- お役立ち記事
- Fundamentals of hydrodynamic bearings, design methods, and troubleshooting
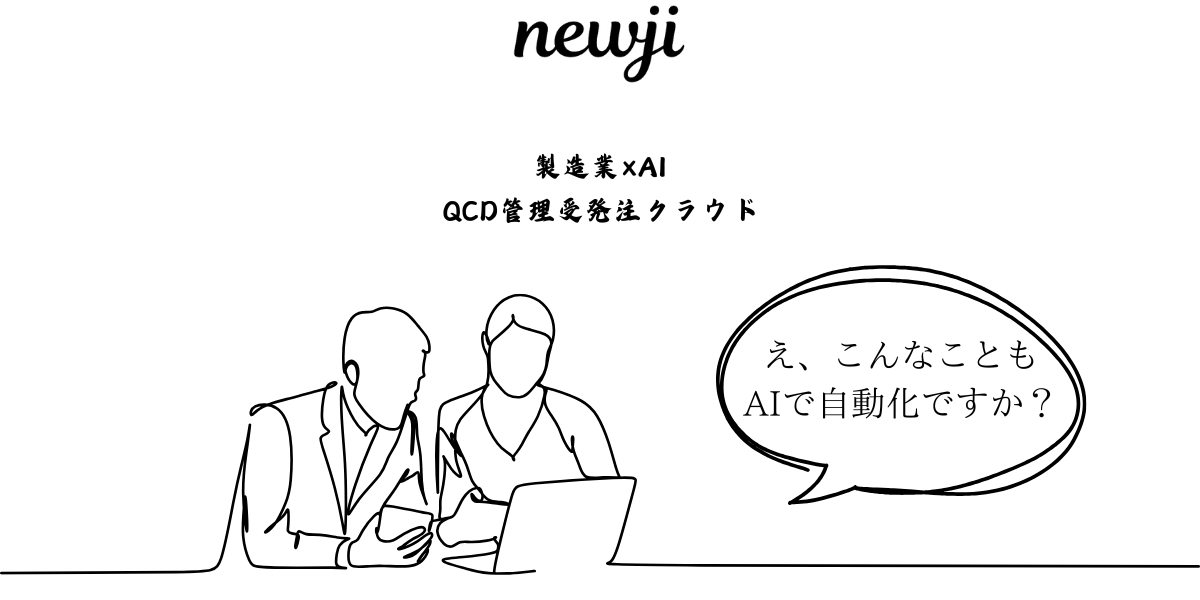
Fundamentals of hydrodynamic bearings, design methods, and troubleshooting
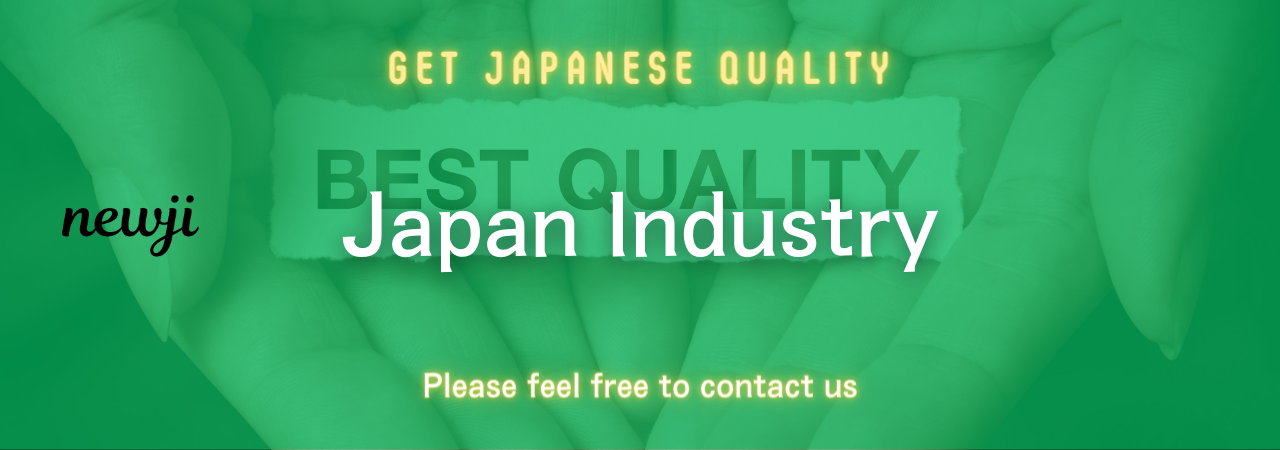
目次
Understanding Hydrodynamic Bearings
Hydrodynamic bearings are a fascinating component used in various machinery to reduce friction and wear between moving parts.
By understanding the fundamentals of how these bearings work, their design methods, and common troubleshooting techniques, we can better appreciate their critical role in ensuring the smooth operation of equipment.
In essence, hydrodynamic bearings rely on a thin film of fluid to create a wear-resistant layer between components, allowing for relative motion with minimal friction.
This fluid film is generated as the moving parts, typically a shaft, begin to rotate, drawing lubricant into the bearing and creating a pressure field that supports the load.
Basic Principles of Hydrodynamic Bearings
The key to the operation of hydrodynamic bearings is the formation of a lubricating film between the bearing surfaces.
When the shaft inside the bearing starts to spin, it drags the lubricant into the space between the shaft and the bearing surface.
This action generates what is known as a wedge-shaped film of lubricant, lifting and separating the surfaces.
During operation, the rotation speed is crucial; it must be sufficient to maintain the pressure and thickness of the lubricant film to support the load.
If the speed is too low or the load is too high, the film can break down, leading to direct contact between components and increased wear.
Design Methods for Hydrodynamic Bearings
Designing an efficient hydrodynamic bearing requires a thorough understanding of the system’s requirements and constraints.
Here, we’ll look into some of the critical design considerations:
Material Selection
Selecting the right materials for hydrodynamic bearings is essential for reliability and performance.
Common materials include white metals, bronze, and certain polymers, each chosen based on factors like load capacity, operating temperature, and corrosion resistance.
The choice of material impacts the bearing’s ability to form an effective lubricating film and resist wear.
Bearing Geometry
The geometry of a hydrodynamic bearing defines its ability to generate an adequate lubricant film.
Designers may opt for various shapes, such as cylindrical or tapered bearings, depending on the application’s specific demands.
A well-designed bearing geometry will ensure that the lubricant distribution is uniform, reducing the risk of localized wear.
Lubricant Selection
Choosing the appropriate lubricant is vital for the optimal performance of hydrodynamic bearings.
Factors to consider include viscosity, operating temperature ranges, and compatibility with bearing materials.
The right lubricant should maintain its film-forming capabilities across the entire operational temperature and speed spectrum.
Load and Speed Considerations
Understanding the axial and radial loads, along with the anticipated rotational speeds, is integral to the bearing design process.
These factors influence the size and design of the bearing to ensure it can sustain the loads without compromising performance.
Engineers must find a balance between speed, load capacity, and bearing size to achieve the highest efficiency.
Troubleshooting Common Issues
Even with a robust design, hydrodynamic bearings can encounter problems during operation.
Knowing how to troubleshoot these issues is essential for maintaining machinery health and preventing downtime.
Inadequate Lubrication
One common issue in hydrodynamic bearings is insufficient lubrication.
This can result from incorrect lubricant selection, low oil levels, or improper maintenance practices.
To mitigate this, ensure that the lubricant is regularly checked and replenished and that the correct type is used as per the design specifications.
Excessive Wear
If the lubricant film breaks down, it may lead to excessive wear of the bearing surfaces.
Possible causes include contaminants in the lubricant, improper bearing alignment, or the bearing being subjected to loads beyond its designed capacity.
Regular inspection and maintenance can help identify wear patterns early, allowing adjustments or replacements before significant damage occurs.
Temperature Fluctuations
A substantial rise in operational temperatures can diminish the viscosity of the lubricant, affecting the film’s ability to carry loads.
Temperature fluctuations may be due to external factors or a sign of internal issues like friction or misalignment.
Monitoring temperature and addressing anomalies swiftly can prevent damage and maintain bearing efficiency.
Noisy Operation
Unusual noises during operation can be a telltale sign of a failing hydrodynamic bearing.
Vibrations or rattling sounds might stem from misalignment, imbalanced loads, or impending breakdown of the lubricating film.
Immediate investigation into the root cause of such noises can prevent more severe problems down the line.
Conclusion
Hydrodynamic bearings play an indispensable role in countless mechanical systems where low-friction movement is crucial.
A solid understanding of their fundamentals, thoughtful design practices, and proactive troubleshooting measures can significantly enhance their performance and longevity.
By continually monitoring performance parameters and maintaining proper lubrication, machinery equipped with hydrodynamic bearings can enjoy increased reliability and efficiency, ultimately leading to smoother and more cost-effective operations.
資料ダウンロード
QCD調達購買管理クラウド「newji」は、調達購買部門で必要なQCD管理全てを備えた、現場特化型兼クラウド型の今世紀最高の購買管理システムとなります。
ユーザー登録
調達購買業務の効率化だけでなく、システムを導入することで、コスト削減や製品・資材のステータス可視化のほか、属人化していた購買情報の共有化による内部不正防止や統制にも役立ちます。
NEWJI DX
製造業に特化したデジタルトランスフォーメーション(DX)の実現を目指す請負開発型のコンサルティングサービスです。AI、iPaaS、および先端の技術を駆使して、製造プロセスの効率化、業務効率化、チームワーク強化、コスト削減、品質向上を実現します。このサービスは、製造業の課題を深く理解し、それに対する最適なデジタルソリューションを提供することで、企業が持続的な成長とイノベーションを達成できるようサポートします。
オンライン講座
製造業、主に購買・調達部門にお勤めの方々に向けた情報を配信しております。
新任の方やベテランの方、管理職を対象とした幅広いコンテンツをご用意しております。
お問い合わせ
コストダウンが利益に直結する術だと理解していても、なかなか前に進めることができない状況。そんな時は、newjiのコストダウン自動化機能で大きく利益貢献しよう!
(Β版非公開)