- お役立ち記事
- Fundamentals of PID control, PID tuning and application examples
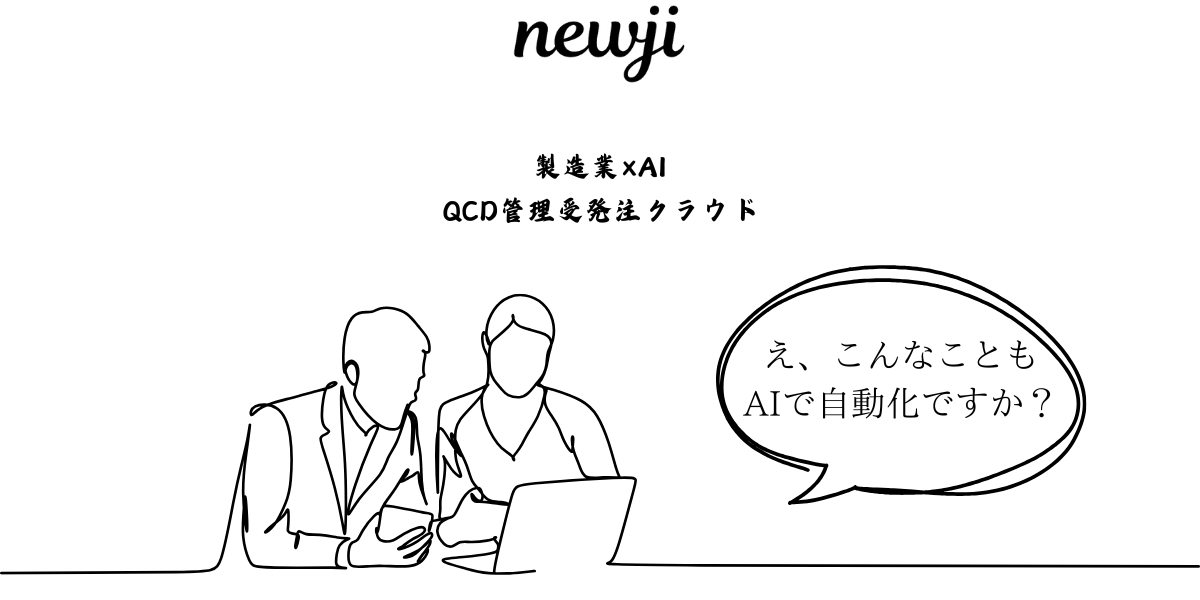
Fundamentals of PID control, PID tuning and application examples
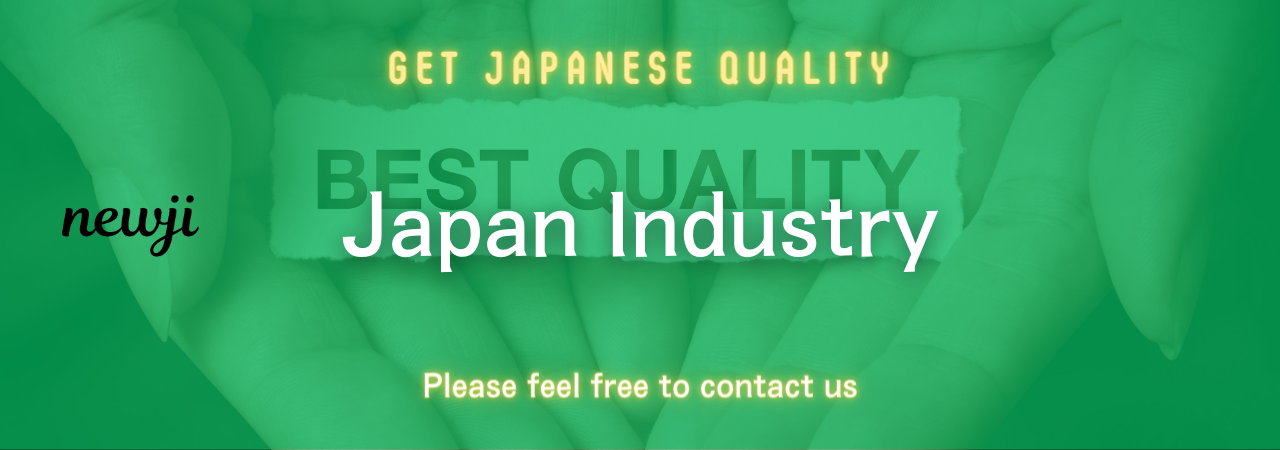
目次
Understanding PID Control
PID control, short for Proportional-Integral-Derivative control, is a critical technology used in industrial control systems and various applications where precise control of some physical process is needed.
It’s a control loop feedback mechanism that calculates an error value as a difference between a desired setpoint and a measured process variable.
The controller attempts to minimize the error by adjusting the process control inputs.
What Does PID Stand For?
PID is an acronym for Proportional, Integral, and Derivative, the three terms of the algorithm.
Each term is responsible for different functions:
– **Proportional (P):** This component depends on the present error.
The proportional response can be adjusted by multiplying the error by a constant known as the proportional gain (Kp).
A larger Kp will result in a larger change in the output for a given error.
– **Integral (I):** This part of the control accounts for the past values of the error.
If the error has been present for a longer period, the integral term will accumulate and apply more correction to eliminate the residual steady-state error.
The contribution of the integral term is proportional to both the magnitude of the error and the duration of the error.
– **Derivative (D):** This term predicts the future behavior of the error.
By considering the rate of change of the process variable, the derivative response can “predict” where the error is heading and counteracts the change.
This can improve stability and response time significantly.
Why Use PID Control?
PID controllers are widely used because of their simplicity, ease of use, and effectiveness.
They do not require an accurate model of the process and can handle complex processes with time delays and non-linearities.
They are also versatile and can be used in a wide range of processes including temperature control, motor speed control, and other industrial process controls.
Benefits of PID Control
1. **Accuracy:** PID controllers can achieve precise control of processes by continuously adjusting the control inputs.
2. **Stability:** They help in stabilizing processes by reducing oscillations and achieving steady-state at a faster rate.
3. **Robustness:** PID control works well in a variety of environments and is resilient to disturbances and changes in process conditions.
4. **Ease of Implementation:** PID controllers can be implemented with simple algorithms in digital controllers or analog systems.
PID Tuning
Tuning a PID controller involves setting the optimal values of Kp, Ki, and Kd to achieve desired performance.
The tuning process can be challenging and often requires trial and error, as it depends on the characteristics of the specific process being controlled.
Common Tuning Methods
1. **Zeigler-Nichols Method:** This is a classic and widely used method for tuning PID controllers.
It involves setting the I and D gains to zero and increasing the P gain until it reaches the ultimate gain, where the system starts to oscillate.
From the oscillatory behavior, the parameters for all three components can be calculated using the Zeigler-Nichols table.
2. **Trial and Error:** This method involves manually adjusting the PID settings while observing the process response until an acceptable result is found.
This is often used when other methods are not applicable and can be time-consuming.
3. **Software Tools:** There are software tools and apps available that can assist in tuning PID controllers by running simulations and adjusting the parameters automatically.
Tips for Effective PID Tuning
– **Start with conservative settings and gradually adjust:** Begin with lower gain settings to avoid excessive oscillation or instability.
– **Understand the process characteristics:** Knowing how the process responds to changes can help in setting accurate PID parameters.
– **Use step response testing:** Apply a step change to the input and analyze how quickly and accurately the system responds to adjust the settings accordingly.
– **Ensure process stability before fine-tuning:** Stability should be the first goal, followed by improvements in performance.
Application Examples of PID Control
PID controllers are used in various industries and applications for control purposes, from simple household devices to complex industrial systems.
Temperature Control in HVAC Systems
In heating, ventilation, and air conditioning (HVAC) systems, PID controllers maintain the desired temperature by adjusting the heating or cooling inputs.
For example, in an air conditioning system, the PID controller manages the compressor speed to maintain room temperature within a specified range.
Motor Speed Control
PID controllers are commonly used to control the speed of electric motors.
For instance, in conveyor belts used in manufacturing, PID control ensures the motor runs at a constant speed despite changes in load, leading to smoother operation and reduced wear.
Industrial Process Control
In industrial environments, PID controllers manage processes like flow, pressure, and chemical concentrations.
For example, in a chemical plant, PID controllers ensure the correct mixture of chemicals by adjusting valves and pumps, optimizing the production process for quality and efficiency.
Robotics
In robotics, PID control is crucial for managing movement and positioning.
Robots often employ PID algorithms to ensure precise control over their joints and movements, enabling tasks such as welding or assembly with high accuracy.
Conclusion
PID control is an essential aspect of modern automatic control systems.
Understanding the fundamentals of PID control, its tuning, and applications can significantly enhance the efficiency and stability of processes across different industries.
With proper tuning methods and understanding of process behavior, PID controllers can achieve outstanding performance in controlling various dynamic systems.
資料ダウンロード
QCD調達購買管理クラウド「newji」は、調達購買部門で必要なQCD管理全てを備えた、現場特化型兼クラウド型の今世紀最高の購買管理システムとなります。
ユーザー登録
調達購買業務の効率化だけでなく、システムを導入することで、コスト削減や製品・資材のステータス可視化のほか、属人化していた購買情報の共有化による内部不正防止や統制にも役立ちます。
NEWJI DX
製造業に特化したデジタルトランスフォーメーション(DX)の実現を目指す請負開発型のコンサルティングサービスです。AI、iPaaS、および先端の技術を駆使して、製造プロセスの効率化、業務効率化、チームワーク強化、コスト削減、品質向上を実現します。このサービスは、製造業の課題を深く理解し、それに対する最適なデジタルソリューションを提供することで、企業が持続的な成長とイノベーションを達成できるようサポートします。
オンライン講座
製造業、主に購買・調達部門にお勤めの方々に向けた情報を配信しております。
新任の方やベテランの方、管理職を対象とした幅広いコンテンツをご用意しております。
お問い合わせ
コストダウンが利益に直結する術だと理解していても、なかなか前に進めることができない状況。そんな時は、newjiのコストダウン自動化機能で大きく利益貢献しよう!
(Β版非公開)