- お役立ち記事
- Product design that takes into account the basics and workability of press working and molds, and effective defect countermeasures.
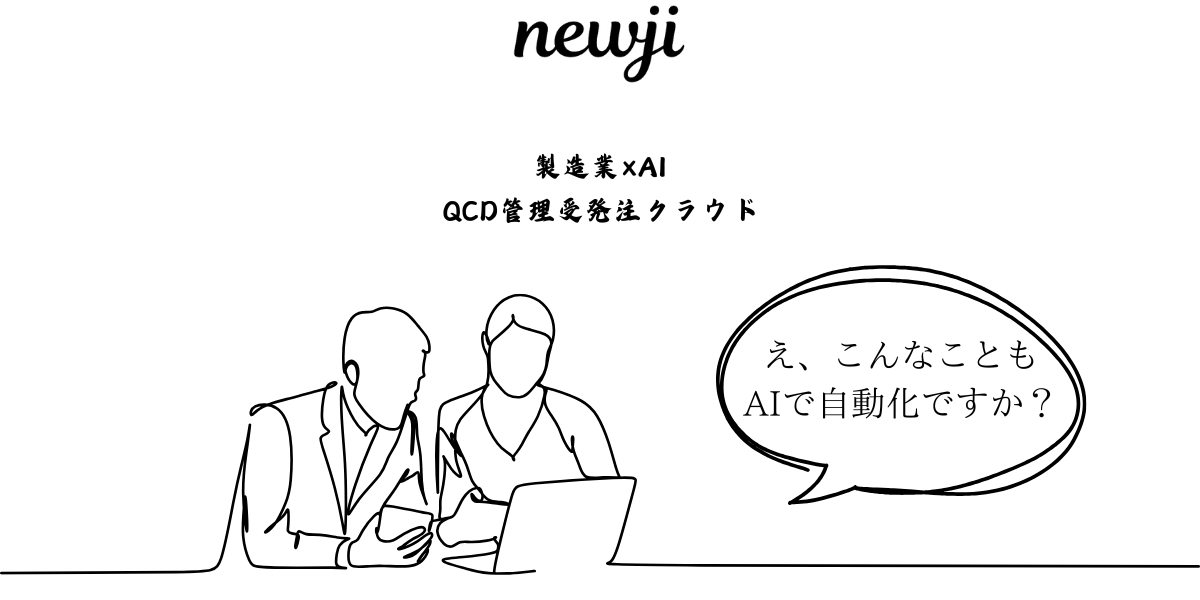
Product design that takes into account the basics and workability of press working and molds, and effective defect countermeasures.
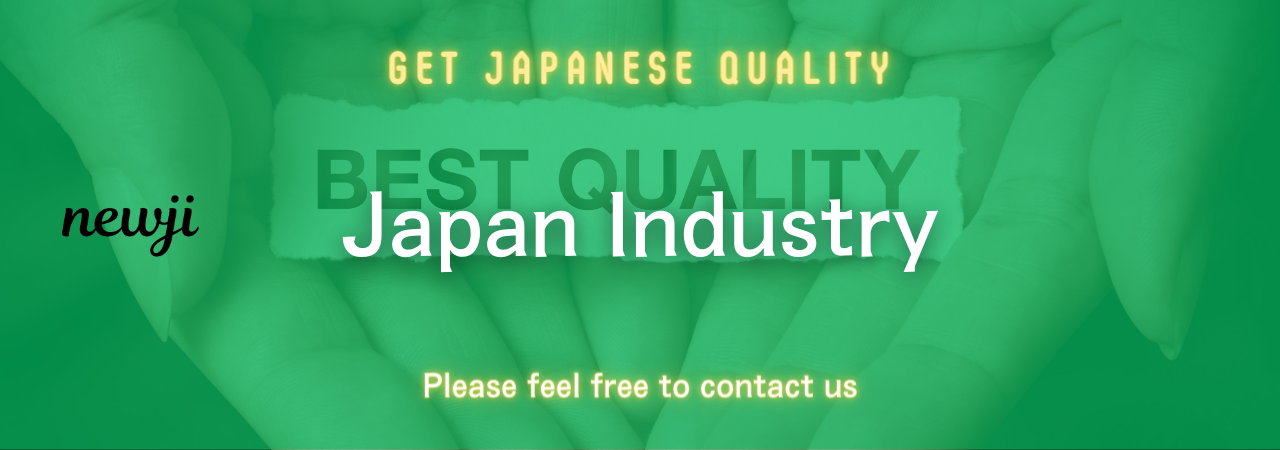
目次
Understanding Press Working and Molds
When it comes to product design, one of the most crucial aspects to consider is how your design will be brought to life through manufacturing processes like press working and mold creation.
Press working involves shaping metal sheets into specific forms using a press machine. This method is highly efficient and cost-effective for mass production, making it essential for many industries.
Molds, on the other hand, are used primarily in injection molding, where materials like plastic are shaped. The mold itself is the tool that determines the final shape of the product.
Having a thorough understanding of these processes allows designers to create products that are not only aesthetically pleasing but also feasible and reliable in production.
The Basics of Press Working
Press working, or stamping, consists of several steps including cutting, bending, and drawing. These steps are performed using a press machine and a die to transform flat metal sheets into three-dimensional parts.
The basic operations in press working are:
– **Cutting:** This involves shearing the metal into the desired blank shape.
– **Bending:** The metal is bent at certain angles to create contours.
– **Drawing:** The metal sheet is stretched into a cavity to create hollow-shaped parts.
Each of these processes requires precision tools and machinery to ensure that the end product meets the desired specifications.
Moreover, understanding material properties is key, as different metals react differently under pressure and heat.
Types of Press Machines
Press machines come in various types, all serving different purposes in the press working process.
These include:
– **Mechanical Presses:** Known for their speed and repeatability, ideal for high-volume production.
– **Hydraulic Presses:** Offer high force through hydraulic cylinders, used for deep-drawing operations.
– **Pneumatic Presses:** Suitable for applications requiring moderate force and speed.
Each machine type has its advantages and considerations, and selecting the right one for a specific task is paramount for efficient production.
Mold Design Fundamentals
In injection molding, the mold is the centerpiece of the process. It directly affects the shape, quality, and consistency of the final product.
Mold design should focus on several critical elements, including:
– **Material Selection:** The mold material should be durable and compatible with the product material.
– **Cooling Channels:** Adequate cooling is essential to ensure even solidification, reducing defects.
– **Ejection System:** Proper ejection ensures that the product is released without damage or distortion.
By addressing these fundamentals, designers can ensure that the mold effectively shapes the product to meet design specifications.
Common Mold Types
Molds vary depending on the production requirements. Common types include:
– **Single-cavity Molds:** Designed to produce one part per cycle, used for custom or low-volume production.
– **Multi-cavity Molds:** Allow for multiple parts in a single cycle, suitable for high-volume manufacturing.
– **Family Molds:** Consist of multiple cavities for different parts in a single cycle, often used for product kits.
Choosing the appropriate mold type is vital for optimizing production efficiency and cost-effectiveness.
Effective Defect Countermeasures
Both press working and mold processes can encounter defects which impact the quality and functionality of the final product. Identifying and addressing potential defects early in the design phase is key.
For Press Working
Common defects in press working include:
– **Cracks:** Often due to excessive stress or improper material selection.
– **Wrinkling:** Resulting from insufficient material flow or inappropriate die design.
– **Springback:** Material’s tendency to return to original shape after bending, affecting precision.
Countermeasures include:
– **Material Testing:** Choose materials with appropriate ductility and strength.
– **Simulation Software:** Use tools to predict how materials will behave and adjust designs accordingly.
– **Die Maintenance:** Regular inspection and maintenance ensure machinery precision and accuracy.
For Mold Processes
Defects in molded products can include:
– **Warpage:** Parts deforming after release, often due to uneven cooling.
– **Sink Marks:** Surface depressions caused by improper cooling rates.
– **Short Shots:** Incomplete fills in the mold cavity, resulting from insufficient material flow.
Effective strategies to counter mold defects include:
– **Optimizing Mold Design:** Ensure uniform cooling and efficient material flow.
– **Quality Control Measures:** Implement thorough inspection processes to capture defects early.
– **Process Parameter Monitoring:** Regularly observe and adjust temperatures, pressures, and cycle times for consistency.
Integrating Design and Manufacturing
Designing with both product aesthetics and manufacturing feasibility in mind results in better-functioning products that meet client expectations.
Integrating the design process with knowledge of press working and molding can lead to improved product designs that are easier to manufacture, less costly, and exhibit fewer defects.
Collaborate closely with engineers and manufacturers during the product development process to ensure all aspects of design align with the chosen manufacturing techniques.
Keeping communication open and ongoing helps in foreseeing potential issues and adjusting designs accordingly before production begins.
Incorporating these principles into your product design process helps achieve a balance between innovation and manufacturability, ultimately leading to successful, high-quality products in the market.
資料ダウンロード
QCD調達購買管理クラウド「newji」は、調達購買部門で必要なQCD管理全てを備えた、現場特化型兼クラウド型の今世紀最高の購買管理システムとなります。
ユーザー登録
調達購買業務の効率化だけでなく、システムを導入することで、コスト削減や製品・資材のステータス可視化のほか、属人化していた購買情報の共有化による内部不正防止や統制にも役立ちます。
NEWJI DX
製造業に特化したデジタルトランスフォーメーション(DX)の実現を目指す請負開発型のコンサルティングサービスです。AI、iPaaS、および先端の技術を駆使して、製造プロセスの効率化、業務効率化、チームワーク強化、コスト削減、品質向上を実現します。このサービスは、製造業の課題を深く理解し、それに対する最適なデジタルソリューションを提供することで、企業が持続的な成長とイノベーションを達成できるようサポートします。
オンライン講座
製造業、主に購買・調達部門にお勤めの方々に向けた情報を配信しております。
新任の方やベテランの方、管理職を対象とした幅広いコンテンツをご用意しております。
お問い合わせ
コストダウンが利益に直結する術だと理解していても、なかなか前に進めることができない状況。そんな時は、newjiのコストダウン自動化機能で大きく利益貢献しよう!
(Β版非公開)