- お役立ち記事
- Basics and principles of injection molding
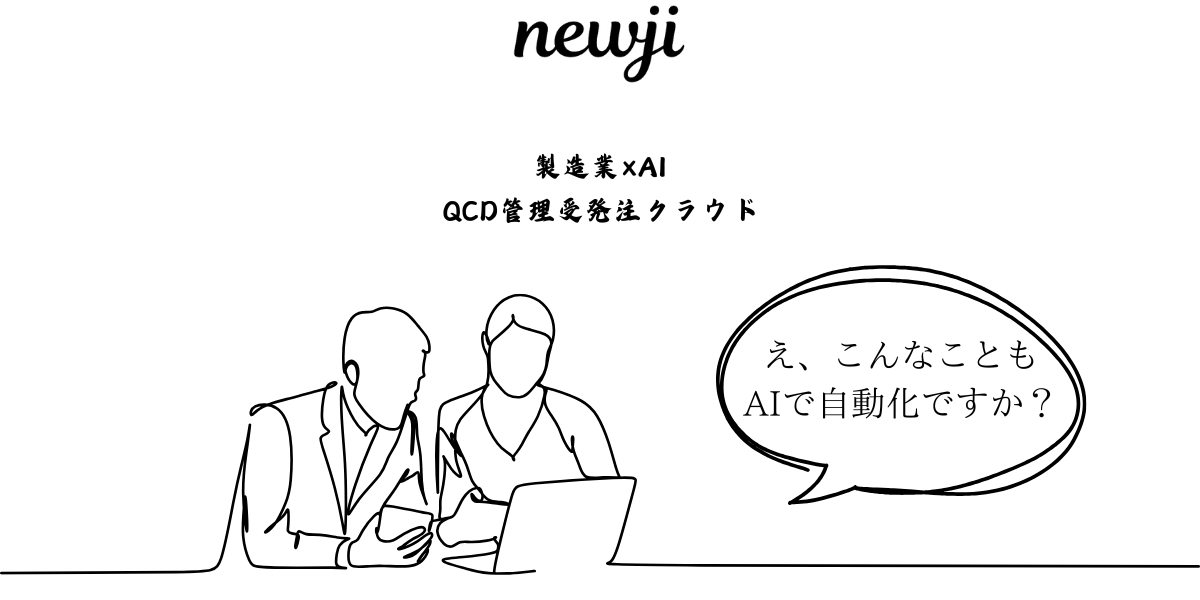
Basics and principles of injection molding
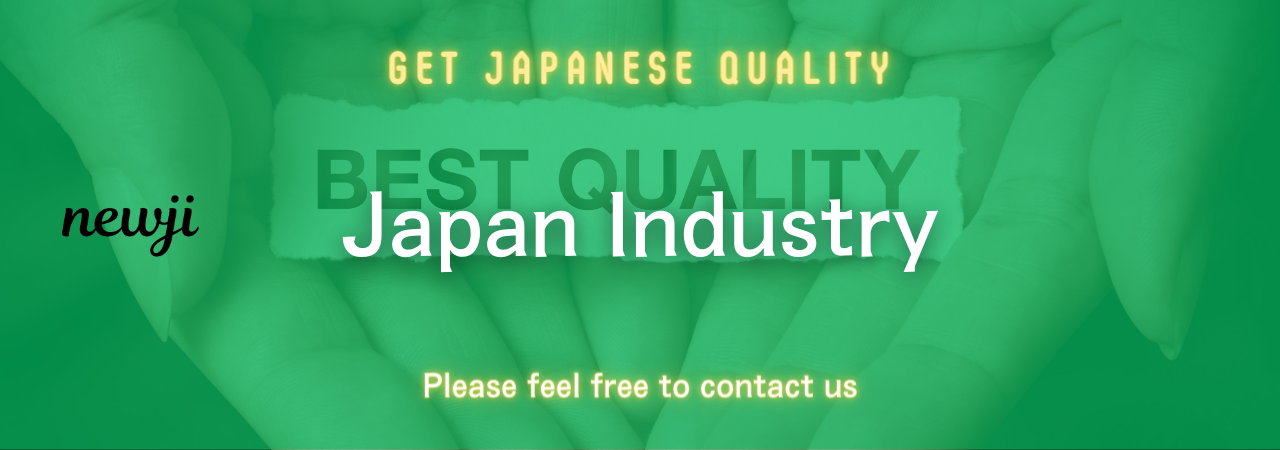
目次
Understanding Injection Molding
Injection molding is a manufacturing process used to create products by injecting molten material into a mold.
The process is highly versatile and can be used to produce a variety of items, from small components to large vehicle parts.
Injection molding is an essential method in modern manufacturing, particularly in producing plastic products.
The Injection Molding Process
Injection molding begins with the design of a mold specific to the product intended for creation.
The mold is usually made from metal like steel or aluminum and consists of cavities that define the shape of the final product.
Once the mold is ready, the material, typically a plastic polymer, is heated until molten.
The molten material is then injected into the mold under high pressure.
This injection ensures that the material fills every cavity of the mold.
Once filled, the material cools and solidifies into the shape of the mold.
After cooling, the mold opens, and the newly created part is ejected.
This cycle repeats with the next injection, making the process fast and efficient for mass production.
Key Components of Injection Molding Machines
The injection molding machine plays a critical role in the process.
Understanding its components is essential for grasping how the process works.
Injection Unit
The injection unit is responsible for melting and injecting the material into the mold.
It typically consists of a hopper, barrel, and nozzle.
The hopper holds the plastic granules that feed into the barrel.
The barrel, equipped with a screw, heats the plastic and mixes it uniformly.
The nozzle at the end of the barrel injects the molten plastic into the mold.
Clamping Unit
The clamping unit holds the mold together during the injection process and opens it to eject the finished product.
It consists of a platen, mold halves, and a clamp mechanism.
The platen supports the mold and maintains its alignment.
The clamp mechanism applies force to keep the mold halves together during injection.
The Control System
Modern injection molding machines are equipped with advanced control systems.
These systems manage the machine’s temperature, pressure, and cycle time.
The control system ensures precision and consistency in the production process.
Operators use the system to adjust parameters based on the material and mold used.
Materials Used in Injection Molding
A wide variety of materials can be used in injection molding.
The choice of material depends on the product’s intended application and desired properties.
Thermoplastics
Thermoplastics are the most common materials used in injection molding.
They can be melted and reshaped multiple times, making them ideal for the process.
Popular thermoplastic materials include polyethylene, polypropylene, and ABS.
These materials are known for their strength, durability, and flexibility.
Thermosetting Plastics
Thermosetting plastics are another option for injection molding.
Once cured, these plastics cannot be remelted, providing high thermal and chemical resistance.
Materials like phenolics and epoxy resins fall under this category.
They are used in applications requiring high heat and chemical resistance.
Elastomers
Elastomers offer flexibility and resilience and are used in applications where rubber-like properties are needed.
Silicone is a common elastomer used in injection molding.
Advantages of Injection Molding
Injection molding offers several benefits, making it a preferred method for many manufacturers.
Cost Efficiency
The process allows for high-volume production at a low cost per unit.
Once the initial investment in the mold is made, production costs decrease significantly with volume.
Consistency and Precision
Injection molding produces parts with precise dimensions and high repeatability.
The process minimizes material waste and ensures uniformity across products.
Design Flexibility
The method provides immense design flexibility, allowing for complex shapes and intricate details.
Injection molding can create products with fine features that other processes might struggle to reproduce.
Challenges in Injection Molding
Despite its advantages, injection molding has challenges that manufacturers must address.
Mold Design
Creating a mold requires careful planning and precision.
Any error in the mold design can lead to defects in the finished product, making mold design a critical component.
Material Selection
Choosing the right material is crucial for the product’s functionality and quality.
Considerations include the material’s mechanical properties, cost, and processing characteristics.
Processing Parameters
Controlling the temperature, pressure, and cooling time is essential for producing quality parts.
Mismanagement can result in defects, such as warping or incomplete filling.
Conclusion
Injection molding is a fascinating and complex process essential to modern manufacturing.
From simple toys to intricate automotive parts, products we encounter daily are made using this technology.
By understanding the basic principles and components involved, one can appreciate the precision and efficiency of this manufacturing method.
Though challenges exist, the advantages of injection molding make it a vital technology for creating diverse, high-quality products.
資料ダウンロード
QCD調達購買管理クラウド「newji」は、調達購買部門で必要なQCD管理全てを備えた、現場特化型兼クラウド型の今世紀最高の購買管理システムとなります。
ユーザー登録
調達購買業務の効率化だけでなく、システムを導入することで、コスト削減や製品・資材のステータス可視化のほか、属人化していた購買情報の共有化による内部不正防止や統制にも役立ちます。
NEWJI DX
製造業に特化したデジタルトランスフォーメーション(DX)の実現を目指す請負開発型のコンサルティングサービスです。AI、iPaaS、および先端の技術を駆使して、製造プロセスの効率化、業務効率化、チームワーク強化、コスト削減、品質向上を実現します。このサービスは、製造業の課題を深く理解し、それに対する最適なデジタルソリューションを提供することで、企業が持続的な成長とイノベーションを達成できるようサポートします。
オンライン講座
製造業、主に購買・調達部門にお勤めの方々に向けた情報を配信しております。
新任の方やベテランの方、管理職を対象とした幅広いコンテンツをご用意しております。
お問い合わせ
コストダウンが利益に直結する術だと理解していても、なかなか前に進めることができない状況。そんな時は、newjiのコストダウン自動化機能で大きく利益貢献しよう!
(Β版非公開)