- お役立ち記事
- Maintaining manufacturing equipment and ensuring long-term stable operation
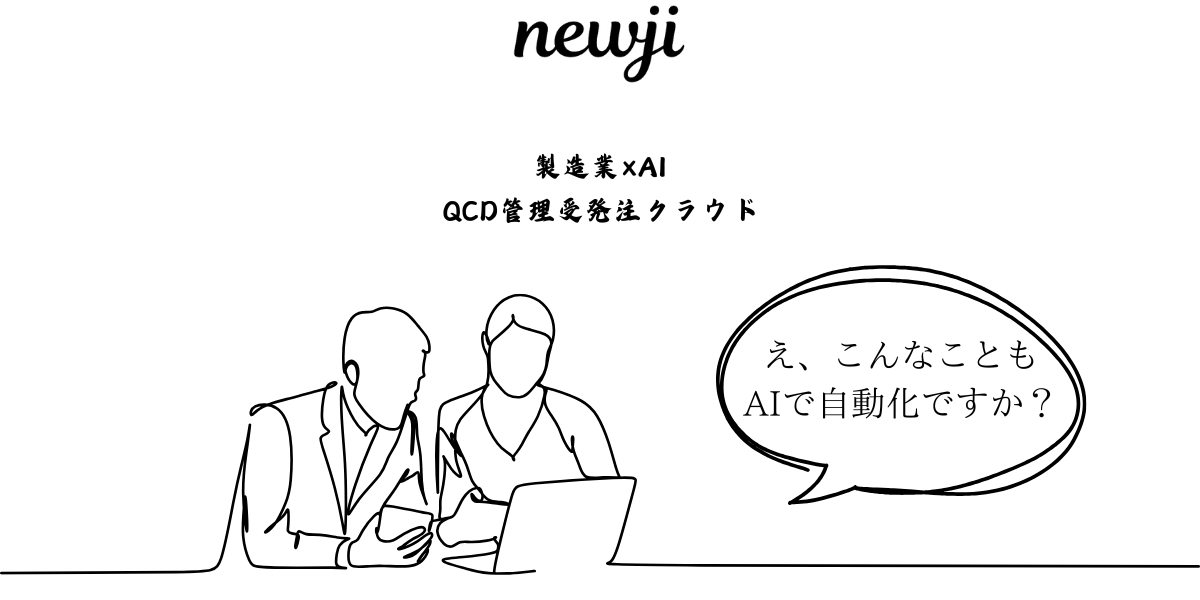
Maintaining manufacturing equipment and ensuring long-term stable operation
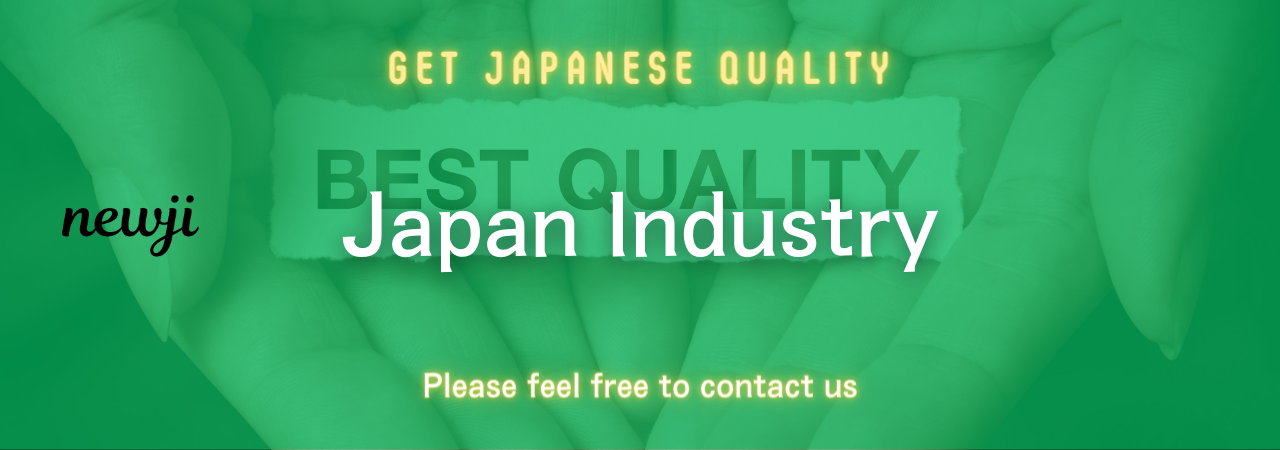
目次
Introduction to Manufacturing Equipment Maintenance
In the world of manufacturing, equipment is the backbone of any successful operation.
Without well-maintained machinery, production can grind to a halt, causing delays and financial losses.
Ensuring the long-term stable operation of manufacturing equipment is crucial for maintaining productivity and competitiveness in today’s fast-paced market.
Maintenance of manufacturing equipment involves regular inspections, timely repairs, and consistent upgrades.
It is not merely a task but a strategic approach to prolong the lifespan of machines, ensure safety, and optimize efficiency.
Understanding the importance of equipment maintenance and implementing best practices can lead to reduced downtime and significant cost savings.
The Importance of Equipment Maintenance
Maintenance is vital for several reasons.
First, it ensures the safe operation of equipment.
Machines that are not regularly maintained can pose safety hazards to workers, leading to potential accidents and injuries.
Regular inspections help in identifying and mitigating potential risks.
Second, maintenance minimizes downtime.
Broken or malfunctioning equipment can cause unexpected interruptions in production schedules.
By keeping machines in top condition, companies can maintain a steady workflow and meet delivery deadlines.
Third, maintenance practices contribute to equipment longevity.
Manufacturing machinery is a significant investment, and prolonging its life can save companies from frequent costly replacements.
Well-maintained equipment also tends to perform more efficiently, consuming less energy and reducing operational costs.
Types of Maintenance Strategies
There are several maintenance strategies that manufacturing companies can adopt to ensure the optimal performance of their equipment.
Reactive Maintenance
Reactive maintenance is a strategy where repairs are made only after equipment has already malfunctioned.
While this approach can work in some cases, it often leads to longer downtimes and can increase the overall repair costs.
It is generally not recommended for critical machinery where failures can have significant implications.
Preventive Maintenance
Preventive maintenance involves routine inspections and servicing at scheduled intervals to prevent problems before they occur.
This strategy can help identify wear and tear early, allowing for timely replacements and avoiding sudden breakdowns.
Regular oiling, cleaning, and part replacements are common preventive measures.
Predictive Maintenance
Predictive maintenance uses data analysis tools and techniques to predict when equipment will need maintenance.
Sensors and IoT devices collect real-time data on machine conditions and performance.
This approach allows companies to address issues before they lead to failures, optimizing both time and resources.
Condition-Based Maintenance
Condition-based maintenance closely monitors the actual condition of the equipment to determine what maintenance should be done and when.
This method employs various evaluations such as vibration analysis, thermal imaging, and ultrasonic inspections.
These evaluations ensure that maintenance occurs only when necessary, which can be more cost-effective than routine checks.
Best Practices for Maintaining Manufacturing Equipment
To maintain manufacturing equipment and ensure its long-term, stable operation, companies should consider several best practices.
Implement Regular Training Programs
Training employees on how to operate machinery correctly and safely is essential.
Proper use of equipment reduces wear and tear and minimizes the risk of accidental damage.
Training programs should also educate workers on identifying signs of equipment distress and following standard operating procedures.
Create a Maintenance Schedule
Developing a comprehensive maintenance schedule helps ensure that all equipment receives regular checks and servicing.
It is vital to maintain a log of all maintenance activities, which can be referenced in the future to predict potential issues.
Use High-Quality Replacement Parts
Using subpar or incompatible parts during repairs can compromise the integrity of the equipment and lead to further issues.
Always use high-quality, manufacturer-recommended parts for replacements and upgrades.
Utilize Technology and Automation
Modern technologies provide numerous solutions for improving maintenance operations.
Automation in maintenance processes can help streamline tasks, reduce human error, and enhance precision in detecting problems early.
Investing in software that provides condition monitoring and predictive analysis can significantly improve maintenance strategies.
Establish a Feedback Loop
Create a system where operators can report issues and provide feedback on equipment performance without hesitation.
This feedback loop can help maintenance teams address problems quickly and improve overall maintenance procedures.
Benefits of Effective Equipment Maintenance
Implementing effective maintenance strategies for manufacturing equipment comes with numerous benefits.
Enhanced Equipment Reliability
One of the primary benefits is improved equipment reliability.
Regular maintenance ensures machines run smoothly and predictably, which is essential for meeting production targets.
Cost Savings
While maintenance does incur costs, the long-term savings it provides are considerable.
By preventing major breakdowns and extending the life of machines, companies save on expensive repairs and replacements.
Improved Workplace Safety
Proper maintenance reduces the risk of accidents by ensuring that machinery operates safely and efficiently.
This not only protects workers but also avoids potential legal and compensation costs associated with workplace incidents.
Increased Operational Efficiency
Well-maintained equipment operates at optimal performance levels, reducing energy consumption and waste.
This efficiency boosts overall productivity and enhances the quality of the products manufactured.
Conclusion
Maintaining manufacturing equipment is essential for achieving long-term stable operations, improving efficiency, and ensuring safety.
By adopting suitable maintenance strategies and best practices, manufacturers can significantly enhance their operations.
Investing in maintenance is investing in the company’s success and sustainability.
資料ダウンロード
QCD調達購買管理クラウド「newji」は、調達購買部門で必要なQCD管理全てを備えた、現場特化型兼クラウド型の今世紀最高の購買管理システムとなります。
ユーザー登録
調達購買業務の効率化だけでなく、システムを導入することで、コスト削減や製品・資材のステータス可視化のほか、属人化していた購買情報の共有化による内部不正防止や統制にも役立ちます。
NEWJI DX
製造業に特化したデジタルトランスフォーメーション(DX)の実現を目指す請負開発型のコンサルティングサービスです。AI、iPaaS、および先端の技術を駆使して、製造プロセスの効率化、業務効率化、チームワーク強化、コスト削減、品質向上を実現します。このサービスは、製造業の課題を深く理解し、それに対する最適なデジタルソリューションを提供することで、企業が持続的な成長とイノベーションを達成できるようサポートします。
オンライン講座
製造業、主に購買・調達部門にお勤めの方々に向けた情報を配信しております。
新任の方やベテランの方、管理職を対象とした幅広いコンテンツをご用意しております。
お問い合わせ
コストダウンが利益に直結する術だと理解していても、なかなか前に進めることができない状況。そんな時は、newjiのコストダウン自動化機能で大きく利益貢献しよう!
(Β版非公開)