- お役立ち記事
- Cost reduction measures and practical points to eliminate “waste” and “loss” at manufacturing sites
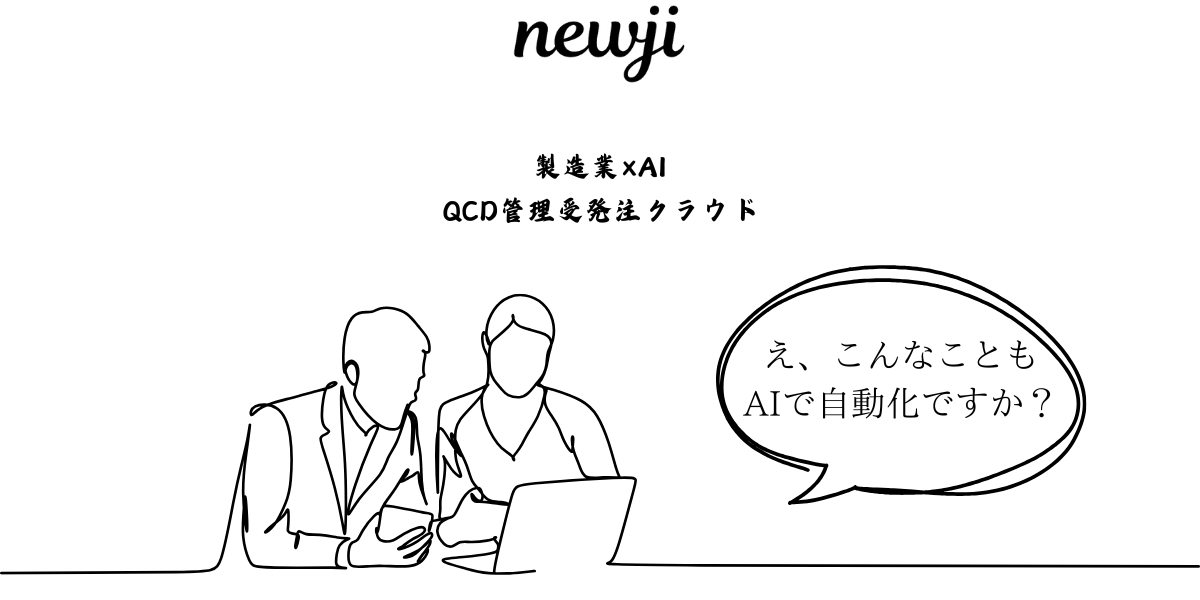
Cost reduction measures and practical points to eliminate “waste” and “loss” at manufacturing sites
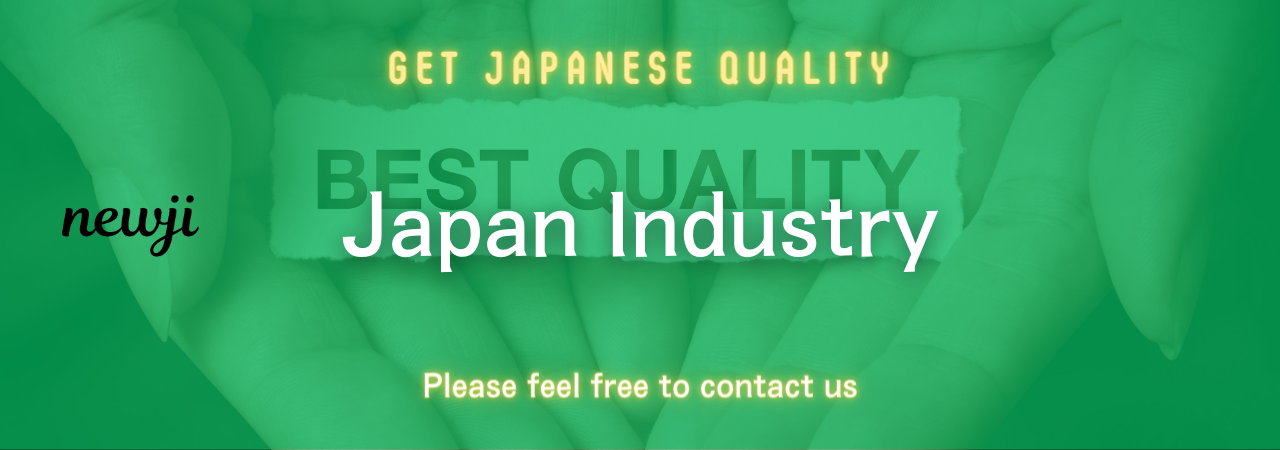
目次
Understanding Waste and Loss in Manufacturing
Manufacturing companies are constantly on the lookout for ways to improve efficiency and reduce costs.
One of the most effective strategies for achieving this is by identifying and eliminating “waste” and “loss” at manufacturing sites.
To begin, it’s important to understand what waste and loss entail.
Waste in manufacturing refers to any activity or process that does not add value to the product.
This can include overproduction, waiting, unnecessary transportation, excess inventory, over-processing, defects, and unused employee creativity.
Recognizing these types of waste is the first step in devising cost reduction measures.
Loss, on the other hand, involves any decrease in resources that could potentially translate into reduced profit margins.
This may be due to equipment inefficiencies, poor quality control, or ineffective use of personnel and materials.
Addressing both waste and loss requires a strategic approach to manufacturing operations.
Identifying Opportunities for Cost Reduction
To effectively reduce costs, companies need to focus on identifying opportunities for improvement within their processes.
This involves a thorough analysis of current procedures to pinpoint areas where resources are being wasted or lost.
One effective method for identifying waste is to conduct regular audits of the manufacturing process.
These audits should involve a comprehensive examination of each stage of production, from raw materials to finished goods.
During these audits, teams should look for any steps that do not directly contribute to the creation of value for the customer.
By identifying these non-value-added activities, manufacturers can begin to streamline operations and eliminate unnecessary costs.
In addition to audits, manufacturers can implement continuous improvement methodologies like Lean or Six Sigma.
These approaches emphasize the importance of involving employees at all levels in the identification and elimination of waste.
By fostering a culture of continuous improvement, companies can ensure that waste reduction becomes an integral part of their operations.
Implementing Effective Cost Reduction Measures
Once areas of waste and loss have been identified, the next step is to implement effective cost reduction measures.
There are several practical points that companies can consider to achieve this goal.
Optimize Inventory Management
Excess inventory is a common form of waste in manufacturing that can significantly increase costs.
By optimizing inventory management, companies can reduce the amount of capital tied up in unused materials.
Just-in-time (JIT) inventory systems can be particularly effective, allowing manufacturers to order materials only as they are needed.
This results in reduced storage costs and a lower risk of obsolescence.
Enhance Quality Control
Defects and rework account for a significant portion of waste and loss in manufacturing.
Enhancing quality control processes is crucial to minimizing these issues.
Companies should invest in advanced quality monitoring systems that offer real-time data and analytics.
This investment enables the early detection of defects and prevents them from escalating into larger problems.
By maintaining high-quality standards, manufacturers can reduce costs associated with rework and customer returns.
Leverage Technology
Technology can play a vital role in reducing waste and loss at manufacturing sites.
The integration of automation and Robotics Process Automation (RPA) can streamline repetitive tasks and improve overall efficiency.
Additionally, using data analytics can provide insightful information about production inefficiencies, allowing managers to make data-driven decisions that enhance productivity.
Improve Energy Efficiency
Energy is a significant cost factor in manufacturing.
Improving energy efficiency can lead to substantial cost savings.
Measures such as replacing outdated machinery, optimizing production schedules, and implementing energy-efficient practices contribute to reducing energy consumption.
Additionally, renewable energy sources can be explored to further decrease operational costs.
Boost Employee Engagement
Employees are an invaluable resource in any organization, and their engagement can substantially impact cost reduction efforts.
By involving employees in decision-making processes and encouraging them to share ideas for improvement, companies can foster a culture of ownership and accountability.
Increased employee engagement often leads to innovative ideas for cost reduction and process improvements.
Monitoring and Sustaining Cost Reduction Measures
Implementing cost reduction measures is only effective if their results are monitored and sustained over time.
Companies should put in place key performance indicators (KPIs) to measure the effectiveness of these measures.
Regular assessments should be conducted to ensure that improvements are maintained and new opportunities for cost reduction are identified.
Furthermore, creating a feedback loop empowers employees to share insights and observations about ongoing operations.
This feedback can highlight any reoccurrence of waste or loss and prompt immediate corrective actions.
To further sustain cost reduction measures, companies should emphasize training programs that educate employees on the importance of continuous improvement.
By continually updating the skill sets of employees, organizations can keep pace with evolving industry trends and maintain a competitive edge in the market.
Conclusion
Reducing waste and loss in manufacturing is a critical strategy for cost reduction that can lead to increased profitability and competitiveness.
By identifying and addressing areas of waste and loss, optimizing inventory, enhancing quality control, leveraging technology, and involving employees, companies can implement effective cost reduction measures.
Through consistent monitoring and sustaining these measures, manufacturers can ensure long-term success and operational efficiency in their manufacturing sites.
資料ダウンロード
QCD調達購買管理クラウド「newji」は、調達購買部門で必要なQCD管理全てを備えた、現場特化型兼クラウド型の今世紀最高の購買管理システムとなります。
ユーザー登録
調達購買業務の効率化だけでなく、システムを導入することで、コスト削減や製品・資材のステータス可視化のほか、属人化していた購買情報の共有化による内部不正防止や統制にも役立ちます。
NEWJI DX
製造業に特化したデジタルトランスフォーメーション(DX)の実現を目指す請負開発型のコンサルティングサービスです。AI、iPaaS、および先端の技術を駆使して、製造プロセスの効率化、業務効率化、チームワーク強化、コスト削減、品質向上を実現します。このサービスは、製造業の課題を深く理解し、それに対する最適なデジタルソリューションを提供することで、企業が持続的な成長とイノベーションを達成できるようサポートします。
オンライン講座
製造業、主に購買・調達部門にお勤めの方々に向けた情報を配信しております。
新任の方やベテランの方、管理職を対象とした幅広いコンテンツをご用意しております。
お問い合わせ
コストダウンが利益に直結する術だと理解していても、なかなか前に進めることができない状況。そんな時は、newjiのコストダウン自動化機能で大きく利益貢献しよう!
(Β版非公開)