- お役立ち記事
- Hydrogen embrittlement mechanism and hydrogen embrittlement suppression technology
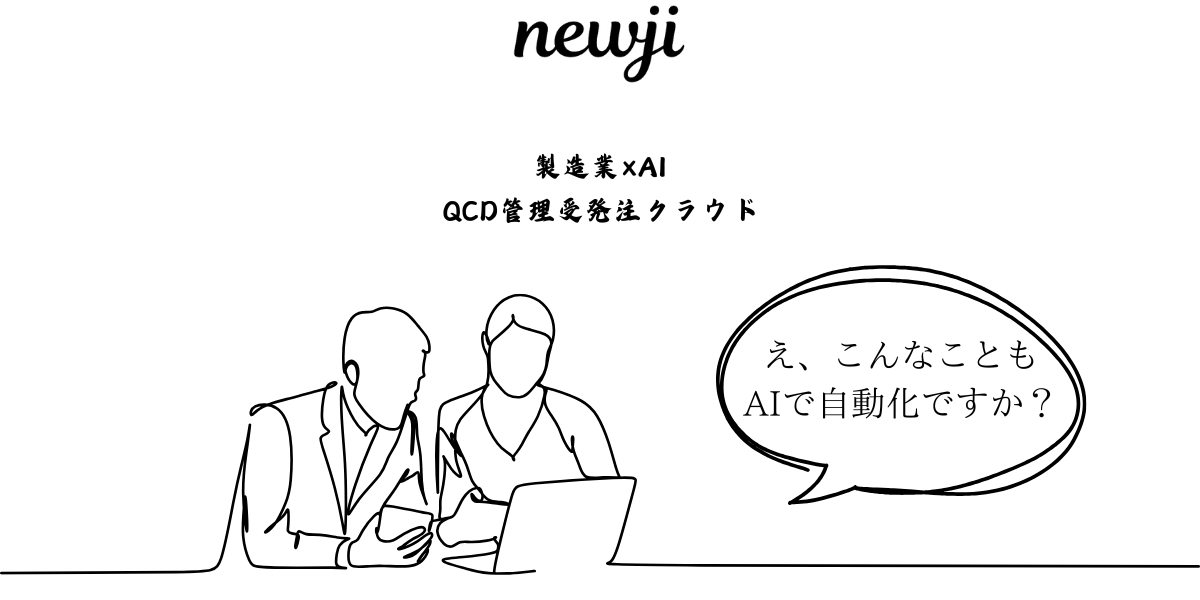
Hydrogen embrittlement mechanism and hydrogen embrittlement suppression technology
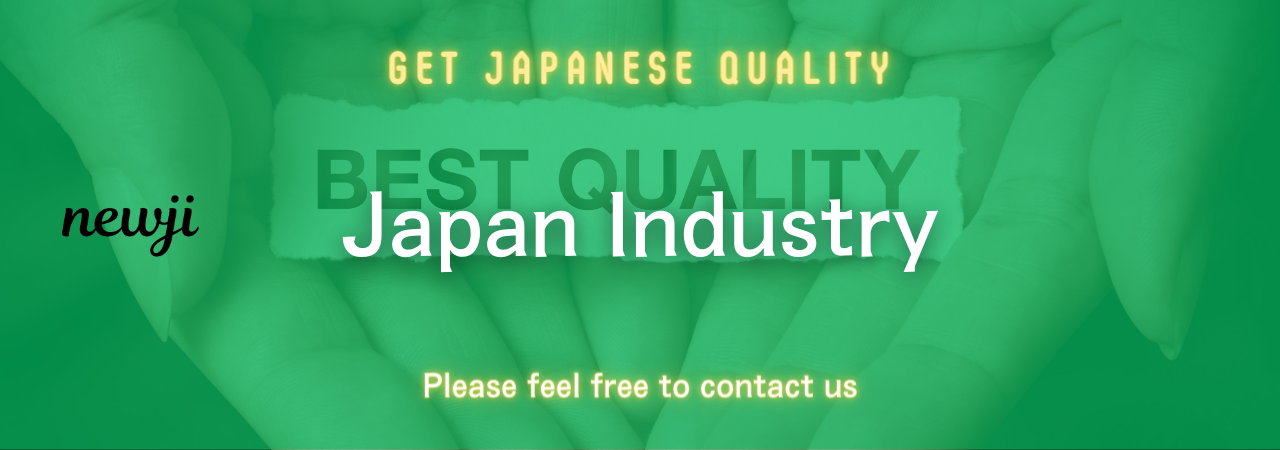
目次
Understanding Hydrogen Embrittlement
Hydrogen embrittlement is a phenomenon that affects various metals, making them more brittle and prone to failure.
This condition poses significant challenges in industries where metal components are exposed to hydrogen environments, such as in aerospace, automotive, and energy sectors.
Understanding how hydrogen embrittlement occurs is crucial for developing effective prevention and suppression strategies.
What is Hydrogen Embrittlement?
Hydrogen embrittlement occurs when hydrogen atoms penetrate a metal’s structure, leading to a reduction in its ductility and toughness.
The process can result in metal cracking, brittle fracture, and, ultimately, component failure.
This can happen in different metals, including steel, titanium, and aluminum alloys.
The problem typically arises when metals are exposed to hydrogen-rich environments, either while in service or during manufacturing processes like welding and plating.
The Mechanism of Hydrogen Embrittlement
Hydrogen embrittlement involves a complex interaction between hydrogen atoms and the metal’s microstructure.
When hydrogen atoms enter the metal lattice, they can migrate into defects, such as cracks, voids, or grain boundaries.
These atoms can create pressure within these defects, leading to increased stress concentrations in the local areas.
This stress buildup can ultimately result in crack initiation and propagation, drastically reducing the metal’s mechanical integrity.
Another mechanism involves hydrogen atoms creating a weaker bond between metallic atoms, reducing the metal’s ability to deform under stress.
This makes the metal more susceptible to cracking even under lower loads than it would typically withstand without hydrogen.
Factors Affecting Hydrogen Embrittlement
Several factors can influence the susceptibility of metals to hydrogen embrittlement.
One of the critical variables is the type of metal or alloy used.
High-strength steels, for example, tend to be more susceptible to embrittlement than softer, more ductile metals.
The environment also plays a significant role.
The presence of moisture, acidity, and temperature can all affect the rate of hydrogen uptake and the resulting embrittlement.
Additionally, the method of hydrogen exposure—whether from gaseous hydrogen, aqueous solution, or during electrochemical reactions like plating—can impact how embrittlement progresses.
Preventing Hydrogen Embrittlement
Preventing hydrogen embrittlement involves a combination of material selection, design considerations, and processing conditions.
Material Selection
Choosing materials that are less susceptible to hydrogen absorption is one of the primary ways to prevent embrittlement.
Metals such as austenitic stainless steels and nickel-based alloys generally exhibit better resistance to hydrogen embrittlement.
In cases where high-strength steels are necessary, alloying elements that improve resistance, like chromium and molybdenum, can be considered.
Design Considerations
Designing components to minimize stress concentrations and regions where hydrogen may accumulate can also help prevent embrittlement.
This includes eliminating sharp corners, notches, and other features that could act as starting points for cracks.
Additionally, employing coatings or surface treatments can serve as barriers to hydrogen penetration.
Protective layers like zinc or aluminum coatings can significantly reduce the risk of hydrogen entering the metal substrate.
Processing Conditions
Controlling the manufacturing processes that involve hydrogen exposure is crucial.
For instance, during welding, using lower heat inputs can reduce the formation of microstructures that are prone to hydrogen absorption.
Post-processing techniques like baking or heat treatment can also be employed to drive off any absorbed hydrogen.
These methods are particularly effective in removing hydrogen that might have been introduced during manufacturing.
Technological Advances in Suppression
Advancements in technology have opened new avenues for suppressing hydrogen embrittlement.
Coating Technologies
Innovative coating technologies are being developed to create stronger barriers against hydrogen entry.
These include advanced ceramic coatings that provide a robust shield to the metal substrate.
Additionally, research is ongoing into polymer-based coatings that offer flexibility alongside hydrogen protection.
Alloy Development
Researchers are working on developing new alloy compositions that are inherently resistant to hydrogen embrittlement.
These next-generation alloys aim to maintain high strength and toughness, even in hydrogen-rich environments.
By optimizing the microstructure and composition, these new materials exhibit improved performance characteristics, reducing their susceptibility to embrittlement.
Hydrogen Sensors
The development of hydrogen sensors has significantly aided in the early detection of hydrogen buildup in critical components.
These sensors provide real-time monitoring of hydrogen levels, allowing for preventative measures to be taken before significant embrittlement occurs.
Conclusion
Hydrogen embrittlement remains a challenging issue in various industrial applications.
Understanding its mechanisms and factors is essential in preventing metal failures.
Through careful material selection, design, processing controls, and technological advancements, industries can effectively mitigate the risks associated with hydrogen embrittlement.
Continuing research and development in this area will further enhance our ability to prevent this phenomenon, ensuring the integrity and safety of metal components exposed to hydrogen.
By leveraging these strategies, we can minimize potential failures and extend the service life of critical components across multiple sectors.
資料ダウンロード
QCD調達購買管理クラウド「newji」は、調達購買部門で必要なQCD管理全てを備えた、現場特化型兼クラウド型の今世紀最高の購買管理システムとなります。
ユーザー登録
調達購買業務の効率化だけでなく、システムを導入することで、コスト削減や製品・資材のステータス可視化のほか、属人化していた購買情報の共有化による内部不正防止や統制にも役立ちます。
NEWJI DX
製造業に特化したデジタルトランスフォーメーション(DX)の実現を目指す請負開発型のコンサルティングサービスです。AI、iPaaS、および先端の技術を駆使して、製造プロセスの効率化、業務効率化、チームワーク強化、コスト削減、品質向上を実現します。このサービスは、製造業の課題を深く理解し、それに対する最適なデジタルソリューションを提供することで、企業が持続的な成長とイノベーションを達成できるようサポートします。
オンライン講座
製造業、主に購買・調達部門にお勤めの方々に向けた情報を配信しております。
新任の方やベテランの方、管理職を対象とした幅広いコンテンツをご用意しております。
お問い合わせ
コストダウンが利益に直結する術だと理解していても、なかなか前に進めることができない状況。そんな時は、newjiのコストダウン自動化機能で大きく利益貢献しよう!
(Β版非公開)