- お役立ち記事
- Making technical information usable using evolutionary QFD and its application to FMEA, DRBFM, quality engineering, and problem analysis
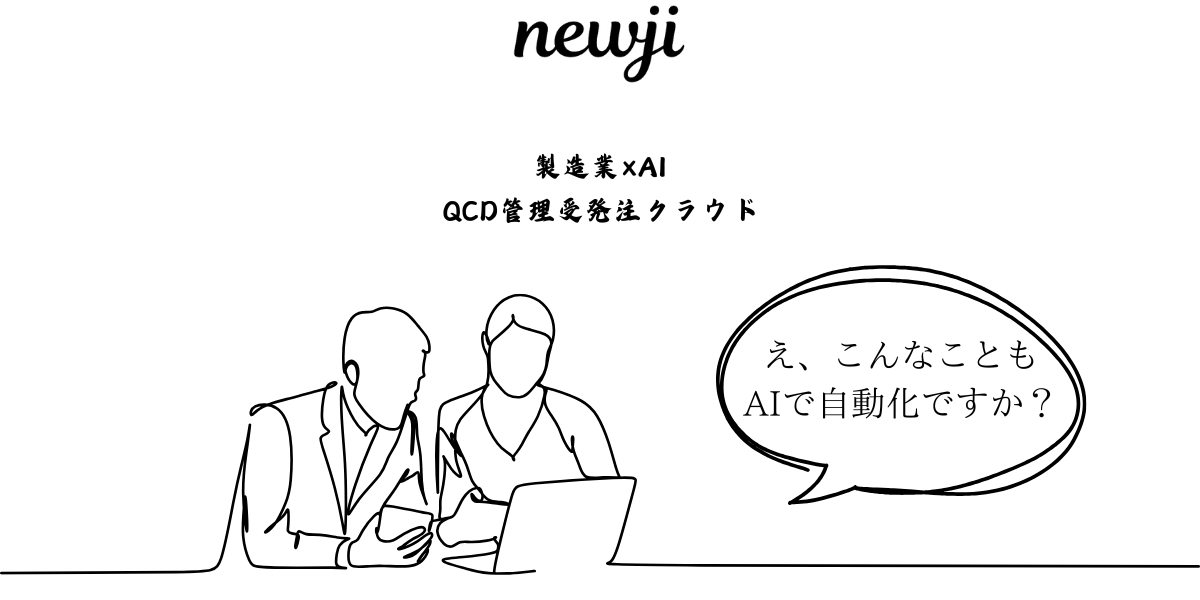
Making technical information usable using evolutionary QFD and its application to FMEA, DRBFM, quality engineering, and problem analysis
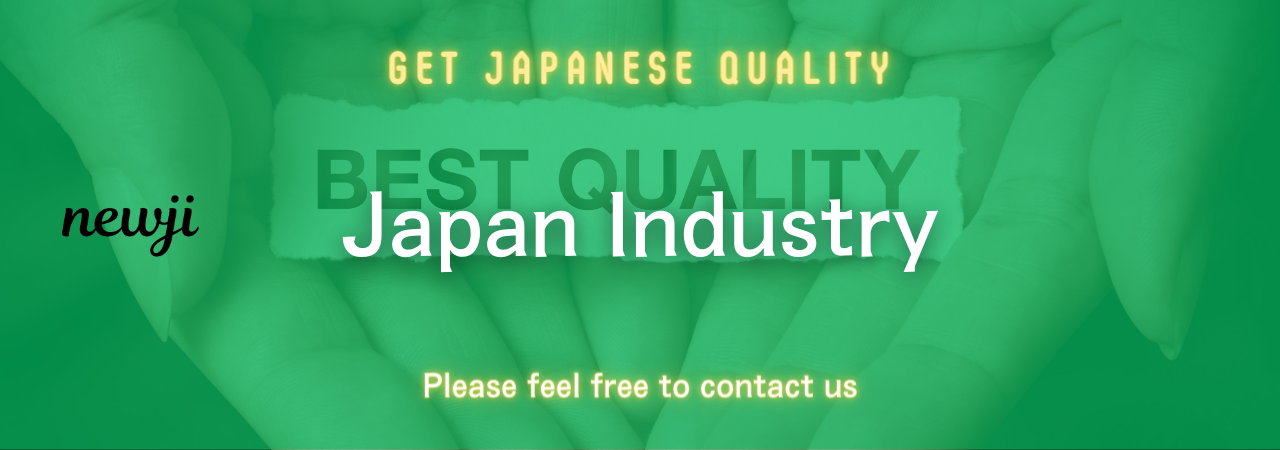
目次
Understanding the Basics of QFD
Quality Function Deployment (QFD) is a tool used in product development and quality management.
Originally developed in Japan, QFD’s primary purpose is to transform customer needs into engineering characteristics for a product or service.
This structured method helps bring clarity to communication between different departments and ensures the final product aligns closely with what customers want.
At its core, QFD utilizes a series of matrices, typically referred to as “House of Quality,” to translate vague customer desires into precise specifications.
The process involves multiple phases, including voice of the customer analysis, benchmarking, and prioritization of critical characteristics.
This approach ensures that the product or service fulfills customer expectations while maintaining technical feasibility.
The Evolution of QFD
Over the years, QFD has evolved significantly, expanding its applications beyond simple product design.
It now plays a crucial role in various functions including design for reliability, quality engineering, and even problem-solving.
This evolution has been driven by a need to address increasingly complex market demands and integrate new technologies.
The newer versions of QFD incorporate tools such as the Failure Mode and Effects Analysis (FMEA) and Design Review Based on Failure Mode (DRBFM).
These tools aid in identifying potential failures and designing preventive measures, ensuring that the product not only meets quality standards but also excels in reliability.
Furthermore, the integration of these tools highlights QFD’s adaptive nature, making it suitable for diverse sectors from automotive to electronics.
Application of QFD in FMEA
Failure Mode and Effects Analysis (FMEA) is a crucial technique for identifying and mitigating risks in product design and process development.
QFD aids in the implementation of FMEA by systematically ensuring that potential risks are evaluated early in the design phase.
By using QFD matrices, teams can identify critical failure modes through the analysis of customer requirements and product specifications.
This structured approach ensures that each potential failure is documented, along with its effects and necessary control measures.
The synergy of QFD and FMEA enhances a product’s reliability and safety by addressing risks proactively.
Moreover, by using QFD for FMEA, teams can ensure that engineering adjustments directly address customer concerns while staying aligned with the overall design goals.
This alignment not only improves customer satisfaction but also optimizes resource allocation during the development process.
Integrating QFD with DRBFM
Design Review Based on Failure Mode (DRBFM) is another methodology that benefits considerably from QFD.
DRBFM focuses on changes between new and existing designs, ensuring that each modification is thoroughly reviewed to prevent unforeseen issues.
QFD’s structured approach helps teams in DRBFM activities by emphasizing customer expectations and highlighting which product attributes are critical to quality.
These insights allow engineers to concentrate their efforts on areas most likely to impact the customer, thus tailoring modifications to enhance user experience.
Through QFD-influenced DRBFM, organizations can effectively reduce development cycles and improve overall design efficiency.
This reduction is achieved by continously keeping the customer’s needs at the forefront, thus minimizing costly redesigns and field failures.
Improving Quality Engineering Through QFD
Quality engineering is an essential part of manufacturing and production processes aimed at maximizing product performance and minimizing costs.
QFD complements quality engineering by ensuring that quality metrics are directly aligned with customer requirements.
By implementing QFD, organizations can effectively balance quality costs with customer satisfaction.
For instance, through its rigorous analysis process, QFD helps pinpoint which areas should be prioritized for quality improvements, ensuring optimal resource utilization.
Moreover, QFD aids in setting clear objectives for quality engineers by translating broad objectives into measurable design parameters.
This streamlined process fosters a culture of continuous improvement and innovation, crucial components of successful quality engineering.
Utilizing QFD for Effective Problem Analysis
Problem analysis is a critical element in any organization’s quest to maintain and enhance quality assurance.
QFD provides a robust framework for diagnosing issues by comparing customer needs against product capabilities.
Utilizing QFD in problem analysis involves identifying discrepancies and their sources, thus streamlining the troubleshooting processes.
By doing so, teams can prioritize addressing the issues that hold the greatest potential for impacting customer satisfaction and operational efficiency.
Furthermore, the complete documentation of matrices involved in QFD ensures that all team members have access to accurate and comprehensive insights, paving the way for collaborative problem-solving.
Such transparency fosters an environment where teams are more likely to identify the root causes of problems and implement long-lasting solutions.
The Future of QFD
As industries continue to grow more competitive and consumer needs evolve, the importance of utilizing comprehensive tools like QFD has never been more pronounced.
The integration of QFD with modern technologies and methodologies continues to grow, providing opportunities for further enhancements in quality assurance and product development.
By embracing the evolving capabilities of QFD, organizations can remain agile, anticipating market trends while ensuring that products align closely with customer needs.
As new challenges in product development emerge, QFD serves as a versatile instrument, empowering companies to not only adapt but thrive in an ever-changing marketplace.
資料ダウンロード
QCD調達購買管理クラウド「newji」は、調達購買部門で必要なQCD管理全てを備えた、現場特化型兼クラウド型の今世紀最高の購買管理システムとなります。
ユーザー登録
調達購買業務の効率化だけでなく、システムを導入することで、コスト削減や製品・資材のステータス可視化のほか、属人化していた購買情報の共有化による内部不正防止や統制にも役立ちます。
NEWJI DX
製造業に特化したデジタルトランスフォーメーション(DX)の実現を目指す請負開発型のコンサルティングサービスです。AI、iPaaS、および先端の技術を駆使して、製造プロセスの効率化、業務効率化、チームワーク強化、コスト削減、品質向上を実現します。このサービスは、製造業の課題を深く理解し、それに対する最適なデジタルソリューションを提供することで、企業が持続的な成長とイノベーションを達成できるようサポートします。
オンライン講座
製造業、主に購買・調達部門にお勤めの方々に向けた情報を配信しております。
新任の方やベテランの方、管理職を対象とした幅広いコンテンツをご用意しております。
お問い合わせ
コストダウンが利益に直結する術だと理解していても、なかなか前に進めることができない状況。そんな時は、newjiのコストダウン自動化機能で大きく利益貢献しよう!
(Β版非公開)