- お役立ち記事
- Discovering the Art of Precision: How Japanese Manufacturing is Revolutionizing Titanium Components
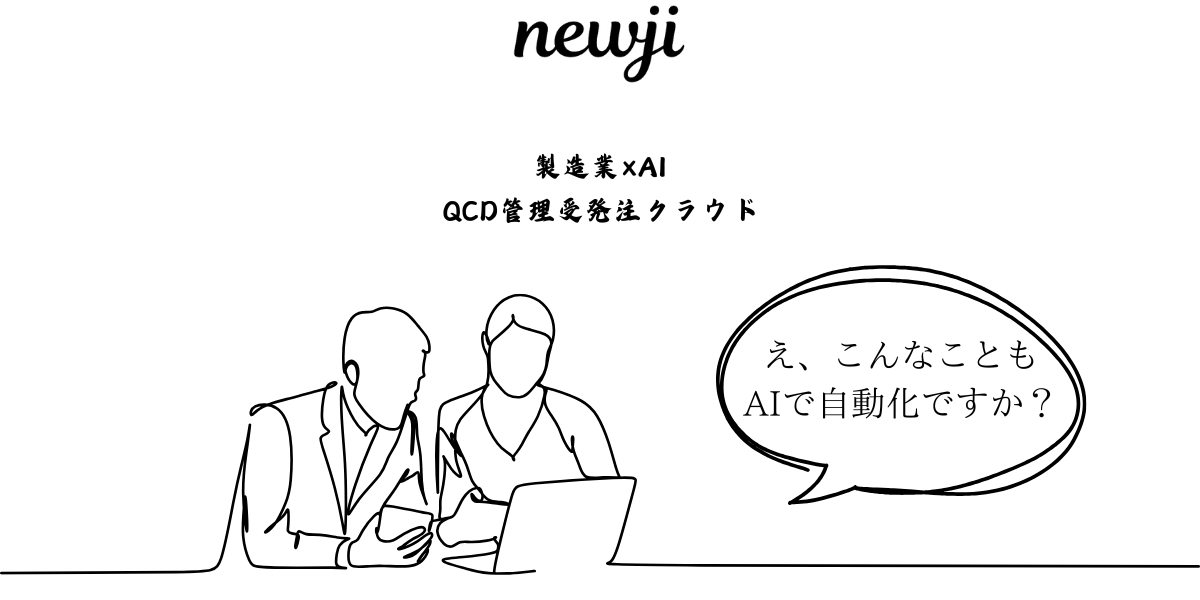
Discovering the Art of Precision: How Japanese Manufacturing is Revolutionizing Titanium Components
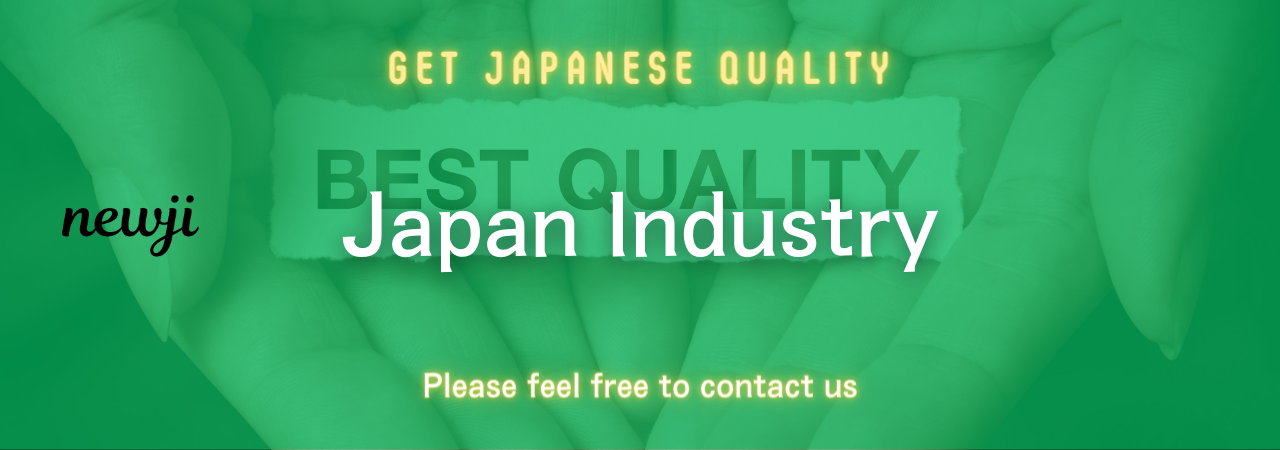
目次
Introduction to Japanese Precision in Titanium Manufacturing
Japanese manufacturing has long been synonymous with precision, quality, and innovation. In the realm of titanium component production, these attributes are particularly pronounced. Titanium, known for its exceptional strength-to-weight ratio and corrosion resistance, is a critical material in industries such as aerospace, medical devices, and automotive engineering. Japanese manufacturers have harnessed advanced technologies and refined processes to revolutionize the production of titanium components, setting new standards in the global market.
The Pillars of Japanese Manufacturing Excellence
Commitment to Quality Control
Quality control is at the heart of Japanese manufacturing philosophy. Companies implement rigorous quality assurance protocols at every stage of production. From raw material inspection to final product testing, each step is meticulously monitored. This attention to detail ensures that titanium components meet the highest standards of performance and reliability. The adoption of Six Sigma and Total Quality Management (TQM) methodologies further enhances process consistency and defect reduction.
Advanced Production Technologies
Japanese manufacturers are pioneers in integrating cutting-edge technologies into their production processes. The use of Computer Numerical Control (CNC) machining allows for unparalleled precision in shaping titanium components. Additionally, additive manufacturing, or 3D printing, is increasingly employed to create complex geometries that would be challenging or impossible to achieve with traditional methods. Automation and robotics streamline production, increase efficiency, and minimize human error.
Skilled Workforce and Continuous Training
A highly skilled workforce is a cornerstone of Japanese manufacturing success. Workers undergo extensive training to master sophisticated machinery and complex processes. Continuous professional development programs ensure that employees remain adept at using the latest technologies and adhere to best practices. This emphasis on human capital complements technological advancements, driving innovation and maintaining high productivity levels.
Lean Manufacturing Practices
Lean manufacturing principles are deeply ingrained in Japanese production systems. By focusing on waste reduction, process optimization, and value stream mapping, companies enhance operational efficiency and reduce costs. Techniques such as Just-In-Time (JIT) inventory management ensure that materials are available precisely when needed, minimizing excess stock and associated holding costs.
Advantages of Japanese Titanium Component Manufacturing
Unmatched Precision and Consistency
Japanese manufacturers excel in producing titanium components with exceptional precision and consistency. High tolerances are achieved through advanced machining techniques and stringent quality controls. This reliability is crucial for applications where precision is paramount, such as aerospace components or medical implants.
Innovative Design Capabilities
The integration of design and manufacturing processes fosters innovation. Japanese companies often collaborate with clients during the design phase to optimize component functionality and manufacturability. Advanced simulation and modeling tools enable the creation of innovative designs that enhance performance while simplifying production.
Strong Supplier Relationships
Japanese manufacturers cultivate long-term, mutually beneficial relationships with their suppliers. This collaboration ensures the consistent supply of high-quality raw materials and components. Reliable supplier partnerships contribute to seamless production flows and help maintain stringent quality standards.
Adaptability and Responsiveness
Japanese companies are renowned for their ability to swiftly adapt to changing market demands and technological advancements. Agile manufacturing practices allow for rapid adjustments in production processes, facilitating the introduction of new products and the customization of existing ones to meet specific client requirements.
Challenges and Disadvantages
Higher Production Costs
The emphasis on quality and advanced technologies can result in higher production costs compared to competitors in regions with lower labor and operational expenses. These costs may be passed on to clients, potentially impacting price competitiveness. However, the long-term benefits of superior quality and reliability often justify the investment.
Cultural and Communication Barriers
Working with Japanese suppliers may present cultural and communication challenges. Differences in business etiquette, language barriers, and varying work practices can complicate negotiations and collaboration. Overcoming these barriers requires cultural sensitivity, effective communication strategies, and potentially the use of intermediaries or bilingual personnel.
Longer Lead Times
The meticulous manufacturing processes that ensure high quality can also lead to longer lead times. Clients requiring rapid turnaround may find it challenging to meet their deadlines when sourcing from Japanese manufacturers. Balancing quality with speed often necessitates careful planning and communication between suppliers and clients.
Supplier Negotiation Techniques
Building Trust and Long-Term Relationships
Japanese business culture places a strong emphasis on trust and long-term relationships. Establishing a foundation of mutual respect and reliability is crucial for successful negotiations. Investing time in relationship-building activities, such as visits and face-to-face meetings, can facilitate smoother negotiations and foster ongoing collaboration.
Understanding Cultural Nuances
A deep understanding of Japanese cultural norms and business practices enhances negotiation effectiveness. Showing respect through proper etiquette, such as exchanging business cards with both hands and using formal titles, demonstrates cultural sensitivity. Awareness of indirect communication styles and the importance of consensus can lead to more productive discussions.
Clear Communication of Requirements
Clearly articulating specifications, expectations, and contractual terms is essential. Detailed documentation and explicit communication help prevent misunderstandings and ensure that both parties are aligned on project goals. Providing comprehensive technical requirements and production timelines facilitates accurate quoting and planning.
Leveraging Technical Expertise
Japanese manufacturers value technical competence and problem-solving capabilities. Demonstrating a solid understanding of titanium manufacturing processes and showcasing technical expertise can enhance credibility during negotiations. Offering insights or innovative ideas may also strengthen the negotiating position and foster collaborative solutions.
Flexibility and Compromise
Negotiations often involve give-and-take. Being open to compromise on certain aspects while maintaining essential requirements can lead to mutually beneficial agreements. Flexibility in areas such as payment terms, delivery schedules, or order quantities may help overcome obstacles and secure favorable terms.
Market Conditions and Trends
Growing Demand for Lightweight Materials
The increasing demand for lightweight materials in industries like aerospace, automotive, and electronics drives the need for high-quality titanium components. Japanese manufacturers are well-positioned to capitalize on this trend by offering components that contribute to weight reduction and enhanced performance.
Technological Advancements
Continuous technological advancements, including additive manufacturing and smart manufacturing, are transforming the production of titanium components. Japanese companies are investing in research and development to incorporate these technologies, enabling the creation of more complex and efficient products.
Sustainability and Environmental Considerations
Sustainability is becoming a critical factor in manufacturing. Japanese manufacturers are adopting eco-friendly practices, such as recycling titanium scrap and reducing energy consumption. Compliance with environmental regulations and the implementation of sustainable processes enhance the appeal of Japanese titanium components to environmentally conscious clients.
Global Supply Chain Dynamics
Global supply chain fluctuations, influenced by geopolitical factors and economic conditions, impact the availability and cost of raw materials. Japanese manufacturers mitigate these risks through diversified sourcing strategies and strong supplier relationships, ensuring a stable supply of high-quality titanium for production.
Best Practices in Procuring Japanese Titanium Components
Comprehensive Supplier Evaluation
Conducting a thorough evaluation of potential suppliers is essential. Assess factors such as the manufacturer’s reputation, quality certifications, production capabilities, and financial stability. Evaluating past performance and client testimonials can provide insights into the supplier’s reliability and expertise.
Clear Contractual Agreements
Establishing clear and detailed contractual agreements helps prevent disputes and ensure smooth transactions. Contracts should outline specifications, quality standards, delivery schedules, payment terms, and liability clauses. Legal counsel familiar with Japanese business law can assist in drafting enforceable agreements.
Regular Performance Monitoring
Ongoing performance monitoring ensures that suppliers consistently meet quality and delivery expectations. Implementing key performance indicators (KPIs) and conducting regular audits can help identify and address any issues promptly. Maintaining open lines of communication facilitates continuous improvement and reinforces accountability.
Collaboration in Product Development
Engaging suppliers early in the product development process fosters collaboration and innovation. Jointly developing prototypes, sharing technical knowledge, and conducting joint testing can enhance product design and manufacturability. This collaborative approach leads to higher-quality titanium components and strengthens the supplier-client relationship.
Risk Management and Contingency Planning
Effective risk management involves identifying potential risks and developing contingency plans. Diversifying suppliers, maintaining safety stock, and establishing alternative sourcing options can mitigate disruptions in the supply chain. Proactively addressing risks ensures the continuity of production and minimizes potential setbacks.
Case Studies: Japanese Manufacturers Leading the Way
Company A: Pioneering Titanium Aerospace Components
Company A, a leading Japanese manufacturer, has revolutionized the aerospace industry with its advanced titanium components. By integrating additive manufacturing into its production processes, the company can produce complex geometries with reduced material waste. Its commitment to quality and precision has earned it contracts with major aerospace firms globally, contributing to lighter and more fuel-efficient aircraft.
Company B: Innovating Medical Titanium Implants
Company B specializes in the production of titanium implants for the medical industry. Utilizing state-of-the-art CNC machining and surface treatment technologies, the company ensures biocompatibility and structural integrity of its products. Strong collaboration with medical professionals during the design phase has led to the development of implants that enhance patient outcomes and recovery times.
Company C: Advancing Automotive Lightweighting
In the automotive sector, Company C has made significant strides in lightweighting vehicles through its high-precision titanium components. By leveraging lean manufacturing practices and continuous process improvement, the company delivers components that reduce vehicle weight without compromising strength or safety. Its innovations contribute to improved fuel efficiency and lower emissions, aligning with global sustainability goals.
Future Outlook for Japanese Titanium Manufacturing
Embracing Industry 4.0
The future of Japanese titanium manufacturing lies in the full adoption of Industry 4.0 technologies. Integrating the Internet of Things (IoT), artificial intelligence (AI), and big data analytics into production systems will enable smarter manufacturing processes, predictive maintenance, and enhanced supply chain visibility. These advancements will further improve efficiency, reduce costs, and drive innovation.
Expanding into Emerging Markets
Japanese manufacturers are increasingly targeting emerging markets where demand for high-quality titanium components is growing. Regions such as Southeast Asia, India, and South America offer substantial growth opportunities. Establishing local partnerships and adapting products to regional needs will be key strategies for expanding market presence.
Sustainable and Eco-Friendly Manufacturing
Sustainability will continue to play a pivotal role in shaping the future of Japanese titanium manufacturing. Companies are investing in green technologies, such as energy-efficient production methods and sustainable material sourcing. Emphasizing environmental responsibility not only meets regulatory requirements but also appeals to environmentally conscious consumers and businesses.
Advancements in Material Science
Ongoing advancements in material science will open new possibilities for titanium component applications. Research into titanium alloys with enhanced properties, such as improved toughness or temperature resistance, will expand the range of applications. Japanese manufacturers, with their strong focus on R&D, are poised to lead these innovations and meet evolving industry demands.
Conclusion
Japanese manufacturing continues to set benchmarks in the production of precision titanium components. Through unwavering commitment to quality, adoption of advanced technologies, and a skilled workforce, Japanese manufacturers deliver products that meet the exacting standards of global industries. While challenges such as higher production costs and cultural barriers exist, the benefits of unparalleled precision, innovative design, and strong supplier relationships make Japanese titanium components highly sought after.
For procurement and purchasing professionals, partnering with Japanese manufacturers offers access to cutting-edge engineering capabilities and reliable, high-quality products. By understanding and navigating the unique aspects of Japanese business practices, companies can leverage the strengths of Japanese titanium manufacturing to enhance their own product offerings and achieve competitive advantage in the global marketplace.
As the industry evolves, Japanese manufacturers are well-positioned to lead innovations in titanium component production, driven by a continuous pursuit of excellence and sustainability. Embracing these advancements and best practices will enable businesses worldwide to harness the full potential of titanium as a transformative material in various high-performance applications.
資料ダウンロード
QCD調達購買管理クラウド「newji」は、調達購買部門で必要なQCD管理全てを備えた、現場特化型兼クラウド型の今世紀最高の購買管理システムとなります。
ユーザー登録
調達購買業務の効率化だけでなく、システムを導入することで、コスト削減や製品・資材のステータス可視化のほか、属人化していた購買情報の共有化による内部不正防止や統制にも役立ちます。
NEWJI DX
製造業に特化したデジタルトランスフォーメーション(DX)の実現を目指す請負開発型のコンサルティングサービスです。AI、iPaaS、および先端の技術を駆使して、製造プロセスの効率化、業務効率化、チームワーク強化、コスト削減、品質向上を実現します。このサービスは、製造業の課題を深く理解し、それに対する最適なデジタルソリューションを提供することで、企業が持続的な成長とイノベーションを達成できるようサポートします。
オンライン講座
製造業、主に購買・調達部門にお勤めの方々に向けた情報を配信しております。
新任の方やベテランの方、管理職を対象とした幅広いコンテンツをご用意しております。
お問い合わせ
コストダウンが利益に直結する術だと理解していても、なかなか前に進めることができない状況。そんな時は、newjiのコストダウン自動化機能で大きく利益貢献しよう!
(Β版非公開)