- お役立ち記事
- The shortest route from prototype to mass production
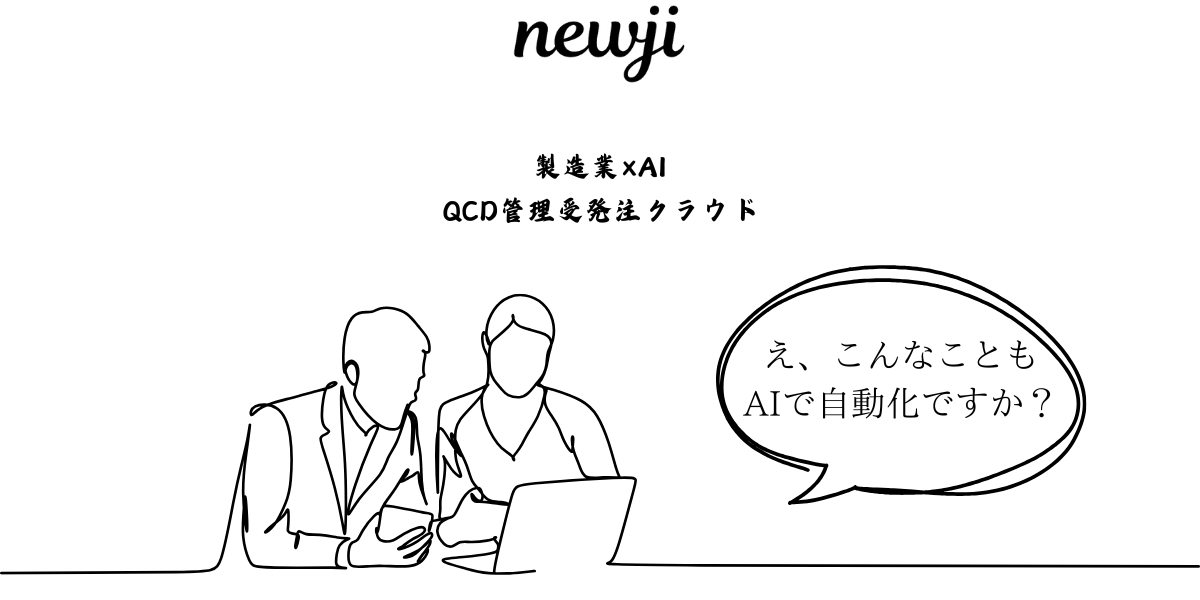
The shortest route from prototype to mass production
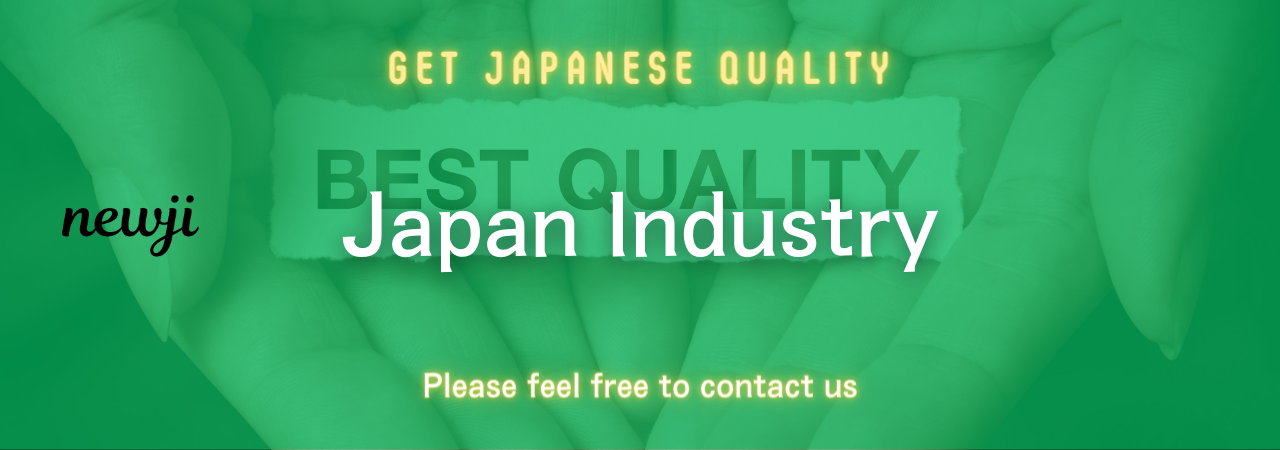
目次
Understanding the Journey from Prototype to Mass Production
When developing a new product, the path from prototype to mass production can seem daunting.
However, with strategic planning and a structured approach, this journey can be more straightforward.
Let’s explore the steps and strategies that can help you efficiently transition a prototype into a full-scale production model.
Start with a Strong Prototype
To successfully navigate the path to mass production, it is crucial to begin with a robust prototype.
The prototype serves as the foundation for all future developments in the product’s lifecycle.
First, ensure that your prototype accurately represents your product idea.
This means it should embody all critical features and functions you envision in the final product.
Testing is vital at this stage.
Conduct thorough functional and performance testing to identify potential issues early on.
This proactive approach helps avoid surprises that could surface later in production.
Moreover, gather feedback.
Engage with potential customers and stakeholders to gain insights.
Their input not only validates your design but also highlights areas for improvement.
Optimize Design for Manufacturing
Once your prototype is solid, the next step is to optimize the design for manufacturing.
This involves reviewing your design to ensure that it is conducive to mass production.
One critical aspect is to simplify your design as much as possible.
Look for ways to reduce the number of components in your product, which can streamline the manufacturing process and reduce costs.
Additionally, choose materials wisely.
Select materials that balance quality with availability and cost-effectiveness.
Ensure that your design is easily replicable.
Align your design with standard industry practices to avoid unnecessary complexities during manufacturing.
This alignment can also make it easier to find suppliers and partners familiar with these processes.
Select the Right Manufacturing Partners
Choosing the right manufacturing partners can make a significant difference in the transition from prototype to mass production.
These partners play a crucial role in realizing your design efficiently and cost-effectively.
Conduct thorough research to identify manufacturers that specialize in your product’s niche.
Evaluate potential partners based on their experience, capacity, and reputation.
Also, consider visiting manufacturing facilities to assess their capabilities and quality control measures firsthand.
Establish clear communication channels with your manufacturing partners.
Clear communication ensures that your product specifications and expectations are fully understood and met.
Develop a Comprehensive Production Plan
Having a comprehensive production plan is essential for a smooth transition to mass production.
This plan serves as your roadmap, guiding the production process from start to finish.
Begin by establishing a clear production schedule.
Determine key milestones and timelines for each phase of production.
This schedule will help you stay on track and manage resources efficiently.
Additionally, calculate your production costs meticulously.
This includes material costs, labor, machinery, and logistics.
Ensure that your budget aligns with production needs to avoid unexpected financial strain.
Incorporate flexibility into your production plan.
Account for possible delays or issues that may arise and have contingency plans ready.
Implement Quality Assurance Protocols
Quality assurance cannot be overlooked when scaling up production.
Ensuring consistent product quality maintains brand integrity and customer satisfaction.
Develop quality assurance protocols tailored to your product.
These protocols should outline inspection points and testing criteria throughout the production process.
Regularly review and update these protocols to reflect any changes in production practices.
Train your staff and manufacturing partners on these quality measures.
Everyone involved in production should be aware of the quality standards expected at each stage.
Having a robust quality assurance system in place reduces the risk of defects and recalls, thereby safeguarding your product’s reputation.
Scale Production Gradually
Jumping into full-scale production immediately may not be the most efficient approach.
Instead, consider scaling production gradually.
Begin with a controlled production run.
This helps in identifying any unforeseen issues during the manufacturing process that were not evident during prototyping.
It also allows for adjustments before a full production rollout.
During this phase, monitor the production closely.
Gather data on production efficiency, product quality, and any bottlenecks that occur.
Use this information to refine and improve production processes.
Leverage Automation and Technology
Incorporating automation and modern technology can significantly enhance production efficiency.
Consider automating repetitive tasks to increase production speed and reduce human error.
Automation can help in maintaining consistent quality while lowering labor costs.
Stay abreast of technological advancements in manufacturing.
Adopting new technologies can offer competitive advantages and improve production processes.
However, balance is essential.
Evaluate the cost and benefits of technology investments to ensure they align with your production goals and budget.
Monitor Market Feedback
Once your product is in mass production and available to the public, market feedback becomes invaluable.
This feedback can inform future production decisions and product iterations.
Encourage customer reviews and listen to their experiences with your product.
Use this information to refine and enhance your offerings continually.
Also, keep an eye on market trends and competitors.
This vigilance allows you to adapt quickly and stay relevant in a competitive marketplace.
Conclusion
The journey from prototype to mass production requires strategic planning, resourcefulness, and adaptability.
By focusing on strong prototyping, efficient design for manufacturing, and selecting the right partners, you set a solid foundation for successful production.
Implementing quality assurance, scaling gradually, leveraging technology, and listening to market feedback further ensure that your product enters the market smoothly and is well-received.
Each step is a building block in bringing your innovative idea from conception to reality, ultimately achieving business success.
資料ダウンロード
QCD調達購買管理クラウド「newji」は、調達購買部門で必要なQCD管理全てを備えた、現場特化型兼クラウド型の今世紀最高の購買管理システムとなります。
ユーザー登録
調達購買業務の効率化だけでなく、システムを導入することで、コスト削減や製品・資材のステータス可視化のほか、属人化していた購買情報の共有化による内部不正防止や統制にも役立ちます。
NEWJI DX
製造業に特化したデジタルトランスフォーメーション(DX)の実現を目指す請負開発型のコンサルティングサービスです。AI、iPaaS、および先端の技術を駆使して、製造プロセスの効率化、業務効率化、チームワーク強化、コスト削減、品質向上を実現します。このサービスは、製造業の課題を深く理解し、それに対する最適なデジタルソリューションを提供することで、企業が持続的な成長とイノベーションを達成できるようサポートします。
オンライン講座
製造業、主に購買・調達部門にお勤めの方々に向けた情報を配信しております。
新任の方やベテランの方、管理職を対象とした幅広いコンテンツをご用意しております。
お問い合わせ
コストダウンが利益に直結する術だと理解していても、なかなか前に進めることができない状況。そんな時は、newjiのコストダウン自動化機能で大きく利益貢献しよう!
(Β版非公開)