- お役立ち記事
- “Revolutionizing Japanese Manufacturing: The Role of Illuminance Sensors in Precision and Efficiency”
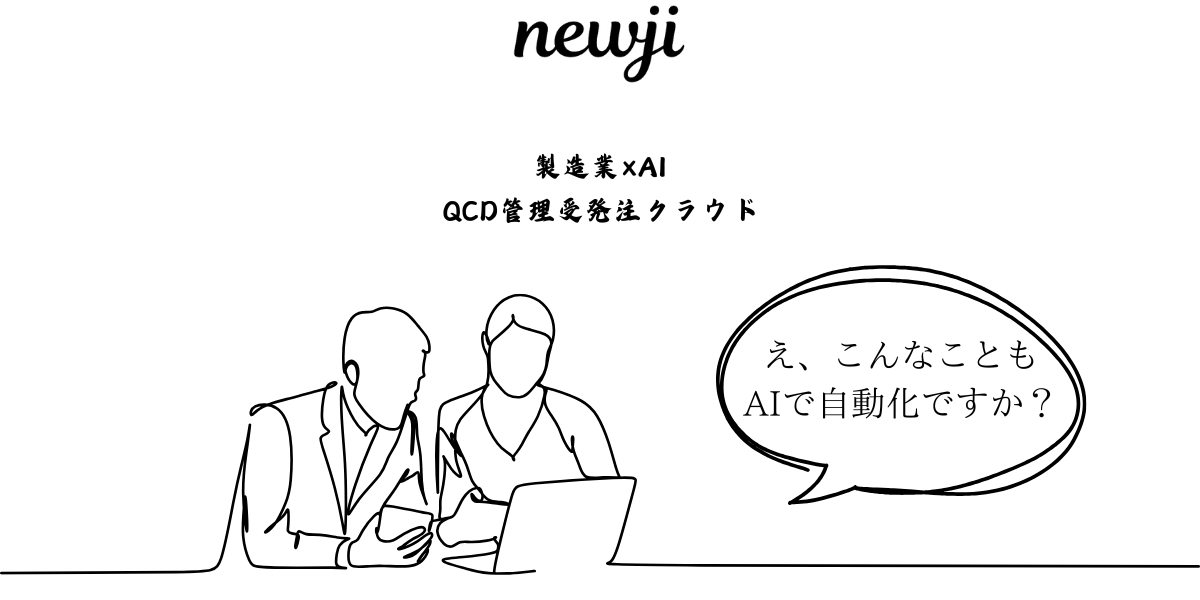
“Revolutionizing Japanese Manufacturing: The Role of Illuminance Sensors in Precision and Efficiency”
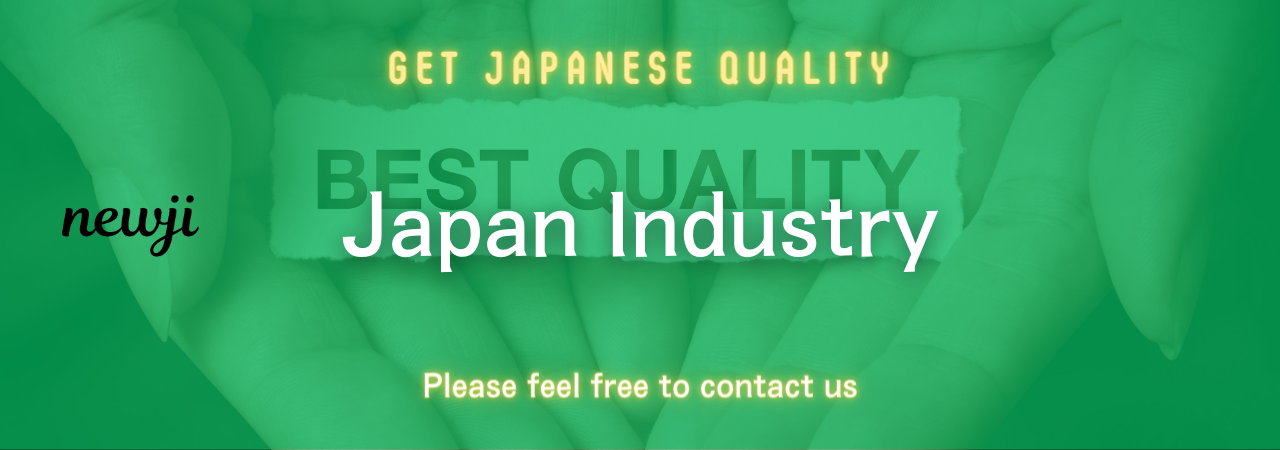
目次
Introduction
In the competitive landscape of global manufacturing, Japanese companies continue to set benchmarks in precision and efficiency. A key contributor to this success is the integration of advanced technologies such as illuminance sensors. These sensors play a pivotal role in enhancing manufacturing processes, ensuring product quality, and optimizing operational efficiency. This article delves into the significance of illuminance sensors in Japanese manufacturing, exploring their advantages, challenges, procurement strategies, market conditions, and best practices for implementation.
The Importance of Illuminance Sensors in Japanese Manufacturing
Illuminance sensors, also known as light sensors, are devices that measure the intensity of light in an environment. In the context of manufacturing, these sensors are crucial for several applications, including quality control, automation, and energy management. Japanese manufacturers leverage illuminance sensors to maintain high standards of precision and to streamline production processes. By accurately monitoring lighting conditions, companies can ensure optimal working environments, reduce energy consumption, and enhance the overall efficiency of their manufacturing operations.
Advantages of Using Illuminance Sensors
Enhanced Precision
Illuminance sensors contribute significantly to the precision of manufacturing processes. By providing accurate and real-time data on lighting conditions, these sensors enable manufacturers to maintain consistent quality in their products. For instance, in industries where color accuracy is paramount, such as electronics and automotive manufacturing, precise lighting ensures that products meet stringent quality standards.
Improved Efficiency
The integration of illuminance sensors leads to improved operational efficiency. These sensors can regulate lighting systems based on real-time requirements, ensuring that energy is used only when necessary. This dynamic adjustment minimizes waste and ensures that production areas are adequately lit, enhancing worker productivity and reducing downtime.
Energy Savings
Energy efficiency is a critical concern in modern manufacturing. Illuminance sensors play a vital role in reducing energy consumption by automatically adjusting lighting levels in response to ambient light conditions. This not only lowers operational costs but also supports sustainability initiatives by minimizing the environmental footprint of manufacturing facilities.
Challenges and Disadvantages
Initial Investment Costs
One of the primary challenges associated with the adoption of illuminance sensors is the initial investment required. High-quality sensors and the integration processes can be costly, posing a barrier for smaller manufacturers. However, the long-term benefits in terms of energy savings and improved efficiency often justify the initial expenditure.
Integration with Existing Systems
Integrating illuminance sensors with existing manufacturing systems can be complex. It requires seamless communication between sensors and control systems, which may necessitate upgrades or modifications to current infrastructure. This integration process can be time-consuming and may require specialized expertise.
Maintenance and Calibration
Maintaining and calibrating illuminance sensors is essential to ensure their accuracy and reliability. Over time, sensors can degrade or become misaligned, leading to inaccurate readings. Regular maintenance schedules and calibration procedures are necessary to mitigate these issues, adding to the operational costs.
Procurement and Purchasing Perspectives
Sourcing Japanese Suppliers for Illuminance Sensors
Japan is renowned for its high-quality manufacturing and technological advancements. When sourcing illuminance sensors from Japanese suppliers, companies benefit from cutting-edge technology, reliability, and superior performance. Establishing strong relationships with reputable suppliers is crucial to ensure consistent quality and timely delivery of components.
Negotiation Techniques
Effective negotiation with Japanese suppliers involves understanding cultural nuances and building trust. Japanese businesses value long-term relationships and mutual respect. Transparent communication, respect for timelines, and a focus on collaborative partnerships can lead to favorable terms and successful negotiations.
Quality Control and Assurance
Japanese suppliers are known for their stringent quality control measures. Implementing robust quality assurance processes ensures that the illuminance sensors meet the required standards and specifications. Regular audits, certifications, and quality checks are essential components of the procurement process to maintain high-quality outputs.
Market Conditions and Trends
Current Market Landscape
The global market for illuminance sensors is witnessing significant growth, driven by advancements in smart manufacturing and automation. Japanese manufacturers are at the forefront of this trend, offering innovative solutions that cater to diverse industrial needs. The demand for energy-efficient and high-precision sensors is increasing, reflecting the broader shift towards sustainable and intelligent manufacturing practices.
Future Trends
The future of illuminance sensors in manufacturing is poised for further innovation. Trends such as the integration of artificial intelligence, IoT connectivity, and enhanced data analytics are expected to shape the next generation of sensors. These advancements will enable more sophisticated monitoring and control systems, fostering greater precision and efficiency in manufacturing processes.
Best Practices in Implementing Illuminance Sensors
Selection Criteria
When selecting illuminance sensors, manufacturers should consider factors such as accuracy, response time, durability, and compatibility with existing systems. Evaluating the specific needs of the production environment and selecting sensors that align with those requirements is crucial for successful implementation.
Implementation Strategies
A strategic approach to implementation involves phased integration, starting with pilot projects to test sensor performance and system compatibility. Training staff on the proper use and maintenance of sensors ensures smooth adoption and maximizes the benefits of the technology.
Continuous Improvement
Continuous monitoring and feedback loops are essential for optimizing the performance of illuminance sensors. Regularly reviewing sensor data and system performance allows manufacturers to make informed adjustments, driving ongoing improvements in precision and efficiency.
Case Studies
Successful Implementations in Japanese Manufacturing
Several Japanese manufacturing firms have successfully integrated illuminance sensors into their operations. For instance, a leading automotive manufacturer implemented illuminance sensors in their assembly lines, resulting in a 15% increase in production efficiency and a significant reduction in energy costs. Another electronics company utilized these sensors to enhance color precision in their display manufacturing, achieving higher product quality and customer satisfaction.
Conclusion
Illuminance sensors are instrumental in revolutionizing Japanese manufacturing by enhancing precision and efficiency. Despite the challenges associated with their adoption, the long-term benefits in terms of quality, energy savings, and operational efficiency make them a valuable investment. By adopting strategic procurement practices, understanding market dynamics, and implementing best practices, manufacturers can fully leverage the advantages of illuminance sensors. As technology continues to evolve, the role of these sensors in manufacturing is set to become even more critical, driving further advancements in the industry.
資料ダウンロード
QCD調達購買管理クラウド「newji」は、調達購買部門で必要なQCD管理全てを備えた、現場特化型兼クラウド型の今世紀最高の購買管理システムとなります。
ユーザー登録
調達購買業務の効率化だけでなく、システムを導入することで、コスト削減や製品・資材のステータス可視化のほか、属人化していた購買情報の共有化による内部不正防止や統制にも役立ちます。
NEWJI DX
製造業に特化したデジタルトランスフォーメーション(DX)の実現を目指す請負開発型のコンサルティングサービスです。AI、iPaaS、および先端の技術を駆使して、製造プロセスの効率化、業務効率化、チームワーク強化、コスト削減、品質向上を実現します。このサービスは、製造業の課題を深く理解し、それに対する最適なデジタルソリューションを提供することで、企業が持続的な成長とイノベーションを達成できるようサポートします。
オンライン講座
製造業、主に購買・調達部門にお勤めの方々に向けた情報を配信しております。
新任の方やベテランの方、管理職を対象とした幅広いコンテンツをご用意しております。
お問い合わせ
コストダウンが利益に直結する術だと理解していても、なかなか前に進めることができない状況。そんな時は、newjiのコストダウン自動化機能で大きく利益貢献しよう!
(Β版非公開)