- お役立ち記事
- Failure mechanisms and failure analysis techniques for electronic components and materials and their key points
月間77,185名の
製造業ご担当者様が閲覧しています*
*2025年2月28日現在のGoogle Analyticsのデータより
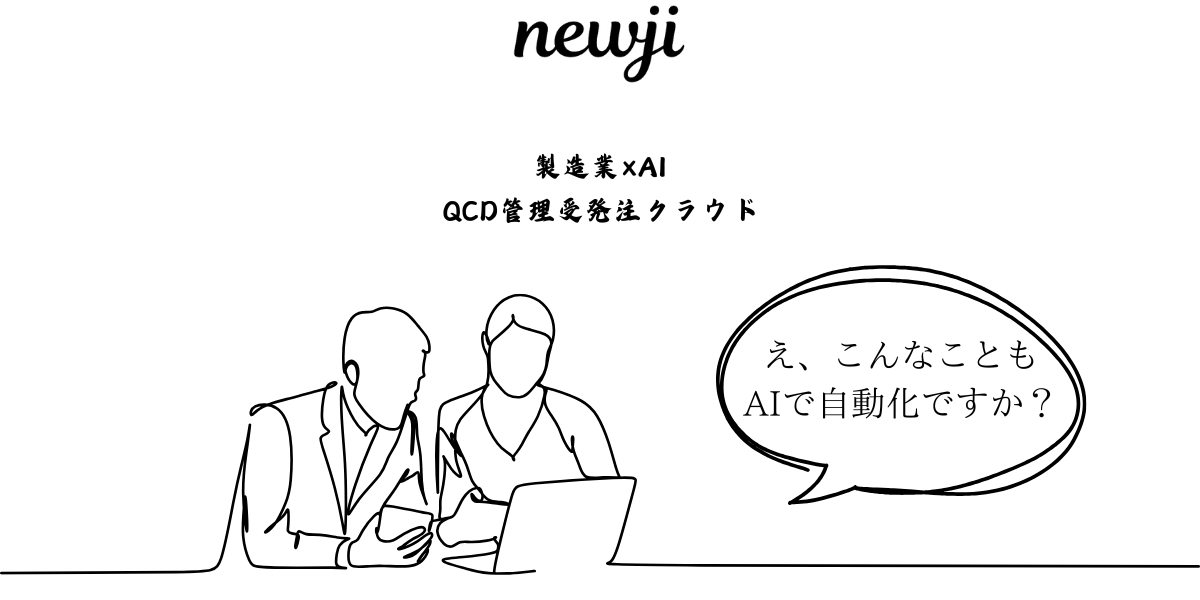
Failure mechanisms and failure analysis techniques for electronic components and materials and their key points
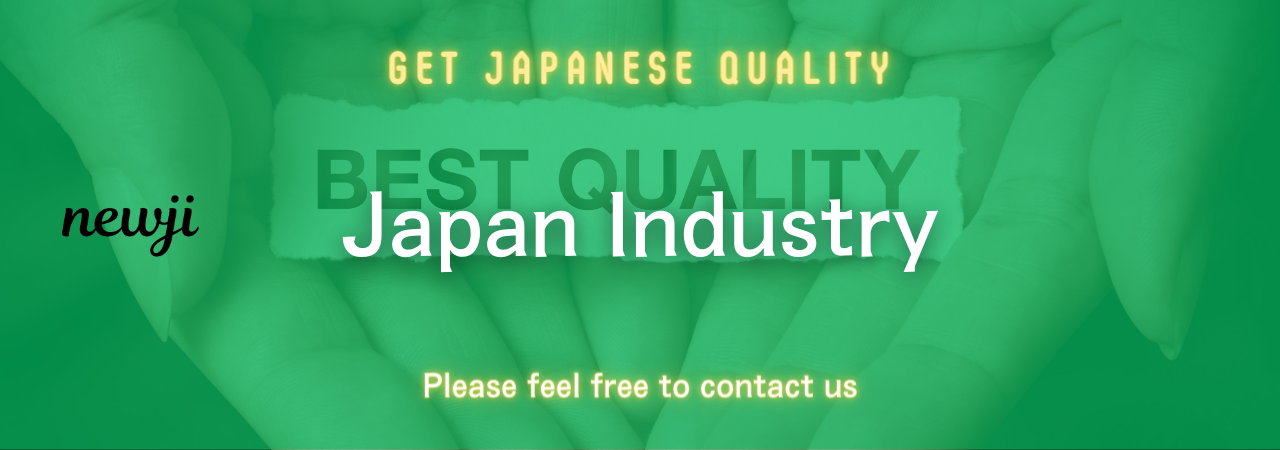
目次
Understanding Failure Mechanisms in Electronics
Electronics are an integral part of modern life, powering everything from smartphones to complex industrial machinery.
However, like all technologies, electronic components and materials can fail over time.
Understanding the failure mechanisms is crucial for enhancing device reliability, longevity, and performance.
Electronic failures can occur due to a variety of reasons.
These include environmental stress, mechanical fatigue, thermal cycling, and manufacturing defects.
Each of these factors contributes uniquely to the degradation of electronic components.
One common failure mechanism is thermal cycling.
As electronic devices operate, they undergo repeated heating and cooling.
This expansion and contraction can lead to mechanical fatigue, causing materials to crack or solder joints to weaken.
Over time, these tiny flaws can propagate, leading to complete failure of the device.
Moisture and humidity also pose significant risks to electronic components.
When exposed to humid environments, electronic materials can undergo corrosion.
This can lead to short circuits, reduced performance, or total failure of the system.
Failure Analysis Techniques
To address these failure mechanisms, engineers and scientists employ a variety of failure analysis techniques.
These tools help in diagnosing the root causes of a failure, ensuring that future designs are more robust and reliable.
Visual Inspection
The first step in failure analysis often involves a detailed visual inspection.
Using high-powered microscopes, analysts look for signs of physical damage, such as cracks or discoloration.
This examination can quickly identify obvious issues, such as burnt components or broken wires.
Scanning Electron Microscopy (SEM)
For a more in-depth analysis, Scanning Electron Microscopy (SEM) is used.
SEM provides high-resolution images of a component’s surface, revealing microscale features that are invisible to the naked eye.
It is particularly useful in identifying cracks, voids, and other imperfections that may not be apparent during a visual inspection.
X-ray Analysis
X-ray analysis is another powerful tool used in failure analysis.
It allows engineers to see through solid objects, identifying hidden defects such as internal cracks or voids.
This non-destructive technique is invaluable for examining components like integrated circuits and printed circuit boards.
Thermal Imaging
Thermal imaging is used to detect hot spots on a device, which can indicate areas of high electrical resistance or poor heat dissipation.
These hot spots are potential points of failure and can pinpoint problematic areas that need attention.
Electrical Testing
Electrical testing involves measuring the electrical properties of a component, such as resistance, capacitance, and inductance.
By comparing these measurements against the component’s specifications, engineers can determine if a device is functioning correctly or if there is a problem.
Key Points in Conducting Failure Analysis
Conducting a successful failure analysis requires careful consideration and meticulous methodology.
The following key points are essential for a comprehensive analysis:
Comprehensive Documentation
Document every step of the analysis process, including initial observations, test results, and conclusions.
This documentation is critical not only for current analysis but also for future reference and for improving product designs.
Understanding the Operating Environment
Consider the environment in which the electronic component operates.
Factors such as temperature extremes, humidity levels, and mechanical stresses can greatly influence a component’s performance and lifespan.
Use of Appropriate Techniques
Choose the right analytical techniques based on the type of failure and the component being analyzed.
For example, while visual inspection might reveal surface anomalies, internal issues might require X-ray or SEM analysis.
Interdisciplinary Approach
Failure analysis often requires insights from multiple disciplines, including materials science, electrical engineering, and mechanical engineering.
Collaborating across these fields enables a more comprehensive understanding of the failure mechanisms at play.
Learning and Iteration
Each failure analysis provides valuable lessons that can be used to improve future designs.
Adopting an iterative approach ensures continuous learning and enhancement of product reliability.
Conclusion
Failure mechanisms in electronic components are complex and multifaceted.
However, with the right failure analysis techniques, engineers can uncover the underlying causes of these failures.
By understanding these mechanisms and emphasizing key points in the analysis process, designers can create more reliable and durable electronic products.
In the fast-evolving world of electronics, staying informed about failure mechanisms and analysis techniques is essential for innovation and advancement.
資料ダウンロード
QCD管理受発注クラウド「newji」は、受発注部門で必要なQCD管理全てを備えた、現場特化型兼クラウド型の今世紀最高の受発注管理システムとなります。
ユーザー登録
受発注業務の効率化だけでなく、システムを導入することで、コスト削減や製品・資材のステータス可視化のほか、属人化していた受発注情報の共有化による内部不正防止や統制にも役立ちます。
NEWJI DX
製造業に特化したデジタルトランスフォーメーション(DX)の実現を目指す請負開発型のコンサルティングサービスです。AI、iPaaS、および先端の技術を駆使して、製造プロセスの効率化、業務効率化、チームワーク強化、コスト削減、品質向上を実現します。このサービスは、製造業の課題を深く理解し、それに対する最適なデジタルソリューションを提供することで、企業が持続的な成長とイノベーションを達成できるようサポートします。
製造業ニュース解説
製造業、主に購買・調達部門にお勤めの方々に向けた情報を配信しております。
新任の方やベテランの方、管理職を対象とした幅広いコンテンツをご用意しております。
お問い合わせ
コストダウンが利益に直結する術だと理解していても、なかなか前に進めることができない状況。そんな時は、newjiのコストダウン自動化機能で大きく利益貢献しよう!
(β版非公開)