- お役立ち記事
- Basics of fracture surface analysis (fractography) and its application to estimating the cause of failure
月間77,185名の
製造業ご担当者様が閲覧しています*
*2025年2月28日現在のGoogle Analyticsのデータより
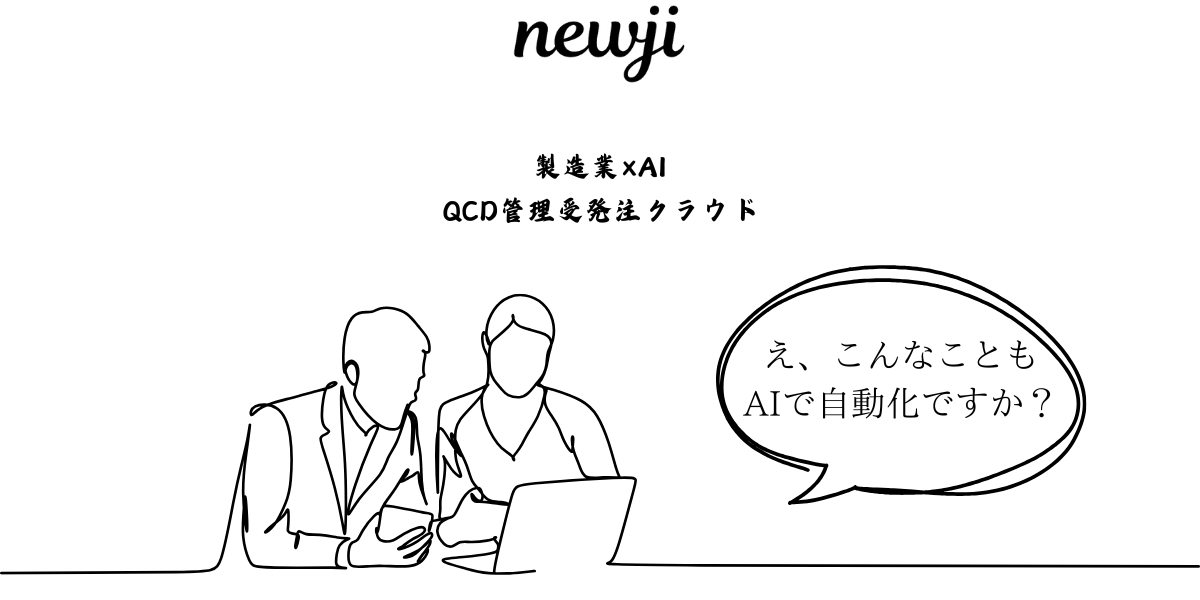
Basics of fracture surface analysis (fractography) and its application to estimating the cause of failure
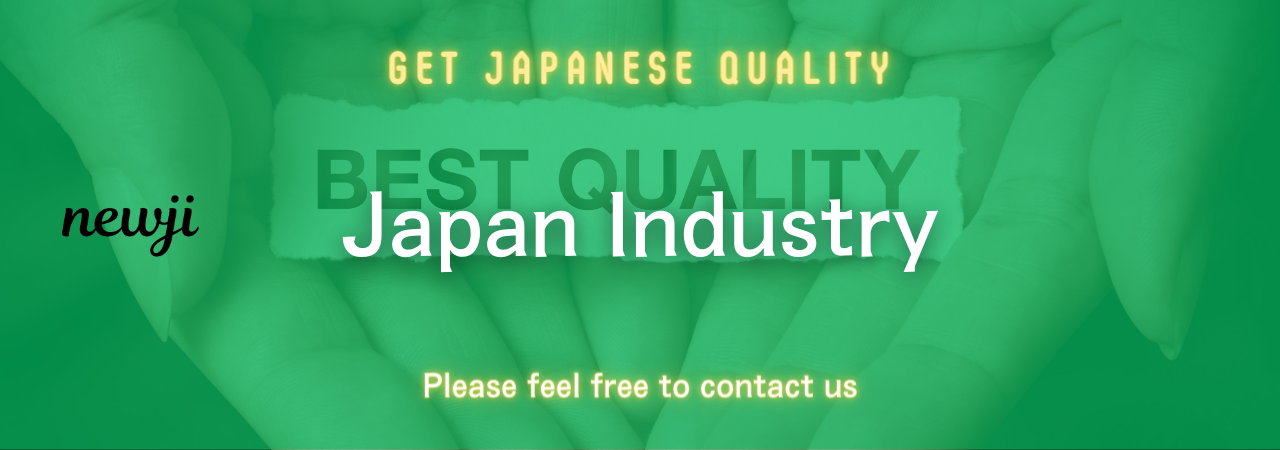
目次
Understanding Fracture Surface Analysis
Fracture surface analysis, often referred to as fractography, is a specialized field that plays a crucial role in understanding the failure of materials.
By examining the fracture surfaces of materials, scientists and engineers can determine the cause and mode of failure.
This is especially important in industries where material performance is critical, such as aerospace, automotive, and construction.
The insights gained from fracture surface analysis can lead to improved material design, enhanced performance, and greater safety.
The primary objective of fracture surface analysis is to identify the type and nature of the failure.
Understanding whether a fracture was caused by fatigue, overload, or environmental conditions helps engineers prevent future occurrences.
In general, the process involves both macroscopic and microscopic examination of the fracture surfaces.
Tools and Techniques in Fractography
Fractography utilizes a range of tools and techniques to analyze fracture surfaces.
At a basic level, visual inspection of the fracture surface can provide immediate insights.
A magnifying glass or a low-power optical microscope might reveal features such as crack initiation sites or signs of corrosion.
For detailed analysis, scanning electron microscopy (SEM) is widely used.
SEM offers high-resolution images that can reveal minute details on the fracture surface.
It can magnify the surface by up to 100,000 times, allowing for examination of the microstructural features that may have contributed to the failure.
Other advanced techniques include transmission electron microscopy (TEM) and atomic force microscopy (AFM).
These techniques provide even deeper insights into the material’s structure at the atomic level.
Key Characteristics of Fracture Surfaces
Fracture surfaces often exhibit distinct features that indicate the mode of failure.
For instance, a ductile fracture generally shows a rough and fibrous surface.
This appearance is due to the significant plastic deformation the material undergoes before fracture.
On the other hand, brittle fractures have a smooth and shiny surface.
Such fractures occur with minimal plastic deformation and are often associated with high-strength materials that fail suddenly.
Fatigue fractures usually display beach marks or striations, concentric patterns around the crack initiation point.
These features indicate a failure due to cyclic loading, where cracks grow incrementally over repeated stress cycles.
Macroscopic Analysis
Macroscopic analysis involves examining features visible to the naked eye or with low magnification.
Key indicators include the general shape of the fracture surface, the presence of radial lines, and the overall fracture pattern.
This analysis helps determine whether the failure was brittle or ductile.
Microscopic Analysis
Microscopic analysis delves deeper into the fracture surface’s fine features.
SEM is the preferred tool, providing detailed images of crack propagation and material defects.
By examining these microstructural details, engineers can pinpoint the exact cause of failure and assess material performance.
Common Causes of Material Failure
Understanding the causes of failure through fracture surface analysis is essential for preventive measures.
Fatigue Failure
Fatigue failure is common in structures subjected to repeated loading and unloading cycles.
The continuous application of stress, even if below the material’s yield strength, can lead to microscopic crack initiation and propagation.
Fatigue fractures are characterized by the presence of beach marks or striations, indicating the progressive growth of a crack over time.
Detecting fatigue failure early is crucial, as it often leads to catastrophic failures if unchecked.
Overload Failure
Overload failure occurs when a material is subjected to stress levels that exceed its ultimate tensile strength.
This often happens suddenly, leaving little to no warning before fracture.
The fracture surface in an overload failure typically features a rough texture, characteristic of ductile fracture, or a smooth, mirror-like appearance in the case of brittle fracture.
Corrosion-Induced Failure
Corrosion can significantly weaken materials, making them susceptible to failure.
When materials are exposed to environmental conditions that promote chemical reactions, such as moisture or salt, corrosion can occur.
Fracture surfaces showing signs of corrosion often have pitted or rough textures, indicating material degradation over time.
Application in Industry
Fracture surface analysis is vital across various industries where material integrity and performance are critical.
Aerospace
In the aerospace industry, safety is paramount.
Components are subject to extreme conditions, including intense vibrations, pressures, and temperatures.
Fractography helps engineers identify potential weaknesses in materials used in aircraft and spacecraft, ensuring they meet stringent safety standards.
By analyzing failed components, improvements in material selection and design can be made.
Automotive
The automotive industry relies heavily on fracture surface analysis to ensure vehicle safety and performance.
Engine parts, suspension systems, and structural components undergo rigorous testing.
Fractography aids in detecting fatigue cracks and other defects, helping manufacturers enhance durability and reliability.
Construction
In construction, material failures can lead to catastrophic consequences.
Fracture surface analysis helps identify the root cause of structural failures, such as those due to material defects, overload conditions, or environmental factors.
This knowledge not only aids in failure prevention but also guides the selection of appropriate materials for construction projects.
Enhancing Material Performance
The insights gained from fracture surface analysis inform improvements in material performance.
Through understanding failure mechanisms, engineers can improve material composition, processing, and design.
Improved Material Design
Fractography provides valuable feedback on how materials perform under different conditions.
This information guides the design of new materials with enhanced properties, such as greater resistance to fatigue or corrosion.
Preventive Measures
By identifying the cause of past failures, industries can implement preventive measures to avoid recurrence.
These include changes in material processing, such as heat treatments or surface coatings that enhance durability.
Quality Control
Fracture surface analysis is an integral part of quality control processes.
Regular inspections and failure analysis ensure that materials meet required specifications and performance standards.
In conclusion, fracture surface analysis is a powerful tool that helps industries and engineers understand material failures.
By examining fracture surfaces, one can identify failure modes, improve material performance, and enhance safety across various applications.
The knowledge gained from fractography informs not only current practices but also the future development of more resilient materials.
資料ダウンロード
QCD管理受発注クラウド「newji」は、受発注部門で必要なQCD管理全てを備えた、現場特化型兼クラウド型の今世紀最高の受発注管理システムとなります。
ユーザー登録
受発注業務の効率化だけでなく、システムを導入することで、コスト削減や製品・資材のステータス可視化のほか、属人化していた受発注情報の共有化による内部不正防止や統制にも役立ちます。
NEWJI DX
製造業に特化したデジタルトランスフォーメーション(DX)の実現を目指す請負開発型のコンサルティングサービスです。AI、iPaaS、および先端の技術を駆使して、製造プロセスの効率化、業務効率化、チームワーク強化、コスト削減、品質向上を実現します。このサービスは、製造業の課題を深く理解し、それに対する最適なデジタルソリューションを提供することで、企業が持続的な成長とイノベーションを達成できるようサポートします。
製造業ニュース解説
製造業、主に購買・調達部門にお勤めの方々に向けた情報を配信しております。
新任の方やベテランの方、管理職を対象とした幅広いコンテンツをご用意しております。
お問い合わせ
コストダウンが利益に直結する術だと理解していても、なかなか前に進めることができない状況。そんな時は、newjiのコストダウン自動化機能で大きく利益貢献しよう!
(β版非公開)