- お役立ち記事
- Vacuum (or compressed air) forming and post-processing of small thermoplastic elastomer parts
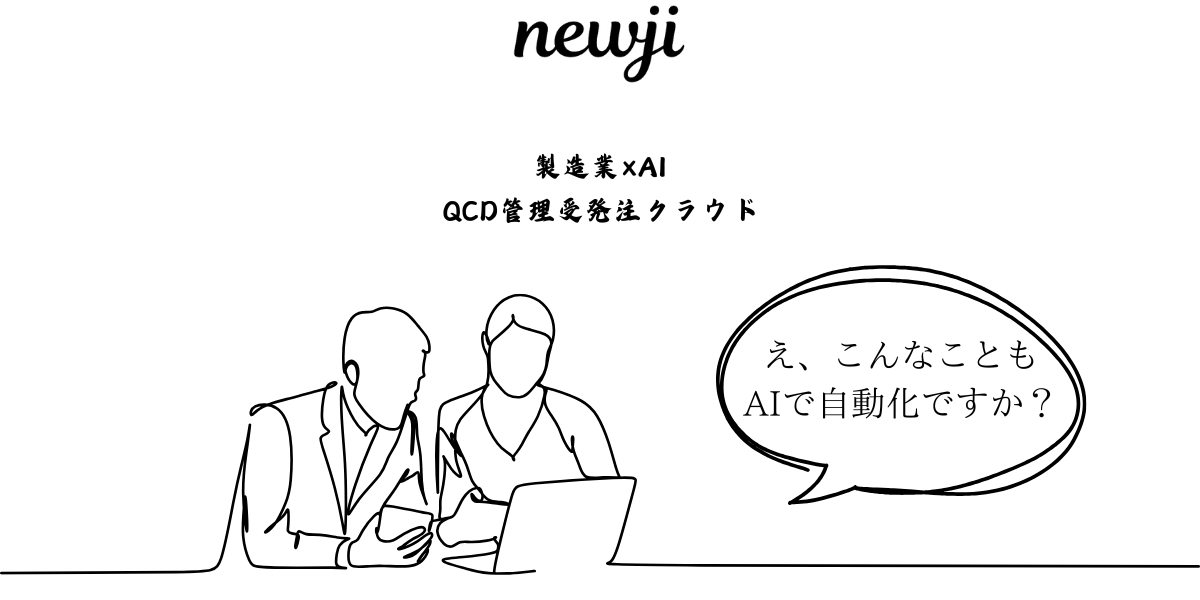
Vacuum (or compressed air) forming and post-processing of small thermoplastic elastomer parts
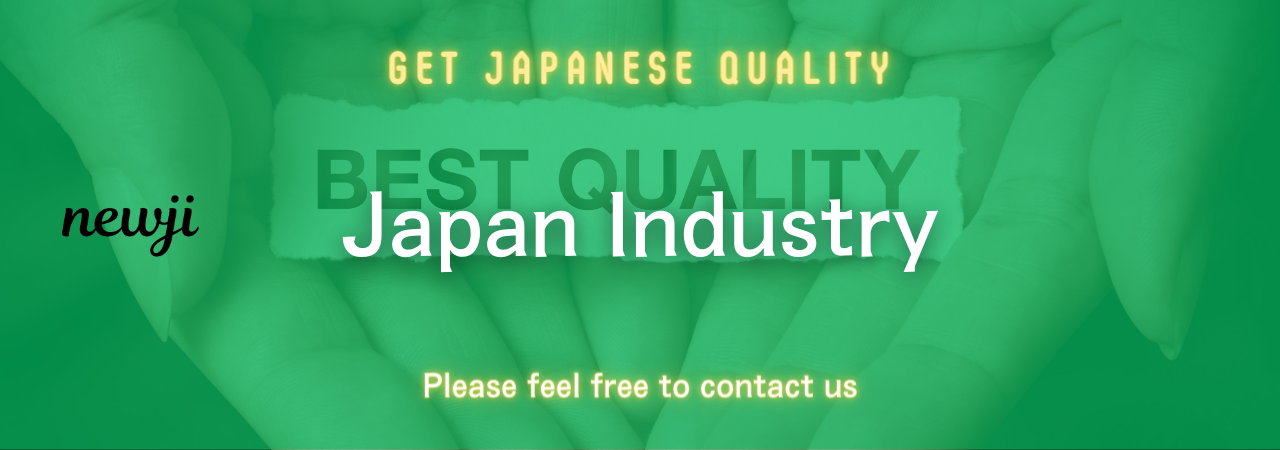
目次
Understanding Vacuum and Compressed Air Forming
Vacuum or compressed air forming is a fascinating process often used in the creation of small thermoplastic elastomer parts.
This technique involves shaping a plastic sheet by stretching it over a mold with the assistance of either vacuum or compressed air.
The process is essential in various industries because of its efficiency and precision in creating complex parts.
What are Thermoplastic Elastomers?
Thermoplastic elastomers (TPEs) are unique materials that combine the beneficial properties of both rubber and plastic.
They are known for their flexibility, durability, and ability to be molded easily when heated.
These materials are widely used in various applications, from automotive parts and medical devices to consumer goods.
The Process of Vacuum Forming
Vacuum forming begins with the heating of a plastic sheet until it becomes pliable.
Once the material is ready, it is placed over a mold.
A vacuum is then applied, pulling the heated material tightly over the mold’s surface.
This creates the desired shape as the material cools and hardens.
One of the advantages of vacuum forming is its ability to produce detailed parts with fine features quickly.
Additionally, it is cost-effective for small to medium production runs, making it ideal for industries requiring customized components.
The Role of Compressed Air in Forming
Compressed air forming, also known as pressure forming, is similar to vacuum forming but with added air pressure.
This method involves using pressurized air to push the material against the mold.
This extra force allows for even greater detail and sharper edges, essential for creating highly detailed parts.
This process is often chosen for parts that require precision and strength, as the increased pressure offers more control over the final product’s appearance and dimensions.
Applications of Vacuum and Compressed Air Forming
Various industries benefit from vacuum and compressed air forming due to its versatility and efficiency.
Automotive Industry
In the automotive industry, these processes are used to make interior components, gaskets, seals, and other parts that require flexibility and resilience.
The ability to produce lightweight yet durable components makes TPE an attractive option for vehicle manufacturers.
Medical Devices
The medical industry also relies on these forming technologies to produce devices and components, such as grips, tubing, and enclosures.
The biocompatibility of TPE materials ensures they are safe for direct contact with the human body.
Consumer Goods
Consumer goods manufacturers use vacuum and compressed air forming to create products ranging from soft-touch handles to protective cases.
The customization options and ability to produce intricate designs make these processes valuable to the market.
Post-Processing Techniques
Once a thermoplastic elastomer part is formed, it often requires post-processing to meet specific requirements or enhance its properties.
Trimming and Machining
Trimming and machining are common post-processing steps to ensure the part meets precise dimensions.
Trimming involves removing excess material around the edges, while machining can create holes or additional features.
These steps are crucial for ensuring the final product fits perfectly into its intended application.
Surface Finishing
Surface finishing can involve several techniques, such as polishing, painting, or coating, to enhance the appearance and texture of the part.
These additional treatments can also improve resistance to wear and environmental factors.
Assembly and Bonding
In some cases, TPE parts need to be combined with other components.
Assembly techniques may involve welding, adhesives, or mechanical fasteners to ensure a secure fit.
Bonding methods are chosen based on the specific requirements of the assembled product.
Advantages of Using Vacuum and Compressed Air Forming
The primary advantage of vacuum and compressed air forming is the cost-effectiveness of producing small batches of detailed parts.
The processes are generally quicker and less costly than molding methods like injection molding.
Additionally, vacuum and compressed air forming allows for a high level of design flexibility.
Manufacturers can quickly switch between different molds and designs with minimal downtime.
This versatility benefits those who wish to test various prototypes or require frequent design updates.
Conclusion
Vacuum and compressed air forming are remarkable processes that provide essential solutions for creating small thermoplastic elastomer parts across diverse industries.
These techniques offer multiple benefits, including cost-effectiveness, design flexibility, and precision.
Understanding the processes involved and their applications highlights the integral role they play in modern manufacturing.
Post-processing steps further ensure the parts produced are functional, aesthetic, and ready for use in their intended applications.
資料ダウンロード
QCD調達購買管理クラウド「newji」は、調達購買部門で必要なQCD管理全てを備えた、現場特化型兼クラウド型の今世紀最高の購買管理システムとなります。
ユーザー登録
調達購買業務の効率化だけでなく、システムを導入することで、コスト削減や製品・資材のステータス可視化のほか、属人化していた購買情報の共有化による内部不正防止や統制にも役立ちます。
NEWJI DX
製造業に特化したデジタルトランスフォーメーション(DX)の実現を目指す請負開発型のコンサルティングサービスです。AI、iPaaS、および先端の技術を駆使して、製造プロセスの効率化、業務効率化、チームワーク強化、コスト削減、品質向上を実現します。このサービスは、製造業の課題を深く理解し、それに対する最適なデジタルソリューションを提供することで、企業が持続的な成長とイノベーションを達成できるようサポートします。
オンライン講座
製造業、主に購買・調達部門にお勤めの方々に向けた情報を配信しております。
新任の方やベテランの方、管理職を対象とした幅広いコンテンツをご用意しております。
お問い合わせ
コストダウンが利益に直結する術だと理解していても、なかなか前に進めることができない状況。そんな時は、newjiのコストダウン自動化機能で大きく利益貢献しよう!
(Β版非公開)