- お役立ち記事
- New technology that reduces waste in the prototyping process
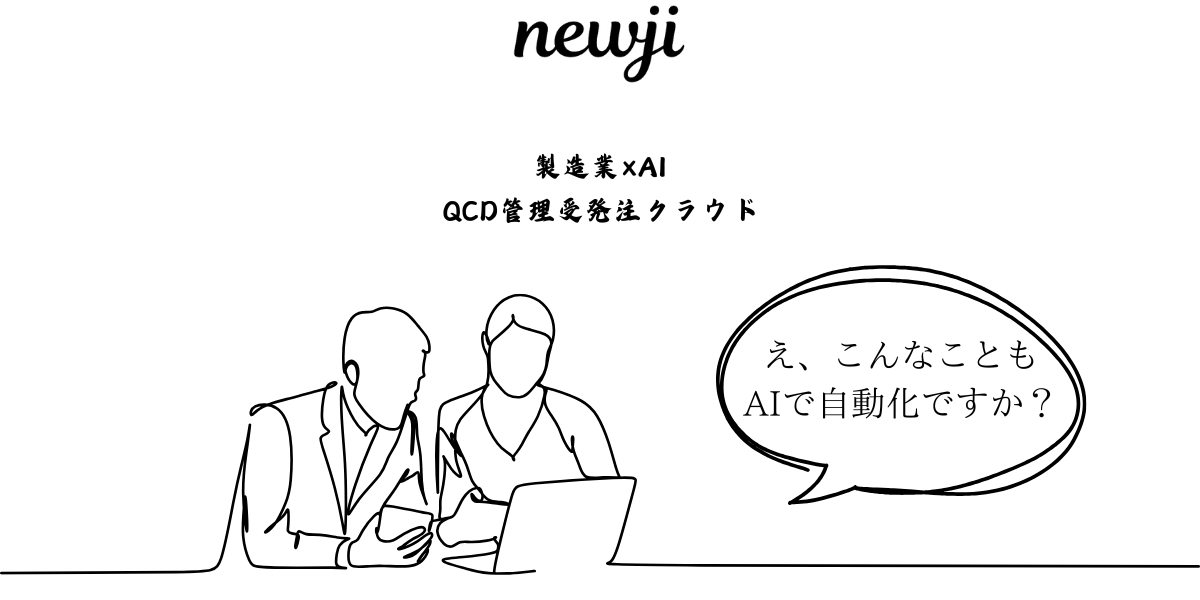
New technology that reduces waste in the prototyping process
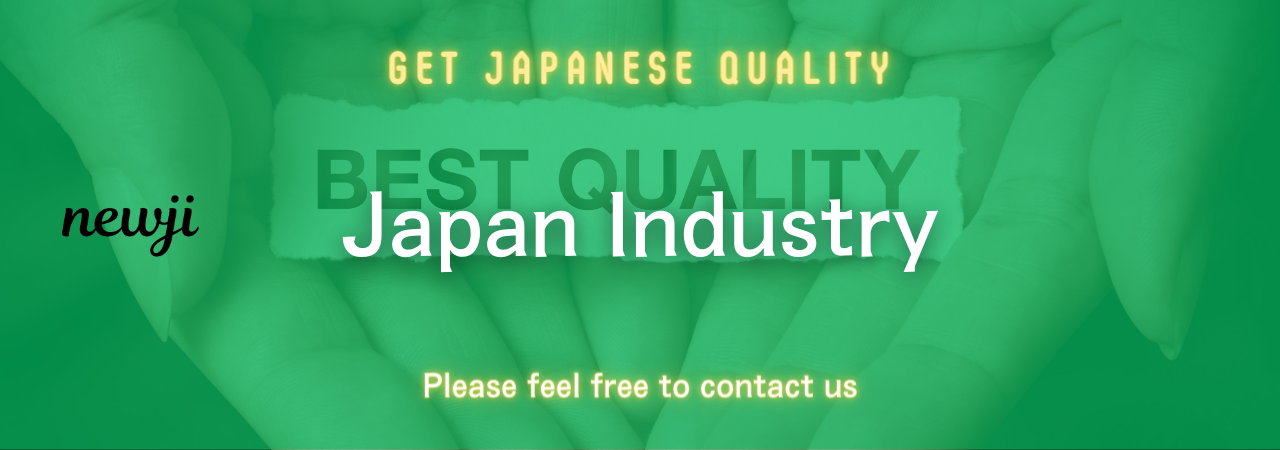
目次
Introduction to Waste Reduction in Prototyping
In the ever-evolving world of manufacturing and design, the prototyping process holds significant importance.
It’s a stage where ideas are transformed into tangible representations, allowing for testing and refinement before final production.
However, traditional prototyping methods often lead to considerable waste, both in terms of materials and time.
With growing environmental awareness and the push for sustainable practices, industries are turning towards innovative technologies that minimize waste in prototyping.
These advancements not only benefit the environment but also streamline operations, reducing costs and enhancing efficiency.
Understanding the Traditional Prototyping Process
Prototyping is a crucial phase in product development where a basic model or version of a product is created to test its feasibility and design.
Traditionally, this process has involved substantial use of materials which, if the prototype is unsuccessful, leads to discarded waste.
Moreover, multiple iterations are often necessary, consuming more resources and time.
Materials like plastic, metal, and other composites commonly used in prototyping can have significant environmental impacts if not managed correctly.
Furthermore, the labor-intensive nature of traditional methods adds to both the financial and environmental costs.
Emergence of New Technologies
Recent technological advancements are revolutionizing the prototyping process.
These new methods reduce waste by improving precision, minimizing material use, and enhancing recycling capabilities.
3D Printing
3D printing, or additive manufacturing, is one of the most notable innovations.
This technology builds prototypes layer by layer, reducing excess material.
3D printing allows for complex designs that were previously impossible or too costly to achieve using traditional methods.
Its precision reduces the need for multiple iterations, saving both time and resources.
Computer-Aided Design (CAD)
Computer-aided design software has significantly enhanced the efficiency of the prototyping process.
With CAD, designers can create accurate digital models before physical prototypes are made.
This allows for thorough testing and changes at the digital phase, hence reducing the need for physical prototypes.
This technology not only cuts down material waste but also shortens the development timeline.
Recyclable and Biodegradable Materials
The shift towards using recyclable and biodegradable materials is another significant step in reducing prototyping waste.
By incorporating these materials into prototypes, industries can decrease their environmental footprint.
While there may be a higher upfront cost, the long-term savings in waste management and disposal are substantial.
Benefits of Waste Reduction in Prototyping
Reducing waste in the prototyping process brings a multitude of benefits.
These advancements not only cater to environmental needs but also provide significant economic advantages.
Cost Efficiency
Minimizing material use directly correlates with cost savings.
New technologies reduce the amount of raw materials needed, cutting expenses.
Moreover, by reducing the number of prototypes required to perfect a design, labor costs also decline.
The long-term financial benefits of investing in sustainable technology can be significant, offering a competitive edge in the marketplace.
Environmental Impact
One of the most critical benefits is the reduction of environmental impact.
Waste from prototyping often ends up in landfills, contributing to pollution.
By decreasing the amount of waste produced and using sustainable materials, industries can significantly reduce their carbon footprint.
This aligns businesses with eco-friendly practices, appealing to environmentally conscious consumers.
Improved Design Process
The implementation of modern technologies not only reduces waste but also enhances the design process.
With tools like 3D printing and CAD, the precision and quality of prototypes improve, allowing for more innovative and complex designs.
This leads to better end products and increased customer satisfaction.
Challenges and Considerations
While the benefits are clear, adopting new technologies in prototyping isn’t without challenges.
Costs, training, and integration into existing systems are all considerations that must be addressed.
Initial Investment
Adopting cutting-edge technologies requires a significant initial investment.
From purchasing equipment like 3D printers to acquiring advanced software, the upfront costs can be daunting for small businesses.
However, these costs are often offset by the long-term savings achieved through waste reduction and increased efficiency.
Training and Skill Development
New technologies come with a learning curve.
Employees must be trained to use new equipment and software effectively, which requires time and resources.
Investing in skill development is crucial for the successful adoption of these technologies.
Integration with Existing Processes
Integrating new technologies into established workflows can be complex.
Companies must ensure that these innovations align with their current processes to avoid disruptions.
This may involve revamping entire operations or gradually introducing changes to ease the transition.
Conclusion
The push towards reducing waste in the prototyping process is not just a trend but a necessity for sustainable industrial practices.
Innovative technologies like 3D printing, CAD, and sustainable materials are paving the way for a more efficient and environmentally conscious approach to design and manufacturing.
While challenges exist, the long-term benefits of adopting these technologies make them a wise investment for the future.
By reducing waste, companies not only contribute to a healthier planet but also enhance their bottom line through improved processes and customer satisfaction.
資料ダウンロード
QCD調達購買管理クラウド「newji」は、調達購買部門で必要なQCD管理全てを備えた、現場特化型兼クラウド型の今世紀最高の購買管理システムとなります。
ユーザー登録
調達購買業務の効率化だけでなく、システムを導入することで、コスト削減や製品・資材のステータス可視化のほか、属人化していた購買情報の共有化による内部不正防止や統制にも役立ちます。
NEWJI DX
製造業に特化したデジタルトランスフォーメーション(DX)の実現を目指す請負開発型のコンサルティングサービスです。AI、iPaaS、および先端の技術を駆使して、製造プロセスの効率化、業務効率化、チームワーク強化、コスト削減、品質向上を実現します。このサービスは、製造業の課題を深く理解し、それに対する最適なデジタルソリューションを提供することで、企業が持続的な成長とイノベーションを達成できるようサポートします。
オンライン講座
製造業、主に購買・調達部門にお勤めの方々に向けた情報を配信しております。
新任の方やベテランの方、管理職を対象とした幅広いコンテンツをご用意しております。
お問い合わせ
コストダウンが利益に直結する術だと理解していても、なかなか前に進めることができない状況。そんな時は、newjiのコストダウン自動化機能で大きく利益貢献しよう!
(Β版非公開)