- お役立ち記事
- Unleashing Precision: How Anodizing OEM Revolutionizes Japanese Manufacturing Excellence
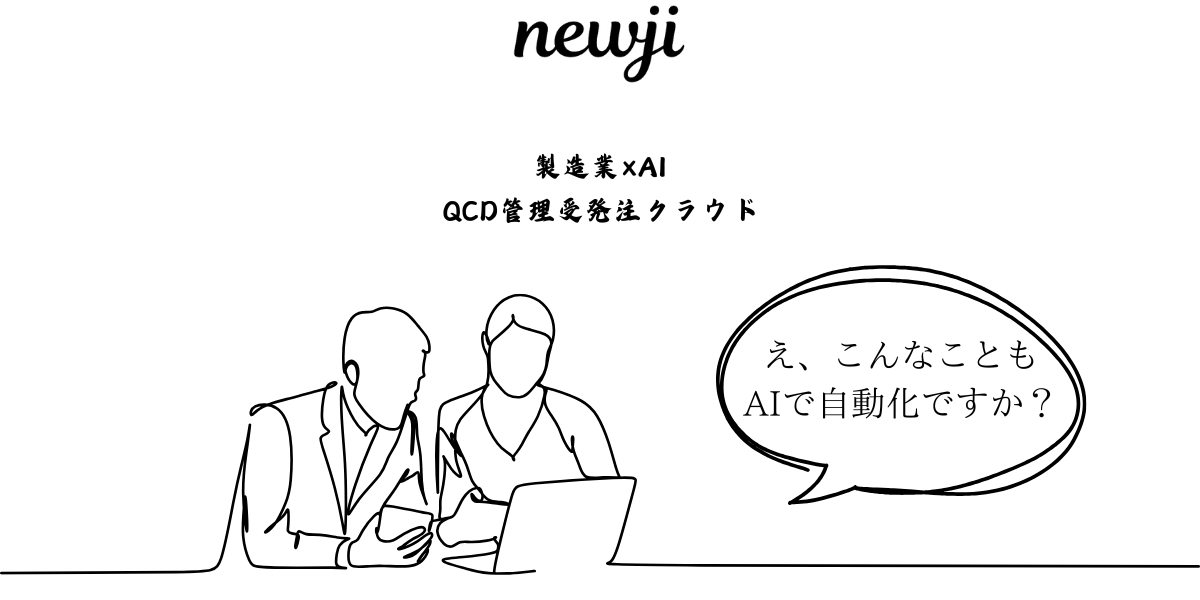
Unleashing Precision: How Anodizing OEM Revolutionizes Japanese Manufacturing Excellence
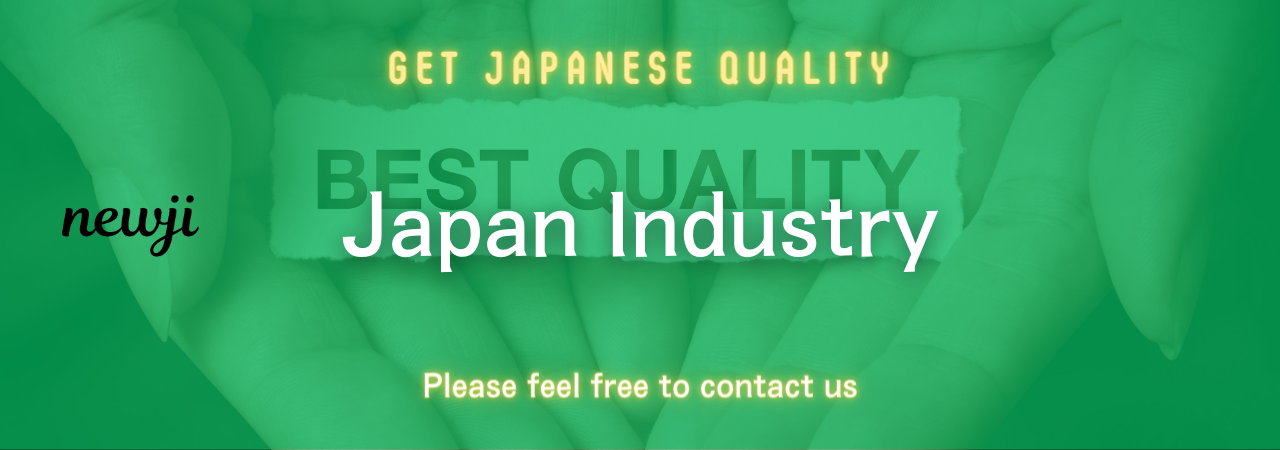
目次
Introduction
Anodizing has long been a cornerstone in the manufacturing processes of Japanese companies, renowned for their precision and quality. In the realm of Original Equipment Manufacturing (OEM), anodizing plays a pivotal role in enhancing product durability, aesthetics, and performance.
This article delves into how OEM anodizing revolutionizes Japanese manufacturing excellence. We will explore the intricacies of anodizing in the OEM context, its advantages and disadvantages, supplier negotiation techniques, current market conditions, and best practices in procurement and purchasing. By understanding these facets, procurement professionals can harness the full potential of anodizing to drive manufacturing success.
Understanding Anodizing in OEM
Anodizing is an electrochemical process that converts the metal surface into a durable, corrosion-resistant, and aesthetically pleasing oxide layer. In OEM settings, anodizing is applied to a variety of components, particularly those made of aluminum, to enhance their properties and extend their lifespan.
The Anodizing Process
The anodizing process involves immersing the metal parts in an acid electrolyte bath and passing an electric current through the medium. This process thickens the natural oxide layer on the surface of the metal, providing increased resistance to wear and corrosion. The thickness of the anodized layer can be controlled to meet specific performance requirements, making it highly adaptable for various applications.
Types of Anodizing
There are several types of anodizing processes used in OEM manufacturing, each tailored to different needs:
- Type I Anodizing: Also known as chromic acid anodizing, it offers a thinner oxide layer and is used for components that require minimal weight increase.
- Type II Anodizing: Sulfuric acid anodizing is the most common type, providing a thicker oxide layer suitable for a wide range of applications.
- Type III Anodizing: Hardcoat anodizing produces a very thick oxide layer, offering superior hardness and corrosion resistance, ideal for heavy-duty parts.
Importance in Japanese Manufacturing
Japanese manufacturing is synonymous with quality and precision. Anodizing OEM plays a critical role in maintaining these high standards by enhancing the functional and aesthetic qualities of components.
Enhancing Product Quality
Anodizing improves the surface hardness and corrosion resistance of components, ensuring that products perform reliably over extended periods. This is particularly important in industries such as automotive, electronics, and aerospace, where component failure can have significant consequences.
Aesthetic Appeal
Japanese consumers and industries place a high value on the appearance of products. Anodizing allows manufacturers to achieve a variety of finishes and colors, enhancing the visual appeal without compromising the material’s integrity.
Cost-Effectiveness
While anodizing involves an additional processing step, the long-term benefits of increased durability and reduced maintenance costs make it a cost-effective solution. This aligns with Japanese manufacturing principles of efficiency and waste reduction.
Advantages of Anodizing OEM
Anodizing offers numerous benefits that contribute to manufacturing excellence in the OEM sector. Understanding these advantages can help procurement professionals make informed decisions.
Improved Durability
The anodized layer significantly increases the hardness and wear resistance of components. This ensures that parts can withstand mechanical stresses and harsh environmental conditions, extending their service life.
Enhanced Corrosion Resistance
Anodized surfaces are highly resistant to corrosion, making them ideal for use in environments where exposure to moisture, chemicals, or salts is prevalent. This is particularly beneficial in automotive and aerospace applications.
Superior Aesthetic Options
Anodizing allows for a wide range of color options and finishes, enabling manufacturers to meet specific design requirements and enhance brand identity. The aesthetic versatility of anodized components can be a key differentiator in competitive markets.
Environmental Benefits
Anodizing is an environmentally friendly process compared to other surface treatments. It does not produce harmful by-products and the anodized layer is fully recyclable. This aligns with the growing emphasis on sustainability in manufacturing.
Cost Efficiency
Despite the initial investment, anodizing can lead to significant cost savings over time. The increased lifespan of components reduces the need for frequent replacements, lowering overall maintenance and operational costs.
Disadvantages of Anodizing OEM
While anodizing offers many benefits, it is essential to consider its limitations to make balanced procurement decisions.
Initial Setup Costs
Implementing anodizing processes requires investment in specialized equipment and facilities. This can be a barrier for smaller manufacturers or those looking to scale quickly.
Process Complexity
Anodizing involves precise control over various parameters such as temperature, voltage, and electrolyte composition. Maintaining consistent quality requires skilled technicians and rigorous quality control measures.
Material Limitations
Anodizing is primarily suitable for aluminum and certain other non-ferrous metals. Its application on ferrous metals is limited and may require additional surface preparation or alternative treatments.
Surface Porosity
The anodized layer is inherently porous, which can trap contaminants and moisture. While sealing processes can mitigate this issue, it adds another step to the overall manufacturing process.
Potential for Color Fading
Colored anodized coatings may fade over time when exposed to extreme environmental conditions or UV radiation. Selecting appropriate dyeing and sealing techniques is crucial to ensure color longevity.
Supplier Negotiation Techniques
Effective negotiation with anodizing suppliers can lead to better quality, cost savings, and more reliable supply chains. Here are key strategies for procurement professionals.
Understand Supplier Capabilities
Before entering negotiations, thoroughly assess the supplier’s technical capabilities, quality standards, and certifications. Understanding their strengths and limitations will inform your negotiation strategy and help set realistic expectations.
Leverage Volume Commitments
Manufacturers can negotiate better terms by committing to larger volumes. Suppliers often offer discounts or favorable pricing structures for bulk orders, providing mutual benefits of increased sales and cost savings.
Establish Clear Specifications
Clearly define the technical specifications and quality standards required for anodized components. This includes surface finish, color, thickness, and performance criteria. Clear specifications reduce misunderstandings and ensure that suppliers meet your exact needs.
Build Long-Term Relationships
Fostering strong, long-term partnerships with suppliers can lead to more favorable terms and better collaboration. Trust and reliability are key components of successful negotiations, leading to consistent quality and timely deliveries.
Flexible Payment Terms
Negotiating favorable payment terms can improve cash flow management. Options such as extended payment periods or early payment discounts can benefit both parties and strengthen the business relationship.
Insist on Quality Assurance
Ensure that suppliers adhere to stringent quality control measures. Negotiating the inclusion of regular quality audits, certifications, and compliance with industry standards can safeguard the integrity of your supply chain.
Negotiate Lead Times
Discuss and negotiate lead times that align with your production schedules. Reliable delivery schedules are essential to maintaining efficient manufacturing processes and preventing delays.
Explore Value-Added Services
Suppliers may offer additional services such as custom coloring, finishing, or assembly. Including these value-added services in negotiations can enhance the overall value proposition and streamline your production process.
Market Conditions and Trends
Understanding the current market landscape is crucial for effective procurement and purchasing strategies in anodizing OEM.
Global Supply Chain Dynamics
Global supply chains are subject to fluctuations due to geopolitical tensions, trade policies, and economic shifts. Staying informed about these dynamics helps anticipate potential disruptions and develop contingency plans.
Technological Advancements
Advances in anodizing technology, such as improved sealing techniques and environmentally friendly processes, are shaping the industry. Adopting these innovations can enhance product quality and operational efficiency.
Demand for Sustainability
There is a growing emphasis on sustainable manufacturing practices. Anodizing processes that minimize environmental impact and use eco-friendly materials are increasingly in demand, influencing supplier selection and procurement strategies.
Competitive Pricing Pressures
Intense competition in the manufacturing sector drives the need for cost-effective solutions. Balancing cost with quality is essential to maintain competitiveness without compromising on product standards.
Customization and Flexibility
Customers are seeking more customized and flexible manufacturing solutions. Suppliers that can offer tailored anodizing services to meet specific design and performance requirements are highly valued.
Regulatory Compliance
Compliance with international and local regulations is paramount. Staying updated on regulatory changes ensures that anodizing processes and products meet required standards, avoiding legal and financial repercussions.
Best Practices in Procurement and Purchasing
Implementing best practices in procurement and purchasing can optimize the anodizing process and enhance overall manufacturing efficiency.
Comprehensive Supplier Evaluation
Conduct thorough evaluations of potential suppliers, considering factors such as technical expertise, quality control measures, delivery reliability, and financial stability. Utilizing a structured evaluation framework ensures consistent and objective assessments.
Strategic Sourcing
Adopt strategic sourcing approaches to identify and engage with suppliers that align with your long-term business goals. Diversifying the supplier base can mitigate risks and provide access to a broader range of capabilities.
Collaborative Planning
Work closely with suppliers to forecast demand, plan production schedules, and coordinate logistics. Collaborative planning enhances supply chain visibility and ensures timely availability of anodized components.
Performance Monitoring
Regularly monitor supplier performance through key performance indicators (KPIs) such as on-time delivery, defect rates, and responsiveness. Continuous performance assessment helps identify areas for improvement and maintain high standards.
Lean Procurement Practices
Implement lean procurement practices to eliminate waste, streamline processes, and reduce costs. Techniques such as just-in-time ordering and inventory optimization contribute to efficient resource utilization.
Risk Management
Develop and implement risk management strategies to address potential disruptions in the anodizing supply chain. This includes identifying critical suppliers, assessing vulnerabilities, and establishing contingency plans.
Continuous Improvement
Foster a culture of continuous improvement by regularly reviewing procurement processes and seeking feedback from stakeholders. Embracing methodologies such as Six Sigma or Total Quality Management can drive ongoing enhancements.
Leveraging Technology
Utilize procurement software and digital tools to automate routine tasks, enhance data accuracy, and improve decision-making. Technology integration can lead to greater efficiency and better visibility into the procurement lifecycle.
Quality Control and Assurance
Maintaining high quality in anodized components is essential for sustaining manufacturing excellence. Robust quality control and assurance practices are integral to achieving consistent and reliable outcomes.
Establishing Quality Standards
Define clear quality standards and specifications for anodized components. These standards should cover aspects such as surface finish, color consistency, coating thickness, and corrosion resistance.
Supplier Quality Management
Implement a comprehensive supplier quality management program that includes regular audits, performance evaluations, and compliance checks. Ensuring that suppliers adhere to your quality standards is critical for maintaining product integrity.
In-Process Inspections
Conduct in-process inspections during the anodizing process to identify and address potential defects early. Monitoring critical parameters such as electrolyte concentration, temperature, and voltage helps maintain process consistency.
Final Product Testing
Perform rigorous testing on completed anodized components to verify compliance with quality standards. Tests may include adhesion tests, hardness measurements, corrosion resistance evaluations, and visual inspections.
Documentation and Traceability
Maintain detailed documentation and traceability throughout the anodizing process. Comprehensive records facilitate problem-solving, ensure accountability, and support compliance with industry regulations.
Training and Development
Invest in training programs for personnel involved in the anodizing process. Skilled and knowledgeable staff are essential for executing quality control measures effectively and sustaining high manufacturing standards.
Logistics and Supply Chain Management
Efficient logistics and supply chain management are vital for ensuring the timely and cost-effective delivery of anodized components.
Optimizing Inventory Levels
Balance inventory levels to meet production demands without overstocking. Techniques such as just-in-time inventory can reduce storage costs and minimize the risk of obsolescence.
Streamlining Transportation
Evaluate transportation options to determine the most efficient and cost-effective methods for delivering anodized components. Consider factors such as lead times, shipping costs, and reliability when selecting logistics partners.
Enhancing Supply Chain Visibility
Implement systems that provide real-time visibility into supply chain operations. Enhanced transparency allows for better coordination, quicker response to disruptions, and improved decision-making.
Collaborative Relationships
Foster collaborative relationships with suppliers, logistics providers, and other supply chain partners. Strong partnerships enhance communication, facilitate problem-solving, and contribute to overall supply chain resilience.
Implementing Technology Solutions
Leverage technology solutions such as supply chain management software, RFID tracking, and automated warehousing systems to improve efficiency and accuracy in logistics operations.
Risk Mitigation Strategies
Identify potential risks in the supply chain and develop mitigation strategies to address them. This may include diversifying suppliers, maintaining safety stock, and establishing contingency plans for unforeseen disruptions.
Case Studies
Examining real-world examples of successful anodizing OEM implementations provides valuable insights into best practices and effective strategies.
Case Study 1: Automotive Component Manufacturer
A leading Japanese automotive component manufacturer sought to enhance the durability and aesthetic appeal of its aluminum parts through anodizing. By partnering with a specialized anodizing supplier, the company achieved a significant reduction in corrosion-related defects. The collaboration also enabled the supplier to implement custom coloring, aligning with the manufacturer’s design requirements. As a result, the company experienced improved product performance and customer satisfaction, reinforcing its market position.
Case Study 2: Electronics Housing Producer
An electronics housing producer aimed to differentiate its products through high-quality finishes. Implementing Type II anodizing allowed for vibrant colors and consistent surface textures. Through strategic sourcing and long-term partnership with an anodizing OEM, the company secured competitive pricing and reliable supply. The enhanced aesthetic qualities contributed to the product’s premium positioning, leading to increased sales and brand recognition.
Case Study 3: Aerospace Component Supplier
A supplier of aerospace components faced stringent requirements for surface integrity and performance. By adopting hardcoat anodizing (Type III), the company met the rigorous standards for hardness and corrosion resistance demanded by its clients. Comprehensive quality control measures and regular supplier audits ensured consistent compliance. This commitment to quality enabled the supplier to secure long-term contracts with major aerospace manufacturers, driving business growth.
Conclusion
Anodizing OEM is a transformative process that significantly contributes to the manufacturing excellence for which Japanese companies are renowned. By enhancing the durability, corrosion resistance, and aesthetic appeal of components, anodizing supports the creation of high-quality products that meet the stringent demands of various industries.
Effective procurement and purchasing strategies are essential to fully leverage the benefits of anodizing. This includes understanding the nuances of the anodizing process, evaluating supplier capabilities, negotiating favorable terms, and implementing best practices in quality control and supply chain management. Staying informed about market conditions and trends further empowers procurement professionals to make strategic decisions that drive efficiency and innovation.
While there are challenges associated with anodizing, such as initial setup costs and process complexity, the long-term advantages far outweigh these drawbacks. By adopting a comprehensive and strategic approach to anodizing OEM, manufacturers can unlock new levels of precision and excellence, solidifying their position in competitive global markets.
資料ダウンロード
QCD調達購買管理クラウド「newji」は、調達購買部門で必要なQCD管理全てを備えた、現場特化型兼クラウド型の今世紀最高の購買管理システムとなります。
ユーザー登録
調達購買業務の効率化だけでなく、システムを導入することで、コスト削減や製品・資材のステータス可視化のほか、属人化していた購買情報の共有化による内部不正防止や統制にも役立ちます。
NEWJI DX
製造業に特化したデジタルトランスフォーメーション(DX)の実現を目指す請負開発型のコンサルティングサービスです。AI、iPaaS、および先端の技術を駆使して、製造プロセスの効率化、業務効率化、チームワーク強化、コスト削減、品質向上を実現します。このサービスは、製造業の課題を深く理解し、それに対する最適なデジタルソリューションを提供することで、企業が持続的な成長とイノベーションを達成できるようサポートします。
オンライン講座
製造業、主に購買・調達部門にお勤めの方々に向けた情報を配信しております。
新任の方やベテランの方、管理職を対象とした幅広いコンテンツをご用意しております。
お問い合わせ
コストダウンが利益に直結する術だと理解していても、なかなか前に進めることができない状況。そんな時は、newjiのコストダウン自動化機能で大きく利益貢献しよう!
(Β版非公開)