- お役立ち記事
- Lifespan evaluation and end-of-life evaluation to prevent breakdowns and accidents of electrical and electronic equipment and how to utilize them for reliability and safety design
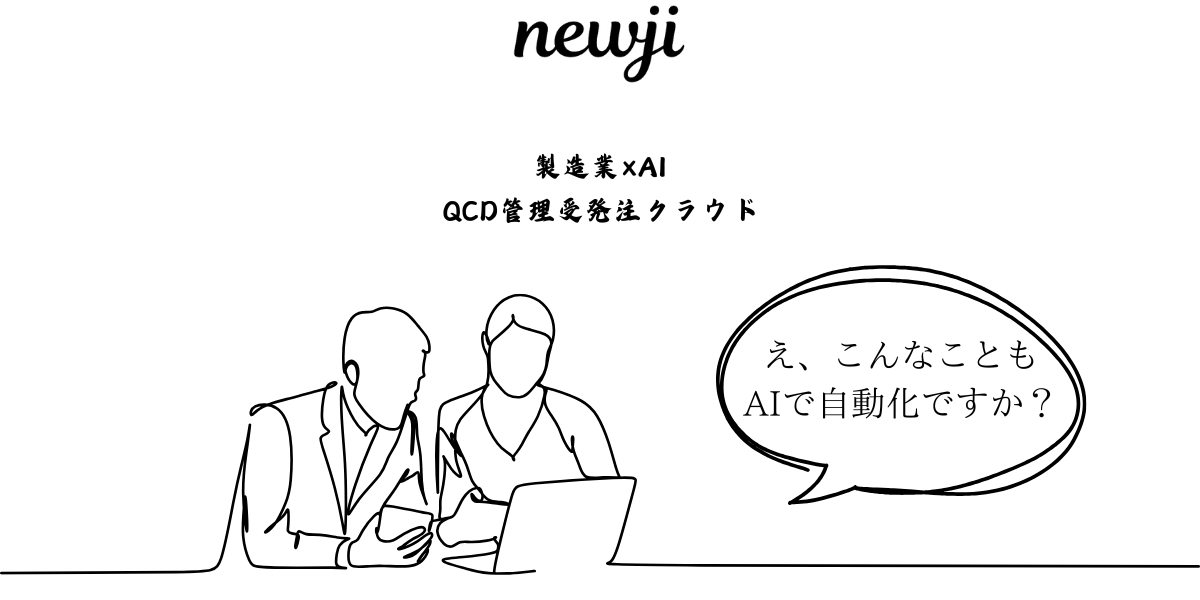
Lifespan evaluation and end-of-life evaluation to prevent breakdowns and accidents of electrical and electronic equipment and how to utilize them for reliability and safety design
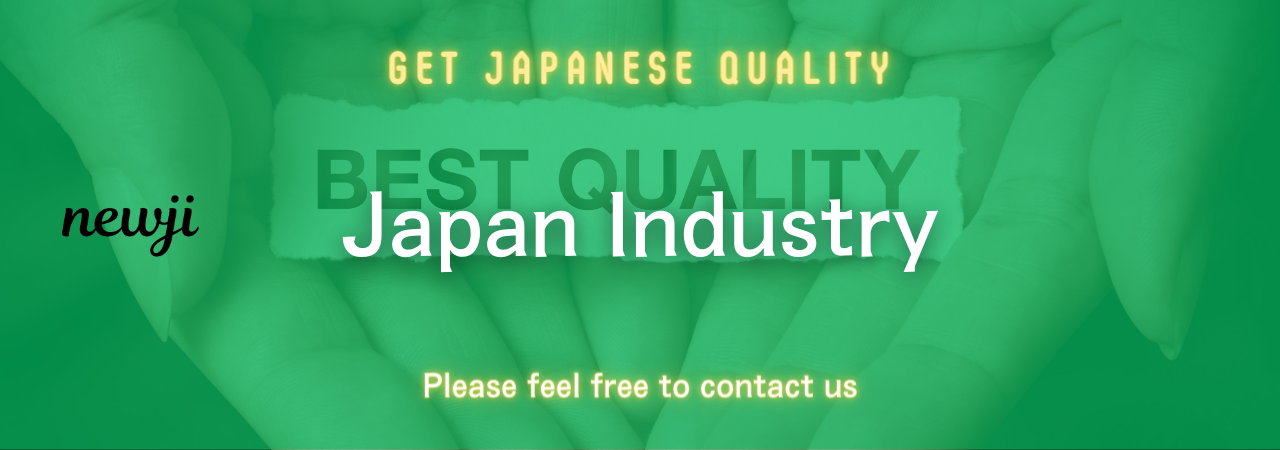
目次
Understanding Lifespan Evaluation of Electrical Equipment
Lifespan evaluation is a crucial aspect of maintaining electrical and electronic equipment effectively.
By understanding how long equipment is expected to function optimally, manufacturers and users can plan maintenance, replacements, and end-of-life strategies to avoid unexpected failures.
Lifespan evaluation involves testing equipment under various conditions to predict when and how it might fail.
This helps in understanding the durability and reliability of the equipment.
The process usually examines several factors, including environmental influences, operational stress, and material degradation over time.
One common method of lifespan evaluation is accelerated life testing.
This process subjects equipment to increased stress levels to mimic the wear and tear that would occur over an extended period.
By doing this, engineers can identify potential weaknesses and failure points before they occur in real-world scenarios.
Understanding lifespan allows manufacturers to design equipment with a clear end-of-life timeline.
This timeline helps businesses and consumers plan for replacements, ensuring continuity of service and minimizing the risk of unexpected breakdowns.
End-of-Life Evaluation in Preventing Accidents
End-of-life evaluation is another vital component in ensuring safety and reliability in electrical and electronic equipment.
It deals with assessing when a product has reached or is approaching the end of its useful life.
At this stage, the risk of failure and safety hazards increases significantly if not managed correctly.
Effective end-of-life evaluation helps in planning the decommissioning or replacement of equipment before it becomes a hazard.
It considers factors like the condition of components, the history of use, and any incidents of malfunction or repair.
This evaluation process also includes a comprehensive inspection of the equipment to identify any signs of wear or potential failure.
Equipment nearing its end of life may exhibit signs such as unusual noises, overheating, decreased performance, or visible damage.
Spotting these signs early ensures that preventive measures can be taken to avoid accidents.
The end-of-life evaluation also guides the safe disposal or recycling of electrical equipment.
Proper disposal ensures that hazardous materials are not discarded improperly, preventing environmental pollution and complying with legal regulations.
Integrating Lifespan and End-of-Life Evaluations into Design
For manufacturers, integrating lifespan and end-of-life evaluations into the design phase is fundamental to producing safe and reliable equipment.
These evaluations provide crucial data that inform design choices that enhance product robustness and longevity.
By considering lifespan evaluations, designers can select materials that better withstand environmental conditions and stresses.
This proactive approach reduces the likelihood of premature failures and extends the equipment’s functional lifespan.
Additionally, end-of-life evaluations inform designers about the risks associated with aging components.
With this knowledge, manufacturers can create designs that allow for easier maintenance and part replacements, further improving the safety and reliability of the equipment.
Another important aspect is designing for sustainability.
As products approach their end of life, they should be easier to recycle or dispose of safely.
This requirement leads to using materials that are less harmful to the environment and creating components that can be separated and processed for recycling.
By embedding these evaluations in the design phase, manufacturers not only improve product safety but also enhance customer trust and satisfaction.
Utilizing Evaluations for Reliability and Safety
For any business that relies on electrical and electronic equipment, utilizing lifespan and end-of-life evaluations is key to ensuring reliability and safety.
These evaluations enable informed decision-making regarding maintenance schedules, part replacements, and equipment upgrades.
Businesses can implement predictive maintenance strategies based on lifespan data, where equipment is serviced only when necessary instead of on a fixed schedule.
This approach increases equipment uptime and reduces maintenance costs by preventing unnecessary servicing.
End-of-life evaluations are particularly useful for industries where equipment failure could lead to significant safety hazards.
By identifying equipment that is near the end of its life, businesses can take preemptive measures to replace or upgrade it, reducing the risk of accidents and operational interruptions.
Moreover, these evaluations aid in risk management, as understanding equipment life cycles allows for better contingency planning and resource allocation.
This preparedness ensures minimal disruption in operations and enhances the overall safety of the workplace.
The Broader Impact on Industry Standards
Lifespan and end-of-life evaluations have a significant influence on industry standards and regulations.
They provide a scientific basis for developing standards that ensure the safety, reliability, and environmental sustainability of electrical products.
These evaluations help establish criteria for testing equipment durability, performance under stress, and safety during decommissioning.
As a result, they contribute to creating standards that manufacturers must comply with to enter or remain in the market.
Furthermore, these evaluations support the advancement of technology by providing feedback that can drive innovation.
For example, identifying common failure modes can encourage the development of new materials or designs that overcome existing limitations.
In essence, lifespan and end-of-life evaluations are integral to advancing the safety, reliability, and environmental responsibility of the electrical and electronic industries.
They not only protect users and the environment but also enhance the quality and sustainability of modern technology.
資料ダウンロード
QCD調達購買管理クラウド「newji」は、調達購買部門で必要なQCD管理全てを備えた、現場特化型兼クラウド型の今世紀最高の購買管理システムとなります。
ユーザー登録
調達購買業務の効率化だけでなく、システムを導入することで、コスト削減や製品・資材のステータス可視化のほか、属人化していた購買情報の共有化による内部不正防止や統制にも役立ちます。
NEWJI DX
製造業に特化したデジタルトランスフォーメーション(DX)の実現を目指す請負開発型のコンサルティングサービスです。AI、iPaaS、および先端の技術を駆使して、製造プロセスの効率化、業務効率化、チームワーク強化、コスト削減、品質向上を実現します。このサービスは、製造業の課題を深く理解し、それに対する最適なデジタルソリューションを提供することで、企業が持続的な成長とイノベーションを達成できるようサポートします。
オンライン講座
製造業、主に購買・調達部門にお勤めの方々に向けた情報を配信しております。
新任の方やベテランの方、管理職を対象とした幅広いコンテンツをご用意しております。
お問い合わせ
コストダウンが利益に直結する術だと理解していても、なかなか前に進めることができない状況。そんな時は、newjiのコストダウン自動化機能で大きく利益貢献しよう!
(Β版非公開)