- お役立ち記事
- Revolutionizing Japanese Manufacturing: How CC-Link Transforms Industrial Automation Systems
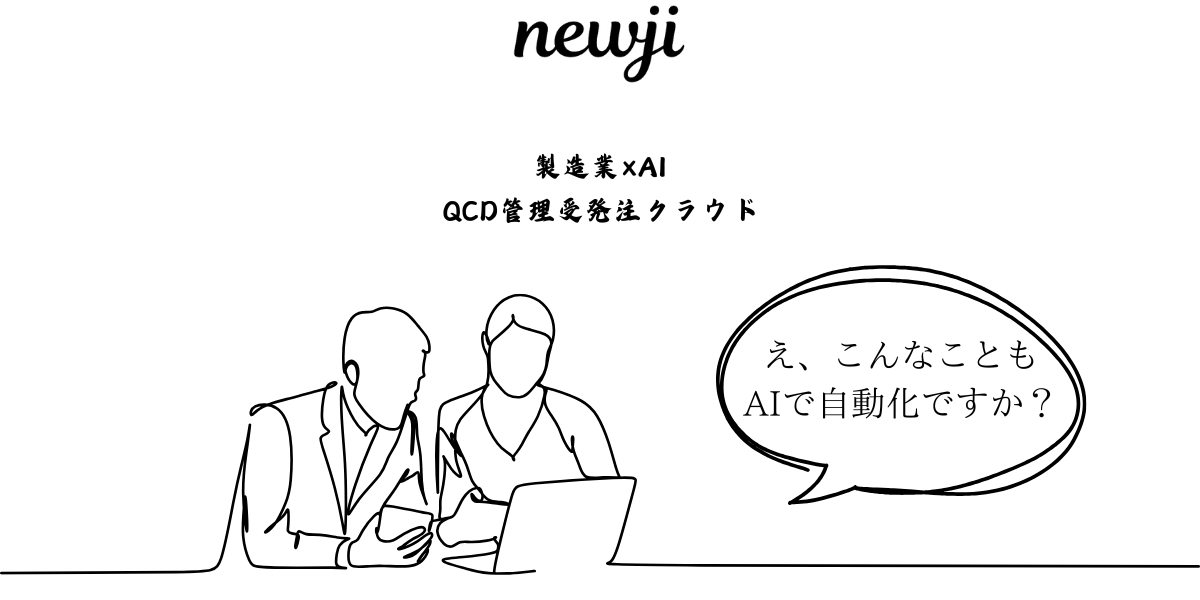
Revolutionizing Japanese Manufacturing: How CC-Link Transforms Industrial Automation Systems
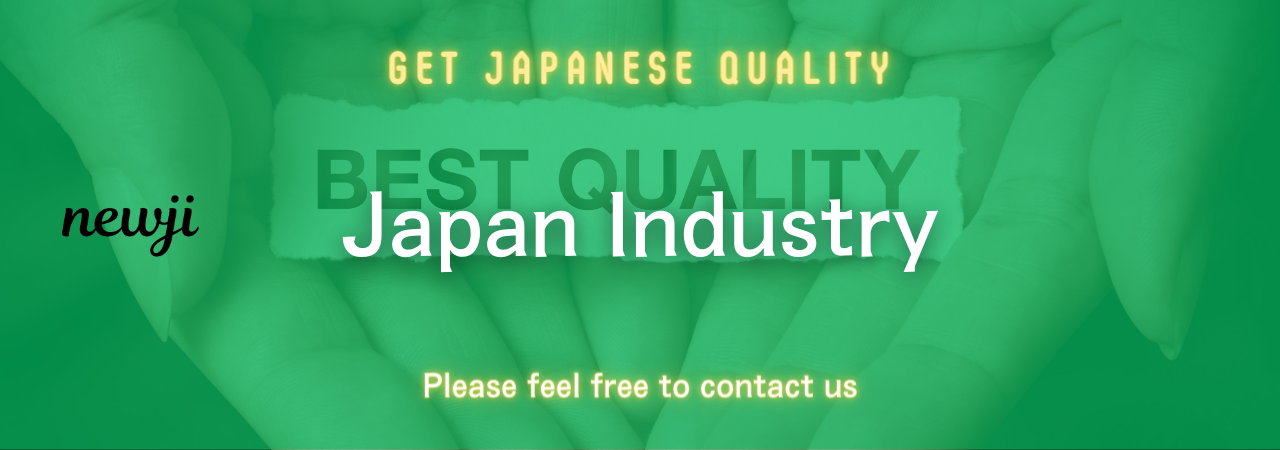
目次
Introduction to CC-Link in Japanese Manufacturing
Japanese manufacturing has long been synonymous with precision, efficiency, and innovation. Central to this reputation is the integration of advanced industrial automation systems that streamline production processes and enhance product quality. Among the various technologies driving this transformation, CC-Link stands out as a pivotal communication protocol that revolutionizes industrial automation. This article explores how CC-Link is reshaping Japanese manufacturing, its advantages and disadvantages, strategic supplier negotiation techniques, current market conditions, and best practices for implementation.
Understanding CC-Link: An Overview
CC-Link, short for Control & Communication Link, is an open network protocol designed for real-time communication between machines in industrial automation systems. Developed by Mitsubishi Electric in the early 1990s, CC-Link has evolved to become a cornerstone in factories seeking high-speed, reliable, and scalable communication solutions.
The Evolution of CC-Link
Initially conceived to address the limitations of existing proprietary networks, CC-Link has undergone significant advancements to meet the growing demands of modern manufacturing. The introduction of CC-Link IE (Industrial Ethernet) expanded its capabilities, allowing for higher data transfer rates and greater integration with IT systems.
Key Features of CC-Link
– **Real-Time Communication:** CC-Link ensures timely data exchange between devices, crucial for synchronized operations.
– **High-Speed Data Transfer:** Facilitates rapid communication, reducing latency and enhancing overall system performance.
– **Scalability:** Supports large networks, making it suitable for both small workshops and expansive manufacturing plants.
– **Interoperability:** Designed to work seamlessly with various devices from different manufacturers, fostering a collaborative industrial ecosystem.
Advantages of Implementing CC-Link in Manufacturing
Adopting CC-Link offers numerous benefits that can significantly enhance manufacturing processes. Below, we delve into the primary advantages that make CC-Link a preferred choice in Japanese manufacturing.
Enhanced Productivity and Efficiency
CC-Link’s high-speed communication minimizes delays between machines, leading to more efficient production lines. Real-time data exchange allows for swift adjustments to processes, reducing downtime and increasing overall productivity.
Improved Quality Control
With precise and timely data, manufacturers can monitor and control production parameters more effectively. This leads to consistent product quality and reduces the incidence of defects, aligning with the stringent quality standards prevalent in Japanese manufacturing.
Cost-Effective Scalability
CC-Link’s scalable architecture allows manufacturers to expand their networks without significant infrastructure changes. This flexibility ensures that as production demands grow, the communication system can adapt without incurring excessive costs.
Interoperability and Flexibility
CC-Link’s ability to integrate devices from various manufacturers fosters a versatile and adaptable manufacturing environment. This interoperability is crucial for manufacturers aiming to incorporate diverse technologies and equipment into their production lines.
Robustness and Reliability
Designed for industrial environments, CC-Link networks are highly reliable and resilient against disruptions. This robustness ensures continuous and uninterrupted operations, which is vital for maintaining production schedules and meeting delivery deadlines.
Disadvantages and Challenges of CC-Link
While CC-Link offers numerous advantages, it is essential to acknowledge the potential drawbacks and challenges associated with its implementation.
Initial Implementation Costs
Setting up a CC-Link network can involve significant initial investment, especially for small to medium-sized enterprises. Costs related to hardware, software, and training personnel can be substantial, posing a barrier to entry for some manufacturers.
Complexity in Integration
Integrating CC-Link with existing systems and machinery may present technical challenges. Ensuring compatibility and seamless communication between diverse devices often requires specialized knowledge and expertise.
Limited Global Adoption
While CC-Link is widely adopted in Japan and certain regions, its global presence is not as extensive as some other industrial communication standards. This limited adoption can restrict the availability of compatible devices and technical support in certain markets.
Dependency on Specific Vendors
Despite being an open protocol, substantial components of the CC-Link ecosystem may rely on specific vendors. This dependency can limit flexibility in choosing equipment and may lead to higher costs due to limited competition.
Supplier Negotiation Techniques for CC-Link Implementation
Successful implementation of CC-Link in manufacturing requires strategic collaboration with suppliers. Effective negotiation techniques can ensure favorable terms, cost savings, and reliable partnerships.
Understanding Supplier Capabilities and Offerings
Before entering negotiations, it is crucial to thoroughly understand the supplier’s product offerings, capabilities, and compatibility with CC-Link. Assessing the technical specifications and support services provided by suppliers ensures alignment with manufacturing requirements.
Leveraging Volume Discounts
Manufacturers planning large-scale implementations can negotiate volume discounts. Suppliers are often willing to offer reduced pricing for bulk purchases, leading to significant cost savings.
Ensuring Comprehensive Support and Training
Negotiating for comprehensive support packages and training services can enhance the implementation process. Suppliers that provide ongoing technical support and training ensure smooth integration and operation of CC-Link systems.
Contract Flexibility and Scalability
Flexible contract terms that allow for scalability can accommodate future growth and changes in manufacturing demands. Negotiating terms that provide scalability options ensures that the communication system can adapt without renegotiating contracts.
Exploring Long-Term Partnerships
Building long-term relationships with suppliers fosters trust and collaboration. Long-term partnerships can lead to preferential pricing, priority support, and exclusive access to new technologies, benefiting both parties.
Market Conditions and Trends Influencing CC-Link Adoption
Understanding the current market conditions and emerging trends is essential for manufacturers considering CC-Link implementation. Several factors influence the adoption and evolution of CC-Link in the industrial automation landscape.
Increasing Demand for Automation
The global push towards automation to enhance productivity and reduce labor costs has accelerated the adoption of communication protocols like CC-Link. Manufacturers are investing in advanced automation systems to remain competitive, driving the demand for robust communication solutions.
Advancements in Industrial Internet of Things (IIoT)
The integration of IIoT with industrial automation systems necessitates reliable and high-speed communication protocols. CC-Link’s capabilities align with IIoT requirements, facilitating the seamless exchange of data between connected devices.
Focus on Energy Efficiency and Sustainability
Manufacturers are increasingly prioritizing energy efficiency and sustainable practices. CC-Link enables precise control and monitoring of machinery, contributing to optimized energy usage and reduced environmental impact.
Technological Innovations and Upgrades
Continuous technological advancements in CC-Link, such as the development of CC-Link IE and CC-Link EZ, keep the protocol relevant and adaptable to evolving industrial needs. These innovations ensure that CC-Link remains a viable option for modern manufacturing systems.
Competitive Landscape
The presence of competing communication protocols, such as EtherCAT, PROFINET, and Modbus, creates a competitive environment. Manufacturers must evaluate the strengths and weaknesses of each protocol to make informed decisions based on their specific requirements.
Best Practices for Implementing CC-Link in Manufacturing
To maximize the benefits of CC-Link, manufacturers should adhere to best practices during implementation. These practices ensure a smooth integration process, optimal performance, and long-term sustainability of the automation system.
Comprehensive Planning and Assessment
Begin with a thorough assessment of current systems and production processes. Identify areas where CC-Link can add the most value and develop a detailed implementation plan that outlines goals, timelines, and resource allocation.
Engage Stakeholders Early
Involve key stakeholders, including engineers, IT personnel, and management, from the outset. Early engagement ensures that all perspectives are considered, and potential challenges are addressed proactively.
Invest in Training and Education
Provide comprehensive training to personnel responsible for managing and maintaining the CC-Link network. Well-trained staff can effectively troubleshoot issues, optimize system performance, and ensure seamless operations.
Collaborate with Experienced Suppliers and Partners
Partner with suppliers and system integrators who have extensive experience with CC-Link. Their expertise can facilitate the implementation process, mitigate risks, and ensure that best practices are followed.
Implement Robust Testing and Quality Assurance
Conduct rigorous testing to verify the functionality and reliability of the CC-Link network. Quality assurance measures help identify and rectify issues before they impact production, ensuring smooth and uninterrupted operations.
Maintain Regular Maintenance and Updates
Establish a maintenance schedule to regularly inspect and update the CC-Link network. Regular maintenance ensures the longevity of the system, prevents unexpected downtime, and incorporates the latest advancements in technology.
Optimize Network Design for Scalability
Design the CC-Link network with scalability in mind. Anticipate future expansion and ensure that the network architecture can accommodate additional devices and increased data traffic without significant modifications.
Case Studies: CC-Link Transformations in Japanese Manufacturing
Examining real-world applications of CC-Link provides valuable insights into its impact on Japanese manufacturing. The following case studies highlight how different industries have leveraged CC-Link to enhance their automation systems.
Automotive Manufacturing
In the automotive sector, precision and efficiency are paramount. A leading Japanese automotive manufacturer integrated CC-Link into its assembly line, linking robotics, conveyor systems, and quality inspection devices. The real-time communication facilitated by CC-Link enabled synchronized operations, reducing assembly time and minimizing defects. As a result, the manufacturer achieved a 15% increase in production efficiency and a significant improvement in product quality.
Electronics Manufacturing
A prominent electronics manufacturer implemented CC-Link IE to connect automated testing equipment and assembly robots. The high-speed data transfer capabilities of CC-Link IE allowed for rapid communication between testing stations and robotic arms, enhancing the speed and accuracy of the manufacturing process. This integration led to a 20% reduction in testing time and improved overall production throughput.
Food and Beverage Industry
In the food and beverage sector, maintaining hygiene and ensuring production consistency are critical. A Japanese food processing company adopted CC-Link to automate its packaging and labeling lines. The robust and reliable CC-Link network ensured seamless communication between packaging machines, conveyors, and quality control systems. This implementation resulted in a 10% increase in packaging speed and ensured consistent labeling accuracy, meeting stringent industry standards.
Future Prospects of CC-Link in Industrial Automation
The future of CC-Link in industrial automation is promising, driven by ongoing technological advancements and the evolving needs of manufacturing. Several trends and developments are set to shape the trajectory of CC-Link in the coming years.
Integration with Advanced Technologies
The integration of CC-Link with emerging technologies such as artificial intelligence (AI), machine learning, and advanced analytics will enhance its capabilities. These integrations will enable predictive maintenance, real-time optimization, and more intelligent decision-making processes within manufacturing systems.
Expansion of CC-Link IE Edge
CC-Link IE Edge, designed for decentralized networking, is expected to see increased adoption. This protocol facilitates communication at the machine and device level, providing greater flexibility and efficiency in managing distributed automation systems.
Enhanced Security Features
As industrial networks become more interconnected, cybersecurity becomes a critical concern. Future developments in CC-Link will focus on enhancing security features to protect against cyber threats, ensuring the integrity and reliability of manufacturing operations.
Global Standardization and Adoption
Efforts to standardize CC-Link on a global scale are likely to enhance its adoption beyond Japan. Increased standardization will promote interoperability, expand the availability of compatible devices, and foster a broader ecosystem of suppliers and partners.
Sustainability and Energy Efficiency
Sustainability will continue to be a driving force in manufacturing. CC-Link’s ability to optimize energy consumption and streamline processes will align with manufacturers’ efforts to reduce their environmental footprint and achieve sustainable growth.
Conclusion
CC-Link has undeniably transformed industrial automation systems in Japanese manufacturing, driving efficiency, quality, and scalability. Its robust communication capabilities, combined with strategic implementation practices, offer manufacturers the tools needed to navigate the complexities of modern production environments. While challenges such as initial implementation costs and integration complexities exist, the advantages and future prospects of CC-Link make it a valuable asset for manufacturers aiming to maintain competitiveness in an ever-evolving market. By adopting best practices, leveraging supplier partnerships, and staying abreast of technological advancements, Japanese manufacturers can continue to harness the full potential of CC-Link, ensuring sustained growth and innovation.
資料ダウンロード
QCD調達購買管理クラウド「newji」は、調達購買部門で必要なQCD管理全てを備えた、現場特化型兼クラウド型の今世紀最高の購買管理システムとなります。
ユーザー登録
調達購買業務の効率化だけでなく、システムを導入することで、コスト削減や製品・資材のステータス可視化のほか、属人化していた購買情報の共有化による内部不正防止や統制にも役立ちます。
NEWJI DX
製造業に特化したデジタルトランスフォーメーション(DX)の実現を目指す請負開発型のコンサルティングサービスです。AI、iPaaS、および先端の技術を駆使して、製造プロセスの効率化、業務効率化、チームワーク強化、コスト削減、品質向上を実現します。このサービスは、製造業の課題を深く理解し、それに対する最適なデジタルソリューションを提供することで、企業が持続的な成長とイノベーションを達成できるようサポートします。
オンライン講座
製造業、主に購買・調達部門にお勤めの方々に向けた情報を配信しております。
新任の方やベテランの方、管理職を対象とした幅広いコンテンツをご用意しております。
お問い合わせ
コストダウンが利益に直結する術だと理解していても、なかなか前に進めることができない状況。そんな時は、newjiのコストダウン自動化機能で大きく利益貢献しよう!
(Β版非公開)