- お役立ち記事
- Fundamentals of material mechanics and fatigue strength and how to utilize them to estimate the cause of fracture through fracture surface analysis
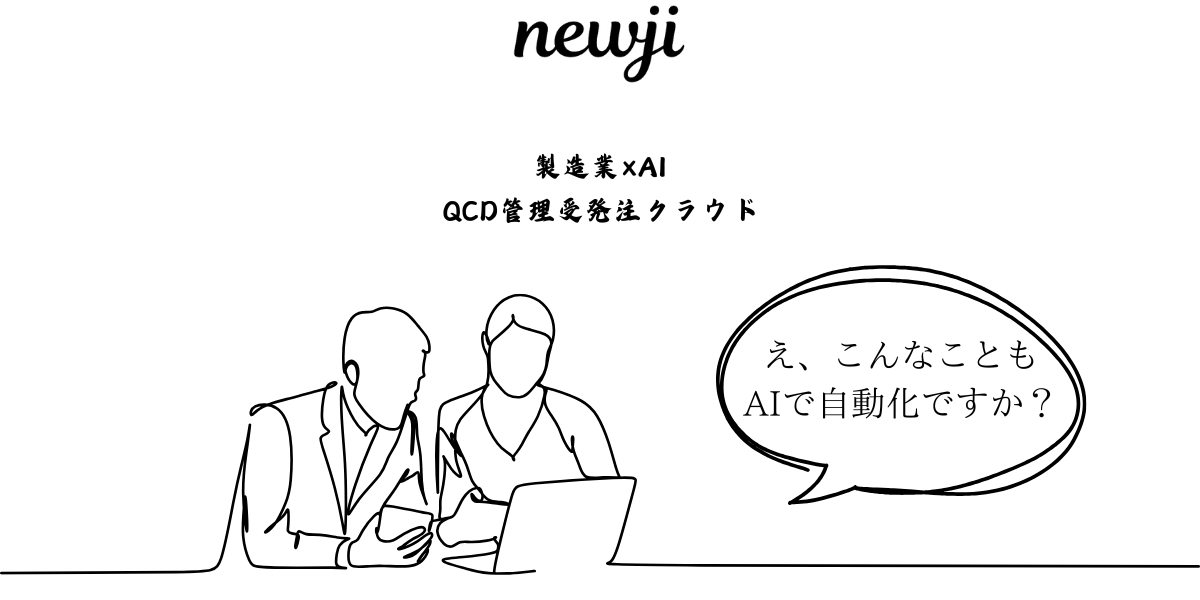
Fundamentals of material mechanics and fatigue strength and how to utilize them to estimate the cause of fracture through fracture surface analysis
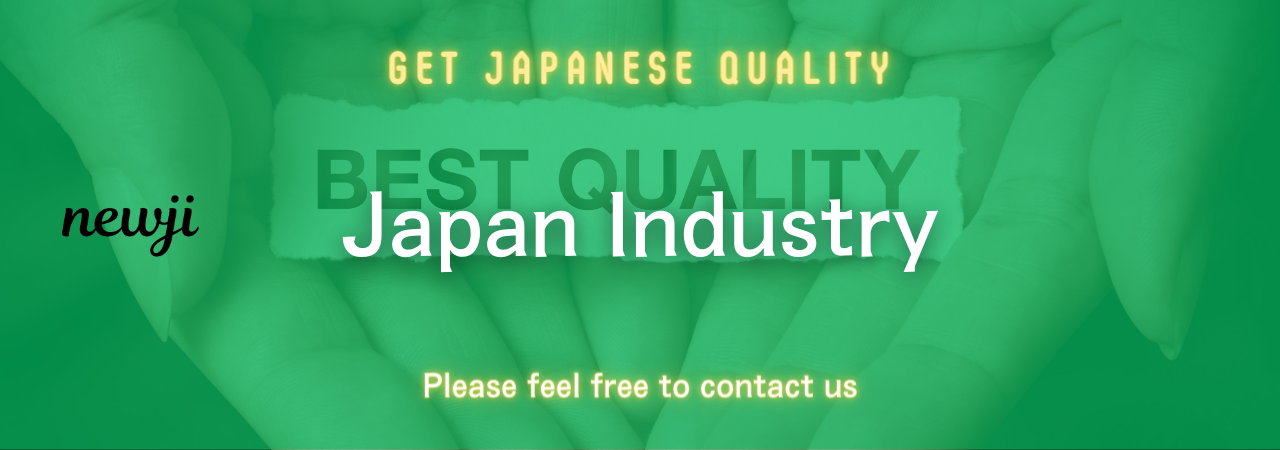
目次
Understanding Material Mechanics and Fatigue Strength
Material mechanics is a critical area of study in engineering that helps us understand how different materials respond to various forces and stresses.
Whether it’s steel in a skyscraper or the composite materials in an aircraft, knowing how materials behave under load helps engineers design safer and more efficient structures.
At the core of material mechanics are concepts related to stress, strain, and elasticity.
Stress refers to the internal forces that develop within a material when it is subjected to an external load.
Strain, on the other hand, describes the deformation or displacement that occurs as a result of these internal forces.
Elasticity is the ability of a material to return to its original shape after the load is removed.
Fatigue strength, an important aspect of material mechanics, describes a material’s ability to withstand repeated cycles of stress.
Unlike a single, overwhelming force, fatigue strength is concerned with the gradual weakening of a material over time due to small, repetitive loads.
Understanding fatigue strength is vital because the repeated application of stress can ultimately lead to material failure even if the stress is lower than the material’s ultimate tensile strength.
How Fracture Surface Analysis Helps in Estimating the Cause of Fracture
Fracture surface analysis is a technique used to determine the cause of a material’s failure by examining the surface where the fracture occurred.
When materials fail, they leave behind telltale marks that can give valuable clues about how and why the failure happened.
By analyzing the fracture surface, engineers can determine whether the failure was due to stress concentration, fatigue, or another mode of failure.
For instance, a smooth, semicircular pattern might indicate fatigue failure, where the damage accumulated over many cycles before the final break.
Conversely, a jagged and uneven surface might point toward a brittle fracture, which occurs suddenly without much prior deformation.
There are various methods employed in fracture surface analysis, including visual inspection, scanning electron microscopy (SEM), and energy-dispersive X-ray spectroscopy (EDS).
These techniques help identify not only the mode of the fracture but also the environment in which the failure occurred.
For instance, the presence of corrosion products can indicate that environmental factors contributed to the failure.
Steps to Estimate the Cause of Fracture
1. **Visual Inspection:**
Start by carefully examining the fracture surface with the naked eye or a low-power magnifying tool.
Look for characteristic features such as fracture lines, patterns, and discolorations.
This initial observation provides a basic understanding of the fracture’s characteristics.
2. **Determine Fracture Mode:**
Identify whether the fracture mode is ductile, brittle, or fatigue.
Ductile fractures show significant plastic deformation, while brittle fractures exhibit little to no deformation with a more jagged surface.
Fatigue fractures often present as smooth with distinct crack initiation points.
3. **Use Magnification Tools:**
Employ tools such as scanning electron microscopes (SEM) for detailed analysis of the microstructural features of the fracture surface.
SEM can reveal fine details that are not visible to the naked eye, allowing for precise determination of crack initiation and propagation.
4. **Chemical Analysis:**
Conduct chemical analyses like energy-dispersive X-ray spectroscopy (EDS) to detect the presence of foreign substances or corrosion byproducts that might have contributed to the failure.
This step can help connect environmental factors to the failure mechanism.
5. **Compare with Known Failure Cases:**
Compare the findings with documented cases of similar failures.
This comparative analysis can highlight if the observed failure is part of a known failure type or if it’s an unusual occurrence requiring further investigation.
6. **Simulate the Conditions:**
If possible, replicate the original conditions leading to failure in a controlled laboratory setting.
This can confirm the hypothesis formulated from the fracture surface analysis and provide further insight into the material’s behavior.
Applications and Implications of Fracture Surface Analysis
Fracture surface analysis is a powerful tool used across various industries, including aerospace, automotive, construction, and manufacturing.
By accurately determining the cause of a material failure, engineers and researchers can prevent future failures, improve design, and enhance safety.
In aerospace, for instance, understanding fatigue failures in turbine blades can prevent catastrophic engine failures.
In the automotive industry, analyzing fractures in critical components like axles can lead to better designs that improve vehicle reliability and safety.
Moreover, the insights gained from fracture analysis contribute to the development of new materials with improved mechanical properties.
By understanding how and why materials fail, engineers can push the boundaries of material science, creating materials that are stronger, lighter, and more resistant to environmental factors.
Conclusion
Material mechanics and fatigue strength are fundamental concepts that play an essential role in designing and maintaining the safety and reliability of various structures and components.
When coupled with fracture surface analysis, these principles provide a robust framework for understanding material failures and their causes.
Through careful observation and detailed analysis, engineers can not only identify the underlying reasons for material failures but also develop more effective and efficient materials and designs.
This process ensures safety, reliability, and innovation across industries, making our world safer and more sustainable.
資料ダウンロード
QCD調達購買管理クラウド「newji」は、調達購買部門で必要なQCD管理全てを備えた、現場特化型兼クラウド型の今世紀最高の購買管理システムとなります。
ユーザー登録
調達購買業務の効率化だけでなく、システムを導入することで、コスト削減や製品・資材のステータス可視化のほか、属人化していた購買情報の共有化による内部不正防止や統制にも役立ちます。
NEWJI DX
製造業に特化したデジタルトランスフォーメーション(DX)の実現を目指す請負開発型のコンサルティングサービスです。AI、iPaaS、および先端の技術を駆使して、製造プロセスの効率化、業務効率化、チームワーク強化、コスト削減、品質向上を実現します。このサービスは、製造業の課題を深く理解し、それに対する最適なデジタルソリューションを提供することで、企業が持続的な成長とイノベーションを達成できるようサポートします。
オンライン講座
製造業、主に購買・調達部門にお勤めの方々に向けた情報を配信しております。
新任の方やベテランの方、管理職を対象とした幅広いコンテンツをご用意しております。
お問い合わせ
コストダウンが利益に直結する術だと理解していても、なかなか前に進めることができない状況。そんな時は、newjiのコストダウン自動化機能で大きく利益貢献しよう!
(Β版非公開)