- お役立ち記事
- Fundamentals and practical points of DC motor control design/controller design
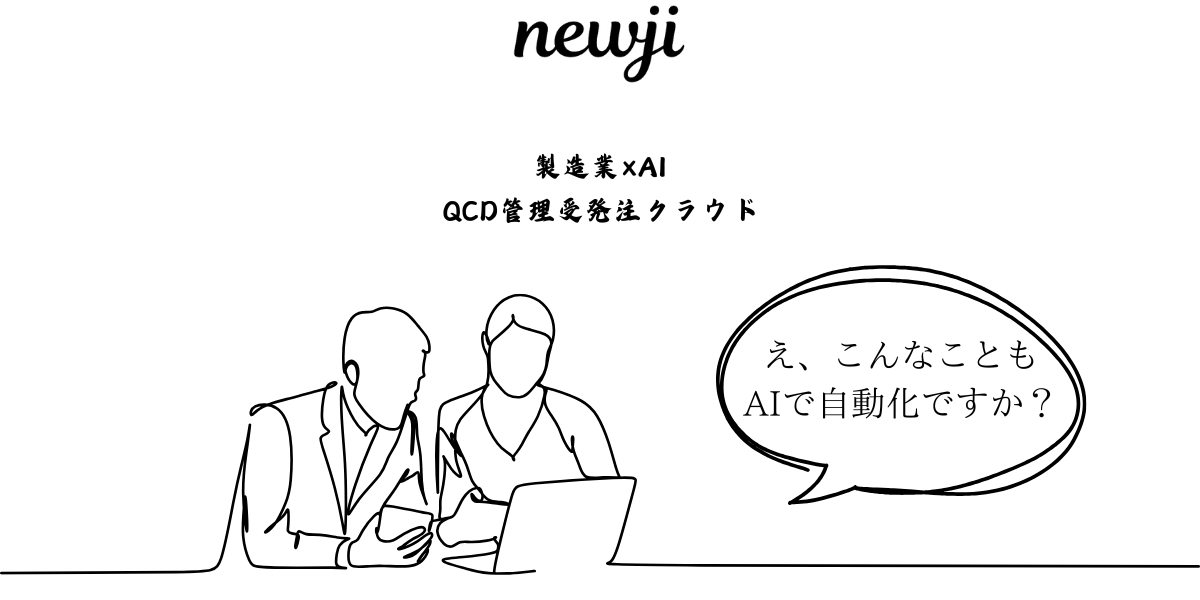
Fundamentals and practical points of DC motor control design/controller design
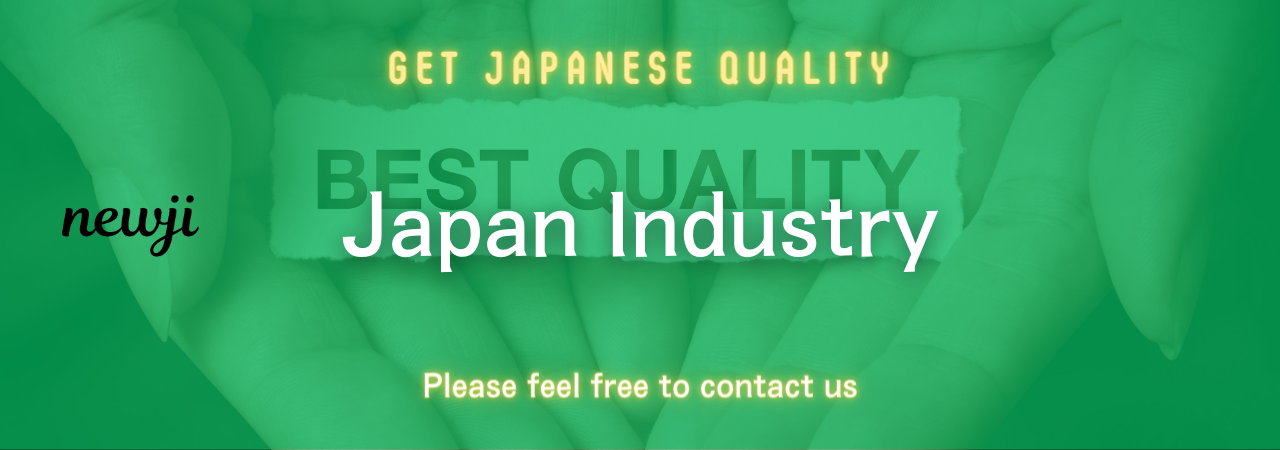
Understanding DC Motor Control
DC motors are widely used in various applications due to their simplicity, reliability, and ease of control.
Understanding the fundamentals of DC motor control is crucial for designing efficient and effective control systems.
In this article, we will explore the basics of DC motor control, as well as practical aspects of controller design.
Basics of DC Motor Operation
A DC motor converts electrical energy into mechanical energy through the interaction of magnetic fields.
The basic components of a DC motor include the armature, the field winding, and the commutator.
The armature is a rotating coil that experiences torque when subjected to a magnetic field.
The field winding generates the magnetic field required for the motor’s operation.
The commutator helps in reversing the current direction in the armature to maintain constant rotation.
Types of DC Motors
DC motors are categorized into different types based on their configuration and application.
The three most common types are:
1. **Shunt-wound DC motor**: In this type, the field winding is connected in parallel with the armature.
This configuration offers good speed regulation, making it suitable for applications that require constant speed.
2. **Series-wound DC motor**: Here, the field winding is connected in series with the armature.
This type provides high starting torque, making it ideal for applications like electric trains and cranes.
3. **Compound-wound DC motor**: This motor combines features of both shunt and series motors.
It is suitable for applications requiring a mix of high torque and good speed regulation.
Principles of DC Motor Control
The main objective of DC motor control is to regulate speed and position.
To achieve this, various control methods are employed, such as:
1. **Speed Control**:
– **Armature Control**: Varying the voltage across the armature to control speed.
– **Field Control**: Adjusting the field current to change the speed.
– **Voltage Control**: Using a variable voltage source to control speed.
2. **Position Control**: Achieved by using feedback mechanisms to maintain the desired position.
Feedback in DC Motor Control
Feedback is a crucial component of any control system.
In DC motor control, feedback is used to monitor the output and adjust inputs accordingly.
Common feedback mechanisms include:
– **Tachometers**: Measure rotational speed, providing real-time data for speed control.
– **Encoders**: Provide position feedback, essential for precise position control.
Designing a DC Motor Controller
Designing an effective DC motor controller involves multiple steps, starting from understanding system requirements to implementing the control logic.
Define System Requirements
Identify the performance goals, such as speed range, precision, and response time.
Consider the load characteristics and any environmental conditions that may affect motor performance.
Choose a Control Strategy
Select an appropriate control strategy based on the application requirements.
Common strategies include:
– **PID (Proportional-Integral-Derivative) Control**: Combines three control actions to achieve desired performance.
– **Fuzzy Logic Control**: Uses fuzzy logic principles for systems with uncertainties.
– **Model Predictive Control**: Uses a predictive model to optimize control actions.
Design the Control Circuit
Once a strategy is chosen, design the control circuit.
This involves selecting components that align with the control objectives, such as sensors, processors, and power electronics.
Ensure the design can handle the power requirements of the motor and any safety norms.
Implement Software Algorithms
Develop algorithms to execute the chosen control strategy.
Simulate the algorithm to validate its performance before deploying it in the actual system.
Testing and Optimization
After implementation, thoroughly test the controller’s performance under various conditions.
Identify any areas of improvement and make necessary adjustments.
Continuously monitor system performance and make iterative changes to improve efficiency and responsiveness.
Challenges in DC Motor Control Design
The design of DC motor controls can be complex and presents several challenges:
– **Non-linearity**: DC motors often exhibit non-linear behavior, complicating control strategies.
– **Load Variations**: Unexpected changes in load can affect performance, requiring adaptive control techniques.
– **Environmental Factors**: Temperature and humidity variations can influence motor performance.
Conclusion
DC motor control is a fundamental aspect of many industrial and consumer applications.
Understanding the types of DC motors, their operation, and control principles is essential for designing efficient controllers.
By carefully considering system requirements, choosing suitable control strategies, and implementing robust testing, an effective motor control system can be devised.
Being aware of challenges and continuously optimizing the system ensures long-term reliability and performance.
資料ダウンロード
QCD調達購買管理クラウド「newji」は、調達購買部門で必要なQCD管理全てを備えた、現場特化型兼クラウド型の今世紀最高の購買管理システムとなります。
ユーザー登録
調達購買業務の効率化だけでなく、システムを導入することで、コスト削減や製品・資材のステータス可視化のほか、属人化していた購買情報の共有化による内部不正防止や統制にも役立ちます。
NEWJI DX
製造業に特化したデジタルトランスフォーメーション(DX)の実現を目指す請負開発型のコンサルティングサービスです。AI、iPaaS、および先端の技術を駆使して、製造プロセスの効率化、業務効率化、チームワーク強化、コスト削減、品質向上を実現します。このサービスは、製造業の課題を深く理解し、それに対する最適なデジタルソリューションを提供することで、企業が持続的な成長とイノベーションを達成できるようサポートします。
オンライン講座
製造業、主に購買・調達部門にお勤めの方々に向けた情報を配信しております。
新任の方やベテランの方、管理職を対象とした幅広いコンテンツをご用意しております。
お問い合わせ
コストダウンが利益に直結する術だと理解していても、なかなか前に進めることができない状況。そんな時は、newjiのコストダウン自動化機能で大きく利益貢献しよう!
(Β版非公開)