- お役立ち記事
- “Exploring Japan’s Manufacturing Mastery: How ‘Frequency Response’ Shapes Innovative Technologies”
月間77,185名の
製造業ご担当者様が閲覧しています*
*2025年2月28日現在のGoogle Analyticsのデータより
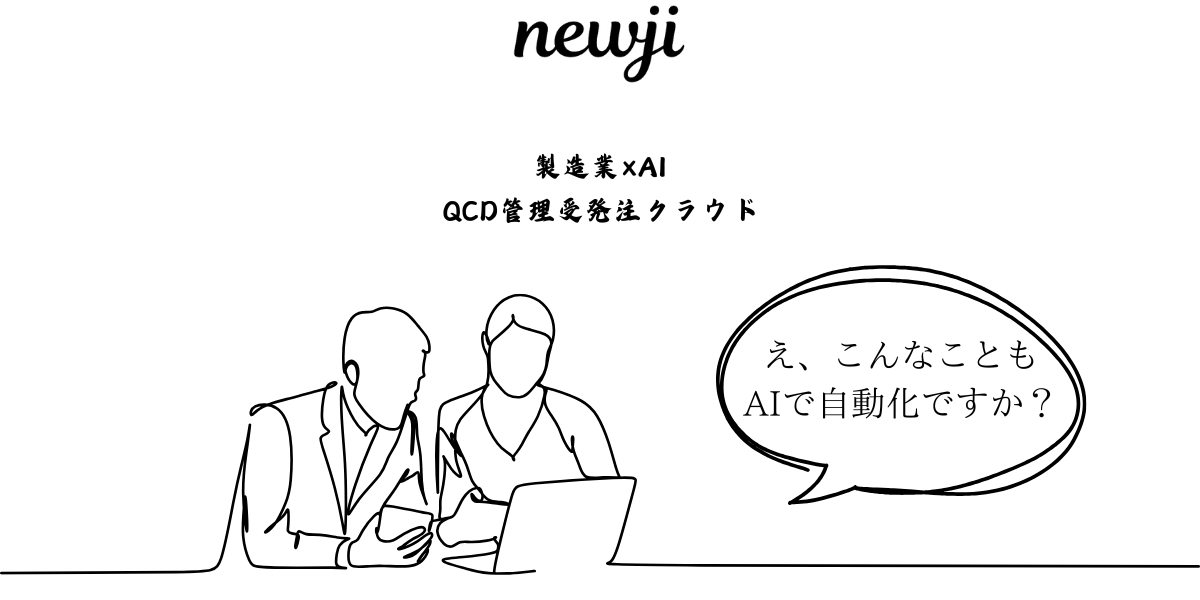
“Exploring Japan’s Manufacturing Mastery: How ‘Frequency Response’ Shapes Innovative Technologies”
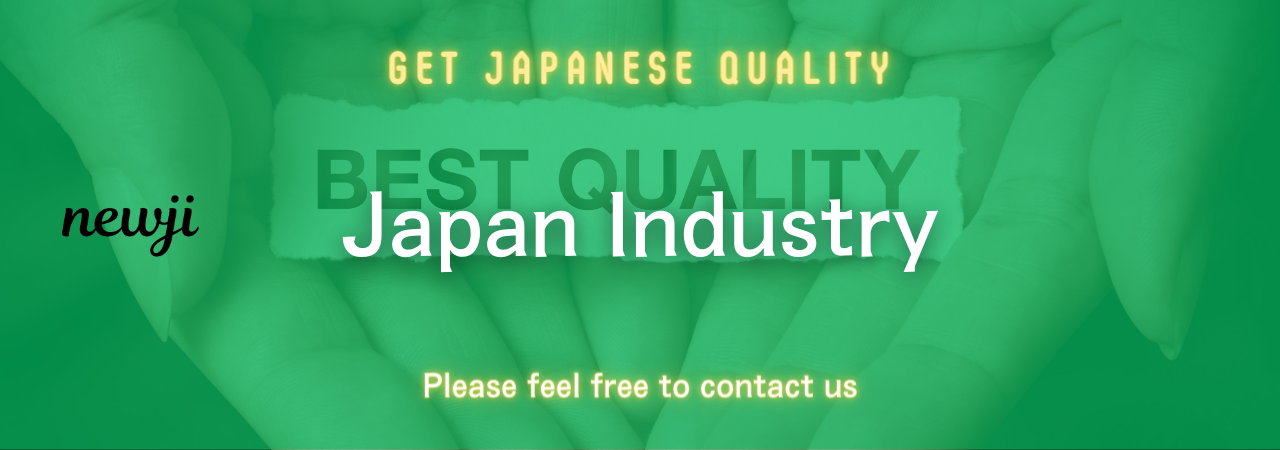
目次
Understanding Frequency Response in Manufacturing
Frequency response is a critical concept in various manufacturing processes, particularly in industries that rely on precision and high-performance technologies. It refers to the ability of a system or component to accurately respond to different frequencies of input signals. In manufacturing, this concept is essential for ensuring that machinery and equipment operate efficiently and produce products that meet stringent quality standards.
Definition and Importance
Frequency response essentially measures how a system reacts to different frequencies of input. In the context of manufacturing, this could pertain to the performance of machinery, control systems, or electronic components used in production lines. A system with a well-characterized frequency response can predictably handle varying operational conditions, leading to more reliable and consistent manufacturing outcomes.
The importance of frequency response in manufacturing cannot be overstated. It directly impacts the precision and quality of the products being manufactured. For instance, in industries like automotive or aerospace, where even minor deviations can lead to significant issues, understanding and optimizing frequency response is crucial. It ensures that machinery can handle dynamic loads and operational speeds without compromising on performance or safety.
Applications in Modern Technologies
Modern manufacturing technologies, such as automation and robotics, heavily rely on precise control systems that utilize frequency response principles. These systems must respond accurately to control signals to perform tasks like material handling, assembly, and quality inspection. Additionally, in semiconductor manufacturing, frequency response plays a role in the precision of equipment used for processes like lithography and etching.
Another significant application is in the field of vibration analysis. Manufacturing equipment often generates vibrations that can affect the quality of products and the lifespan of machinery. By analyzing the frequency response of these systems, manufacturers can identify and mitigate sources of unwanted vibrations, leading to smoother operations and reduced maintenance costs.
Japanese Manufacturing Prowess
Japan has long been recognized as a leader in the manufacturing sector, known for its commitment to quality, innovation, and efficiency. The country’s manufacturing excellence is driven by its emphasis on continuous improvement, known as Kaizen, and its ability to integrate advanced technologies into production processes.
Historical Overview
Japan’s rise in the manufacturing world began post-World War II, as the country focused on rebuilding its economy through industrial growth. Companies like Toyota, Sony, and Mitsubishi became global symbols of quality and reliability. Japan’s dedication to refining manufacturing processes, investing in research and development, and fostering a skilled workforce solidified its position in the global market.
Current Market Leaders
Today, Japanese manufacturers continue to lead in various sectors, including automotive, electronics, machinery, and robotics. Companies like Toyota and Honda dominate the automotive industry with their innovative manufacturing techniques and commitment to quality. In electronics, firms like Panasonic and Sony are renowned for their cutting-edge products and technological advancements. Additionally, Japan remains at the forefront of robotics and automation, developing sophisticated systems used worldwide.
The Role of Frequency Response in Japanese Innovations
Japanese manufacturers have effectively leveraged frequency response principles to enhance their technological capabilities and maintain their competitive edge in the global market. This integration has been pivotal in areas such as electronics manufacturing and production engineering.
Integration in Electronics Manufacturing
In the electronics sector, precise control over frequency response is essential for producing high-quality components. Japanese manufacturers utilize advanced frequency response analysis to design and test electronic devices, ensuring they meet stringent performance criteria. This meticulous approach allows for the development of reliable and efficient products, from consumer electronics to industrial equipment.
For example, in the production of semiconductors, frequency response plays a crucial role in the performance of lithography machines. These machines must operate with extreme precision to create intricate patterns on silicon wafers. By optimizing the frequency response of their equipment, Japanese manufacturers can achieve higher yields and better-quality semiconductor devices.
Enhancements in Production Engineering
Production engineering in Japan benefits significantly from a deep understanding of frequency response. In manufacturing environments, machinery and equipment must handle various operational frequencies without degradation in performance. Japanese engineers design production systems that incorporate frequency response analysis to ensure stability and efficiency.
This approach is evident in the robotics industry, where precision and reliability are paramount. By optimizing the frequency response of robotic joints and control systems, Japanese manufacturers can produce robots that perform complex tasks with high accuracy and minimal error. This level of precision is essential in industries like automotive assembly, where even slight deviations can impact the final product’s quality.
Procurement and Purchasing from Japanese Suppliers
Engaging with Japanese suppliers offers numerous advantages for international manufacturing companies. However, it also presents certain challenges that must be navigated carefully to maximize the benefits of such partnerships.
Advantages and Benefits
Japanese suppliers are renowned for their commitment to quality and reliability. They adhere to strict manufacturing standards and continuously strive for excellence through methodologies like Total Quality Management (TQM) and Kaizen. This ensures that the components and machinery procured from Japanese partners meet high-performance criteria and contribute to the overall efficiency of the manufacturing process.
Another significant advantage is the technological innovation that Japanese suppliers bring to the table. Collaborating with these suppliers allows manufacturers to access cutting-edge technologies and incorporate advanced features into their products. Additionally, Japanese companies often provide comprehensive support services, including technical assistance and training, which can enhance the capabilities of the purchasing company’s workforce.
Potential Challenges
Despite the numerous benefits, procuring from Japanese suppliers can present challenges. One such challenge is the language barrier, which can complicate communication and negotiations. Cultural differences in business practices and decision-making processes may also pose hurdles, requiring patience and adaptability from international buyers.
Another potential issue is the cost. Japanese suppliers may charge higher prices for their products and services compared to their counterparts in other regions. However, this cost can often be justified by the superior quality and reliability of the products. Additionally, the long-term benefits of reduced maintenance and higher efficiency can offset the initial investment.
Supplier Negotiation Techniques
Effective negotiation with Japanese suppliers is essential for building strong, mutually beneficial relationships. Understanding their business culture and employing strategic negotiation techniques can lead to successful partnerships.
Building Strong Relationships
In Japan, building trust and establishing personal relationships are fundamental to successful business interactions. Manufacturers seeking to procure from Japanese suppliers should invest time in developing these relationships. This can involve regular visits, participating in joint projects, and showing genuine interest in the supplier’s operations and goals.
Respect for hierarchy and formality in communication are also important. Negotiations are often conducted with senior representatives, and decisions may take longer due to the consensus-driven approach typical in Japanese businesses. Patience and a respectful demeanor can go a long way in fostering a positive negotiating environment.
Leveraging Frequency Response Capabilities
When negotiating with suppliers, highlighting the importance of frequency response in your manufacturing processes can be a strategic advantage. Demonstrating a deep understanding of this concept and its impact on your operations can position your company as a knowledgeable and serious partner.
Emphasizing how the supplier’s expertise in frequency response can enhance your product quality and operational efficiency can lead to more favorable terms. Additionally, discussing potential collaborations on frequency response optimization can open avenues for innovation and joint development projects, strengthening the partnership further.
Market Conditions and Best Practices
Navigating the dynamic landscape of global manufacturing requires staying abreast of market conditions and adhering to best practices in procurement and purchasing.
Navigating Market Trends
Japanese manufacturers are often leaders in anticipating and setting market trends. By closely monitoring these trends, international companies can align their procurement strategies to benefit from the latest advancements. This proactive approach ensures that the products and components sourced from Japan remain competitive and meet evolving industry standards.
Understanding the economic and geopolitical factors that influence the Japanese market is also crucial. Factors such as exchange rates, trade policies, and supply chain disruptions can impact procurement decisions. Staying informed and adaptable allows companies to mitigate risks and capitalize on opportunities as they arise.
Ensuring Quality Control
Maintaining high-quality standards is paramount when procuring from Japanese suppliers. Implementing robust quality control measures throughout the procurement process helps ensure that the received products meet the required specifications. This can involve setting stringent quality criteria, conducting regular inspections, and establishing clear communication channels for addressing quality issues.
Collaborating closely with suppliers to implement continuous improvement practices can further enhance quality control. By fostering a culture of shared responsibility for quality, both parties can work together to identify and resolve issues promptly, leading to better overall outcomes.
Best Practices in Procurement from Japan
Adhering to best practices in procurement not only facilitates smoother transactions but also strengthens long-term relationships with Japanese suppliers. These practices encompass strategic planning, effective communication, and continuous improvement.
Strategic Planning
Developing a clear procurement strategy is essential for successfully sourcing from Japanese suppliers. This involves identifying the specific products or components needed, understanding the supplier landscape, and setting realistic goals and timelines. Strategic planning helps in aligning procurement activities with overall business objectives, ensuring that the sourcing efforts contribute to the company’s success.
Additionally, conducting thorough market research to understand the capabilities and strengths of potential suppliers can aid in making informed decisions. Evaluating factors such as supplier reputation, technological expertise, and financial stability is crucial for selecting partners that can reliably meet the company’s needs.
Effective Communication
Clear and consistent communication is vital for successful procurement from Japan. Establishing effective communication channels, such as regular meetings, detailed documentation, and prompt feedback mechanisms, helps in minimizing misunderstandings and ensuring that both parties are aligned in their objectives.
Utilizing advanced communication tools and platforms can facilitate real-time interactions and information sharing. Additionally, employing bilingual staff or translators can bridge language gaps, enhancing the clarity and efficiency of communications.
Continuous Improvement
Embracing a mindset of continuous improvement is key to maintaining a successful procurement relationship with Japanese suppliers. This involves regularly reviewing and refining procurement processes, seeking feedback from suppliers, and implementing best practices to enhance efficiency and effectiveness.
Collaborating on innovation projects and sharing insights can lead to mutual growth and the development of more advanced products and technologies. By fostering a culture of continuous improvement, companies can ensure that their procurement strategies remain relevant and competitive in the ever-evolving manufacturing landscape.
Conclusion
Japan’s manufacturing mastery, underpinned by principles like frequency response, continues to shape innovative technologies across various industries. By understanding and leveraging these concepts, international manufacturers can enhance their own processes and products. Effective procurement and purchasing strategies, combined with strong supplier relationships and adherence to best practices, enable companies to reap the benefits of partnering with Japanese suppliers. As the global market evolves, maintaining a focus on quality, innovation, and continuous improvement will be essential for sustaining competitive advantage and achieving long-term success in manufacturing.
資料ダウンロード
QCD管理受発注クラウド「newji」は、受発注部門で必要なQCD管理全てを備えた、現場特化型兼クラウド型の今世紀最高の受発注管理システムとなります。
ユーザー登録
受発注業務の効率化だけでなく、システムを導入することで、コスト削減や製品・資材のステータス可視化のほか、属人化していた受発注情報の共有化による内部不正防止や統制にも役立ちます。
NEWJI DX
製造業に特化したデジタルトランスフォーメーション(DX)の実現を目指す請負開発型のコンサルティングサービスです。AI、iPaaS、および先端の技術を駆使して、製造プロセスの効率化、業務効率化、チームワーク強化、コスト削減、品質向上を実現します。このサービスは、製造業の課題を深く理解し、それに対する最適なデジタルソリューションを提供することで、企業が持続的な成長とイノベーションを達成できるようサポートします。
製造業ニュース解説
製造業、主に購買・調達部門にお勤めの方々に向けた情報を配信しております。
新任の方やベテランの方、管理職を対象とした幅広いコンテンツをご用意しております。
お問い合わせ
コストダウンが利益に直結する術だと理解していても、なかなか前に進めることができない状況。そんな時は、newjiのコストダウン自動化機能で大きく利益貢献しよう!
(β版非公開)