- お役立ち記事
- Basics and practice of model-based development (MBD) and PID controller design
月間76,176名の
製造業ご担当者様が閲覧しています*
*2025年3月31日現在のGoogle Analyticsのデータより
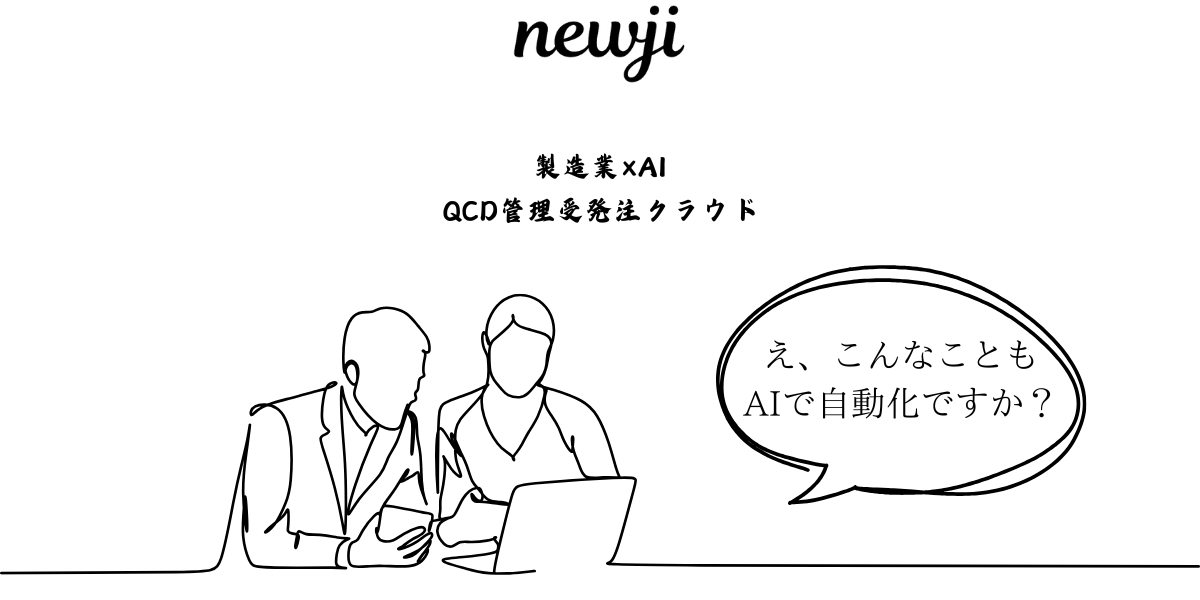
Basics and practice of model-based development (MBD) and PID controller design
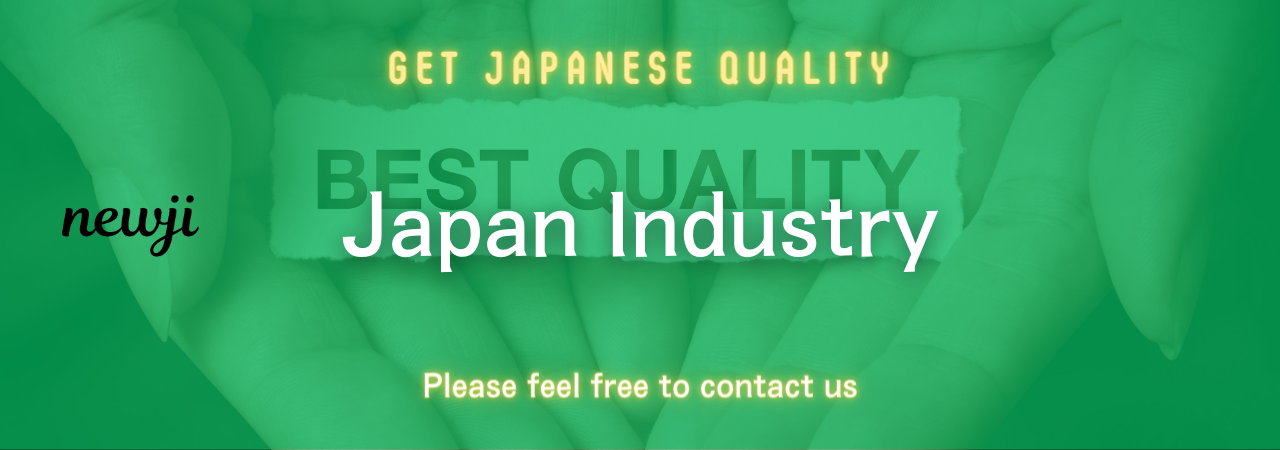
目次
Understanding Model-Based Development (MBD)
Model-Based Development, commonly referred to as MBD, is an approach used in designing and developing complex systems with the help of models.
Instead of traditional trial-and-error methods, MBD relies on simulation and models to validate designs before they are physically created.
The use of MBD in engineering and software development has gained immense popularity due to its efficiency and ability to catch errors early in the design process.
This approach not only saves time but also reduces costs associated with manufacturing flawed products.
Models act as blueprints for developers, offering a visual representation of what the final product should achieve and how it should behave.
By simulating different scenarios and inputs, developers can predict how a design will perform in real-world conditions.
This is particularly useful in industries such as automotive and aerospace, where safety and precision are paramount.
Advantages of Model-Based Development
– **Accuracy**: Instead of guesswork, engineers can use models to explore various scenarios and outcomes.
– **Cost Efficiency**: By catching mistakes early through simulation, the physical prototyping and testing process becomes streamlined, which can lead to significant cost savings.
– **Improved Communication**: Models serve as a common language among teams, allowing for better communication and understanding between different departments.
The Basics of a PID Controller
A PID controller is a crucial component in control systems used to maintain a desired output by correcting errors between a measured process variable and a desired setpoint.
The name PID stands for Proportional, Integral, and Derivative, which are the three fundamental functions of the controller.
– **Proportional Control**: This function produces an output value that is proportional to the current error value.
The proportional gain determines the reaction to the current error, providing immediate adjustments.
– **Integral Control**: This function addresses accumulated errors over time.
It integrates the past errors, ensuring that the controller eliminates the residual steady-state error that the proportional control alone cannot correct.
– **Derivative Control**: This function anticipates future errors based on their rate of change.
It provides a predictive component, which can improve the stability and response time of the controller.
The Importance of PID Controllers
PID controllers are essential in ensuring that systems behave as expected.
They are widely used because of their straightforward implementation and effectiveness in a variety of applications.
For instance, in temperature control systems, a PID controller can maintain the desired temperature by adjusting the heating element.
In motor speed control, it can ensure that the motor operates at the right speed despite changes in load.
Integrating MBD with PID Design
The integration of Model-Based Development with PID controller design leads to more efficient and effective systems.
By using models, engineers can simulate the behavior of a PID controller under various conditions before applying it to the actual system.
Steps in MBD and PID Controller Integration
1. **Model Creation**: The first step is creating a comprehensive model of the system that needs control.
This model should represent all the dynamics and relationships within the system.
2. **Simulate Conditions**: With the model in place, simulate different operating conditions to see how the PID controller would behave.
Adjust the PID parameters accordingly to optimize performance.
3. **Validate the Model**: Validate the model to ensure it accurately reflects real-world conditions.
Various tools can help in this phase, offering insights into how the controller performs in varied scenarios.
4. **Implement and Test**: Once the model is validated, implement the controller into the actual system and conduct real-world testing.
This step ensures that the controller behaves as expected and makes necessary adjustments if needed.
Real-World Applications
The combination of MBD and PID controller design is prevalent in numerous industries.
In automotive design, for instance, MBD with PID controllers helps in designing adaptive cruise control systems.
These systems maintain a safe distance from vehicles ahead by automatically adjusting the car’s speed.
In manufacturing, PID controllers are used to maintain precise conditions such as temperature and pressure to ensure product quality.
The implementation of MBD in this context allows for accurate predictions of how these variables will respond to different conditions.
The Future of MBD and PID Technology
With advancements in technology, both MBD and PID controllers are expected to become more sophisticated.
Artificial Intelligence and machine learning could further enhance the predictive capabilities of models, providing even higher precision and efficiency in designs.
As systems become more complex, the need for reliable and efficient control mechanisms will only increase.
Industries that adopt MBD and PID technologies now will not only improve their current systems but also stay competitive in future markets.
Understanding the basics and practice of model-based development and PID controller design is critical for anyone involved in system engineering.
By leveraging these powerful tools, organizations can improve their design processes and produce high-quality, reliable products.
資料ダウンロード
QCD管理受発注クラウド「newji」は、受発注部門で必要なQCD管理全てを備えた、現場特化型兼クラウド型の今世紀最高の受発注管理システムとなります。
ユーザー登録
受発注業務の効率化だけでなく、システムを導入することで、コスト削減や製品・資材のステータス可視化のほか、属人化していた受発注情報の共有化による内部不正防止や統制にも役立ちます。
NEWJI DX
製造業に特化したデジタルトランスフォーメーション(DX)の実現を目指す請負開発型のコンサルティングサービスです。AI、iPaaS、および先端の技術を駆使して、製造プロセスの効率化、業務効率化、チームワーク強化、コスト削減、品質向上を実現します。このサービスは、製造業の課題を深く理解し、それに対する最適なデジタルソリューションを提供することで、企業が持続的な成長とイノベーションを達成できるようサポートします。
製造業ニュース解説
製造業、主に購買・調達部門にお勤めの方々に向けた情報を配信しております。
新任の方やベテランの方、管理職を対象とした幅広いコンテンツをご用意しております。
お問い合わせ
コストダウンが利益に直結する術だと理解していても、なかなか前に進めることができない状況。そんな時は、newjiのコストダウン自動化機能で大きく利益貢献しよう!
(β版非公開)