- お役立ち記事
- Basics of FEM analysis using CAE, its key points, and improvement of analysis accuracy
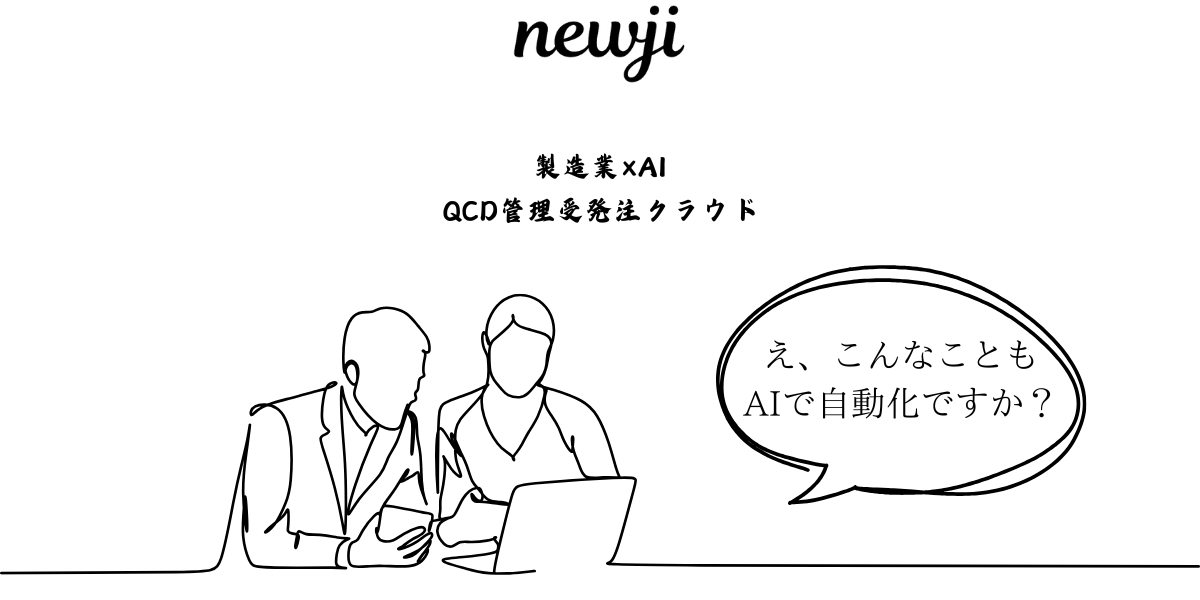
Basics of FEM analysis using CAE, its key points, and improvement of analysis accuracy
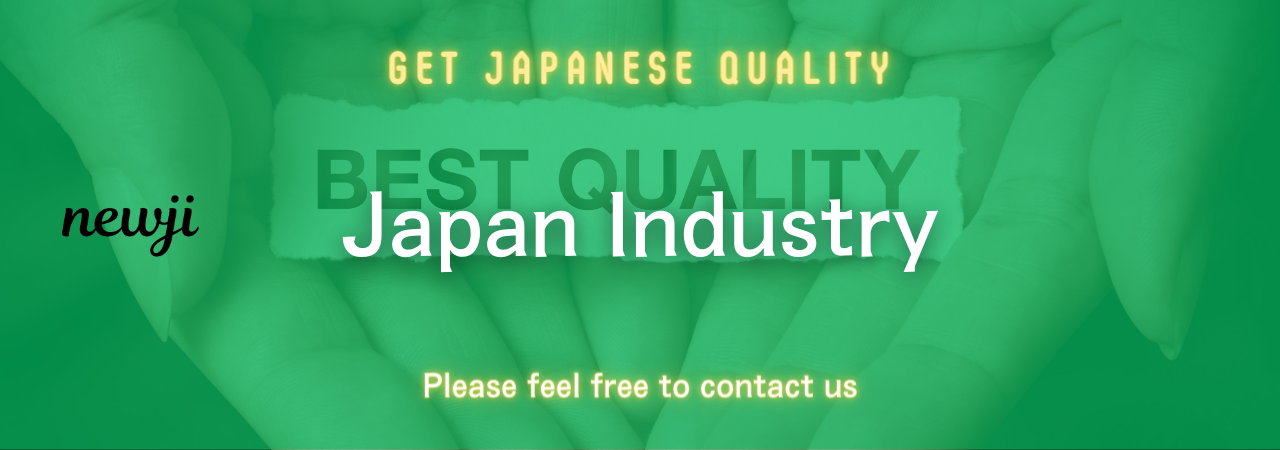
目次
Introduction to FEM Analysis Using CAE
Finite Element Method (FEM) analysis is a crucial tool in the world of computer-aided engineering (CAE).
It allows engineers to simulate physical phenomena using computational models, providing insights into the behavior of materials and designs under various conditions.
Understanding the basics of FEM analysis is essential for improving engineering solutions and ensuring accurate results.
What is FEM Analysis?
FEM is a numerical method used to approximate solutions to complex engineering problems.
It breaks down a large problem into smaller, simpler parts called finite elements.
These elements are connected at points known as nodes, forming a mesh across the entire structure.
The method then solves equations that describe the behavior of each element, giving an overall understanding of how the whole system behaves.
Role of CAE in FEM Analysis
CAE software plays a vital role in FEM analysis by providing tools to create models, apply loads, and analyze results.
These tools streamline the process, making it easier for engineers to conduct complex simulations and test their designs under various scenarios.
By leveraging CAE, engineers can iterate and improve their models efficiently, saving both time and resources.
Key Points in FEM Analysis
When conducting FEM analysis, certain key points must be considered to ensure accurate and meaningful results.
Meshing: The Foundation of FEM Analysis
Meshing is a crucial step in FEM analysis, as it divides the model into finite elements.
A well-defined mesh can significantly impact the accuracy of the results.
Engineers must balance between too coarse a mesh, which may result in inaccurate simulations, and too fine a mesh, which may require excessive computational resources.
Material Properties
Accurate material properties are essential for realistic simulation results.
This includes data such as elasticity, thermal conductivity, and density.
Using inaccurate material data can lead to erroneous conclusions, making it imperative for engineers to have reliable and precise material information.
Boundary Conditions and Load Application
Boundary conditions and load applications define how a system interacts with its environment.
Correctly setting these parameters is critical to simulate real-world conditions accurately.
This includes fixed supports, forces, and thermal loads, among others.
Missteps in this area can skew results, yielding unreliable data for design validation.
Model Validation and Verification
Thorough validation and verification are necessary to ensure that the FEM model behaves as expected.
This involves comparing simulated results with experimental data or analytical solutions when available.
It helps confirm that the model is set up correctly and the analysis is trustworthy.
Improving Analysis Accuracy
Improving the accuracy of FEM analysis involves several strategies to refine and perfect the simulation process.
Refining the Mesh
Improving mesh quality can lead to better analysis outcomes.
Techniques such as adaptive meshing adjust the mesh density based on stress gradients or errors, ensuring a more accurate representation of critical regions without overburdening computational resources.
High-Fidelity Models
High-fidelity models that capture complexities of the real-world system offer more accurate results.
These might include the consideration of nonlinear material behavior, large deformations, or time-dependent phenomena.
Increasing the fidelity of a model often requires more computational power, but it can significantly enhance the accuracy of predictions.
Advanced Solver Techniques
Utilizing advanced solver techniques can improve the accuracy and efficiency of FEM analysis.
Iterative solvers, for example, can handle large-scale problems more effectively than traditional direct solvers.
These techniques make it feasible to solve complex problems with greater precision and reliability.
Ongoing Learning and Development
Staying updated with the latest in FEM analysis technology and methodologies is crucial for improving accuracy.
Participating in workshops, training sessions, and staying abreast of current research helps engineers apply cutting-edge practices and techniques to their FEM analysis projects.
Conclusion
FEM analysis is a powerful tool for engineers, allowing them to model and simulate complex systems with precision.
By understanding its key points and implementing strategies to enhance accuracy, engineers can ensure they are making informed decisions based on reliable data.
Continuous learning and adopting advanced technologies are essential for sustaining high standards in FEM analysis, ultimately leading to improved design and engineering solutions.
資料ダウンロード
QCD調達購買管理クラウド「newji」は、調達購買部門で必要なQCD管理全てを備えた、現場特化型兼クラウド型の今世紀最高の購買管理システムとなります。
ユーザー登録
調達購買業務の効率化だけでなく、システムを導入することで、コスト削減や製品・資材のステータス可視化のほか、属人化していた購買情報の共有化による内部不正防止や統制にも役立ちます。
NEWJI DX
製造業に特化したデジタルトランスフォーメーション(DX)の実現を目指す請負開発型のコンサルティングサービスです。AI、iPaaS、および先端の技術を駆使して、製造プロセスの効率化、業務効率化、チームワーク強化、コスト削減、品質向上を実現します。このサービスは、製造業の課題を深く理解し、それに対する最適なデジタルソリューションを提供することで、企業が持続的な成長とイノベーションを達成できるようサポートします。
オンライン講座
製造業、主に購買・調達部門にお勤めの方々に向けた情報を配信しております。
新任の方やベテランの方、管理職を対象とした幅広いコンテンツをご用意しております。
お問い合わせ
コストダウンが利益に直結する術だと理解していても、なかなか前に進めることができない状況。そんな時は、newjiのコストダウン自動化機能で大きく利益貢献しよう!
(Β版非公開)