- お役立ち記事
- The basics of cost accounting necessary for those in the manufacturing industry and how to utilize it to reduce costs
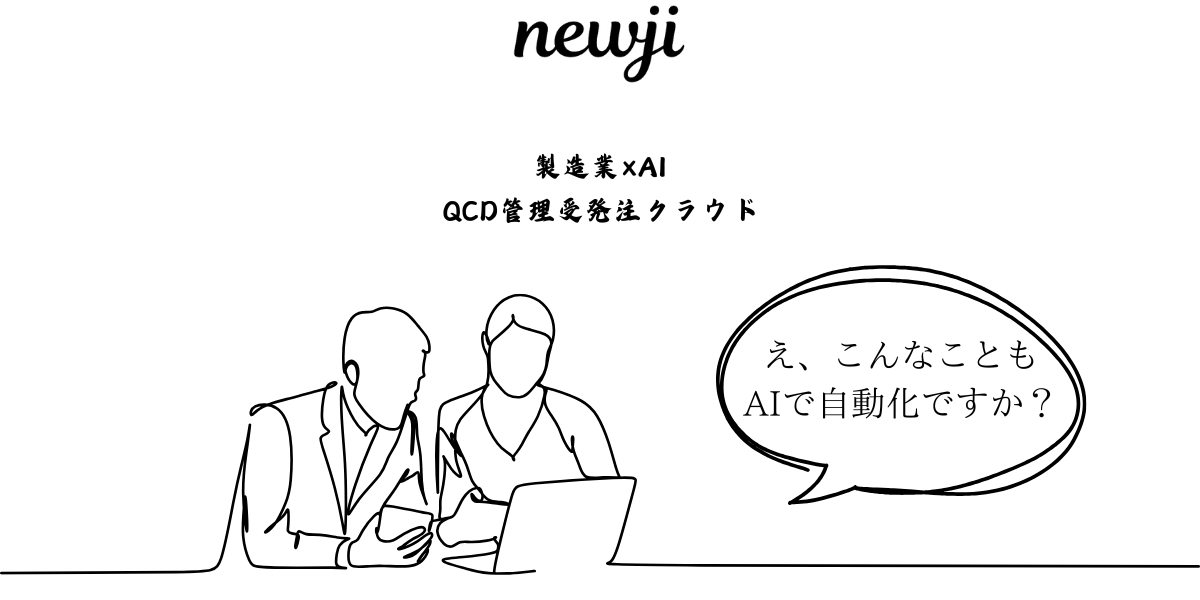
The basics of cost accounting necessary for those in the manufacturing industry and how to utilize it to reduce costs
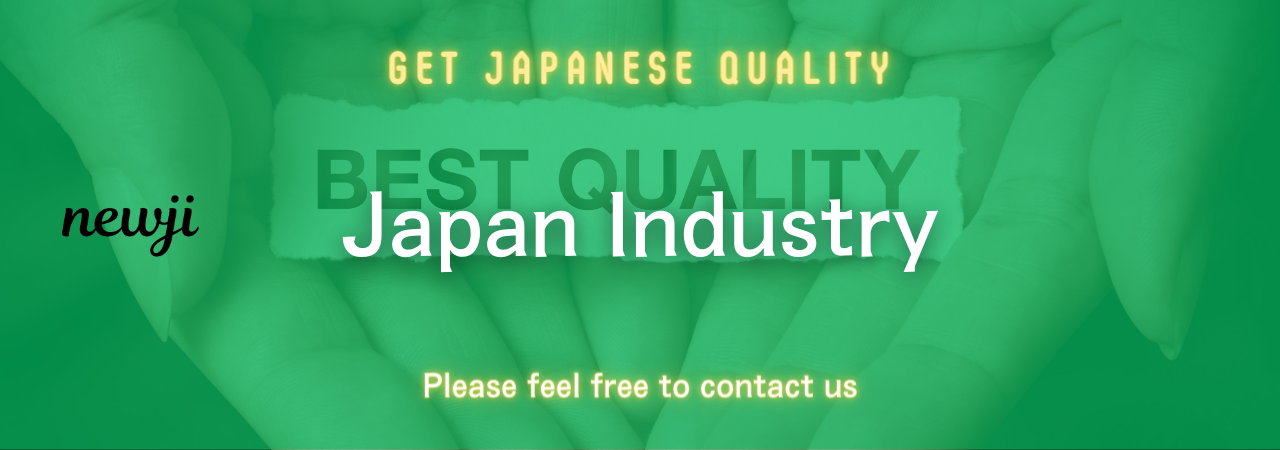
目次
Understanding Cost Accounting in the Manufacturing Industry
Cost accounting is an essential tool for any manufacturing business aiming to improve its operations and profitability.
While financial accounting provides an overall picture of company performance, cost accounting offers detailed insights into individual operational processes.
This type of accounting helps in tracking, recording, and analyzing costs associated with manufacturing.
The information it provides is crucial in making efficient and cost-effective decisions.
Manufacturing businesses need to understand where their money is being spent at every production stage.
This knowledge helps in identifying areas where costs can be cut without affecting product quality.
Furthermore, cost accounting is not just about tracking expenses but also involves planning and controlling future costs.
By applying these practices, manufacturers can enhance their product offerings while maintaining or lowering their expenses.
The Components of Cost Accounting
In cost accounting, costs are typically divided into three major categories: direct materials, direct labor, and overhead.
1. **Direct Materials**: These are raw materials that can be directly traced to the production of a product.
For instance, in a furniture manufacturing company, wood would be considered a direct material.
Keeping a tight rein on direct material costs is critical for manufacturers, as it directly impacts the cost of goods sold.
2. **Direct Labor**: This cost pertains to the wages of employees who are directly involved in the manufacturing process.
It includes all labor efforts that can be directly attributed to the production of goods.
Managing direct labor costs involves optimizing work efficiency and minimizing any wasteful practices that don’t add value to the production process.
3. **Overhead**: These are indirect costs that cannot be easily traced to a single product.
Examples include utilities, maintenance, depreciation of factory equipment, and managerial salaries.
Although overhead does not vary directly with production levels, it still needs to be accounted for to ensure a complete understanding of costs.
Methods of Cost Accounting
Manufacturing firms use several cost accounting methods to gain insights into their operations.
Some of the most common methods include:
– **Job Order Costing**: This method is useful when products are manufactured based on specific customer orders.
Each job has its own specifications and costs, which are tracked individually.
It’s ideal for companies that produce bespoke or customized products.
– **Process Costing**: This method is used when products are indistinguishable from one another and produced in a continuous flow.
Costs are accumulated over a period and divided by the number of units produced for that time frame.
Examples of industries that utilize process costing include chemical production and oil refining.
– **Activity-Based Costing (ABC)**: ABC focuses on identifying activities that drive costs within the manufacturing process and assigns costs accordingly.
It provides more precise costing as it evaluates the cost of each activity.
This helps businesses identify which activities are essential and which can be optimized to improve efficiency.
How to Utilize Cost Accounting to Reduce Costs
Cost accounting, when effectively implemented, can lead to significant cost reductions.
Here are some strategies on how manufacturers can utilize cost accounting insights to lower expenses:
Implementing a Cost Control System
A robust cost control system involves setting cost standards, comparing actual costs with these standards, and analyzing any deviations.
Through continuous monitoring and evaluation, manufacturers can spot inefficiencies promptly and take corrective action.
Setting realistic cost standards is essential—they should be achievable with a bit of effort to drive efficiency improvements.
Analyzing Variability in Costs
Manufacturers should regularly analyze cost behavior and variability.
Knowing which costs are fixed, variable, or semi-variable helps in forecasting future expenses accurately.
During periods of fluctuating demand, having an in-depth understanding of cost behavior enables manufacturers to adjust production levels smartly, ensuring optimal resource utilization.
Streamlining Production Processes
Cost accounting plays a crucial role in identifying bottlenecks and wasteful processes in production.
By utilizing data from cost reports, manufacturers can streamline production techniques, reduce idle time, and minimize material wastage.
Lean manufacturing methods can also be implemented to enhance processes by focusing on value-adding activities.
Optimizing Product Mix
Through the use of cost accounting, manufacturers can determine the profitability of different products.
By analyzing the individual cost structures of each product, businesses can focus on producing high-margin items and potentially eliminate or redesign those that are less profitable.
An optimized product mix enhances revenue while reducing the risk of loss.
Supplier Relationship Management
Effective supplier management can lead to considerable cost savings.
By negotiating favorable terms, manufacturers can reduce the costs of direct materials.
Cost accounting data helps identify which suppliers offer the best balance between cost and quality, enabling businesses to make better purchasing decisions.
Developing long-term partnerships with these suppliers may lead to additional benefits, such as discounts or better payment terms.
Conclusion: Embracing Cost Accounting for Sustainable Growth
In the competitive landscape of manufacturing, cost accounting serves as a vital ally in driving down costs and improving profitability.
By adopting detailed cost-tracking practices, manufacturers can gain deeper insights into their operations.
Implementing the strategies mentioned can enable businesses to streamline their processes, make informed decisions, and ultimately achieve sustainable growth.
As markets evolve, those who master the art of cost accounting will have a significant edge over the competition.
資料ダウンロード
QCD調達購買管理クラウド「newji」は、調達購買部門で必要なQCD管理全てを備えた、現場特化型兼クラウド型の今世紀最高の購買管理システムとなります。
ユーザー登録
調達購買業務の効率化だけでなく、システムを導入することで、コスト削減や製品・資材のステータス可視化のほか、属人化していた購買情報の共有化による内部不正防止や統制にも役立ちます。
NEWJI DX
製造業に特化したデジタルトランスフォーメーション(DX)の実現を目指す請負開発型のコンサルティングサービスです。AI、iPaaS、および先端の技術を駆使して、製造プロセスの効率化、業務効率化、チームワーク強化、コスト削減、品質向上を実現します。このサービスは、製造業の課題を深く理解し、それに対する最適なデジタルソリューションを提供することで、企業が持続的な成長とイノベーションを達成できるようサポートします。
オンライン講座
製造業、主に購買・調達部門にお勤めの方々に向けた情報を配信しております。
新任の方やベテランの方、管理職を対象とした幅広いコンテンツをご用意しております。
お問い合わせ
コストダウンが利益に直結する術だと理解していても、なかなか前に進めることができない状況。そんな時は、newjiのコストダウン自動化機能で大きく利益貢献しよう!
(Β版非公開)