- お役立ち記事
- Basics and key points of FMEA/FTA and application to prevent troubles and prevent recurrence by practicing design reviews
月間77,185名の
製造業ご担当者様が閲覧しています*
*2025年2月28日現在のGoogle Analyticsのデータより
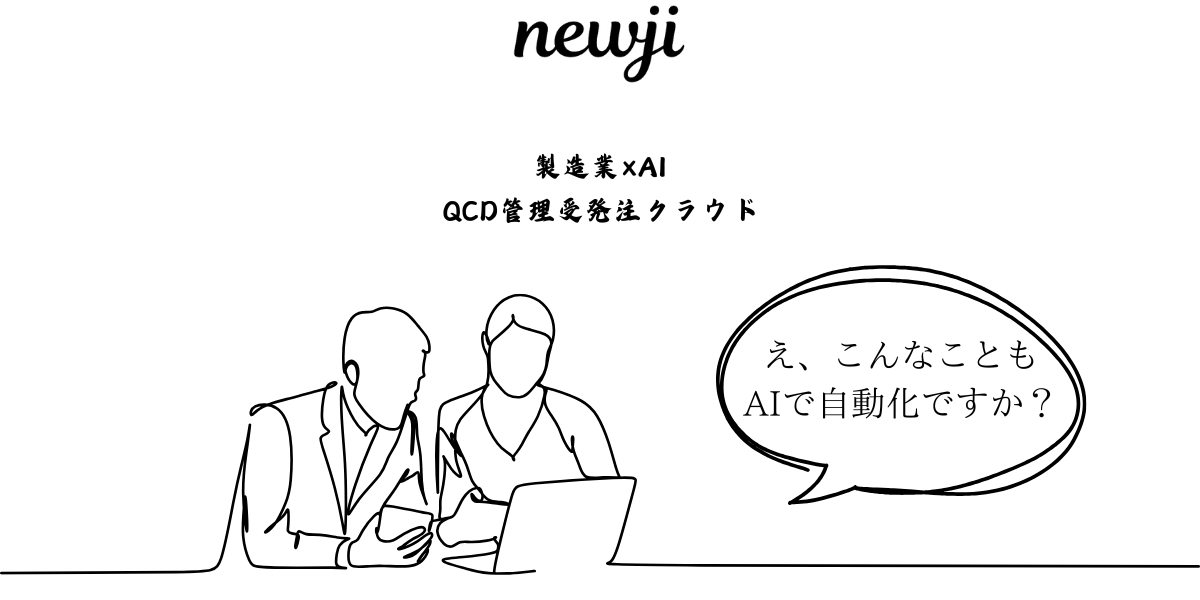
Basics and key points of FMEA/FTA and application to prevent troubles and prevent recurrence by practicing design reviews
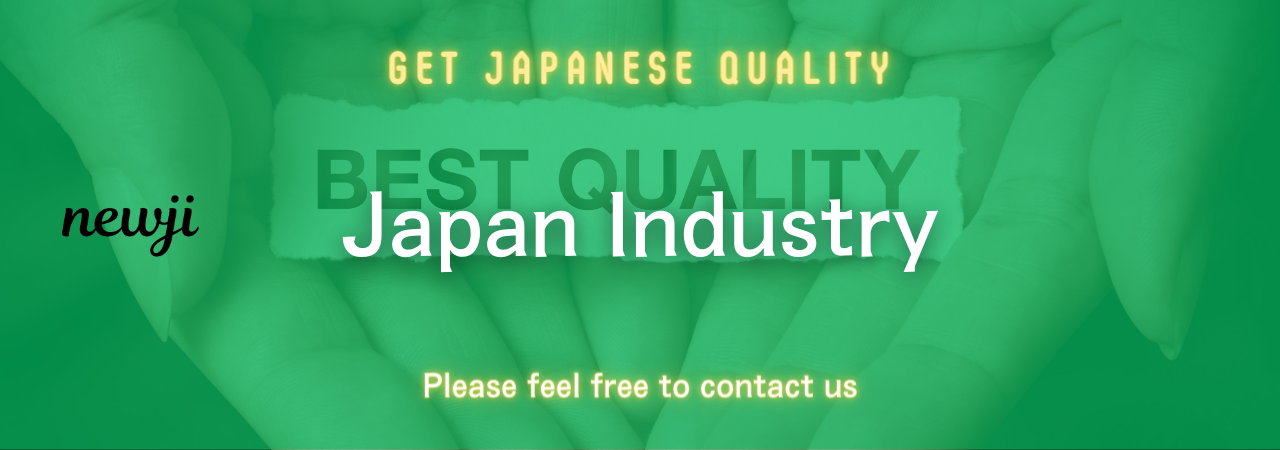
目次
Understanding the Basics of FMEA and FTA
Failure Modes and Effects Analysis (FMEA) and Fault Tree Analysis (FTA) are systematic methodologies used to identify potential failure points and assess risks in processes and systems.
FMEA is a step-by-step approach for identifying all possible failures in a design, manufacturing or assembly process, or product or service.
It helps engineers pinpoint points of potential failure before they occur, allowing for proactive measures to prevent them.
In contrast, FTA is a top-down, deductive failure analysis that starts with an undesirable event (failure) and then works backward to find the root causes.
Both methods are crucial for maintaining high standards of quality and reliability in manufacturing and other engineering applications.
The Importance of FMEA in Design Reviews
Design reviews play a critical role in ensuring that products meet their intended functions without unexpected failures.
Integrating FMEA into design reviews helps teams anticipate and mitigate risks early in the product development lifecycle.
By systematically evaluating each component or process, potential failure modes can be identified and addressed.
This approach not only reduces the likelihood of expensive redesigns but also secures product reliability.
Furthermore, FMEA fosters communication among cross-functional teams, ensuring that all stakeholders understand potential risks and their responsibilities in mitigating them.
Key Steps in Conducting an FMEA
To effectively implement FMEA, follow these key steps:
1. **Identify the scope:** Define the system, process or product to be analyzed.
2. **Gather a multidisciplinary team:** Involve experts from various fields to provide comprehensive insights.
3. **List potential failure modes:** Identify every conceivable way each component could fail.
4. **Determine effects of failures:** Evaluate the consequences of each failure on the system’s performance.
5. **Prioritize potential risks:** Use a risk priority number (RPN) to rank risks based on their severity, occurrence, and detectability.
6. **Identify corrective actions:** Plan measures to reduce or eliminate the high-priority risks.
7. **Implement and review actions:** Execute the corrective actions and periodically review the process to ensure effectiveness.
Exploring Fault Tree Analysis (FTA)
FTA complements FMEA by providing a visual representation of the paths that lead to a system failure.
It breaks down complex systems into simpler events, allowing engineers to trace the causes of a problem back to their origin.
The FTA begins with defining the top event, which is the failure or undesirable event.
From there, a diagram is constructed using AND/OR logic gates to map out the various pathways that could lead to this top event.
Benefits of Integrating FTA in Design Reviews
By incorporating FTA in design reviews, teams gain a clearer understanding of potential failure scenarios and their interdependencies.
This method highlights critical paths and systemic weaknesses that might not be evident in an FMEA.
Additionally, FTA aids in identifying not just what might fail, but how and why it could fail, offering a more robust design verification process.
Through this detailed logical analysis, FTA helps prevent defects, ensuring higher safety and reliability standards in the final product.
Steps for Effective FTA Implementation
To leverage the benefits of FTA, teams should follow these steps:
1. **Define the top event:** Clearly state the primary failure that needs to be avoided.
2. **Develop the fault tree:** Use logical symbols to create a tree that maps out all possible failure causes leading to the top event.
3. **Analyze the fault tree:** Assess each branch’s likelihood and criticality using quantitative or qualitative measures.
4. **Propose solutions:** Identify interventions to minimize or eliminate critical failure paths.
5. **Perform follow-up analysis:** Regular reviews and updates to the fault tree ensure ongoing product integrity and adaptation to any changes in the system.
Applying FMEA and FTA to Prevent Troubles
Proactively applying both FMEA and FTA can effectively prevent unexpected failures and troubleshoot issues as they arise.
When used together, FMEA and FTA provide a comprehensive approach to risk management and quality assurance.
These methodologies are not just about identifying and fixing what’s broken but are also about building safer, more reliable systems from the ground up.
They guide engineers and decision makers in crafting robust designs that are resistant to failure modes and fault causes.
Preventing Recurrence Using FMEA and FTA
Once failures are identified and addressed using FMEA and FTA, it is crucial to ensure they do not recur.
This involves documenting all findings and resolutions, which creates a valuable knowledge base for future projects.
A well-maintained record of past FMEA and FTA analyses can serve to inform new designs and processes, creating a feedback loop of continuous improvement.
This iterative process not only safeguards against repeating past mistakes but also fosters a culture of ongoing vigilance and refinement.
Conclusion
FMEA and FTA are fundamental tools in engineering and manufacturing sectors, helping prevent problems before they occur and ensuring that once identified, they do not recur.
By integrating these techniques into design reviews, organizations can maintain high standards of product reliability and safety.
Understanding and applying the basics and key points of these methodologies is essential for engineers and project managers focused on achieving excellence in their work processes.
Proactively practicing design reviews with FMEA and FTA ensures robust designs and systems, minimizing the risks associated with product failures.
資料ダウンロード
QCD管理受発注クラウド「newji」は、受発注部門で必要なQCD管理全てを備えた、現場特化型兼クラウド型の今世紀最高の受発注管理システムとなります。
ユーザー登録
受発注業務の効率化だけでなく、システムを導入することで、コスト削減や製品・資材のステータス可視化のほか、属人化していた受発注情報の共有化による内部不正防止や統制にも役立ちます。
NEWJI DX
製造業に特化したデジタルトランスフォーメーション(DX)の実現を目指す請負開発型のコンサルティングサービスです。AI、iPaaS、および先端の技術を駆使して、製造プロセスの効率化、業務効率化、チームワーク強化、コスト削減、品質向上を実現します。このサービスは、製造業の課題を深く理解し、それに対する最適なデジタルソリューションを提供することで、企業が持続的な成長とイノベーションを達成できるようサポートします。
製造業ニュース解説
製造業、主に購買・調達部門にお勤めの方々に向けた情報を配信しております。
新任の方やベテランの方、管理職を対象とした幅広いコンテンツをご用意しております。
お問い合わせ
コストダウンが利益に直結する術だと理解していても、なかなか前に進めることができない状況。そんな時は、newjiのコストダウン自動化機能で大きく利益貢献しよう!
(β版非公開)