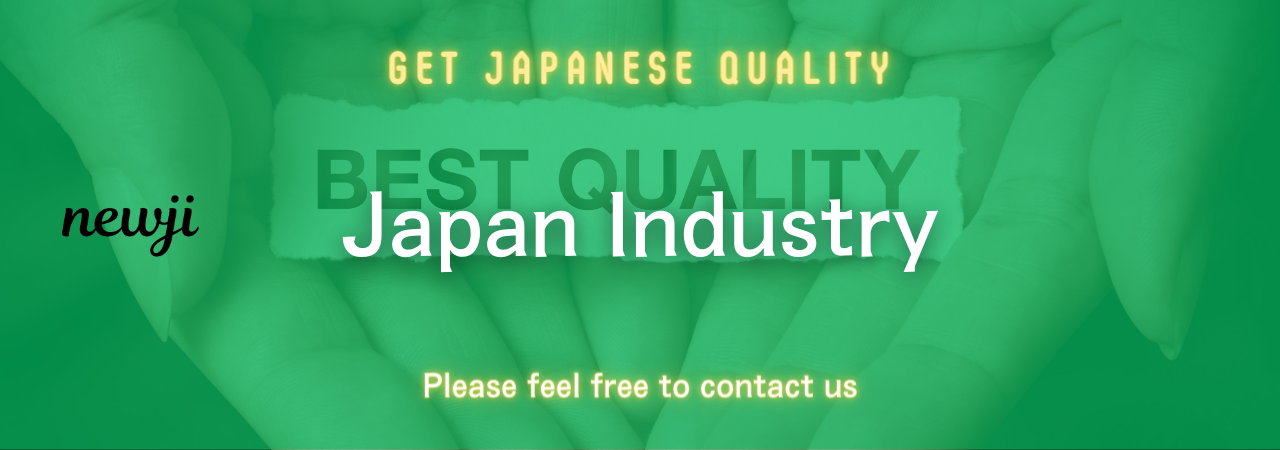
目次
Introduction to Surface Hardening Technology
Surface hardening is a process that strengthens the surface of a material by applying heat treatment techniques.
This process is critical in manufacturing, engineering, and metallurgy, where durability, wear resistance, and functionality of a component are paramount.
Surface hardening enhances the object’s surface properties while maintaining its core’s original toughness and ductility.
In this article, we will delve into the basics of surface hardening technology, its methods, and its applications.
Understanding Heat Treatment
Heat treatment is a controlled process of heating and cooling metals to alter their physical and mechanical properties without changing their shape.
The primary goal is to make the material harder, stronger, or more ductile, depending on its intended use.
Heat treatment includes various techniques, but when it comes to surface hardening, a few specific methods are usually employed to enhance surface characteristics.
Types of Surface Hardening Techniques
Numerous techniques exist for surface hardening via heat treatment.
Some of the most commonly used include:
Induction Hardening
Induction hardening is a non-contact heating process that uses alternating magnetic fields to heat a metal surface quickly and uniformly.
This method is efficient and precise, making it suitable for components like gears, shafts, and bearings.
The rapid heating followed by quenching results in a significantly tougher surface.
Carburizing
Carburizing involves introducing carbon into a steel component’s surface layer at high temperatures.
The steel part is heated in a carbon-rich environment, typically using gas or solid substances.
This process creates a hard outer layer called a ‘case,’ while the interior remains softer.
Carburizing is crucial for components like crankshafts and gears where the surface must withstand high wear and tear.
Nitriding
Nitriding involves infusing nitrogen gas into the surface of a material.
This process forms hard nitrides on the surface, leading to excellent wear and fatigue resistance.
Unlike other surface hardening techniques, nitriding occurs at relatively low temperatures, minimizing distortion.
It is widely used in camshafts, cylinder liners, and extrusion dies.
Flame Hardening
In flame hardening, a component’s surface is heated using an open flame to reach a specified temperature.
After reaching the desired heat level, the surface is immediately quenched, creating a hardened layer.
This method is highly effective for strengthening larger steel components like rollers and rails.
Application of Surface Hardening Technology
The primary reason for employing surface hardening is to enhance the durability and performance of components exposed to friction, impact, and various forms of wear and tear.
Automotive Industry
In the automotive industry, surface hardening is crucial for critical components such as crankshafts, camshafts, and gears.
These parts endure extreme operational conditions, including high speeds and loads, requiring exceptional surface toughness.
Aerospace Industry
Aerospace engineering demands high-strength materials with exceptional wear resistance.
Surface hardening techniques like carburizing and nitriding are used to enhance the durability and lifespan of components like gears and bearings in aircraft engines.
Tool Manufacturing
Tools such as cutting blades, drills, and molds need to withstand immense pressure and wear over time.
Heat-treated surfaces increase their hardness, boosting their effectiveness and longevity.
Construction Equipment
Construction machinery often operates under harsh conditions.
Hardened surfaces in components like excavator teeth and bulldozer blades ensure they resist wear and impacts from heavy-duty operations.
Benefits of Surface Hardening
Surface hardening brings about numerous advantages:
1. **Enhanced Wear Resistance**: By hardening the surface, components become more resistant to abrasion and wear, prolonging their service life.
2. **Improved Fatigue Strength**: Hardened surfaces can better withstand cyclic stress, reducing the risk of component failure under repeated loads.
3. **Corrosion Resistance**: Some hardening processes increase a material’s barrier against corrosion and surface degradation.
4. **Cost-Effectiveness**: While the initial investment in heat treatment may be higher, the longer lifespan of hardened components reduces replacement costs and maintenance, proving cost-effective in the long run.
Conclusion
Surface hardening technology, through heat treatment, plays a vital role in enhancing the functionality and lifespan of a wide range of products across various industries.
With a clear understanding of the different methods and their respective applications, manufacturers can select the best techniques to meet their specific needs.
As advancements in heat treatment continue, the potential for developing even more durable and efficient components grows, driving innovation and economic efficiency in manufacturing processes.
資料ダウンロード
QCD調達購買管理クラウド「newji」は、調達購買部門で必要なQCD管理全てを備えた、現場特化型兼クラウド型の今世紀最高の購買管理システムとなります。
ユーザー登録
調達購買業務の効率化だけでなく、システムを導入することで、コスト削減や製品・資材のステータス可視化のほか、属人化していた購買情報の共有化による内部不正防止や統制にも役立ちます。
NEWJI DX
製造業に特化したデジタルトランスフォーメーション(DX)の実現を目指す請負開発型のコンサルティングサービスです。AI、iPaaS、および先端の技術を駆使して、製造プロセスの効率化、業務効率化、チームワーク強化、コスト削減、品質向上を実現します。このサービスは、製造業の課題を深く理解し、それに対する最適なデジタルソリューションを提供することで、企業が持続的な成長とイノベーションを達成できるようサポートします。
オンライン講座
製造業、主に購買・調達部門にお勤めの方々に向けた情報を配信しております。
新任の方やベテランの方、管理職を対象とした幅広いコンテンツをご用意しております。
お問い合わせ
コストダウンが利益に直結する術だと理解していても、なかなか前に進めることができない状況。そんな時は、newjiのコストダウン自動化機能で大きく利益貢献しよう!
(Β版非公開)