- お役立ち記事
- Bearing damage generation mechanism, countermeasures, and application to effective condition monitoring and diagnosis technology
月間77,185名の
製造業ご担当者様が閲覧しています*
*2025年2月28日現在のGoogle Analyticsのデータより
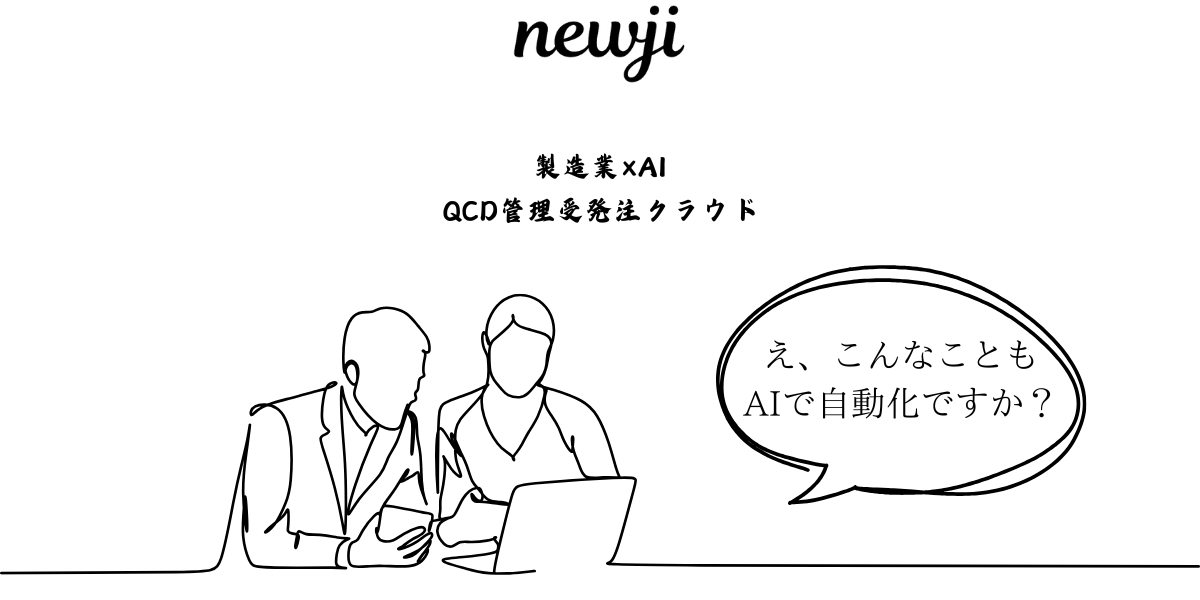
Bearing damage generation mechanism, countermeasures, and application to effective condition monitoring and diagnosis technology
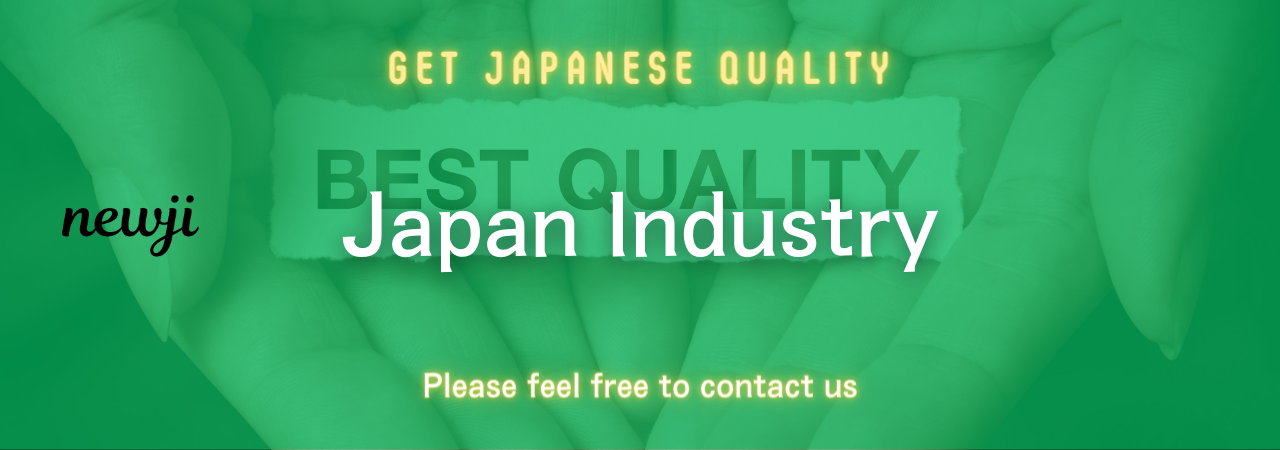
目次
Understanding Bearing Damage
Bearings are critical components in numerous machinery and equipment, providing smooth operation and reducing friction between moving parts.
However, they are prone to damage over time due to various factors.
Understanding the mechanisms that lead to bearing damage is important for preventing machine failures and ensuring efficiency.
Bearing damage typically arises from a few key mechanisms: mechanical wear and tear, inadequate lubrication, contamination, and misalignment.
Let’s delve into each of these causes to better grasp how they can affect the longevity and performance of bearings.
Mechanical Wear and Tear
Mechanical wear and tear occur naturally over time as bearings operate under load.
The repeated stress and strain can cause material fatigue, leading to surface degradation and the formation of small cracks.
Eventually, these cracks can propagate, resulting in spalling, where tiny fragments of material break away from the bearing surface.
This form of damage is exacerbated by excessive loads, improper installation, or operational speeds that exceed the bearing’s specifications.
Inadequate Lubrication
Lubrication plays a crucial role in reducing friction and wear in bearings.
Insufficient or improper lubrication leads to increased friction, causing the bearing surfaces to heat up and degrade.
This can result in abrasive wear, scorch marks, and eventually failure.
Lubrication can be inadequate due to several reasons, including the use of the wrong lubricant, contamination of the lubricant, or simple neglect in maintenance practices.
Contamination
Contaminants such as dirt, dust, moisture, and corrosion-inducing substances can enter the bearing environment.
Once inside, they can cause physical damage to the bearing surfaces or disrupt the efficacy of lubricants.
Contaminants lead to abrasive wear, corrosion, and a host of other issues that significantly reduce bearing life.
Effective sealing and regular maintenance are essential in preventing contamination-related damage.
Misalignment
Misalignment occurs when the bearing and the shaft it supports are not properly aligned.
This misfit can lead to uneven stress distribution across the bearing, causing abnormal wear patterns.
Such misalignment stresses the bearing components excessively, increasing the likelihood of surface damage and premature failure.
Proper installation and alignment verification are critical steps in averting this type of damage.
Countermeasures for Bearing Damage
Preventing bearing damage is essential for prolonging equipment life and minimizing downtime.
Implementing effective countermeasures can mitigate the risks associated with the primary damage mechanisms.
Regular Maintenance
Routine maintenance checks are vital in safeguarding bearings against damage.
During maintenance, it’s crucial to verify the state of lubrication, check for contamination, and ensure proper alignment.
Replacing worn-out parts and keeping track of operational parameters can prevent minor issues from escalating into major problems.
Proper Lubrication Practices
Selecting the right lubricant specific to the operational conditions of the machinery is essential.
Regularly checking and replenishing lubrication levels helps maintain an effective barrier between the contact surfaces.
Moreover, using advanced lubrication systems that monitor lubricant quality and dispense it optimally can maximize bearing performance and lifespan.
Effective Sealing
Installing high-quality seals can significantly reduce the risk of contamination.
Seals prevent external particles and moisture from entering the bearing, thereby maintaining a clean and efficient operational environment.
Regular inspection and replacement of seals, when necessary, are important to keep them functioning effectively.
Accurate Alignment
Proper installation techniques and precise alignment are fundamental to preventing load imbalances.
Using alignment tools and following manufacturer guidelines ensures that bearings and shafts interact correctly.
This minimizes stress on the bearings and helps distribute loads evenly, which is crucial for extending their operational life.
Condition Monitoring and Diagnosis Technology
Condition monitoring and diagnosis technologies have revolutionized the way we maintain and manage bearing health.
These cutting-edge approaches not only help detect early signs of bearing damage but also provide insights into the operational conditions of machinery.
Vibration Analysis
Vibration analysis is a widely used technique to assess bearing condition.
By measuring and analyzing the vibrational patterns of a machine, it is possible to detect abnormalities indicative of wear, misalignment, or imbalance.
This method enables early intervention before minor issues develop into catastrophic failures.
Thermal Imaging
Thermal imaging is used to monitor the heat generated by bearings and surrounding components.
Abnormally high temperatures can signal lubrication issues or increased friction, serving as an early warning for potential problems.
Thermal cameras and sensors provide a non-intrusive way to keep track of equipment condition.
Acoustic Emission Monitoring
This advanced technique involves capturing high-frequency sound waves emitted by the machinery.
Acoustic emissions can reveal defects like crack initiation or abrasive wear in bearings, providing real-time insights into component health.
This real-time data helps identify issues that might not be detectable through traditional monitoring.
Internet of Things (IoT) Integration
IoT technology enhances condition monitoring by allowing sensors and devices to communicate data over the internet.
This connectivity provides a comprehensive view of bearing health by collecting and analyzing data across various parameters.
Real-time alerts and data-driven insights enable predictive maintenance, reducing unexpected breakdowns.
As we continue to adopt these technologies, our capability to monitor and manage bearing health becomes increasingly sophisticated.
The integration of advanced monitoring techniques with traditional preventive measures ensures the longevity and reliability of bearings, critical to the efficient operation of machinery across industries.
This holistic approach not only mitigates risks but also enhances productivity and reduces maintenance costs.
資料ダウンロード
QCD管理受発注クラウド「newji」は、受発注部門で必要なQCD管理全てを備えた、現場特化型兼クラウド型の今世紀最高の受発注管理システムとなります。
ユーザー登録
受発注業務の効率化だけでなく、システムを導入することで、コスト削減や製品・資材のステータス可視化のほか、属人化していた受発注情報の共有化による内部不正防止や統制にも役立ちます。
NEWJI DX
製造業に特化したデジタルトランスフォーメーション(DX)の実現を目指す請負開発型のコンサルティングサービスです。AI、iPaaS、および先端の技術を駆使して、製造プロセスの効率化、業務効率化、チームワーク強化、コスト削減、品質向上を実現します。このサービスは、製造業の課題を深く理解し、それに対する最適なデジタルソリューションを提供することで、企業が持続的な成長とイノベーションを達成できるようサポートします。
製造業ニュース解説
製造業、主に購買・調達部門にお勤めの方々に向けた情報を配信しております。
新任の方やベテランの方、管理職を対象とした幅広いコンテンツをご用意しております。
お問い合わせ
コストダウンが利益に直結する術だと理解していても、なかなか前に進めることができない状況。そんな時は、newjiのコストダウン自動化機能で大きく利益貢献しよう!
(β版非公開)