- お役立ち記事
- Fundamentals of material mechanics and application to strength design of plastic products
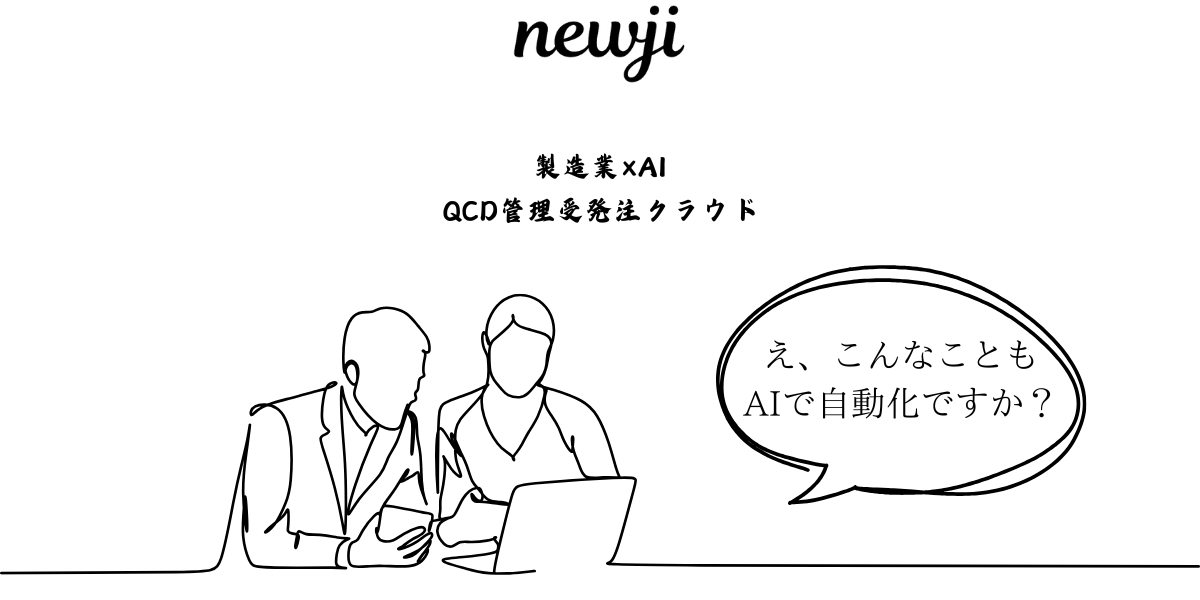
Fundamentals of material mechanics and application to strength design of plastic products
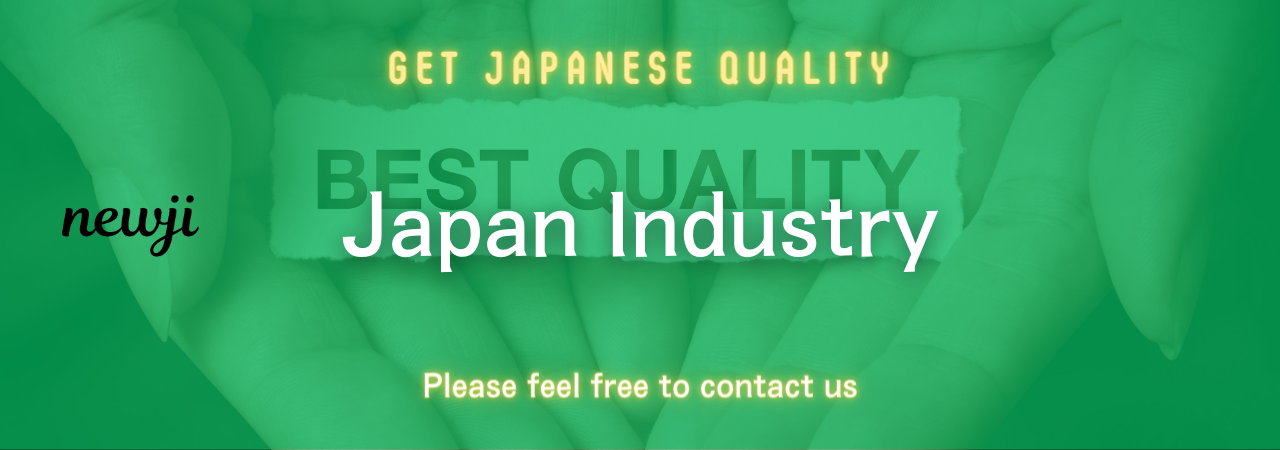
目次
Understanding Material Mechanics
Material mechanics is a crucial field of study that delves into the behavior of materials under various forces and conditions.
It forms the backbone of designing and developing products that can withstand the stresses and strains of their intended uses.
This study is essential for engineers seeking to create robust and reliable plastic products.
Basic Concepts of Material Mechanics
Material mechanics is primarily concerned with how materials deform and fail under different conditions.
It involves understanding concepts like stress, strain, elasticity, plasticity, and strength.
Stress refers to the internal forces that occur within a material.
Strain, on the other hand, is the deformation experienced by the material due to stress.
Elasticity is the ability of a material to return to its original shape after the removal of stress.
Plasticity describes the permanent deformation of a material when subjected to stress beyond its elastic limit.
The strength of a material is its capacity to withstand an applied load without failure.
Importance in Plastic Products
The role of material mechanics in the design of plastic products cannot be overstated.
Plastics, being versatile and widely used materials, need careful consideration during design to ensure that they perform their intended functions effectively.
Understanding the mechanical properties of plastics is vital to predict their behavior under different loads and conditions.
Knowledge of material mechanics allows engineers to choose the right type of plastic for a specific application.
It guides the design process to avoid unnecessary failures or over-engineering, thus optimizing both the material usage and cost.
Application in Strength Design
The application of material mechanics in strength design involves determining how a plastic product will respond to forces it encounters in its service life.
This step is critical in ensuring the structural integrity and longevity of the product.
Analyzing Forces and Loads
For strength design, engineers must first analyze expected forces and loads on the product.
These can range from static loads, which are consistent and unchanging, to dynamic loads, which vary over time.
Understanding these forces helps in designing plastics that are capable of withstanding stressful conditions.
Load analysis is not limited to the forces applied externally.
Engineers must also consider internal factors like temperature changes and chemical exposure, which can affect material performance.
Choosing the Right Plastic
Once the forces and conditions are understood, the next step involves selecting suitable plastic materials.
Different plastics offer varied strength, flexibility, impact resistance, and thermal stability.
For instance, thermoplastics like nylon or polycarbonate might be chosen for high-impact applications due to their toughness.
Thermosets like epoxy, which are hard and brittle, might be selected for their excellent heat resistance.
Designing for Strength
Designing plastic products for strength involves creating structure and shape that help distribute stress evenly and prevent failure.
The geometry of the piece, including thickness and curvature, plays a significant role in how it handles stress.
Designers often use tools like finite element analysis (FEA) to simulate how a product will react under different conditions.
This allows for optimization of design before physical prototypes are produced.
Testing and Prototyping
Prototyping and testing are integral to the design process.
Through prototypes, engineers can physically test the product’s performance and make necessary adjustments.
Various tests, such as tensile strength tests or impact tests, are conducted to ensure that the plastic meets the defined criteria of performance.
Feedback from testing is crucial for refining the design.
It helps finalize the product’s specifications and assures compliance with industry standards or regulations.
Practical Challenges and Considerations
While material mechanics provides a theoretical framework, practical challenges often arise in the strength design of plastic products.
These include handling variability in material properties and accounting for manufacturing inconsistencies.
Material Variability
Plastic materials can vary significantly in terms of quality and properties, even among products from the same batch.
Factors like source material, production methods, and additives can cause variations.
Engineers must account for this variability in their designs to ensure consistent performance across all products.
Manufacturing Processes
Manufacturing processes can also impact the mechanical properties of plastics.
For example, processes like injection molding can introduce stresses or defects if not carefully controlled.
Engineers need to consider these effects during design and work closely with manufacturers to ensure quality control.
Environmental Impact
Environmental conditions such as temperature, humidity, and UV exposure can significantly affect the strength and durability of plastic products.
Designers must ensure that the chosen materials and design are suitable for the intended environment.
Using additives or coatings may help enhance resistance to environmental factors.
The Future of Plastic Product Design
The integration of advanced technologies such as machine learning and 3D printing is shaping the future of strength design for plastic products.
These innovations offer opportunities for more accurate simulations, efficient designs, and personalized product solutions.
Sustainable practices and eco-friendly materials are gaining prominence, urging engineers to reconsider traditional ways of designing with plastic.
Bioplastics and recycled materials are becoming viable alternatives, contributing towards a greener future.
The continuous advancements in material mechanics and strength design principles empower engineers to create innovative and sustainable plastic products.
This ensures that they meet the demands of modern society while aligning with global sustainability goals.
資料ダウンロード
QCD調達購買管理クラウド「newji」は、調達購買部門で必要なQCD管理全てを備えた、現場特化型兼クラウド型の今世紀最高の購買管理システムとなります。
ユーザー登録
調達購買業務の効率化だけでなく、システムを導入することで、コスト削減や製品・資材のステータス可視化のほか、属人化していた購買情報の共有化による内部不正防止や統制にも役立ちます。
NEWJI DX
製造業に特化したデジタルトランスフォーメーション(DX)の実現を目指す請負開発型のコンサルティングサービスです。AI、iPaaS、および先端の技術を駆使して、製造プロセスの効率化、業務効率化、チームワーク強化、コスト削減、品質向上を実現します。このサービスは、製造業の課題を深く理解し、それに対する最適なデジタルソリューションを提供することで、企業が持続的な成長とイノベーションを達成できるようサポートします。
オンライン講座
製造業、主に購買・調達部門にお勤めの方々に向けた情報を配信しております。
新任の方やベテランの方、管理職を対象とした幅広いコンテンツをご用意しております。
お問い合わせ
コストダウンが利益に直結する術だと理解していても、なかなか前に進めることができない状況。そんな時は、newjiのコストダウン自動化機能で大きく利益貢献しよう!
(Β版非公開)