- お役立ち記事
- How to choose the latest tools for manufacturing to streamline maintenance planning
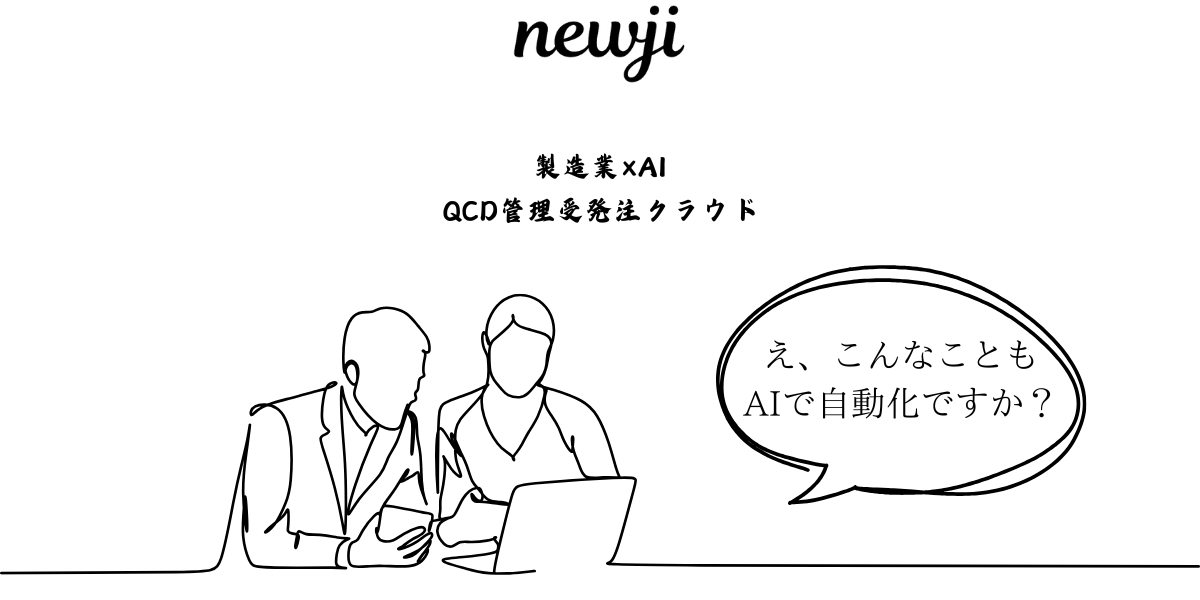
How to choose the latest tools for manufacturing to streamline maintenance planning
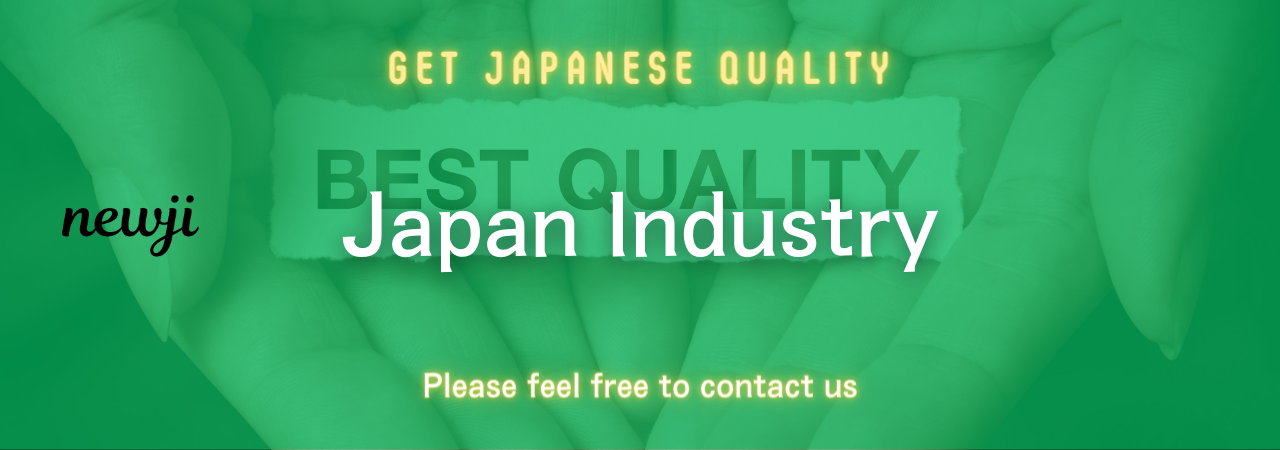
目次
Introduction to Maintenance Planning in Manufacturing
In any manufacturing setting, effective maintenance planning is crucial to ensure smooth operations, minimize downtime, and extend the lifespan of equipment.
A well-structured maintenance plan involves the integration of the latest tools and technologies to streamline processes and improve efficiency.
When it comes to choosing these tools, it is important to understand their implications on workflow and productivity.
In this article, we will explore how to identify and select the latest manufacturing tools for effective maintenance planning.
Understanding Maintenance Planning
Maintenance planning involves organizing and scheduling activities to maintain equipment in optimal condition.
This can range from routine checks and repairs to predictive maintenance, which prevents potential failures before they occur.
A proactive approach to maintenance not only ensures the longevity of machines but also contributes to overall productivity by reducing unexpected downtimes.
Importance of Choosing the Right Tools
Selecting the right tools for maintenance planning is vital for a few reasons:
– It improves efficiency by reducing the time spent on repairs and maintenance activities.
– It enhances the accuracy of predictive maintenance through data analytics and insights.
– It ensures a healthier work environment by reducing risks associated with faulty equipment.
With the ever-evolving landscape of technology, staying updated on the latest manufacturing tools can significantly influence these factors.
Evaluating Your Current Needs
Before diving into new tools, it’s important to evaluate your manufacturing plant’s current needs.
Start by assessing the existing equipment and identifying areas that require improvement.
Consider the following:
– Frequency of equipment breakdowns.
– Average downtime and its impact on production.
– Current maintenance strategies and their effectiveness.
– Budget for new tools and technologies.
This evaluation will provide a clearer picture of what type of tools will be most beneficial.
Types of Tools and Technologies to Consider
There are several categories of tools and technologies that can be considered to enhance maintenance planning:
1. Predictive Maintenance Software
Predictive maintenance software employs sensors and data analytics to monitor equipment performance in real time.
By analyzing data trends, it predicts potential failures and schedules maintenance before a breakdown occurs.
This technology enables manufacturers to reduce unscheduled downtimes significantly.
2. Computerized Maintenance Management Systems (CMMS)
CMMS software is designed to streamline maintenance operations by scheduling tasks, managing work orders, and maintaining a historical database of maintenance activities.
It helps improve resource allocation and ensures that maintenance tasks are executed efficiently and on time.
3. Remote Monitoring Solutions
Remote monitoring tools allow for continuous oversight of equipment performance from a remote location.
This not only increases convenience but also allows for quick identification and resolution of issues, even if they arise off-site.
This can be particularly useful for global enterprises with widespread operations.
4. Internet of Things (IoT) Devices
IoT devices are used to collect and exchange data with other devices and systems over the internet.
By implementing IoT in manufacturing, businesses can gain insights into equipment performance and health.
This aids in enhancing predictive maintenance strategies and improving overall operational efficiency.
5. Augmented Reality (AR)
AR technology can be applied in maintenance by overlaying digital information in a real-world environment.
It supports technicians during repairs and inspections by providing interactive instructions, reducing the likelihood of human error.
Factors to Consider When Choosing Tools
When choosing tools for maintenance planning, consider the following factors:
Compatibility
Ensure that the selected tool integrates seamlessly with your existing systems and processes.
This reduces the learning curve and avoids operational disruptions.
Scalability
The tool should accommodate your current needs as well as future growth.
Choose solutions that can be scaled to match increased demand or changes in operational scale.
Cost Effectiveness
Evaluate the costs involved in procuring and implementing the tool against the potential return on investment.
Consider long-term savings that a tool might provide in terms of reduced downtime and maintenance costs.
User-Friendliness
A tool should be intuitive and easy to use, which facilitates quick adoption by the maintenance team.
Training costs and downtime associated with learning new systems should be minimized.
Implementing the New Tools
Once you have chosen the ideal tools for your manufacturing setup, it’s time to implement them effectively:
– **Training:** Provide comprehensive training to your team on how to use the new tools efficiently.
– **Integration:** Carefully plan the integration process to ensure minimal disruption to existing operations.
– **Monitoring:** Continuously monitor the performance of the new tools and gather feedback from users to make necessary adjustments.
– **Review and Adjust:** Regularly review the performance of the tools against your initial goals to determine their effectiveness and make any needed changes.
Conclusion
In conclusion, the right tools for maintenance planning can transform manufacturing operations by improving efficiency and reducing downtime.
By understanding the specific needs of your facility and evaluating the available technologies against key factors, you can make informed decisions to choose the most suitable tools.
As a result, your maintenance operations will become more proactive, leading to increased productivity and cost savings in the long run.
Stay updated with technological advancements to ensure that your manufacturing plant remains at the frontline of innovation.
資料ダウンロード
QCD調達購買管理クラウド「newji」は、調達購買部門で必要なQCD管理全てを備えた、現場特化型兼クラウド型の今世紀最高の購買管理システムとなります。
ユーザー登録
調達購買業務の効率化だけでなく、システムを導入することで、コスト削減や製品・資材のステータス可視化のほか、属人化していた購買情報の共有化による内部不正防止や統制にも役立ちます。
NEWJI DX
製造業に特化したデジタルトランスフォーメーション(DX)の実現を目指す請負開発型のコンサルティングサービスです。AI、iPaaS、および先端の技術を駆使して、製造プロセスの効率化、業務効率化、チームワーク強化、コスト削減、品質向上を実現します。このサービスは、製造業の課題を深く理解し、それに対する最適なデジタルソリューションを提供することで、企業が持続的な成長とイノベーションを達成できるようサポートします。
オンライン講座
製造業、主に購買・調達部門にお勤めの方々に向けた情報を配信しております。
新任の方やベテランの方、管理職を対象とした幅広いコンテンツをご用意しております。
お問い合わせ
コストダウンが利益に直結する術だと理解していても、なかなか前に進めることができない状況。そんな時は、newjiのコストダウン自動化機能で大きく利益貢献しよう!
(Β版非公開)