- お役立ち記事
- Strength design and residual stress measurement and reduction molding methods for plastic molded products
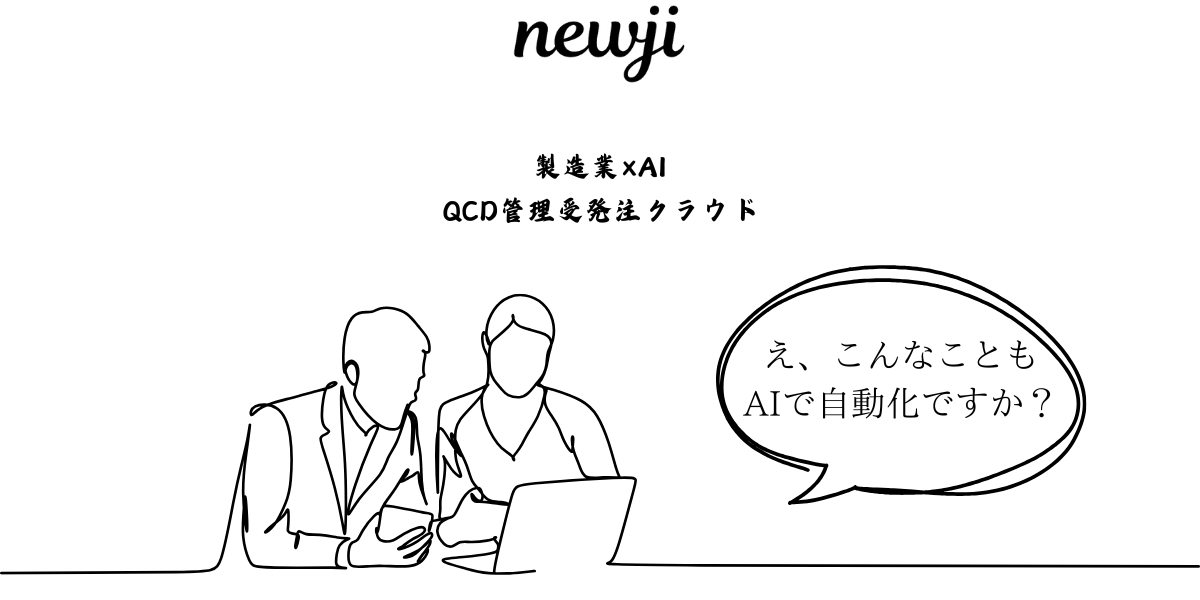
Strength design and residual stress measurement and reduction molding methods for plastic molded products
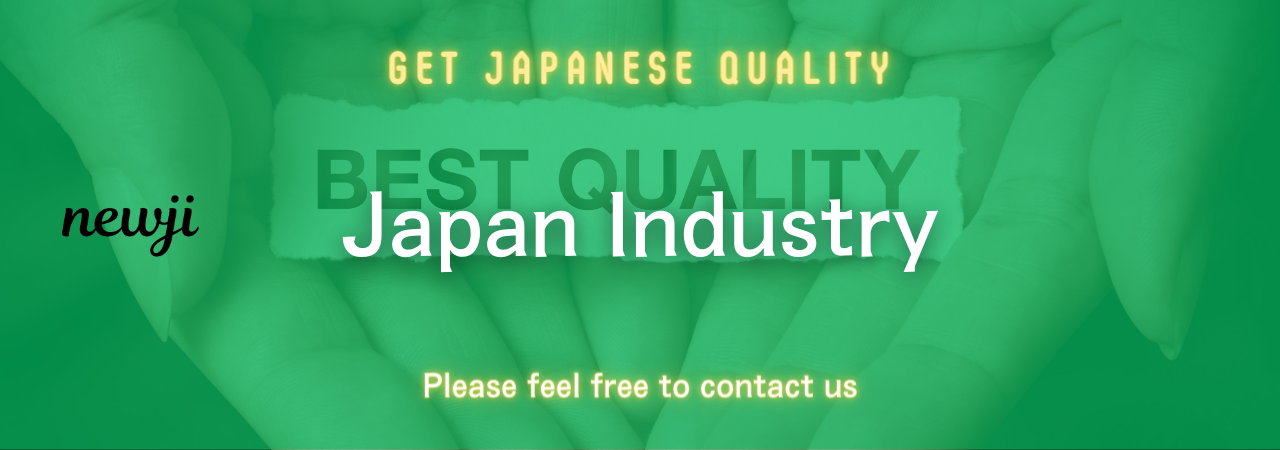
目次
Introduction to Plastic Molded Products
Plastic molded products have become an integral part of our daily lives, encompassing diverse applications from household items to automotive components.
These products are created using different molding techniques, each offering unique advantages and challenges.
Understanding strength design and residual stress in these products is crucial for manufacturing high-quality items.
Understanding Strength Design in Plastic Molded Products
Strength design is a vital concept in the creation of plastic molded products.
It involves ensuring that the product can withstand the intended loads and environmental conditions without failure.
The strength of a molded product is determined by various factors, including the material used, the molding process, and the product’s design.
The Role of Material in Strength Design
The choice of material plays a significant role in determining the strength of a plastic molded product.
Different plastics have varying properties such as tensile strength, toughness, and flexibility.
Therefore, selecting the appropriate material based on the product’s application is essential.
Design Considerations for Enhanced Strength
The design of the molded product also affects its strength. This includes the thickness of the walls, the presence of ribs or gussets for reinforcement, and the overall shape of the product.
A well-designed product can distribute stress evenly, reducing the likelihood of failure.
Residual Stress in Plastic Molded Products
Residual stress is an unavoidable consequence of the molding process.
It refers to the internal stresses that remain in the product after it has been molded and cooled.
These stresses can affect the product’s performance, leading to warping, cracking, or other forms of failure.
Causes of Residual Stress
Residual stress can be caused by several factors during the molding process.
These include uneven cooling, differential shrinkage, and the orientation of polymer chains.
Understanding these causes is crucial for developing strategies to minimize residual stress.
Measuring Residual Stress
Measuring residual stress is essential for assessing the quality of a plastic molded product.
Several techniques are used for this purpose, including optical methods, X-ray diffraction, and thermal analysis.
These methods provide valuable insights into the internal stress distribution within the product.
Methods for Reducing Residual Stress
Reducing residual stress in plastic molded products can significantly enhance their performance and longevity.
Manufacturers employ various techniques to achieve this goal.
Optimizing Molding Conditions
One effective way to reduce residual stress is by optimizing the molding conditions.
This includes controlling the temperature, pressure, and cooling rate during the molding process.
By carefully managing these parameters, manufacturers can minimize stress induction.
Annealing
Annealing is a post-molding process that involves heating the plastic to a specific temperature and then slowly cooling it.
This process allows the polymer chains to relax, reducing internal stresses and improving the product’s structural integrity.
Mold Design Adjustments
Adjusting mold design can also help in minimizing residual stress.
For example, incorporating uniform wall thickness and eliminating sharp corners can prevent stress concentration and ensure even stress distribution.
Molding Techniques for High-Quality Products
Different molding techniques are used to produce plastic products, each with its pros and cons.
Choosing the right method is crucial for achieving the desired product quality.
Injection Molding
Injection molding is one of the most popular techniques for producing plastic products.
It involves injecting molten plastic into a mold under high pressure.
This method is ideal for mass production due to its efficiency and precision.
Blow Molding
Blow molding is used primarily for making hollow products like bottles and containers.
In this process, a tube of molten plastic is expanded against the walls of a mold by blowing air into it.
Blow molding allows for the creation of intricate shapes.
Rotational Molding
Rotational molding is a versatile technique used to produce large, hollow objects such as tanks and playground equipment.
The process involves rotating a mold filled with plastic powder while heating it.
The plastic melts and coats the interior of the mold, forming the desired shape.
Conclusion
Strength design and residual stress management are critical aspects of producing high-quality plastic molded products.
By understanding and implementing the right strategies, manufacturers can enhance product performance and durability.
The choice of material, design considerations, and the selection of appropriate molding techniques all play a significant role in achieving the desired outcomes.
Through careful planning and optimization, it is possible to produce durable, reliable plastic products that meet the needs of various applications.
資料ダウンロード
QCD調達購買管理クラウド「newji」は、調達購買部門で必要なQCD管理全てを備えた、現場特化型兼クラウド型の今世紀最高の購買管理システムとなります。
ユーザー登録
調達購買業務の効率化だけでなく、システムを導入することで、コスト削減や製品・資材のステータス可視化のほか、属人化していた購買情報の共有化による内部不正防止や統制にも役立ちます。
NEWJI DX
製造業に特化したデジタルトランスフォーメーション(DX)の実現を目指す請負開発型のコンサルティングサービスです。AI、iPaaS、および先端の技術を駆使して、製造プロセスの効率化、業務効率化、チームワーク強化、コスト削減、品質向上を実現します。このサービスは、製造業の課題を深く理解し、それに対する最適なデジタルソリューションを提供することで、企業が持続的な成長とイノベーションを達成できるようサポートします。
オンライン講座
製造業、主に購買・調達部門にお勤めの方々に向けた情報を配信しております。
新任の方やベテランの方、管理職を対象とした幅広いコンテンツをご用意しております。
お問い合わせ
コストダウンが利益に直結する術だと理解していても、なかなか前に進めることができない状況。そんな時は、newjiのコストダウン自動化機能で大きく利益貢献しよう!
(Β版非公開)