- お役立ち記事
- Fundamentals of fracture surface observation and analysis of metal materials and application to estimating the cause of damage
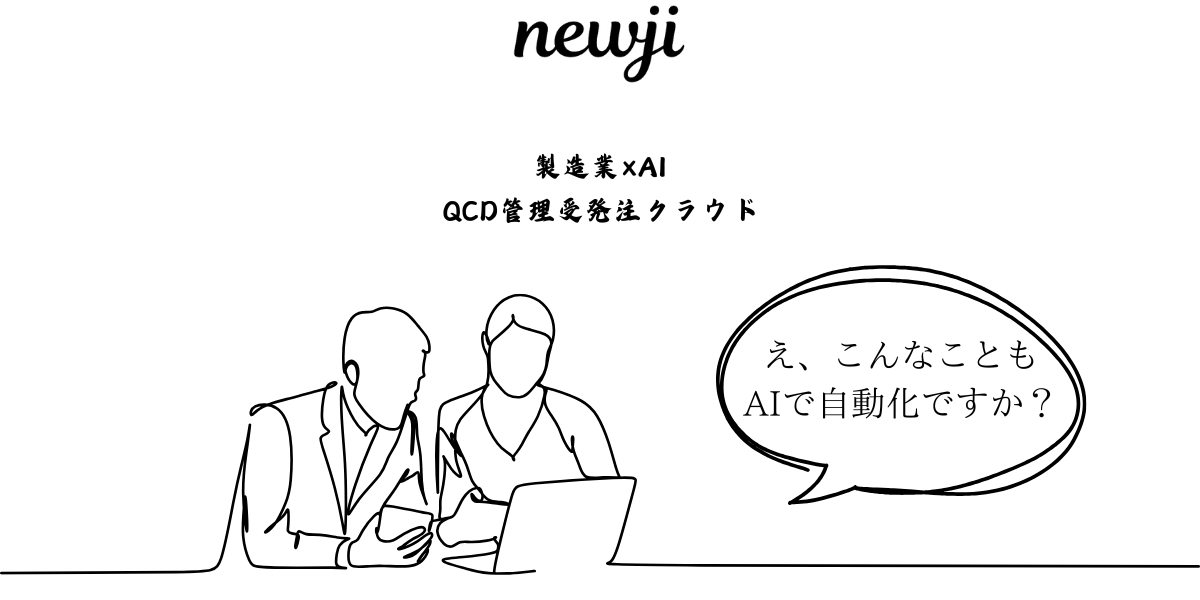
Fundamentals of fracture surface observation and analysis of metal materials and application to estimating the cause of damage
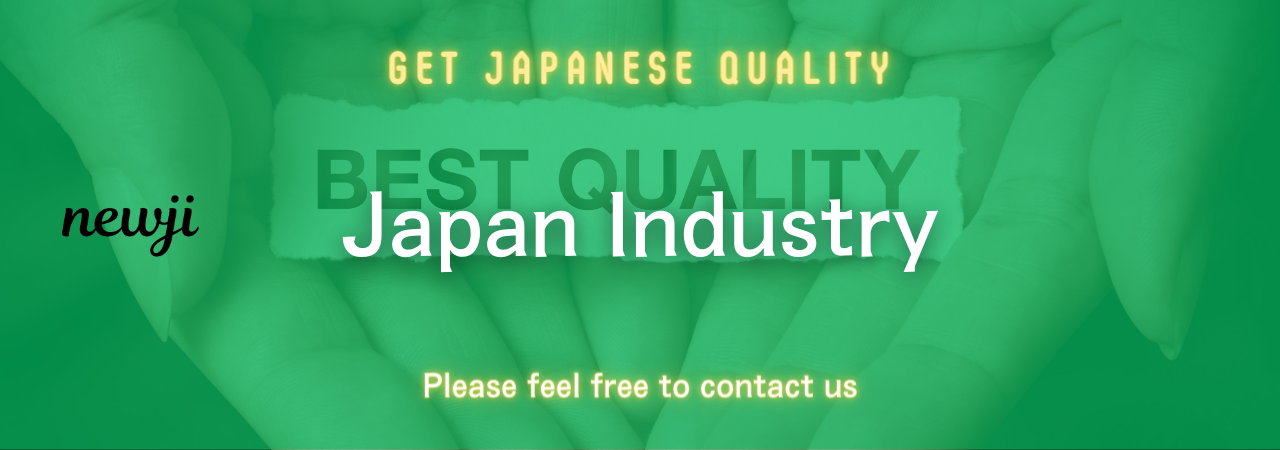
目次
Introduction to Fracture Surface Observation
Fracture surface observation is an essential technique used in understanding how and why materials fail.
When dealing with metal materials, the study of fracture surfaces provides crucial insights into their behavior under stress.
By examining these surfaces, experts can identify the type of fracture, its origin, and the progression of the crack.
This foundational knowledge allows engineers and scientists to predict the causes of failure and design more resilient metal structures.
The Importance of Fracture Analysis in Metal Materials
Metal materials are widely used due to their durability and strength.
However, like all materials, they are prone to wear and tear over time.
Fracture analysis becomes critical in identifying weaknesses and preventing catastrophic failures, especially in structures like bridges, vehicles, and machinery.
Analyzing the surface of a fracture gives us clues about the forces at play, the stress distribution, and potential external factors contributing to the damage.
By understanding these elements, preventative measures can be implemented to enhance the safety and longevity of metal products.
Steps in Fracture Surface Observation
The fracture surface observation process can be broken down into several key steps that ensure a comprehensive analysis.
1. Visual Examination
The first step involves a thorough visual inspection of the fractured surface using the naked eye or a magnifying glass.
This initial examination helps determine the fracture type, such as ductile, brittle, fatigue, or stress-corrosion cracking.
Visual examination provides a broad understanding of where the fracture initiated and how it propagated.
2. Microscopic Analysis
Once a preliminary visual analysis is complete, more detailed observations are conducted using microscopes.
This often includes scanning electron microscopy (SEM), which provides heightened magnification and resolution.
SEM reveals detailed features of the fracture surface, like dimples, river patterns, or striations, which signify different fracture mechanisms.
Microscopic analysis aids in identifying micro-level discrepancies which contribute to a deeper understanding of the fracture process.
3. Chemical Composition Assessment
For a holistic analysis, understanding the material’s chemical composition at the fracture site is essential.
Techniques such as energy-dispersive X-ray spectroscopy (EDX) are employed to detect elemental composition.
This data can reveal if material impurities or chemical reactions contributed to the failure.
4. Mechanical Testing
To correlate fracture observations with mechanical properties, tests like tensile strength, impact resistance, and hardness are conducted.
These tests replicate conditions that might have led to the fracture and validate hypotheses about material performance under stress.
Types of Fractures in Metal Materials
Understanding different fracture types helps in pinpointing specific causes of failure and in choosing suitable materials for various applications.
Ductile Fracture
Ductile fractures are characterized by significant plastic deformation before failure.
They typically occur in metals with high toughness and elongation.
The fracture surface has a rough, fibrous appearance, often populated with dimple patterns.
These features suggest that the material absorbed substantial energy before fracturing, allowing it to stretch and deform significantly.
Brittle Fracture
Brittle fractures occur with minimal plastic deformation and generally propagate rapidly.
The fracture surface appears smooth and flat with distinctive features like cleavage facets and mirror zones.
Brittle fractures are more perilous as they happen abruptly and can lead to catastrophic failure.
Fatigue Fracture
Fatigue fracture results from cyclic loading over prolonged periods, leading to progressive and localized structural damage.
The fracture surface exhibits distinct striations, marking each cycle of loading that contributed to crack growth.
Fatigue fractures often initiate from surface defects or stress concentrators like sharp corners.
Stress-Corrosion Cracking (SCC)
SCC is a type of failure resulting from the combined action of tensile stress and a corrosive environment.
The fracture surfaces in SCC differ significantly from pure mechanical failures, often having brittle appearances with branching cracks.
Recognizing SCC is critical in industries like petrochemical and aerospace, where materials are exposed to harsh environments.
Application of Fracture Analysis in Damage Estimation
Fracture analysis is invaluable in industries where metal failure can have serious consequences.
It equips engineers with the ability to estimate damage causes and implement preventive measures.
Failure Investigation in Engineering
When a metal component fails, understanding its fracture surfaces helps engineers identify the failure mode and its origin.
Such investigations are crucial in designing safer systems and structures.
They allow engineers to implement changes that enhance material performance and safety, thereby preventing future incidents.
Improving Material Selection
By understanding the fracture characteristics of metals, industries can make informed decisions on material selection tailored for specific uses.
This helps ensure that materials chosen possess adequate resistance to anticipated stressors and environmental conditions.
Quality Assurance in Manufacturing
Fracture analysis plays a role in identifying material defects resulting from manufacturing processes.
By examining fracture surfaces, manufacturers can pinpoint process-related issues such as casting defects or improper heat treatment.
Ensuring high-quality manufacturing processes directly translates to more reliable and durable metal products.
Conclusion
Fracture surface observation and analysis are fundamental techniques that enhance our understanding of metal material failures.
These insights not only explain why fractures occur but also guide improvements in material design, selection, and overall engineering practices.
With continued advancements in observational technology and analytical methods, the potential to predict and prevent metal failure is greater than ever.
Such diligence in studying fracture surfaces safeguards a future of more resilient and dependable metal constructs.
資料ダウンロード
QCD調達購買管理クラウド「newji」は、調達購買部門で必要なQCD管理全てを備えた、現場特化型兼クラウド型の今世紀最高の購買管理システムとなります。
ユーザー登録
調達購買業務の効率化だけでなく、システムを導入することで、コスト削減や製品・資材のステータス可視化のほか、属人化していた購買情報の共有化による内部不正防止や統制にも役立ちます。
NEWJI DX
製造業に特化したデジタルトランスフォーメーション(DX)の実現を目指す請負開発型のコンサルティングサービスです。AI、iPaaS、および先端の技術を駆使して、製造プロセスの効率化、業務効率化、チームワーク強化、コスト削減、品質向上を実現します。このサービスは、製造業の課題を深く理解し、それに対する最適なデジタルソリューションを提供することで、企業が持続的な成長とイノベーションを達成できるようサポートします。
オンライン講座
製造業、主に購買・調達部門にお勤めの方々に向けた情報を配信しております。
新任の方やベテランの方、管理職を対象とした幅広いコンテンツをご用意しております。
お問い合わせ
コストダウンが利益に直結する術だと理解していても、なかなか前に進めることができない状況。そんな時は、newjiのコストダウン自動化機能で大きく利益貢献しよう!
(Β版非公開)