- お役立ち記事
- Basics of productization flow to prevent problems, specifications, cost management, and points for mass production
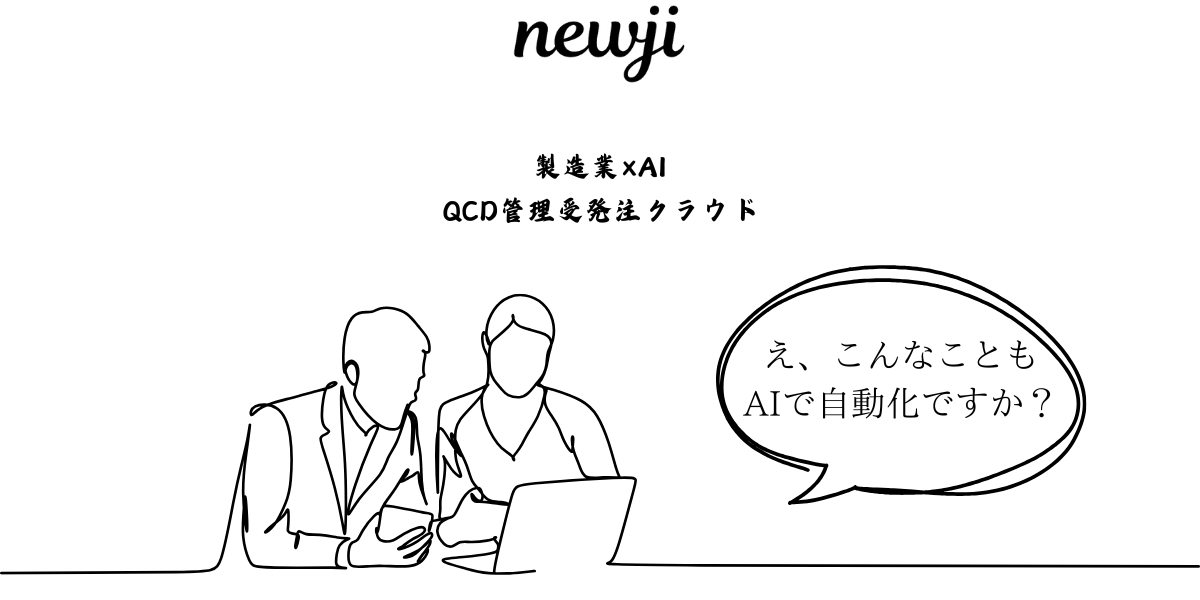
Basics of productization flow to prevent problems, specifications, cost management, and points for mass production
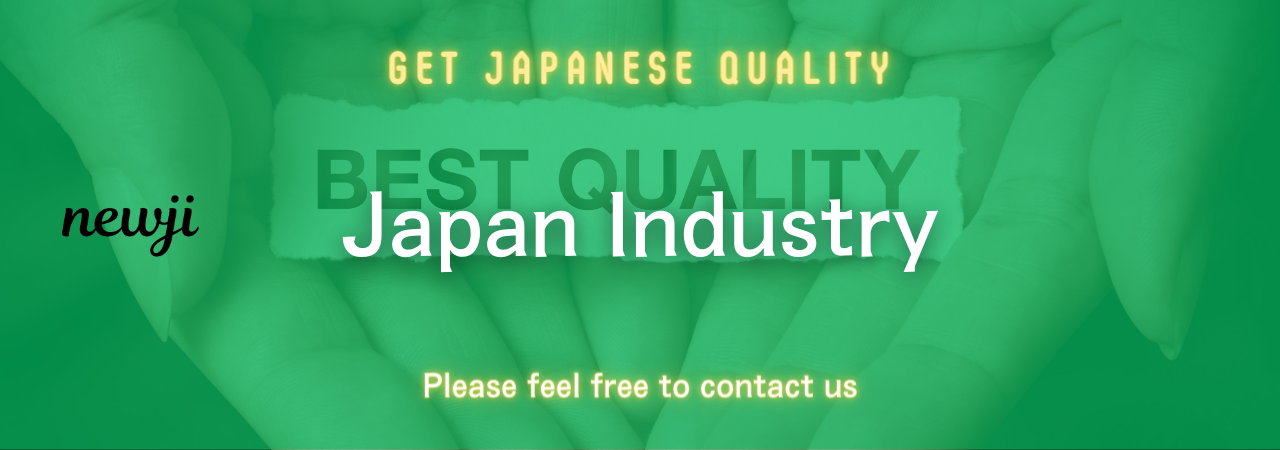
目次
Understanding the Basics of Productization
Productization is a critical process in transforming an idea or prototype into a commercially viable product.
It involves several stages, including developing product specifications, managing costs, and preparing for mass production.
The primary goal is to ensure that the product meets market needs without exceeding budgetary constraints.
To prevent potential issues, it is essential to have a structured approach that guides the product from concept to market.
Steps in the Productization Flow
The productization flow is a series of steps designed to refine a product for market readiness.
Understanding these steps can help prevent common problems and ensure a smoother transition from idea to marketplace.
Here is an overview of the essential stages:
1. Conceptualization and Research
The first step in any productization process is conceptualization.
This involves brainstorming ideas and conducting market research to identify needs and opportunities.
During this phase, the focus is on understanding the target audience and the problems the product intends to solve.
Market research provides insights into customer preferences, competitive products, and potential hurdles.
This information helps in defining the product’s unique value proposition and setting the stage for the next steps.
2. Designing Product Specifications
Once a clear idea is in place, the next step is to develop detailed product specifications.
This involves creating a blueprint that outlines the product’s features, dimensions, materials, and performance criteria.
The goal is to ensure that everyone involved has a clear understanding of what the final product will be.
Product specifications serve as a guide for designers, engineers, and manufacturers.
Clear and detailed specs can prevent miscommunication and errors later in the process.
3. Prototyping and Testing
Prototyping is the process of creating a working model of the product.
This step allows for testing and refinement before full-scale production begins.
Prototypes provide an opportunity to identify design flaws, test functionality, and gather user feedback.
Testing is critical in ensuring the product meets both functional and safety standards.
It is during this phase that necessary adjustments can be made to improve quality and performance.
4. Cost Management and Budgeting
Managing costs is a crucial part of productization.
It involves estimating production costs, setting a budget, and ensuring that every phase of development stays within financial constraints.
Effective cost management requires a thorough understanding of materials, labor, and manufacturing processes.
By setting realistic budgets and monitoring expenditures, businesses can prevent overspending and maintain profitability.
5. Preparing for Mass Production
Preparation for mass production is the final step before launching a product to market.
It involves ensuring that all systems and processes are in place to produce the product at scale.
Consideration must be given to manufacturing capabilities, supply chain logistics, and quality control measures.
Proper planning in this stage ensures a smooth transition into full-scale production and helps maintain the standard of quality.
Preventing Problems in the Productization Process
Even with a robust productization process, challenges can arise.
Here are some strategies to help prevent common problems:
1. Clear Communication
Maintaining clear and consistent communication among team members is key to a successful productization process.
Regular updates and meetings can help ensure everyone is on the same page and can address issues promptly.
2. Iterative Testing
Continuously testing the product throughout development can highlight potential problems early.
Iterative testing allows teams to make adjustments before significant resources are invested in mass production.
3. Risk Analysis
Conducting risk analysis helps identify potential issues that could impact the product’s success.
This process involves evaluating technical, financial, and market-related risks, and developing strategies to mitigate them.
4. Involving Stakeholders
Involving stakeholders, such as investors, partners, and potential customers, provides valuable insights and feedback.
Engaging stakeholders early can align expectations and secure their support.
Points to Consider for Successful Mass Production
Successfully transitioning to mass production requires careful planning and implementation.
Here are points to consider:
1. Quality Assurance
Implementing robust quality assurance measures ensures that the products meet specified standards.
This involves setting clear criteria for performance and reliability and conducting regular inspections.
2. Efficient Supply Chain Management
An efficient supply chain is vital for timely production and delivery.
Ensuring that suppliers are reliable and materials are sourced sustainably can prevent delays and cost overruns.
3. Scalability
The production process should be scalable, accommodating potential increases in demand without compromising quality.
Investing in adaptable manufacturing systems can provide flexibility.
4. Regulatory Compliance
Products must comply with industry standards and regulations to avoid legal issues.
Understanding these requirements early in the process helps incorporate necessary changes without hindering production.
Conclusion
The productization process is complex but essential for bringing a product to market.
By understanding the stages involved, from conceptualization to mass production, businesses can better navigate challenges and capitalize on opportunities.
Focus on clear communication, cost management, iterative testing, and involving stakeholders to enhance success.
With careful planning and execution, the transition from idea to finished product can be smooth and profitable, keeping customer satisfaction and market readiness at the forefront.
資料ダウンロード
QCD調達購買管理クラウド「newji」は、調達購買部門で必要なQCD管理全てを備えた、現場特化型兼クラウド型の今世紀最高の購買管理システムとなります。
ユーザー登録
調達購買業務の効率化だけでなく、システムを導入することで、コスト削減や製品・資材のステータス可視化のほか、属人化していた購買情報の共有化による内部不正防止や統制にも役立ちます。
NEWJI DX
製造業に特化したデジタルトランスフォーメーション(DX)の実現を目指す請負開発型のコンサルティングサービスです。AI、iPaaS、および先端の技術を駆使して、製造プロセスの効率化、業務効率化、チームワーク強化、コスト削減、品質向上を実現します。このサービスは、製造業の課題を深く理解し、それに対する最適なデジタルソリューションを提供することで、企業が持続的な成長とイノベーションを達成できるようサポートします。
オンライン講座
製造業、主に購買・調達部門にお勤めの方々に向けた情報を配信しております。
新任の方やベテランの方、管理職を対象とした幅広いコンテンツをご用意しております。
お問い合わせ
コストダウンが利益に直結する術だと理解していても、なかなか前に進めることができない状況。そんな時は、newjiのコストダウン自動化機能で大きく利益貢献しよう!
(Β版非公開)